- Home
- Building Material
- Steel
- The Progress of the PEB
The Progress of the PEB
Over the years, several technological advancements have contributed to the growth of the Indian construction industry. Pre-engineered or prefab buildings (PEBs) are among the solutions that have had a significant impact. PEBs entered the Indian construction scenario in the late 1990s and have since emerged as a strong alternative to conventional concrete construction.
´The concept entered India in 1997-98 when a few PEBs were imported from the Middle East and installed in Greater Noida, Faridabad and Bengaluru.´ recalls Manish Garg, President & Chief Executive - Steel Building Business, Everest Industries Ltd. ´They were very expensive then. Later, in 1999-2000, indigenous manufacturing units were set up. Initially PEBs were used in warehousing and they later became the preferred choice for industrial buildings. Today, PEBs have wider applications in the industrial, infrastructure and institutional segments, with quality and design matching international standards.´
´There is hardly any difference between the products offered in India and worldwide,´ seconds Dr Greg Pasley, Vice President-Building Solutions, Tata BlueScope Steel Ltd. ´Design practices are similar, design codes and building codes are comparable, material specifications are alike, fabrication and erection tolerances are also compatible.
If there is any difference, it is in the channels to market them and the extent to which PEBs have penetrated construction applications. Compared to the developed world, they are still relatively new in India. As a result, awareness and acceptance is not the same. However, the Indian market is steadily moving away from conventional practices.´
Demand drivers
Massive infrastructure development, increasing popularity of PEB systems in the automotive, power and pharma sectors, and increasing emphasis on green building construction have all contributed to the growth of PEBs.
´Growth of the urban population and the government´s focus on infrastructure development together has accounted for the overall growth of the construction sector, which in turn has led to increasing demand for PEBs,´ states Amol Kotwal, Director, Energy & Environment Practice, Frost & Sullivan. ´Besides, with increasing focus on green buildings, PEBs have an inherent advantage over buildings set up through conventional methods as they comprise high recycled content and reduced greenhouse gas emissions owing to energy-efficient methods of steel production.´ Confirming this, PV Rao, Managing Director, Pennar Engineered Building Systems Ltd, says, ´With increasing awareness of the benefits of eco-friendly construction materials and construction methods, PEBs have become the preferred choice among architects, developers and industrialists, particularly in the industrial, commercial and office building sectors as well as retail stores, warehouses, airports and defence.´
This concept also gained acceptance owing to other factors like the opening up of the economy and a number of multinationals setting up their facilities, avers D Raju, Managing Director, Kirby Building Systems India Pvt Ltd. ´Changes in government regulations, industry-friendly policies and promotion of India as a preferred FDI destination resulting in heavy FDI inflows further boosted the industry,´ he says. ´Over the past seven years, many players have entered the PEB market and more are on the way. In the last decade, the industry has grown at an average of 15-20 per cent per annum.´
However, industry professionals concede that the industry, which witnessed buoyant growth in 2010 -2011, has been subdued in the past few years because of recession, drop in new investments, slump in the domestic market, weak exports and overall slowdown in the manufacturing, infrastructure and construction sectors. However, they were also hopeful that the PEB market, estimated to be around Rs 6,000 crore in terms of revenue in 2014, will gather momentum in the near future owing to improving investor sentiment and reforms announced by the new government.
Emerging effects
Indeed, PEBs come with umpteen benefits like easy and faster construction, quicker return on investment, assured quality and safety, ease of maintenance, design flexibility, eco-friendliness, and easy disassembly or future expansion.
With emerging awareness of the advantages, penetration levels have also been increasing.
´The industry is moving from warehouses and commercial buildings to highly complex pre-engineered sections in infrastructure such as ports and oil and gas utilities, which require specialized design skill sets,´ points out Raju. ´In addition, the quality of construction has improved significantly, project duration has become shorter and there is a special focus on safety standards. There is also a shift from in-site construction to factory-controlled, pre-engineered, high-quality construction. This has also changed the engineering, material and skill requirements of the construction industry.´
Rao too says that PEBs are steadily making inroads in construction and infrastructure projects across the country. ´The main segments are factory buildings, warehouses, retail supermarkets, aircraft hangers, power plants, commercial buildings and defence installations,´ he elaborates. ´This is largely because the PEB-based construction technique ensures efficient, cost-effective and speedy completion of projects. The penetration level, however, is low in the residential sector as the acceptance of a steel building (in place of an RCC building) in housing is yet to gain momentum in India.´
Opening opportunities
No doubt, PEBs have opened up huge opportunities for various sectors - from manufacturing, contracting and construction to engineering design and other allied industries. It has also opened the doors to international market opportunities for Indian players with the rising demand for PEBs world over. Future potential application areas include power plants, metros, airports, logistics, integrated townships and smart cities, to name a few.
Elaborating upon the opportunities, Rao says, ´Every sector, whether it is manufacturing, transport, energy, infrastructure or commodities, is growing at a greater pace and all of them require hi-tech buildings to run their business. On this score, PEB enjoys an edge over conventional construction owing to its many advantages. Also, today PEBs comprise only 10-15 per cent of the total industrial construction in the country compared to 95 per cent in the western world. In India, we expect a growth rate of 20-25 per cent year-on-year.´ He adds that with the government promoting the Swacch Bharat programme, even toilet buildings in schools could be an opportunity. ´According to the Ministry of Human Resource Development, of the total number of 1,094,431 schools in India, there are 253,674 schools without toilets and 164,980 schools with dysfunctional toilets,´ he says. ´Even if we expect 10 per cent of these to be in steel, the requirement will be huge.´
Garg also points out that PEB has primarily opened up huge opportunities for steel manufacturers. ´Today, the PEB industry has provided an opportunity to steel manufactures and others to scale up their capacities,´ he says. ´Any country´s GDP is directly proportional to growth in steel consumption.´ Meanwhile, Kotwal says the huge drivers for the industry in future will be logistics and retail. ´The new potential application areas in the next few years will include warehouses, power plants, offices, retail malls and metro stations. But the demand is expected to be driven by the logistics and retail sectors. Overall, there is huge potential for PEBs in India owing to robust economic growth, increased spending on infrastructure and change in mindset with regard to the use of PEB steel in building and other infrastructure segments.´
What´s more, the growth of the industry has opened up new doors to allied products, like drywalls for instance. As Hemant Khurana, Vice President-Sales & Marketing, Gyproc Division, Saint Gobain India, says, ´Gypsum plasterboard-based drywalls play a crucial role and add value to PEBs in reducing construction time and improving architectural versatility of several projects. They are 8 to 10 times lighter than traditional masonry construction systems, 30-40 per cent faster to install, provide excellent fire rating and acoustics, and are 100 per cent recyclable. Even industrial sectors where PEBs are widely used opt for drywalls. For instance, Cummins and Fiat have used drywalls extensively in their buildings.´ In fact, Delhi´s Dr Ram Manohar Lohia Hospital (DRML), a steel pre-engineered building, has used Saint Gobain´s drywall system in the wards and corridor areas.
Contributing challenges
Like any other industry, the PEB industry has its own challenges, like slow perception shift, sluggish demand, land issues, fluctuating steel prices, dearth of trained workforce, competition from the unorganized sector with questionable standards and high transportation costs.
´One of the main challenges faced is the acceptance level among Indian companies that is still moderate compared to developed economies,´ affirms Raju. ´But in the past decade, there has been increased acceptance of PEB owing to rapidly expanding industrialization. Other challenges include price volatility of raw material, mainly steel, and non-availability of skilled manpower.´
Kotwal agrees, saying, ´Some key challenges faced by PEB solution providers are fluctuating prices of steel, which constitutes almost 65-70 per cent of PEB cost, availability of skilled and trained manpower for PEB construction, transportation and logistics, and lack of quality standards.´
PEBs have a few other downsides to be tackled, like lower fire resistance compared to concrete unless fireproof coating is applied and the need for a protective coating to prevent corrosion of steel, all of which may increase overall fabrication costs appreciably. Further, there is a perception that PEBs are more expensive.
PEB manufacturers, though, beg to differ. ´The fact that the industry has grown by over 15-20 per cent in the first decade of this century in itself shows that these structures are not very expensive,´ asserts Raju. ´In some cases, where the area is large, PEBs are actually found to be less expensive than RCC buildings. Also, faster project completion will provide faster returns.´ Dr Pasley concurs, saying, ´A typical metal building costs less than a conventional structure. The maintenance requirements over the lifespan of the metal building are also likely to be lower.´
Reforms required
Nevertheless, industry professionals believe some measures are required to boost the industry, particularly from the government. ´The industry could be given infrastructure status as it was done initially,´ says Garg. ´Removing excise duty, which is currently 12.36 per cent, would also help.´ For his part, Raju recommends, ´The government should promote steel as construction material for speedy implementation of projects and to avoid cost overruns and project delays. The 100 smart cities planned by the government can be efficiently erected with pre-engineered steel as done in developed countries. Concessions in the form of tax incentives could also be extended for the steel construction industry.´
Some measures are also due from the manufacturer´s side, according to Dr Pasley. ´PEB solution providers should convince building owners that PEBs are a suitable solution to their needs,´ he reasons. ´Next, they must ensure that building design aligns with operational requirements and that the building is completed in a timely and safe manner. As more and more building owners experience the advantages of using PEBs, and the skill set across the value chain improves, the shift to metal buildings will increasingly gain momentum. This is why Tata BlueScope is focusing on building customer awareness through seminars, as well as training and development of our partners and vendors.´
Despite all the challenges and stumbling blocks, however, the industry is poised for a bright future, insists Raju. ´The Indian construction industry is poised for a big PEB wave given India´s renewed focus on infrastructure and the new industrial thrust,´ he says with optimism. ´The Central government´s recent approval of ordinance for amendment of the Land Acquisition Act will give a further boost as this was a major hurdle. These reforms and many other such initiatives promised by the government will make the Indian construction and infrastructure segments much stronger and consequently contribute to the growth of the PEB segment.´
PEB industry has opened up huge opportunities for steel manufacturers.´ - Manish Garg, President & Chief Executive-Steel Building Business, Everest Industries Ltd
A metal building costs less with lower maintenance requirements than conventional ones.´ - Dr Greg Pasley, Vice President-Building Solutions, Tata BlueScope Steel Ltd
PEBs are steadily making inroads in construction and infra projects across India.´ - PV Rao, Managing Director, Pennar Engineered Building Systems Ltd
PEBs have inherently green features in comparison to conventional methods.´ - Amol Kotwal, Director, Energy & Environment Practice, Frost & Sullivan
In some cases, using PEBs in large areas is actually cheaper than RCC buildings.´ - D Raju, Managing Director, Kirby Building Systems India Pvt Ltd
The usage of dry walls, as an allied product to PEBs, has also increased.´ - Hemant Khurana, Vice President-Sales & Marketing, Gyproc Division, Saint Gobain India
Case Study: 1
Project: Multimodal manufacturing facility in Chakan, Pune.
Client: GE India Industrial Pvt Ltd. Period: Mid-2013 to mid-2014.
PEB solution provider: Tata BlueScope Steel Ltd, Pune.
Consultant: CR Narayana Rao, Chennai. Project management consultant: Synefra Infrastructures Ltd.
Project size: 27,081 sq m. Brand: BUTLER« Building Systems.
Roof system: FM-approved MR-24« roof system with BR-IIÖ liner panel.
Special features:
100-metric tonne capacity crane and crane walkway and MEP cable trays.
Aluminium roof walkway with roof life line system.
Background: The plant was to manufacture different products ranging from aviation components and turbo machinery components to measurement and controls and wind turbines. GE was looking for an engineered steel building solution that would create a safe working environment while meeting all operational requirements.
Challenge: The height of building is 24 m; working at that height was identified as the critical risk by the Tata BlueScope Building Solutions (TBBS) team. The major measures taken to ensure safe erection included the following:
Planning and preparation: Three months prior to beginning site activities, the TBBS team identified critical safety requirements, prepared a ´Safe Work Method Statement´ for each activity and a Construction Environmental Health and Safety (EHS) plan. Some new policies like ´No Supervision - No Work´ and ´No Night Work´ were introduced. A risk assessment was undertaken for all activities with solutions to reduce risks. An Occupational Health and Safety hazard register and mitigation action plan were also prepared.
Design changes: At the concept stage, some changes were implemented in the standard product design for safe erection, like lifting holes in the primary members from POD lifting, additional holes and brackets in rafters for fixing lifeline posts around building periphery and standard lifeline posts designed by TBBS as well as a lifeline of steel wire rope.
Erection methodology: To ensure complete safety, working in a boom lift for all work at height, mandatory use of full body harness with double lanyard, and the SKY-WEB II fall protection system during roof liner panel installation were introduced. The use of hydra for material loading or unloading was disallowed and material stacking with height indicators was proposed. Other measures included tying up all tools to prevent fall, roof access staircase of British scaffolding type and an access control system during roof installation, and edge protection at the roof edge.
Work methods: Here are some of the key methods employed:
Most of the erection activity was carried out at ground level under POD erection methodology, where a 36-m-long POD containing four rafters was firmly fixed with purlins and lifted at one time.
A faster and safer method was devised to erect purlins using the crane and boom lift.
The complete canopy with roof sheeting was installed on the ground and then fixed in position with the help of cranes and boom lifts.
Strut pipe erection was done by using cranes and two boom lifts.
Painting touch-up at the ground level and at height was done with boom lifts only.
After installation of the MR-24« roof system, aluminum roof walkway with permanent roof lifeline system was installed to ensure safe access to the roof in future.
Conclusion: Detailed pre-execution EHS planning, effective use of risk-mitigation techniques, rigorous implementation of EHS tracker, erection supervision by a dedicated team, use of boom lifts, the SKY-WEB« II fall protection system, adoption of innovative construction techniques and TBSS´s zero-tolerance approach to safety violations resulted in completion of the GE project safely.
Case Study 2
Project: Stacker reclaimer buildings for coal, lime and additive in Bhilai
Client: ACC Ltd
Period: January 2014 to January 2015
PEB solution provider: Everest Industries Ltd
Area: Over 750,000 sq ft
Height: 24 m
Clear span: 60 m
Special features: One of the largest projects in the industry with 24-m height and 60-m clear span Challenge: Being one of the largest projects ever executed by a PEB company in this industry, it was a big challenge to ensure that every safety aspect was taken care of. Over 10 cranes and 24 boom lifts were used simultaneously to achieve this.
Other features: Special materials were used to paint the entire structure for barrier protection and to make it maintenance-free. Colour-coated galvalume roofing and cladding were used. The project was completed within 12 months from the date of PO involving design, engineering, approval, manufacturing, supply and on-site erection. If erected using conventional methods, such large spans would have taken over 18 months and with a cost at least 20 per cent higher.
- janaki krishnamoorthi
To share your views on the PEB & Prefab market, write in at feedback@ASAPPmedia.com
- Janaki Krishnamoorthi
- PEB
- Construction
- Manish Garg
- Everest Industries Ltd
- Dr Greg Pasley
- Tata BlueScope Steel Ltd
- Automotive
- Power
- Pharma
- Amol Kotwal
- Frost & Sullivan
- PV Rao
- Pennar Engineered Building Systems Ltd
- D Raju
- Kirby Building Systems India Pvt Ltd
- FDI,RCC building,Swacch Bharat programme
- GDP
- Hemant Khurana
- Saint Gobain India
- Cummins
- DRML
- GE India Industrial Pvt Ltd
- CR Narayana Rao
- MEP
- EHS
- Scaffolding
- SKY-WEB
- Naya Raipur Development Authority
- ACC Ltd
- Stacker
- Coal
- Lime
Owing to a host of benefits, PEBs are fast emerging as a credible and sustainable alternative to conventional concrete construction. Over the years, several technological advancements have contributed to the growth of the Indian construction industry. Pre-engineered or prefab buildings (PEBs) are among the solutions that have had a significant impact. PEBs entered the Indian construction scenario in the late 1990s and have since emerged as a strong alternative to conventional concrete construction. ´The concept entered India in 1997-98 when a few PEBs were imported from the Middle East and installed in Greater Noida, Faridabad and Bengaluru.´ recalls Manish Garg, President & Chief Executive - Steel Building Business, Everest Industries Ltd. ´They were very expensive then. Later, in 1999-2000, indigenous manufacturing units were set up. Initially PEBs were used in warehousing and they later became the preferred choice for industrial buildings. Today, PEBs have wider applications in the industrial, infrastructure and institutional segments, with quality and design matching international standards.´ ´There is hardly any difference between the products offered in India and worldwide,´ seconds Dr Greg Pasley, Vice President-Building Solutions, Tata BlueScope Steel Ltd. ´Design practices are similar, design codes and building codes are comparable, material specifications are alike, fabrication and erection tolerances are also compatible. If there is any difference, it is in the channels to market them and the extent to which PEBs have penetrated construction applications. Compared to the developed world, they are still relatively new in India. As a result, awareness and acceptance is not the same. However, the Indian market is steadily moving away from conventional practices.´ Demand drivers Massive infrastructure development, increasing popularity of PEB systems in the automotive, power and pharma sectors, and increasing emphasis on green building construction have all contributed to the growth of PEBs. ´Growth of the urban population and the government´s focus on infrastructure development together has accounted for the overall growth of the construction sector, which in turn has led to increasing demand for PEBs,´ states Amol Kotwal, Director, Energy & Environment Practice, Frost & Sullivan. ´Besides, with increasing focus on green buildings, PEBs have an inherent advantage over buildings set up through conventional methods as they comprise high recycled content and reduced greenhouse gas emissions owing to energy-efficient methods of steel production.´ Confirming this, PV Rao, Managing Director, Pennar Engineered Building Systems Ltd, says, ´With increasing awareness of the benefits of eco-friendly construction materials and construction methods, PEBs have become the preferred choice among architects, developers and industrialists, particularly in the industrial, commercial and office building sectors as well as retail stores, warehouses, airports and defence.´ This concept also gained acceptance owing to other factors like the opening up of the economy and a number of multinationals setting up their facilities, avers D Raju, Managing Director, Kirby Building Systems India Pvt Ltd. ´Changes in government regulations, industry-friendly policies and promotion of India as a preferred FDI destination resulting in heavy FDI inflows further boosted the industry,´ he says. ´Over the past seven years, many players have entered the PEB market and more are on the way. In the last decade, the industry has grown at an average of 15-20 per cent per annum.´ However, industry professionals concede that the industry, which witnessed buoyant growth in 2010 -2011, has been subdued in the past few years because of recession, drop in new investments, slump in the domestic market, weak exports and overall slowdown in the manufacturing, infrastructure and construction sectors. However, they were also hopeful that the PEB market, estimated to be around Rs 6,000 crore in terms of revenue in 2014, will gather momentum in the near future owing to improving investor sentiment and reforms announced by the new government. Emerging effects Indeed, PEBs come with umpteen benefits like easy and faster construction, quicker return on investment, assured quality and safety, ease of maintenance, design flexibility, eco-friendliness, and easy disassembly or future expansion. With emerging awareness of the advantages, penetration levels have also been increasing. ´The industry is moving from warehouses and commercial buildings to highly complex pre-engineered sections in infrastructure such as ports and oil and gas utilities, which require specialized design skill sets,´ points out Raju. ´In addition, the quality of construction has improved significantly, project duration has become shorter and there is a special focus on safety standards. There is also a shift from in-site construction to factory-controlled, pre-engineered, high-quality construction. This has also changed the engineering, material and skill requirements of the construction industry.´ Rao too says that PEBs are steadily making inroads in construction and infrastructure projects across the country. ´The main segments are factory buildings, warehouses, retail supermarkets, aircraft hangers, power plants, commercial buildings and defence installations,´ he elaborates. ´This is largely because the PEB-based construction technique ensures efficient, cost-effective and speedy completion of projects. The penetration level, however, is low in the residential sector as the acceptance of a steel building (in place of an RCC building) in housing is yet to gain momentum in India.´ Opening opportunities No doubt, PEBs have opened up huge opportunities for various sectors - from manufacturing, contracting and construction to engineering design and other allied industries. It has also opened the doors to international market opportunities for Indian players with the rising demand for PEBs world over. Future potential application areas include power plants, metros, airports, logistics, integrated townships and smart cities, to name a few. Elaborating upon the opportunities, Rao says, ´Every sector, whether it is manufacturing, transport, energy, infrastructure or commodities, is growing at a greater pace and all of them require hi-tech buildings to run their business. On this score, PEB enjoys an edge over conventional construction owing to its many advantages. Also, today PEBs comprise only 10-15 per cent of the total industrial construction in the country compared to 95 per cent in the western world. In India, we expect a growth rate of 20-25 per cent year-on-year.´ He adds that with the government promoting the Swacch Bharat programme, even toilet buildings in schools could be an opportunity. ´According to the Ministry of Human Resource Development, of the total number of 1,094,431 schools in India, there are 253,674 schools without toilets and 164,980 schools with dysfunctional toilets,´ he says. ´Even if we expect 10 per cent of these to be in steel, the requirement will be huge.´ Garg also points out that PEB has primarily opened up huge opportunities for steel manufacturers. ´Today, the PEB industry has provided an opportunity to steel manufactures and others to scale up their capacities,´ he says. ´Any country´s GDP is directly proportional to growth in steel consumption.´ Meanwhile, Kotwal says the huge drivers for the industry in future will be logistics and retail. ´The new potential application areas in the next few years will include warehouses, power plants, offices, retail malls and metro stations. But the demand is expected to be driven by the logistics and retail sectors. Overall, there is huge potential for PEBs in India owing to robust economic growth, increased spending on infrastructure and change in mindset with regard to the use of PEB steel in building and other infrastructure segments.´ What´s more, the growth of the industry has opened up new doors to allied products, like drywalls for instance. As Hemant Khurana, Vice President-Sales & Marketing, Gyproc Division, Saint Gobain India, says, ´Gypsum plasterboard-based drywalls play a crucial role and add value to PEBs in reducing construction time and improving architectural versatility of several projects. They are 8 to 10 times lighter than traditional masonry construction systems, 30-40 per cent faster to install, provide excellent fire rating and acoustics, and are 100 per cent recyclable. Even industrial sectors where PEBs are widely used opt for drywalls. For instance, Cummins and Fiat have used drywalls extensively in their buildings.´ In fact, Delhi´s Dr Ram Manohar Lohia Hospital (DRML), a steel pre-engineered building, has used Saint Gobain´s drywall system in the wards and corridor areas. Contributing challenges Like any other industry, the PEB industry has its own challenges, like slow perception shift, sluggish demand, land issues, fluctuating steel prices, dearth of trained workforce, competition from the unorganized sector with questionable standards and high transportation costs. ´One of the main challenges faced is the acceptance level among Indian companies that is still moderate compared to developed economies,´ affirms Raju. ´But in the past decade, there has been increased acceptance of PEB owing to rapidly expanding industrialization. Other challenges include price volatility of raw material, mainly steel, and non-availability of skilled manpower.´ Kotwal agrees, saying, ´Some key challenges faced by PEB solution providers are fluctuating prices of steel, which constitutes almost 65-70 per cent of PEB cost, availability of skilled and trained manpower for PEB construction, transportation and logistics, and lack of quality standards.´ PEBs have a few other downsides to be tackled, like lower fire resistance compared to concrete unless fireproof coating is applied and the need for a protective coating to prevent corrosion of steel, all of which may increase overall fabrication costs appreciably. Further, there is a perception that PEBs are more expensive. PEB manufacturers, though, beg to differ. ´The fact that the industry has grown by over 15-20 per cent in the first decade of this century in itself shows that these structures are not very expensive,´ asserts Raju. ´In some cases, where the area is large, PEBs are actually found to be less expensive than RCC buildings. Also, faster project completion will provide faster returns.´ Dr Pasley concurs, saying, ´A typical metal building costs less than a conventional structure. The maintenance requirements over the lifespan of the metal building are also likely to be lower.´ Reforms required Nevertheless, industry professionals believe some measures are required to boost the industry, particularly from the government. ´The industry could be given infrastructure status as it was done initially,´ says Garg. ´Removing excise duty, which is currently 12.36 per cent, would also help.´ For his part, Raju recommends, ´The government should promote steel as construction material for speedy implementation of projects and to avoid cost overruns and project delays. The 100 smart cities planned by the government can be efficiently erected with pre-engineered steel as done in developed countries. Concessions in the form of tax incentives could also be extended for the steel construction industry.´ Some measures are also due from the manufacturer´s side, according to Dr Pasley. ´PEB solution providers should convince building owners that PEBs are a suitable solution to their needs,´ he reasons. ´Next, they must ensure that building design aligns with operational requirements and that the building is completed in a timely and safe manner. As more and more building owners experience the advantages of using PEBs, and the skill set across the value chain improves, the shift to metal buildings will increasingly gain momentum. This is why Tata BlueScope is focusing on building customer awareness through seminars, as well as training and development of our partners and vendors.´ Despite all the challenges and stumbling blocks, however, the industry is poised for a bright future, insists Raju. ´The Indian construction industry is poised for a big PEB wave given India´s renewed focus on infrastructure and the new industrial thrust,´ he says with optimism. ´The Central government´s recent approval of ordinance for amendment of the Land Acquisition Act will give a further boost as this was a major hurdle. These reforms and many other such initiatives promised by the government will make the Indian construction and infrastructure segments much stronger and consequently contribute to the growth of the PEB segment.´ PEB industry has opened up huge opportunities for steel manufacturers.´ - Manish Garg, President & Chief Executive-Steel Building Business, Everest Industries Ltd A metal building costs less with lower maintenance requirements than conventional ones.´ - Dr Greg Pasley, Vice President-Building Solutions, Tata BlueScope Steel Ltd PEBs are steadily making inroads in construction and infra projects across India.´ - PV Rao, Managing Director, Pennar Engineered Building Systems Ltd PEBs have inherently green features in comparison to conventional methods.´ - Amol Kotwal, Director, Energy & Environment Practice, Frost & Sullivan In some cases, using PEBs in large areas is actually cheaper than RCC buildings.´ - D Raju, Managing Director, Kirby Building Systems India Pvt Ltd The usage of dry walls, as an allied product to PEBs, has also increased.´ - Hemant Khurana, Vice President-Sales & Marketing, Gyproc Division, Saint Gobain India Case Study: 1 Project: Multimodal manufacturing facility in Chakan, Pune. Client: GE India Industrial Pvt Ltd. Period: Mid-2013 to mid-2014. PEB solution provider: Tata BlueScope Steel Ltd, Pune. Consultant: CR Narayana Rao, Chennai. Project management consultant: Synefra Infrastructures Ltd. Project size: 27,081 sq m. Brand: BUTLER« Building Systems. Roof system: FM-approved MR-24« roof system with BR-IIÖ liner panel. Special features: 100-metric tonne capacity crane and crane walkway and MEP cable trays. Aluminium roof walkway with roof life line system. Background: The plant was to manufacture different products ranging from aviation components and turbo machinery components to measurement and controls and wind turbines. GE was looking for an engineered steel building solution that would create a safe working environment while meeting all operational requirements. Challenge: The height of building is 24 m; working at that height was identified as the critical risk by the Tata BlueScope Building Solutions (TBBS) team. The major measures taken to ensure safe erection included the following: Planning and preparation: Three months prior to beginning site activities, the TBBS team identified critical safety requirements, prepared a ´Safe Work Method Statement´ for each activity and a Construction Environmental Health and Safety (EHS) plan. Some new policies like ´No Supervision - No Work´ and ´No Night Work´ were introduced. A risk assessment was undertaken for all activities with solutions to reduce risks. An Occupational Health and Safety hazard register and mitigation action plan were also prepared. Design changes: At the concept stage, some changes were implemented in the standard product design for safe erection, like lifting holes in the primary members from POD lifting, additional holes and brackets in rafters for fixing lifeline posts around building periphery and standard lifeline posts designed by TBBS as well as a lifeline of steel wire rope. Erection methodology: To ensure complete safety, working in a boom lift for all work at height, mandatory use of full body harness with double lanyard, and the SKY-WEB II fall protection system during roof liner panel installation were introduced. The use of hydra for material loading or unloading was disallowed and material stacking with height indicators was proposed. Other measures included tying up all tools to prevent fall, roof access staircase of British scaffolding type and an access control system during roof installation, and edge protection at the roof edge. Work methods: Here are some of the key methods employed: Most of the erection activity was carried out at ground level under POD erection methodology, where a 36-m-long POD containing four rafters was firmly fixed with purlins and lifted at one time. A faster and safer method was devised to erect purlins using the crane and boom lift. The complete canopy with roof sheeting was installed on the ground and then fixed in position with the help of cranes and boom lifts. Strut pipe erection was done by using cranes and two boom lifts. Painting touch-up at the ground level and at height was done with boom lifts only. After installation of the MR-24« roof system, aluminum roof walkway with permanent roof lifeline system was installed to ensure safe access to the roof in future. Conclusion: Detailed pre-execution EHS planning, effective use of risk-mitigation techniques, rigorous implementation of EHS tracker, erection supervision by a dedicated team, use of boom lifts, the SKY-WEB« II fall protection system, adoption of innovative construction techniques and TBSS´s zero-tolerance approach to safety violations resulted in completion of the GE project safely. Case Study 2 Project: Stacker reclaimer buildings for coal, lime and additive in Bhilai Client: ACC Ltd Period: January 2014 to January 2015 PEB solution provider: Everest Industries Ltd Area: Over 750,000 sq ft Height: 24 m Clear span: 60 m Special features: One of the largest projects in the industry with 24-m height and 60-m clear span Challenge: Being one of the largest projects ever executed by a PEB company in this industry, it was a big challenge to ensure that every safety aspect was taken care of. Over 10 cranes and 24 boom lifts were used simultaneously to achieve this. Other features: Special materials were used to paint the entire structure for barrier protection and to make it maintenance-free. Colour-coated galvalume roofing and cladding were used. The project was completed within 12 months from the date of PO involving design, engineering, approval, manufacturing, supply and on-site erection. If erected using conventional methods, such large spans would have taken over 18 months and with a cost at least 20 per cent higher. - janaki krishnamoorthi To share your views on the PEB & Prefab market, write in at feedback@ASAPPmedia.com
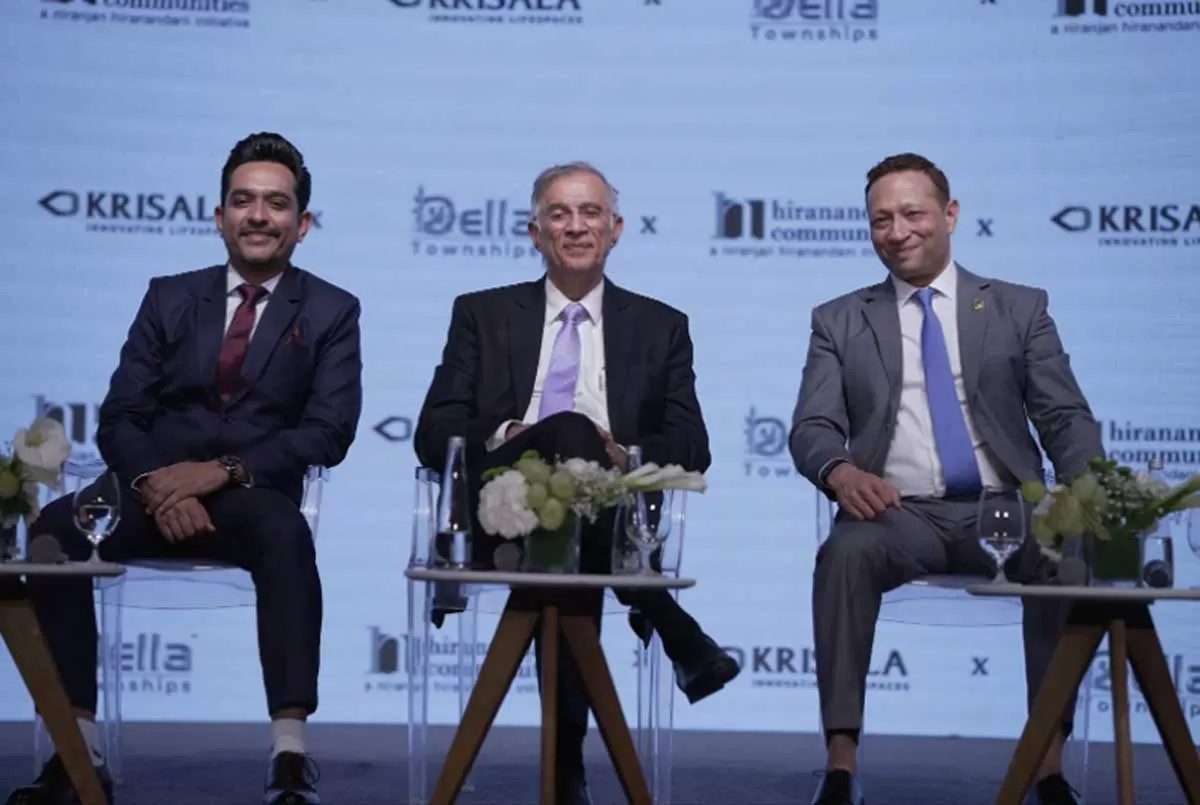
Della, Hiranandani & Krisala unveil Rs 11 billion themed township in Pune
In a first-of-its-kind initiative, Della Resorts & Adventure has partnered with Hiranandani Communities and Krisala Developers to develop a Rs 11 billion racecourse-themed township in North Hinjewadi, Pune. Based on Della’s proprietary CDDMO™ model, the hospitality-led, design-driven project aims to deliver up to 9 per cent returns—significantly higher than the typical 3 per cent in residential real estate.Spanning 40 acres within a 105-acre master plan, the mega township will feature an 8-acre racecourse and international polo club, 128 private villa plots, 112 resort residences, a ..
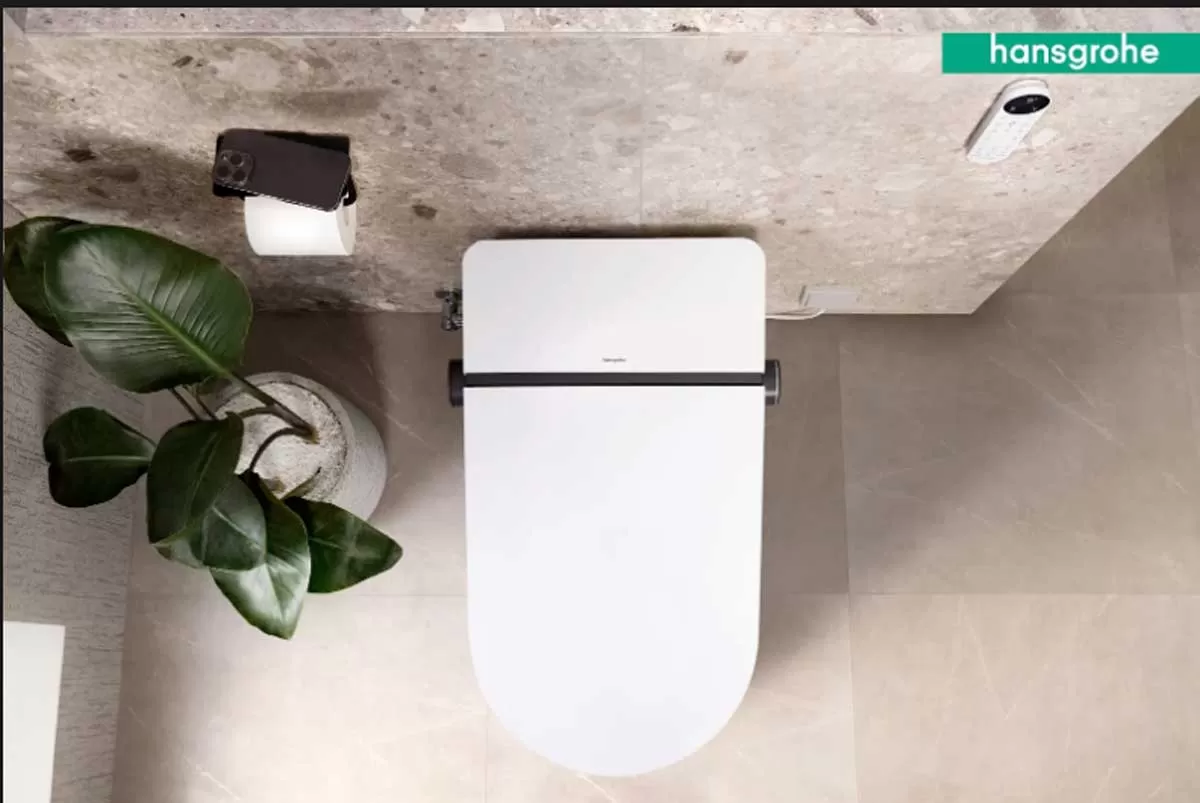
Hansgrohe unveils LavaPura Element S e-toilets in India
Hansgrohe India has launched its latest innovation, the LavaPura Element S e-toilet series, introducing a new standard in hygiene-focused, smart bathroom solutions tailored for Indian homes and high-end hospitality spaces.Blending German engineering with minimalist aesthetics, the LavaPura Element S combines intuitive features with advanced hygiene technology. The series is designed for easy installation and optimal performance under Indian conditions, reinforcing the brand’s focus on functional elegance and modern convenience.“With evolving consumer preferences, smart bathrooms are no lon..
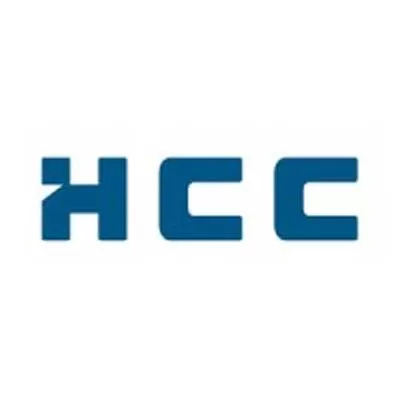
HCC Net Profit Stands at Rs 2.28 Billion for Q4 FY25
Hindustan Construction Company (HCC) reported a standalone net profit of Rs 2.28 billion in Q4 FY25, a sharp increase from Rs 388 million in Q4 FY24. Standalone revenue for the quarter stood at Rs 13.30 billion, compared to Rs 14.28 billion in Q4 FY24. For the full fiscal year, the company reported a standalone net profit of Rs 849 million, down from Rs 1.79 billion in FY24. Standalone revenue for FY25 was Rs 48.01 billion, compared to Rs 50.43 billion in the previous year.Consolidated revenue for Q4 FY25 stood at Rs 13.74 billion, and for FY25 at Rs 56.03 billion, down from Rs 17.73 billion i..
Latest Updates
Advertisement
Recommended for you
Advertisement
Subscribe to Our Newsletter
Get daily newsletters around different themes from Construction world.
Advertisement
Advertisement
Advertisement
subscribe to the newsletter
Don't miss out on valuable insights and opportunities
to connect with like minded professionals