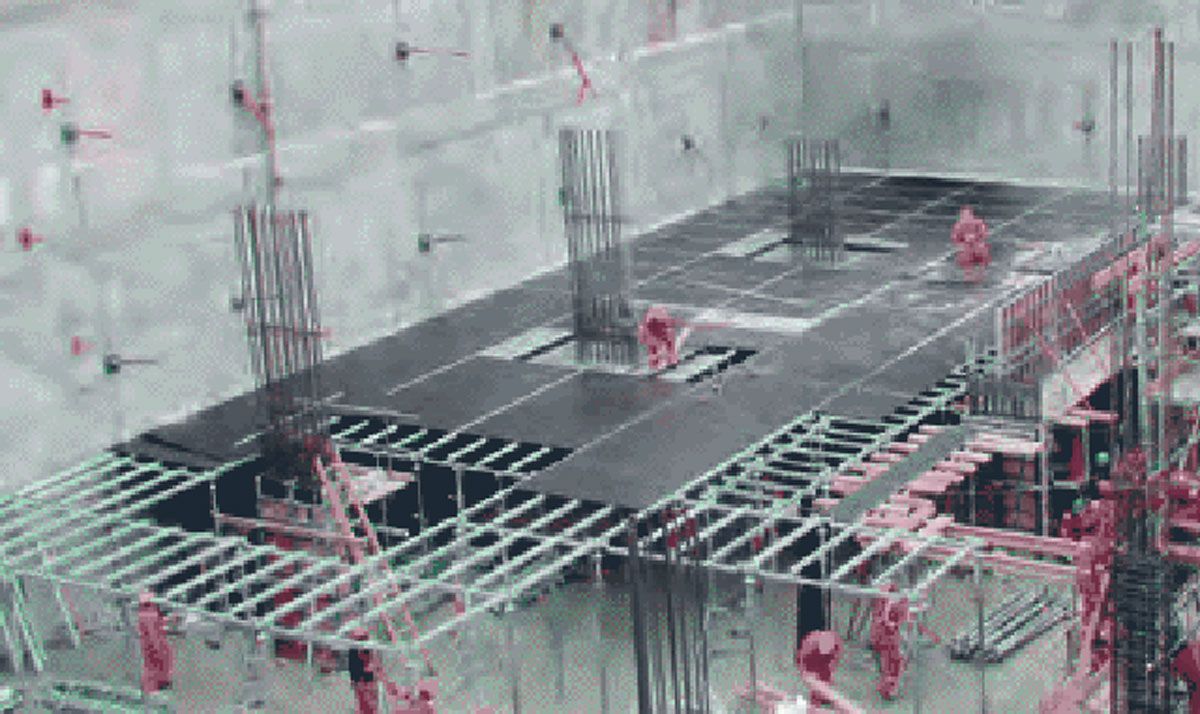
Recoverable Modular Slab Formwork
01 Jul 2022
4 Min Read
Editorial Team
ONADEK is a high-performing
slab formwork system with easy
assembly and maximum flexibility,
especially for commercial and
multi-car parking buildings where
the use of flat slabs is inevitable....
Read full article
Try CW Gold Subscription at 167/Month
CW Gold Benefits
- Weekly Industry Updates
- Industry Feature Stories
- Premium Newsletter Access
- Building Material Prices (weekly) + trends/analysis
- Best Stories from our sister publications - Indian Cement Review, Equipment India, Infrastructure Today
- Sector focused Research Reports
- Sector Wise Updates (infrastructure, cement, equipment & construction) + trend analysis
- Exclusive text & video interviews
- Digital Delivery
- Financial Data for publically listed companies + Analysis
- Preconceptual Projects in the pipeline PAN India