Is India’s Rs 5.7 trillion infrastructure investments at risk?
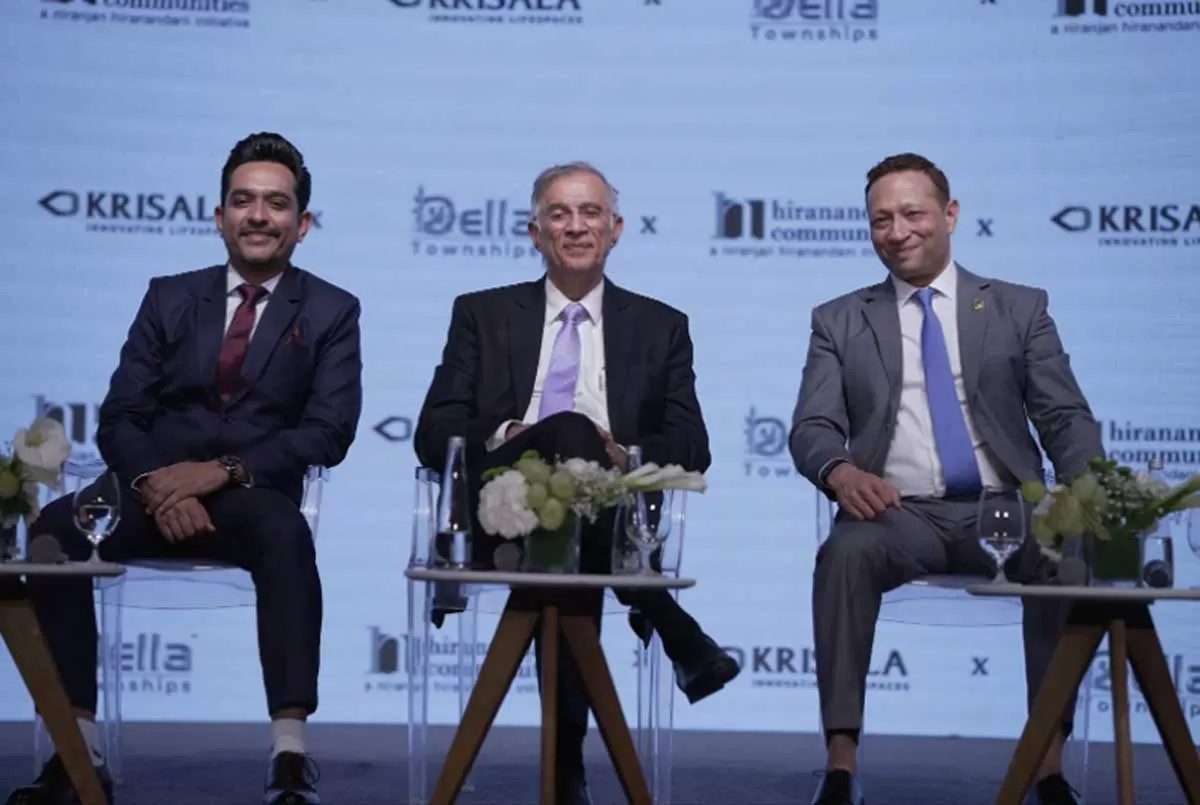
Della, Hiranandani & Krisala unveil Rs 11 billion themed township in Pune
In a first-of-its-kind initiative, Della Resorts & Adventure has partnered with Hiranandani Communities and Krisala Developers to develop a Rs 11 billion racecourse-themed township in North Hinjewadi, Pune. Based on Della’s proprietary CDDMO™ model, the hospitality-led, design-driven project aims to deliver up to 9 per cent returns—significantly higher than the typical 3 per cent in residential real estate.Spanning 40 acres within a 105-acre master plan, the mega township will feature an 8-acre racecourse and international polo club, 128 private villa plots, 112 resort residences, a ..
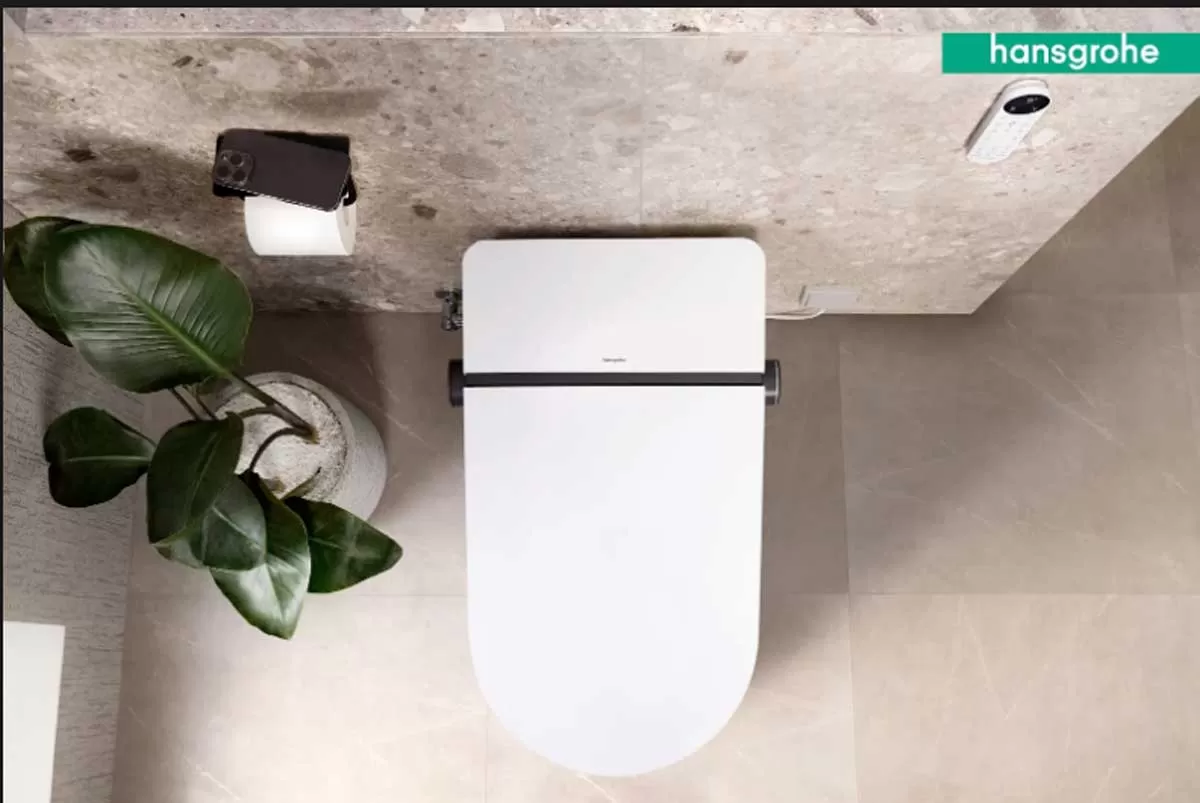
Hansgrohe unveils LavaPura Element S e-toilets in India
Hansgrohe India has launched its latest innovation, the LavaPura Element S e-toilet series, introducing a new standard in hygiene-focused, smart bathroom solutions tailored for Indian homes and high-end hospitality spaces.Blending German engineering with minimalist aesthetics, the LavaPura Element S combines intuitive features with advanced hygiene technology. The series is designed for easy installation and optimal performance under Indian conditions, reinforcing the brand’s focus on functional elegance and modern convenience.“With evolving consumer preferences, smart bathrooms are no lon..
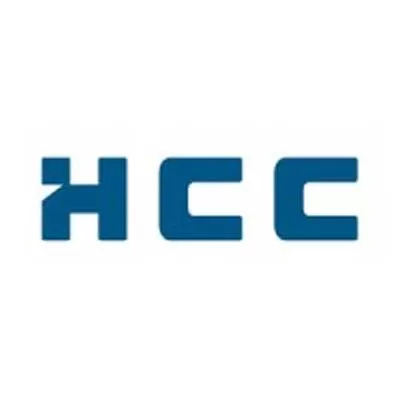
HCC Net Profit Stands at Rs 2.28 Billion for Q4 FY25
Hindustan Construction Company (HCC) reported a standalone net profit of Rs 2.28 billion in Q4 FY25, a sharp increase from Rs 388 million in Q4 FY24. Standalone revenue for the quarter stood at Rs 13.30 billion, compared to Rs 14.28 billion in Q4 FY24. For the full fiscal year, the company reported a standalone net profit of Rs 849 million, down from Rs 1.79 billion in FY24. Standalone revenue for FY25 was Rs 48.01 billion, compared to Rs 50.43 billion in the previous year.Consolidated revenue for Q4 FY25 stood at Rs 13.74 billion, and for FY25 at Rs 56.03 billion, down from Rs 17.73 billion i..