- Home
- Real Estate
- Fabricating strength
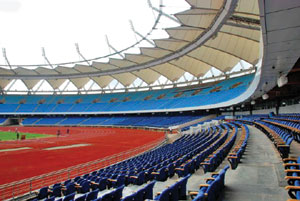
Fabricating strength
Architecture is not just about creating concrete building masses but an environment. With this belief, Manish Jain, DGM (Architecture), Rudrabhishek Enterprises Pvt Ltd, continues to define the term environment by creating a variety of dynamic spaces. "Each space has an identity and soul of its own," he says. Semi-covered, covered and open spaces are easily planned and balanced with a view of the required form and other elements of interest. One such important architectural element is the roof. It defines the scale, proportion, character and overall ambience of the designed space. But where traditional roofs do not have the flexibility of taking any shape, tensile roofs can be designed to various organic shapes that lend fluidity to the space.
While he avers that the industry is not fully aware of the potential tensile textile fabrics hold, he shares its benefits in conversation with Shriyal Sethumadhavan.
The fabrication process
Modular tensile membrane structures are manufactured and erected in workshops and subsequently transported to their final destinations in large containers. These are composed of multiple sections or modules where all the materials and fabrics are assembled. These are further carried on to site and moulded according to the design to form a complete structure. They are easy to install and dismantle and hence can cover a vast area in a short span of time. The most common modular shapes include hypar, cones, barrel vaults, pole tents, pagoda and double vault.
Where it began
While they gained popularity worldwide in 1960s, tensile structures have been around for more than a century. In India, they have been prevalent since the past 10-15 years. The upgraded Jawaharlal Nehru Stadium in New Delhi also has a tensile structure that spans the gallery area of the stadium. They have been used in the Commonwealth Village as well. Other areas of application include car parks, landscaping and entrance areas.
Materials involved
Traditionally, people used polycarbonate and fibre sheets. But in the case of tensile structures, essentially two types of tensile fabric materials are employed. One is polyester-based PVC fabrics, further classified on the basis of their coating; PVC with acrylic coating is widely used in India. Another type is poly tetra fluoro ethylene-coated fibreglass (PTFE). Here, a glass fibre yarn is woven into a fabric. So the basic material in any case is the fabric, which is further coated for the required quality. The coating decides the life of the structure. In the case of PVC coating, the material can last up to 15 years. However, in comparison, the fibreglass type material has a longer life of 25 to 30 years. Hence, for permanent structures like stadiums or to cover galleries, we definitely recommend the use of fibreglass-type materials. Also, while PVC coating is suitable for all weathers, fibreglass has higher retardant features and tensile strength. But despite being more durable compared to PVC, this fabric is not widely used in India. A prime reason is its cost, which is nearly 2.5 times that of PVC.
Uses and applications
Tensile textile fabrics are primarily used in public and semi-public spaces. They can be used in a variety of ways in landscape design such as gazebos. They may also be used to define car parks, entrances and walkways, span larger areas such as stadiums, food courts, atriums, malls, swimming pools, warehouses and aircraft hangers. As for stadiums, some famous examples worldover include Olympic Stadium in Munich, Sidney Myer Bowl in Melbourne, Millennium Dome, etc.
In the case of covering vast open spaces, these lightweight materials make construction easier and cheaper than standard designs.
In the present day, we have proposed tensile structures in REPL's Auto Mall in Lucknow. Based on a unique concept of bringing the automobile industry together under a single roof, the project has been conceptualised in the form of retail towers designed around a central activity area, which will comprise brand promotions, events, etc. For this area, we have proposed a tensile fabric structure for the roof to give it a light and soft feel when juxtaposed against glass showrooms. This will give it an artistic, architectural expression and provide protection against weather and sunlight.
The properties
In a tensile structure, every part is loaded in tension, with no requirement to resist compression or bending forces. Tensile fabric being one of the key components of a tensile structure, the kind of material used depends on the structure's design, durability, aesthetic appeal, and location requirements for the application. With the use of exceptional quality fabric materials, we can create structures and forms that were not possible earlier. Commonly known as tensile fabric structures, these products are also referred to as tension membrane structures, architectural membrane structures and fabric structures, etc. Moreover, they are of two kinds: synclastic or anticlastic.
Anticlastic structures are puretensile surfaces having a curvature at a given point and in a particular direction, which is of the opposite sign to the curvature at that point in a perpendicular direction. In short, they are defined by two curvatures. Synclastic structures are air-supported surfaces with a curvature at a given point and in a particular direction that is of the same sign as the curvature at that point in the perpendicular direction. For such air-supported structures, the fabric envelope is supported by pressurised air but most fabrics derive their strength from their double curved shape.
Good returns
The chief advantages of this material include dispersing natural light with condensed heat load, allowing higher light transmission during daytime (sufficient to reduce artificial lighting requirement from 5 per cent to 20 per cent), absorbing solar energy, and reducing heat load. Also, compared to a material like glass, which is used for similar applications, it also requires low maintenance. On site, there are minimal interruptions as the membrane structures are manufactured in factories. Also, there are no extension joints as the membrane structures are welded into a single weatherproof skin. These are designed for rapid construction and easy installation.
Also, as this material is flexible, it can be explored to cover larger areas like food courts or any sort of landscape, culture garden, etc.
Moreover, tensile textile fabrics can help form atriums in different shapes. An architect may want to interplay with spaces, which is a very soulful thing while designing any project. Further, these fabrics are energy-efficient, hence, a qualifying material for a green project. They absorb heat, further reducing the heat load of a building, and transmit some light. Hence, during the day, you need not depend on artificial light.
Other alternatives to tensile structures are polycarbonate roofs or glass roof glazing systems. However, the forms these can take are limited in comparison to tensile structures, which can create more exciting and organic forms.
The shortcomings
Most fabric structures face the wicking problem, i.e. water seeping into the length of the thread lines of the fabric. This leads to discoloration of the fabric and probable de-lamination. So there can be damages, but mainly in areas of snowfall and heavy rainfall. The solution to this lies primarily in the design and shape given.
And second, choosing the right material in areas with tough weather conditions, the fibreglass type will last for many more years compared to PVC. However, in case of damage, these can also be easily repaired.
The affordability quotient
The materials and the structure are quite affordable as the cost of the fabric is not significant. The main cost lies in the mounting system. However, this will always vary depending on the type of fabric, design and many such factors. At times, we have faced opposition - budget being an issue - and have been restricted to canopies and parking areas. Although the choice of the material purely depends on the client and budgets, if asked to choose, I would select fibreglass. Undoubtedly, in terms of availability, PVC is easily available in India; 95 per cent of textile structures are PVC-based.
Fibreglass, owing to limited usage, is not easily available. Hence, there is an urgent need for awareness, followed by acceptability. But for this, we need to have some landmark structures built with this material to create awareness. And we, as part of the construction and building fraternity, should take the onus. For my part, I look forward to a positive future where tensile textile fabrics will gain their true identity in India.
Share your construction material with us at feedback@ASAPPmedia.com
In the next in a series of features showcasing building materials, Manish Jain, DGM (Architecture), Rudrabhishek Enterprises Pvt Ltd, touches upon the benefits and need for tensile textile fabrics in India. Architecture is not just about creating concrete building masses but an environment. With this belief, Manish Jain, DGM (Architecture), Rudrabhishek Enterprises Pvt Ltd, continues to define the term environment by creating a variety of dynamic spaces. "Each space has an identity and soul of its own," he says. Semi-covered, covered and open spaces are easily planned and balanced with a view of the required form and other elements of interest. One such important architectural element is the roof. It defines the scale, proportion, character and overall ambience of the designed space. But where traditional roofs do not have the flexibility of taking any shape, tensile roofs can be designed to various organic shapes that lend fluidity to the space. While he avers that the industry is not fully aware of the potential tensile textile fabrics hold, he shares its benefits in conversation with Shriyal Sethumadhavan. The fabrication process Modular tensile membrane structures are manufactured and erected in workshops and subsequently transported to their final destinations in large containers. These are composed of multiple sections or modules where all the materials and fabrics are assembled. These are further carried on to site and moulded according to the design to form a complete structure. They are easy to install and dismantle and hence can cover a vast area in a short span of time. The most common modular shapes include hypar, cones, barrel vaults, pole tents, pagoda and double vault. Where it began While they gained popularity worldwide in 1960s, tensile structures have been around for more than a century. In India, they have been prevalent since the past 10-15 years. The upgraded Jawaharlal Nehru Stadium in New Delhi also has a tensile structure that spans the gallery area of the stadium. They have been used in the Commonwealth Village as well. Other areas of application include car parks, landscaping and entrance areas. Materials involved Traditionally, people used polycarbonate and fibre sheets. But in the case of tensile structures, essentially two types of tensile fabric materials are employed. One is polyester-based PVC fabrics, further classified on the basis of their coating; PVC with acrylic coating is widely used in India. Another type is poly tetra fluoro ethylene-coated fibreglass (PTFE). Here, a glass fibre yarn is woven into a fabric. So the basic material in any case is the fabric, which is further coated for the required quality. The coating decides the life of the structure. In the case of PVC coating, the material can last up to 15 years. However, in comparison, the fibreglass type material has a longer life of 25 to 30 years. Hence, for permanent structures like stadiums or to cover galleries, we definitely recommend the use of fibreglass-type materials. Also, while PVC coating is suitable for all weathers, fibreglass has higher retardant features and tensile strength. But despite being more durable compared to PVC, this fabric is not widely used in India. A prime reason is its cost, which is nearly 2.5 times that of PVC. Uses and applications Tensile textile fabrics are primarily used in public and semi-public spaces. They can be used in a variety of ways in landscape design such as gazebos. They may also be used to define car parks, entrances and walkways, span larger areas such as stadiums, food courts, atriums, malls, swimming pools, warehouses and aircraft hangers. As for stadiums, some famous examples worldover include Olympic Stadium in Munich, Sidney Myer Bowl in Melbourne, Millennium Dome, etc. In the case of covering vast open spaces, these lightweight materials make construction easier and cheaper than standard designs. In the present day, we have proposed tensile structures in REPL's Auto Mall in Lucknow. Based on a unique concept of bringing the automobile industry together under a single roof, the project has been conceptualised in the form of retail towers designed around a central activity area, which will comprise brand promotions, events, etc. For this area, we have proposed a tensile fabric structure for the roof to give it a light and soft feel when juxtaposed against glass showrooms. This will give it an artistic, architectural expression and provide protection against weather and sunlight. The properties In a tensile structure, every part is loaded in tension, with no requirement to resist compression or bending forces. Tensile fabric being one of the key components of a tensile structure, the kind of material used depends on the structure's design, durability, aesthetic appeal, and location requirements for the application. With the use of exceptional quality fabric materials, we can create structures and forms that were not possible earlier. Commonly known as tensile fabric structures, these products are also referred to as tension membrane structures, architectural membrane structures and fabric structures, etc. Moreover, they are of two kinds: synclastic or anticlastic. Anticlastic structures are puretensile surfaces having a curvature at a given point and in a particular direction, which is of the opposite sign to the curvature at that point in a perpendicular direction. In short, they are defined by two curvatures. Synclastic structures are air-supported surfaces with a curvature at a given point and in a particular direction that is of the same sign as the curvature at that point in the perpendicular direction. For such air-supported structures, the fabric envelope is supported by pressurised air but most fabrics derive their strength from their double curved shape. Good returns The chief advantages of this material include dispersing natural light with condensed heat load, allowing higher light transmission during daytime (sufficient to reduce artificial lighting requirement from 5 per cent to 20 per cent), absorbing solar energy, and reducing heat load. Also, compared to a material like glass, which is used for similar applications, it also requires low maintenance. On site, there are minimal interruptions as the membrane structures are manufactured in factories. Also, there are no extension joints as the membrane structures are welded into a single weatherproof skin. These are designed for rapid construction and easy installation. Also, as this material is flexible, it can be explored to cover larger areas like food courts or any sort of landscape, culture garden, etc. Moreover, tensile textile fabrics can help form atriums in different shapes. An architect may want to interplay with spaces, which is a very soulful thing while designing any project. Further, these fabrics are energy-efficient, hence, a qualifying material for a green project. They absorb heat, further reducing the heat load of a building, and transmit some light. Hence, during the day, you need not depend on artificial light. Other alternatives to tensile structures are polycarbonate roofs or glass roof glazing systems. However, the forms these can take are limited in comparison to tensile structures, which can create more exciting and organic forms. The shortcomings Most fabric structures face the wicking problem, i.e. water seeping into the length of the thread lines of the fabric. This leads to discoloration of the fabric and probable de-lamination. So there can be damages, but mainly in areas of snowfall and heavy rainfall. The solution to this lies primarily in the design and shape given. And second, choosing the right material in areas with tough weather conditions, the fibreglass type will last for many more years compared to PVC. However, in case of damage, these can also be easily repaired. The affordability quotient The materials and the structure are quite affordable as the cost of the fabric is not significant. The main cost lies in the mounting system. However, this will always vary depending on the type of fabric, design and many such factors. At times, we have faced opposition - budget being an issue - and have been restricted to canopies and parking areas. Although the choice of the material purely depends on the client and budgets, if asked to choose, I would select fibreglass. Undoubtedly, in terms of availability, PVC is easily available in India; 95 per cent of textile structures are PVC-based. Fibreglass, owing to limited usage, is not easily available. Hence, there is an urgent need for awareness, followed by acceptability. But for this, we need to have some landmark structures built with this material to create awareness. And we, as part of the construction and building fraternity, should take the onus. For my part, I look forward to a positive future where tensile textile fabrics will gain their true identity in India. Share your construction material with us at feedback@ASAPPmedia.com