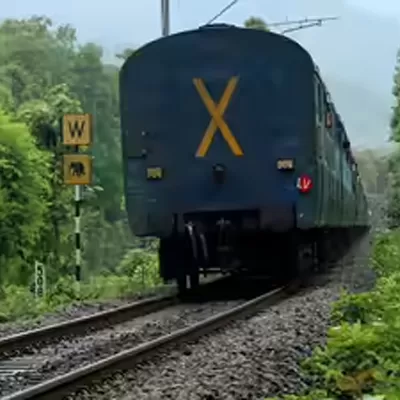
Rs 19.5 Billion Meerut–Nazibabad Rail Electrification Complete
The Rs 19.5 billion railway electrification of the Meerut–Nazibabad section has been completed, marking a major step towards improving connectivity in northern India. The project covers 132 kilometres of track and is expected to enhance operational efficiency while reducing travel time and fuel costs.Officials from the Ministry of Railways said the electrification will enable faster, more reliable train services and contribute to reduced carbon emissions. The initiative aligns with the government’s broader goal of achieving 100 per cent electrification of India’s railway network by 2030...
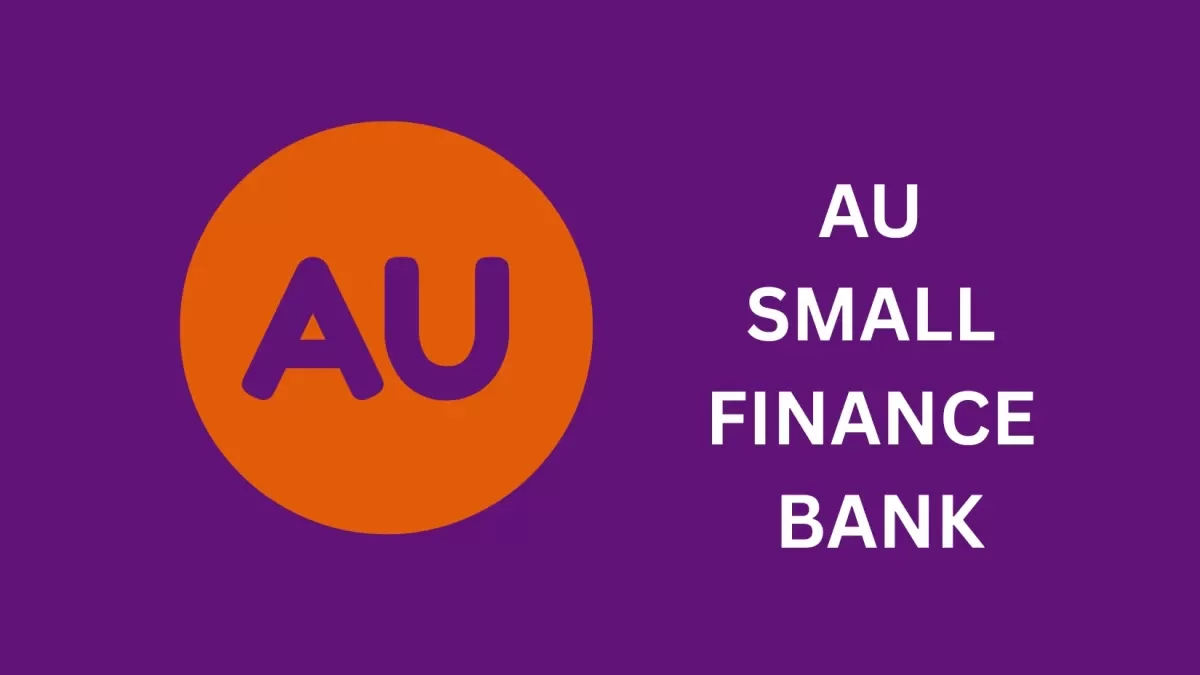
AU Small Finance Bank Secures RBI Approval For Universal Bank
AU Small Finance Bank has received approval from the Reserve Bank of India (RBI) to transition into a universal bank. The move will allow the Jaipur-based lender to expand its range of financial services and compete directly with larger commercial banks.Founded in 1996 as a non-banking finance company, AU Small Finance Bank became a small finance bank in 2017. The transition to a universal bank will enable it to offer a broader portfolio, including enhanced corporate banking, treasury operations, and new retail products.Managing Director and CEO Sanjay Agarwal said the approval marks a signifi..
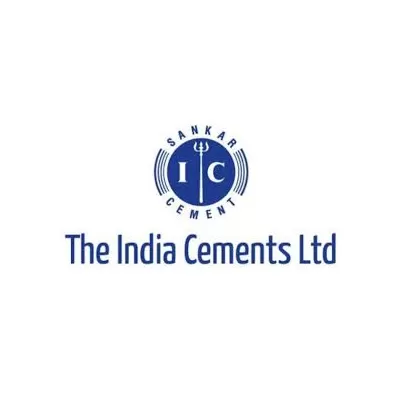
India Cements Q1 Loss Narrows To Rs 276 Million On Higher Sales
India Cements Ltd has reported a consolidated net loss of Rs 276 million for the quarter ended June 2025, narrowing from a loss of Rs 831 million a year earlier. Consolidated revenue from operations rose 20 per cent year-on-year to Rs 17.9 billion from Rs 14.9 billion.The company attributed the improvement to higher sales volumes and better price realisations, which offset some of the impact of elevated fuel and raw material costs. EBITDA turned positive at Rs 1.1 billion, compared with a loss in the same period last year.Vice Chairman and Managing Director N. Srinivasan said the company will ..