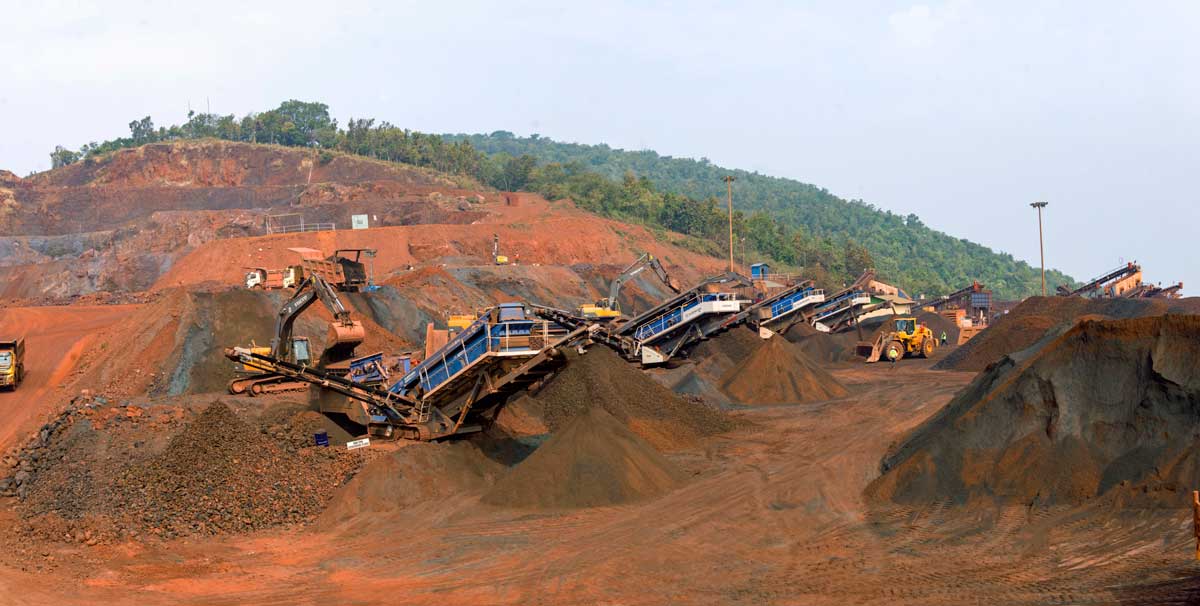
Screening Solution
Read full article
CW Gold Benefits
- Weekly Industry Updates
- Industry Feature Stories
- Premium Newsletter Access
- Building Material Prices (weekly) + trends/analysis
- Best Stories from our sister publications - Indian Cement Review, Equipment India, Infrastructure Today
- Sector focused Research Reports
- Sector Wise Updates (infrastructure, cement, equipment & construction) + trend analysis
- Exclusive text & video interviews
- Digital Delivery
- Financial Data for publically listed companies + Analysis
- Preconceptual Projects in the pipeline PAN India
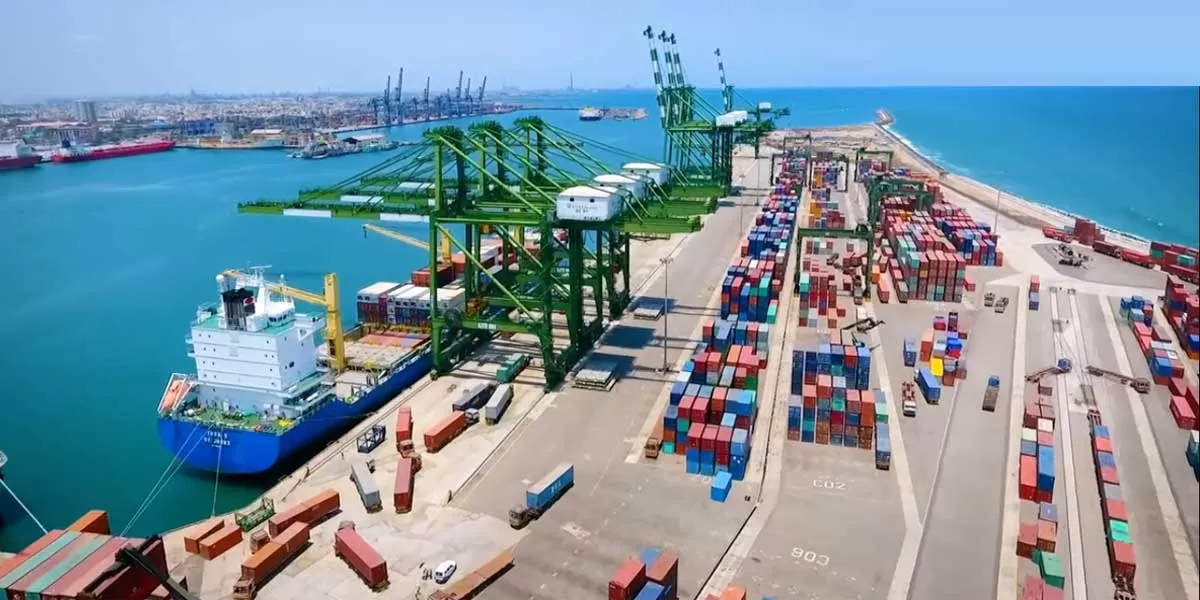
GoM Formed to Review Vadhvan Port Project’s Environmental Impact
The Union government has established a three-member Group of Ministers (GoM) to evaluate the environmental effects of the Rs 76.22 Bn Vadhvan Port project in Maharashtra’s Palghar district. Headed by Commerce and Industry Minister Piyush Goyal, the GoM also includes Sarbananda Sonowal and Bhupender Yadav, who leads the Ministries of Ports and Environment respectively.The GoM will analyse the environmental impact assessment presented by the National Environmental Engineering Research Institute (NEERI), an expert body. It is also authorised to consult additional experts and refer matters for f..
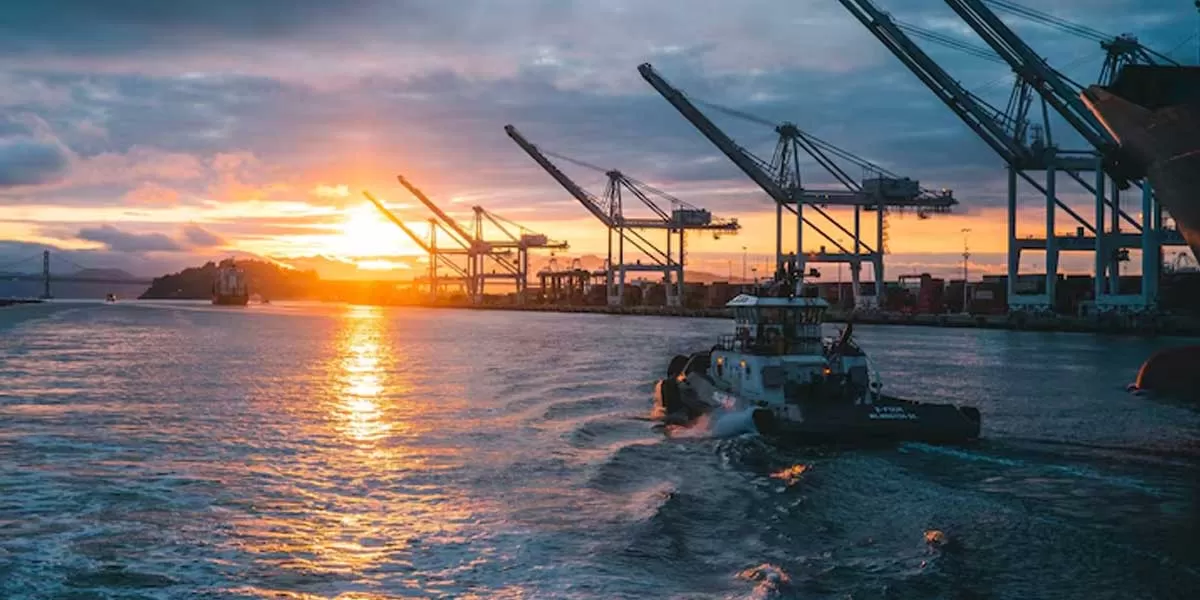
India’s First Offshore Decommissioning Completed at Tapti Field
Shell, Reliance Industries Limited, and Oil and Natural Gas Corporation (ONGC) have successfully completed India’s first offshore oil and gas decommissioning project by dismantling mid and south Tapti field facilities in the Arabian Sea.The project involved removal of five wellhead platforms, infield pipelines, and onshore load-in at a dismantling yard. It also included the safe plugging and abandonment of 38 wells. The Tapti fields ceased production in March 2016.This achievement highlights advanced planning, strong collaboration, and adherence to regulatory standards, with an emphasis on s..
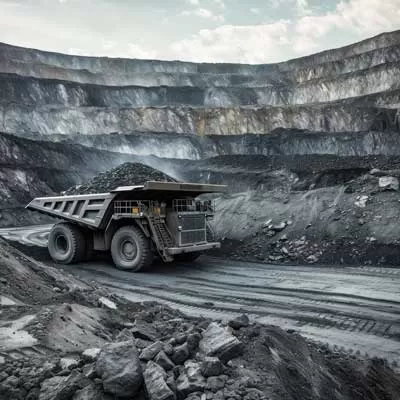
India Posts Record Mineral Output in FY25 Led by Iron Ore, Aluminium
India’s mining sector has recorded significant growth in financial year 2024–25, achieving new highs in the production of key minerals and non-ferrous metals. According to provisional data from the Ministry of Mines, iron ore production reached 289 Mn metric tonnes (MMT), rising by 4.3 per cent from 277 MMT in the previous year. Iron ore alone contributes 70 per cent of the total mineral output regulated under the Mineral Conservation and Development Rules (MCDR) by value.Manganese ore output climbed 11.8 per cent to 3.8 MMT, while bauxite production rose 2.9 per cent to 24.7 MMT. Lead con..