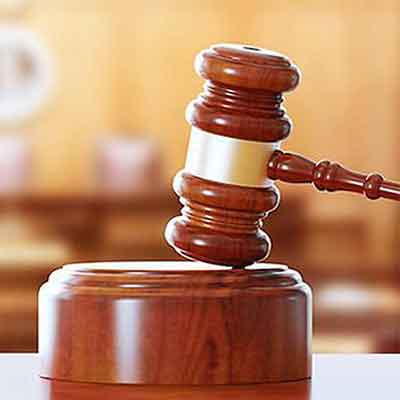
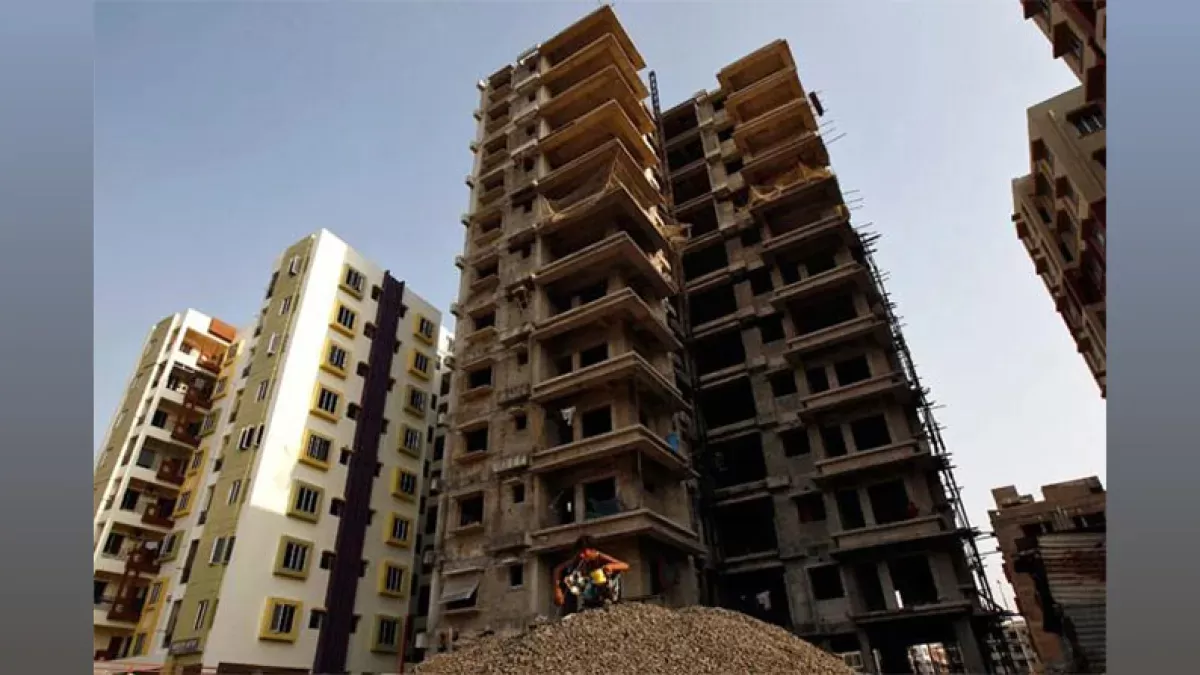
TRU Realty To Launch Rs 2.5 Billion Projects In Mumbai By 2025
TRU Realty, led by former Kolte-Patil CEO Sujay Kalele, is set to enter the Mumbai residential market with two premium housing projects in the Santacruz–Andheri corridor, scheduled for launch in September 2025.Spanning a combined 0.3 million sq ft, the developments involve an investment of Rs 2.5 billion and aim to generate Rs 4 billion in revenue by 2028. Strategically located near Juhu Beach, Andheri Railway Station, and Chhatrapati Shivaji International Airport, the projects are positioned to benefit from limited land availability and strong demand in the city’s high-end housing segment..
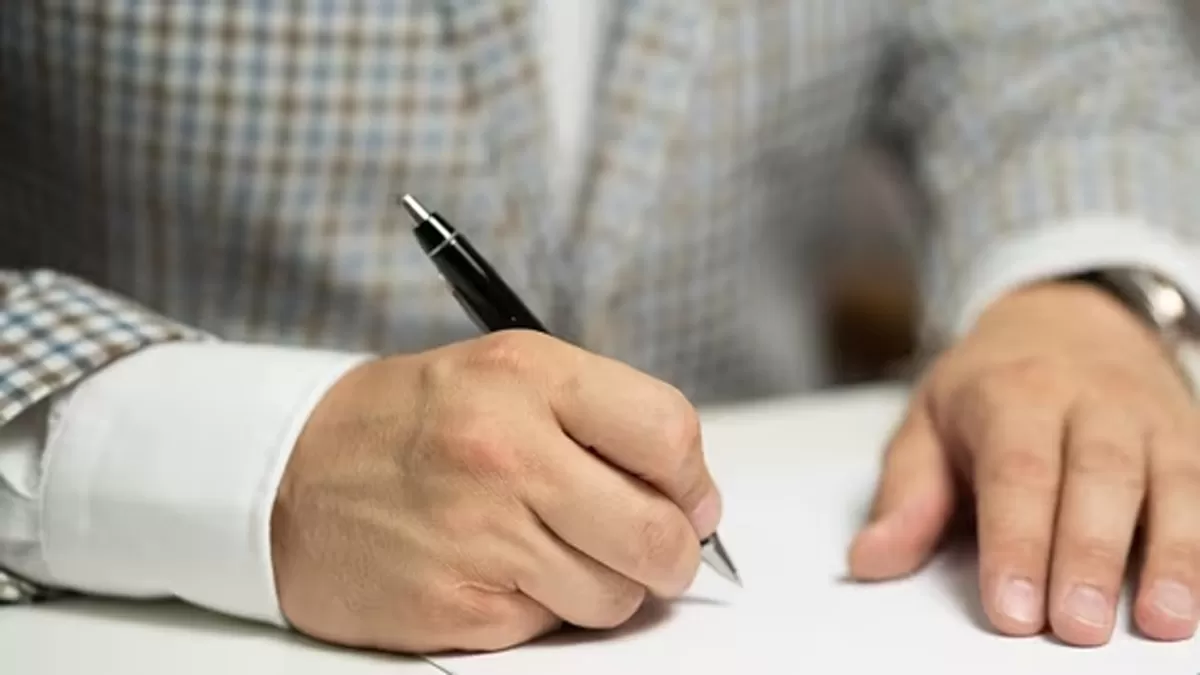
DRA Group, Philippines’ Balajadia Ink $100 Million Commercial JV
Chennai-based real estate firm DRA Group has partnered with Philippines-based Balajadia Family Office to jointly develop a commercial project worth $100 million. The collaboration marks a strategic cross-border alliance between the two companies, aimed at delivering premium commercial and retail spaces in India.Under Phase 1, the venture will develop one million square feet of Grade-A office and retail facilities. The partnership was formalised through a Memorandum of Understanding (MoU) signed at the Philippines–India Business Forum in Bengaluru.The equal joint venture will be executed via ..
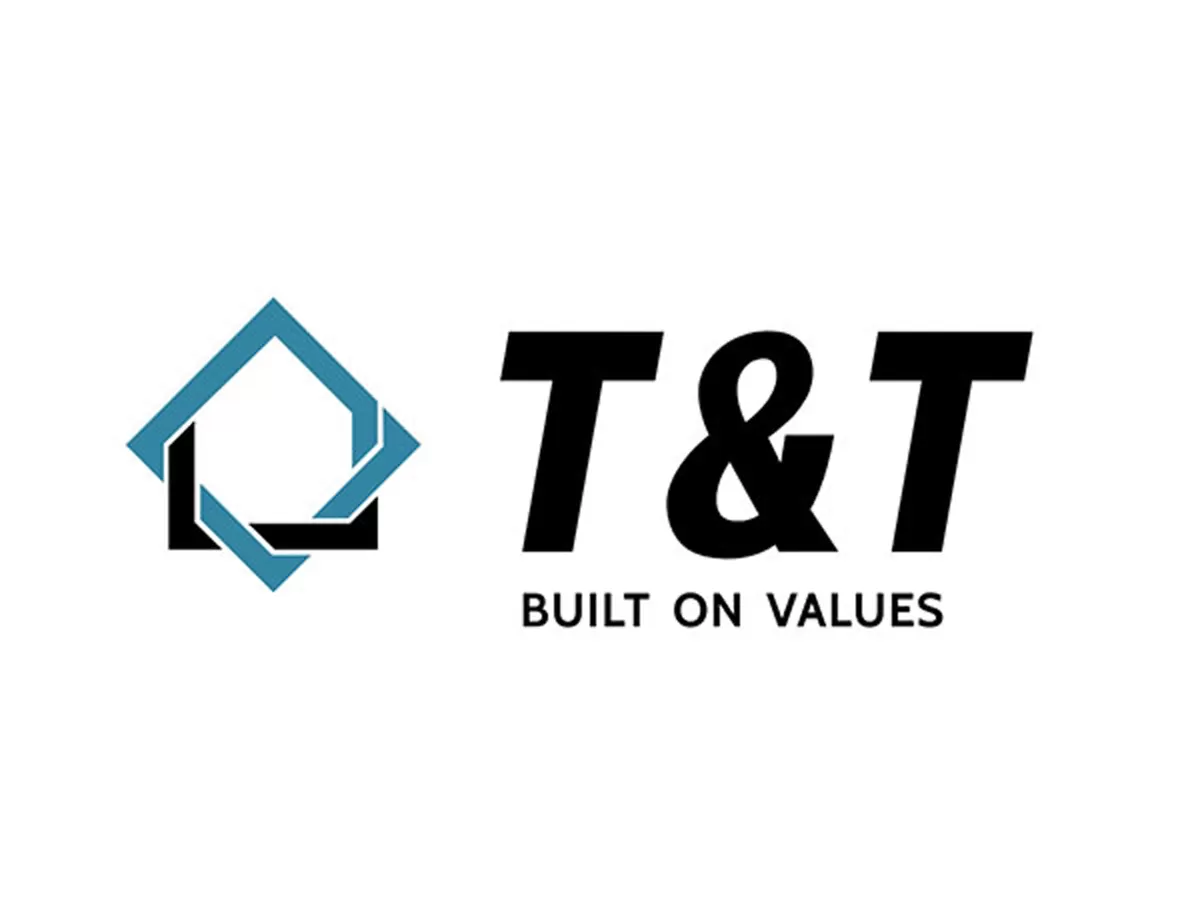
T & T To Launch Rs 7 Billion Luxury Housing In Raj Nagar Extension
Raj Nagar Extension, long known for its affordability, is poised for a transformation as T & T Group prepares to launch a luxury housing project valued at Rs 7 billion. The development is expected to significantly boost the company’s market share in the premium residential segment.Spread across 3.25 acres, the project will feature over one million square feet of built-up area, offering 3 and 4 BHK apartments in Ground + 16-storey towers. Inspired by Victorian and Tudor architecture, the design blends classic elegance with modern comfort.Unlike most housing in the area, which has prioriti..