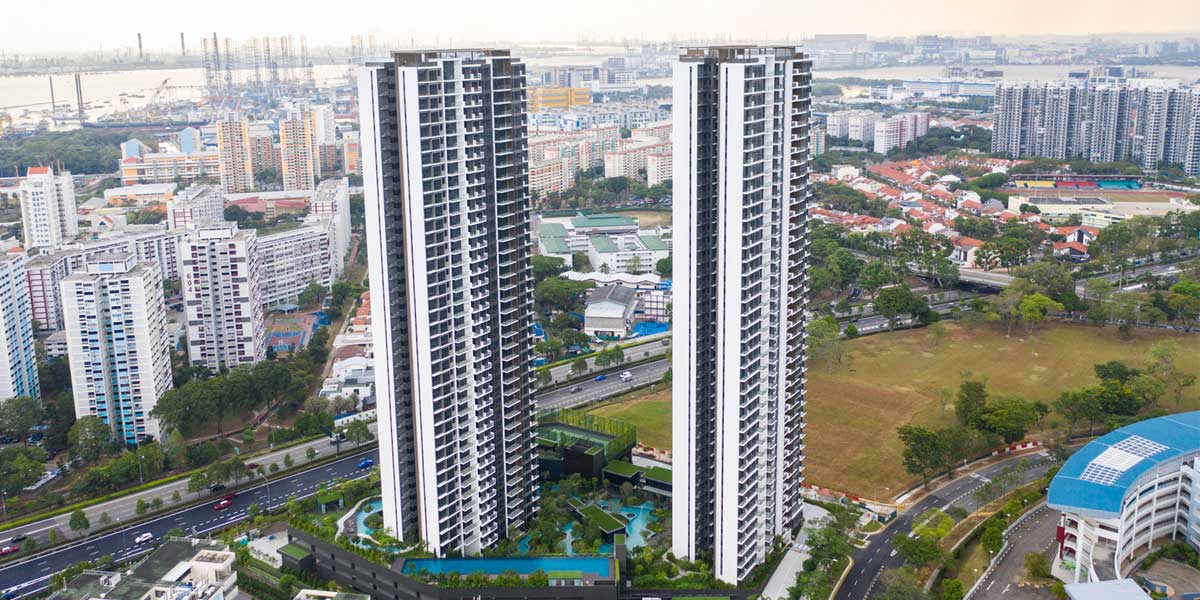
Standing Tall
04 Sep 2020
5 Min Read
Editorial Team
It’s a new record! Built by construction company Bouygues Bâtiment International,Clement Canopy, a pair of 140-mtowers made of prefabricated concrete modules, has set a new benchmark as the tallest modular building in the world. Previously, the title was held by 101 George Street, a 135-m tower b...
Read full article
Try CW Gold Subscription at 167/Month
CW Gold Benefits
- Weekly Industry Updates
- Industry Feature Stories
- Premium Newsletter Access
- Building Material Prices (weekly) + trends/analysis
- Best Stories from our sister publications - Indian Cement Review, Equipment India, Infrastructure Today
- Sector focused Research Reports
- Sector Wise Updates (infrastructure, cement, equipment & construction) + trend analysis
- Exclusive text & video interviews
- Digital Delivery
- Financial Data for publically listed companies + Analysis
- Preconceptual Projects in the pipeline PAN India