- Home
- Infrastructure Energy
- OIL & GAS
- Trenching Trends
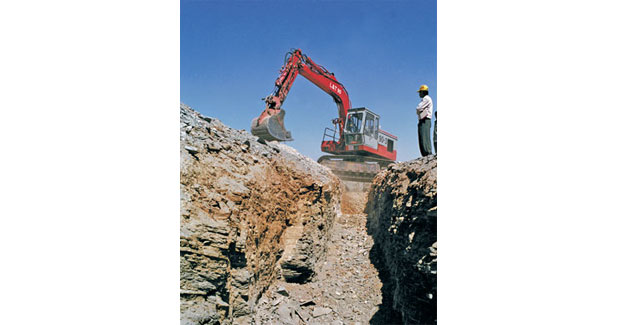
Trenching Trends
India has seen considerable advancement in the way underground infrastructure, such as oil and gas pipelines, telecom network conduits and water pipes, is laid.
Going trenchless
Whereas open trenching used to be the norm for laying pipelines, horizontal directional drilling (HDD) technology, a trenchless method of installing underground pipes, conduits and cables, has become the method of choice for many applications because it is far more efficient, especially in city areas and where environmental and security concerns are prevalent. HDD minimises the risk of damage to existing infrastructure like roads, footpaths, trees and existing underground utilities, and hence saves ensuing repairing and reinstating costs. Also, HDD does not cause traffic jams and dust pollution, inconveniencing local residents.
With HDD, pipes can be installed from 5 m to even 100 m or more below ground level. ¨Horizontal directional drilling allows pipelines of larger diameter and longer lengths to be laid in one stretch,¨ explains Vipin Gupta, Chairman & Managing Director, Trenchless India, a specialist in HDD for oil and gas pipelines from 6 inch to 48 inch and length up to 2,500 m across rivers.
¨So what if laying cables by HDD technology is more expensive than open trenching?¨ asks Ajith Kumar, CEO, Swift Projects, Asia subcontinent dealer for Universal HDD machines.
Opportunities abound
Today, major opportunities have arisen for contractors deploying HDD technology from telecom service providers introducing 4G services necessitating new underground cabling, the Central Government´s Digital India initiative, power corporations releasing contracts for underground cable laying, new gas pipes and oil pipes being laid underground, and water and sewage departments of many states initiating contracts for underground pipe laying, observes Kumar. ¨Tremendous scope exists for HDD as over 10,000 km of oil and gas pipelines alone have to be laid in the next five years,¨ adds Gupta.
HDD technology has also received a huge boost from open excavation being banned in many areas in major cities like Delhi, Bengaluru, Mumbai, etc.
Key market players
Owing to the huge opportunities, HDD machines are in heavy demand at present, according to Kumar, and he sees no let up in the upswing for at least 10 years. Leading equipment providers in the HDD space include overseas companies such as Vermeer, American Augers, Herrenknecht and Prime Drilling for the larger rigs, and Ditchwitch and a number of Chinese players for the smaller rigs, says Gupta. However, he rues the fact that all these rigs aren´t manufactured in India. ¨Relying on imported equipment increases upfront as well as servicing costs and the time taken to acquire and repair machines,¨ he reasons. ¨This lengthens project execution times and tends to cause cost overruns.¨
Longer order lead times means users must plan their work and take procurement action well in advance. As for prompt service, what is helping bring business to Erkat, another player, is having a direct sales-and-service base in India instead of being represented by distributors, and being solely focused on customisable drum cutters and similar attachments, according to Tarun Kumar, Sales Manager-India, Africa & Far East, Erkat. ¨The higher price of imported machines does not deter discerning customers who look for quality products,¨ he adds. ¨Products made in Germany have a quality tag.¨
In recent years, Chinese rigs have taken the cost-conscious Indian market by storm. ¨Priced at about a third of other models, Chinese models accounted for about 10 per cent of the market a decade ago. Today they enjoy 70 per cent of the market,¨ says Gupta. To cater to established players and many (more cost-conscious) first-time buyers entering the HDD segment, Swift Projects offers both new Universal HDD machines as well as used Vermeer machines. ¨Imported used machines can be had for about one-third the price of a new American machine, which is also on a par in price with Chinese machines,¨ says Kumar of Swift Projects.
Greater awareness will grow the market
With the market for HDD growing exponentially and the government´s encouraging ´Make in India´ initiative, Gupta feels it is high-time some industrial house looks at the option of manufacturing rigs in India for domestic use and exports. Meanwhile, overseas brands continue to enter the market.
Inter-Drain Sales bv Holland has a presence in India through an exclusive distributor and after-sales service provider Sunviz Impex. A world leader in trenching technology that manufactures customised trenchers as per customer requirement, Inter-Drain´s machines have so far been deployed for subsurface drainage projects in India. ¨Trenchers fitted with a laser control system have been used to lay PVC corrugated perforated pipes in agricultural fields in Punjab and Haryana to drain heavily waterlogged saline fields to make the top soil more fertile and thereby increase yields,¨ shares Sanil Sahu, CEO, Sunviz Impex Pvt Ltd. ¨Pipes of various diameters as per project design have been laid at a depth of up to about 3 m, with the possibility of laying pipes up to 500-mm diameter up to 3.5 m depth.¨ He believes that opportunities in laying telecommunications cables, potable water pipelines, etc, will boost demand for Inter-Drain trenchers in the near future.
Erkat GmbH offers versatile drum cutters that can be deployed for trenching, quarrying, asphalt or concrete cutting, pile head demolition, underwater cutting and, most of all, cost-effective tunnel excavation where the strata is poor and the conventional drill and blast is either not allowed or too risky owing to danger of roof collapse, shares Kumar of Erkat. Companies such as Afcons, Leighton, Coastal Projects, Gammon, L&T Construction and Mahati Hydro have used Erkat cutters for tunnel excavation jobs for roads, railway and hydro projects. ¨We see scope for demand to grow for all Erkat machines,¨ he adds. ¨Many contractors still use conventional methods like drill and blast, hydraulic breakers, excavator buckets or even manual labour. They need to become aware of the advantages of using specialised attachments for different applications.¨
Quick Bytes
- Opportunities for HDD technology from telecom service providers, the Digital India initiative, power, oil and gas, and water projects.
- Tunnel boring machines being extensively used worldwide for safer, expeditious and cheaper construction of tunnels.
- Chinese models enjoy 70 per cent of the market; high-time to manufacture rigs in India for domestic use and exports.
Tunnelling in India : Sore need for modernisation
PK SOOD, Director, Dr Hutarew & Partner (India) Pvt Ltd, explains why India sorely needs tunnel specifications to mandate the use of the New Austrian Tunnelling Method (NATM) and the challenges along the way.
Almost all the tunnels constructed in India for hydropower projects, railways or highways have been and continue to be constructed using the old drill-and-blast method. It involves sustaining the drilled and blasted underground opening with passive supports in the form of steel ribs.
In contrast, NATM involves blasting and thereafter reinforcing the underground opening with rock bolts and sealing the cracked surface of the exposed rock with pneumatically applied concrete called shotcrete. Rock bolts are given tension, which is checked from time-to-time through instrument monitoring systems. Additional tension is provided if necessary to preserve the integrity of the arch. NATM is faster and more economical than the conventional method because it eliminates the mandatory customised fabrication and installation of heavy steel ribs. Also, the shotcrete spraying and rock bolt installation can happen even while the muck is being removed. NATM is well-suited to the Himalayas because the Alpine rocks where the method was first developed are similar to the young and unpredictable Himalayan rocks. In fact, it is better suited to the Himalayas than tunnel boring, which yields better outcomes in stable rock.
Nowadays, tunnel boring machines (TBMs) are being extensively used worldwide for the safer, expeditious and cheaper construction of tunnels. TBMs can yield a progress of up to 15 m of tunnelling per day per face while the drill-and-blast method limits progress to 2-3 m per day per face. NATM is somewhere between these methods.
TBMs have been successfully applied in the Delhi Metro, which involved the construction of several tunnels at shallow depths in loose, water bearing and weak soil strata, and are now being deployed for the construction of other metros. However, their use in the Himalayas is restricted for want of proper road infrastructure. Their overall use in India is also hampered for want of trained deployment and maintenance manpower. This leads to cost escalations.
India is moving towards greater adoption of NATM with the use of steel ribs being limited to isolated stretches. But greater awareness must be created about the safety of NATM. Ill-informed tunnelling personnel tend to believe that the tunnel will collapse if a steel rib supporting the roof is not installed.
A key challenge is that the success of NATM depends on the availability of modern rock bolts and measuring instruments, which are not being manufactured in India. This is an avenue manufacturers should tap. Relying on imported materials escalates costs.
- Trenching Trends
- Infrastructure
- Vipin Gupta
- Trenchless India
- Ajith Kumar
- Ajith Kumar
- Swift Projects
- Gas Pipes
- Oil Pipes
- Vermeer
- American Augers
- Herrenknecht
- Ditchwitch
- Erkat
- Tarun Kumar
- Make in India
- Sunviz Impex Pvt Ltd
- Sanil Sahu
- Afcons
- Leighton
- Coastal Projects
- Gammon
- L&T Construction
- Mahati Hydro
- PK SOOD
- Dr Hutarew & Partner (India) Pvt Ltd
- New Austrian Tunnelling Met
High-end machines for laying underground infrastructure are in demand, but local manufacturers are conspicuous by their absence. India has seen considerable advancement in the way underground infrastructure, such as oil and gas pipelines, telecom network conduits and water pipes, is laid. Going trenchless Whereas open trenching used to be the norm for laying pipelines, horizontal directional drilling (HDD) technology, a trenchless method of installing underground pipes, conduits and cables, has become the method of choice for many applications because it is far more efficient, especially in city areas and where environmental and security concerns are prevalent. HDD minimises the risk of damage to existing infrastructure like roads, footpaths, trees and existing underground utilities, and hence saves ensuing repairing and reinstating costs. Also, HDD does not cause traffic jams and dust pollution, inconveniencing local residents. With HDD, pipes can be installed from 5 m to even 100 m or more below ground level. ¨Horizontal directional drilling allows pipelines of larger diameter and longer lengths to be laid in one stretch,¨ explains Vipin Gupta, Chairman & Managing Director, Trenchless India, a specialist in HDD for oil and gas pipelines from 6 inch to 48 inch and length up to 2,500 m across rivers. ¨So what if laying cables by HDD technology is more expensive than open trenching?¨ asks Ajith Kumar, CEO, Swift Projects, Asia subcontinent dealer for Universal HDD machines. Opportunities abound Today, major opportunities have arisen for contractors deploying HDD technology from telecom service providers introducing 4G services necessitating new underground cabling, the Central Government´s Digital India initiative, power corporations releasing contracts for underground cable laying, new gas pipes and oil pipes being laid underground, and water and sewage departments of many states initiating contracts for underground pipe laying, observes Kumar. ¨Tremendous scope exists for HDD as over 10,000 km of oil and gas pipelines alone have to be laid in the next five years,¨ adds Gupta. HDD technology has also received a huge boost from open excavation being banned in many areas in major cities like Delhi, Bengaluru, Mumbai, etc. Key market players Owing to the huge opportunities, HDD machines are in heavy demand at present, according to Kumar, and he sees no let up in the upswing for at least 10 years. Leading equipment providers in the HDD space include overseas companies such as Vermeer, American Augers, Herrenknecht and Prime Drilling for the larger rigs, and Ditchwitch and a number of Chinese players for the smaller rigs, says Gupta. However, he rues the fact that all these rigs aren´t manufactured in India. ¨Relying on imported equipment increases upfront as well as servicing costs and the time taken to acquire and repair machines,¨ he reasons. ¨This lengthens project execution times and tends to cause cost overruns.¨ Longer order lead times means users must plan their work and take procurement action well in advance. As for prompt service, what is helping bring business to Erkat, another player, is having a direct sales-and-service base in India instead of being represented by distributors, and being solely focused on customisable drum cutters and similar attachments, according to Tarun Kumar, Sales Manager-India, Africa & Far East, Erkat. ¨The higher price of imported machines does not deter discerning customers who look for quality products,¨ he adds. ¨Products made in Germany have a quality tag.¨ In recent years, Chinese rigs have taken the cost-conscious Indian market by storm. ¨Priced at about a third of other models, Chinese models accounted for about 10 per cent of the market a decade ago. Today they enjoy 70 per cent of the market,¨ says Gupta. To cater to established players and many (more cost-conscious) first-time buyers entering the HDD segment, Swift Projects offers both new Universal HDD machines as well as used Vermeer machines. ¨Imported used machines can be had for about one-third the price of a new American machine, which is also on a par in price with Chinese machines,¨ says Kumar of Swift Projects. Greater awareness will grow the market With the market for HDD growing exponentially and the government´s encouraging ´Make in India´ initiative, Gupta feels it is high-time some industrial house looks at the option of manufacturing rigs in India for domestic use and exports. Meanwhile, overseas brands continue to enter the market. Inter-Drain Sales bv Holland has a presence in India through an exclusive distributor and after-sales service provider Sunviz Impex. A world leader in trenching technology that manufactures customised trenchers as per customer requirement, Inter-Drain´s machines have so far been deployed for subsurface drainage projects in India. ¨Trenchers fitted with a laser control system have been used to lay PVC corrugated perforated pipes in agricultural fields in Punjab and Haryana to drain heavily waterlogged saline fields to make the top soil more fertile and thereby increase yields,¨ shares Sanil Sahu, CEO, Sunviz Impex Pvt Ltd. ¨Pipes of various diameters as per project design have been laid at a depth of up to about 3 m, with the possibility of laying pipes up to 500-mm diameter up to 3.5 m depth.¨ He believes that opportunities in laying telecommunications cables, potable water pipelines, etc, will boost demand for Inter-Drain trenchers in the near future. Erkat GmbH offers versatile drum cutters that can be deployed for trenching, quarrying, asphalt or concrete cutting, pile head demolition, underwater cutting and, most of all, cost-effective tunnel excavation where the strata is poor and the conventional drill and blast is either not allowed or too risky owing to danger of roof collapse, shares Kumar of Erkat. Companies such as Afcons, Leighton, Coastal Projects, Gammon, L&T Construction and Mahati Hydro have used Erkat cutters for tunnel excavation jobs for roads, railway and hydro projects. ¨We see scope for demand to grow for all Erkat machines,¨ he adds. ¨Many contractors still use conventional methods like drill and blast, hydraulic breakers, excavator buckets or even manual labour. They need to become aware of the advantages of using specialised attachments for different applications.¨ Quick Bytes Opportunities for HDD technology from telecom service providers, the Digital India initiative, power, oil and gas, and water projects. Tunnel boring machines being extensively used worldwide for safer, expeditious and cheaper construction of tunnels. Chinese models enjoy 70 per cent of the market; high-time to manufacture rigs in India for domestic use and exports. Tunnelling in India : Sore need for modernisation PK SOOD, Director, Dr Hutarew & Partner (India) Pvt Ltd, explains why India sorely needs tunnel specifications to mandate the use of the New Austrian Tunnelling Method (NATM) and the challenges along the way. Almost all the tunnels constructed in India for hydropower projects, railways or highways have been and continue to be constructed using the old drill-and-blast method. It involves sustaining the drilled and blasted underground opening with passive supports in the form of steel ribs. In contrast, NATM involves blasting and thereafter reinforcing the underground opening with rock bolts and sealing the cracked surface of the exposed rock with pneumatically applied concrete called shotcrete. Rock bolts are given tension, which is checked from time-to-time through instrument monitoring systems. Additional tension is provided if necessary to preserve the integrity of the arch. NATM is faster and more economical than the conventional method because it eliminates the mandatory customised fabrication and installation of heavy steel ribs. Also, the shotcrete spraying and rock bolt installation can happen even while the muck is being removed. NATM is well-suited to the Himalayas because the Alpine rocks where the method was first developed are similar to the young and unpredictable Himalayan rocks. In fact, it is better suited to the Himalayas than tunnel boring, which yields better outcomes in stable rock. Nowadays, tunnel boring machines (TBMs) are being extensively used worldwide for the safer, expeditious and cheaper construction of tunnels. TBMs can yield a progress of up to 15 m of tunnelling per day per face while the drill-and-blast method limits progress to 2-3 m per day per face. NATM is somewhere between these methods. TBMs have been successfully applied in the Delhi Metro, which involved the construction of several tunnels at shallow depths in loose, water bearing and weak soil strata, and are now being deployed for the construction of other metros. However, their use in the Himalayas is restricted for want of proper road infrastructure. Their overall use in India is also hampered for want of trained deployment and maintenance manpower. This leads to cost escalations. India is moving towards greater adoption of NATM with the use of steel ribs being limited to isolated stretches. But greater awareness must be created about the safety of NATM. Ill-informed tunnelling personnel tend to believe that the tunnel will collapse if a steel rib supporting the roof is not installed. A key challenge is that the success of NATM depends on the availability of modern rock bolts and measuring instruments, which are not being manufactured in India. This is an avenue manufacturers should tap. Relying on imported materials escalates costs.