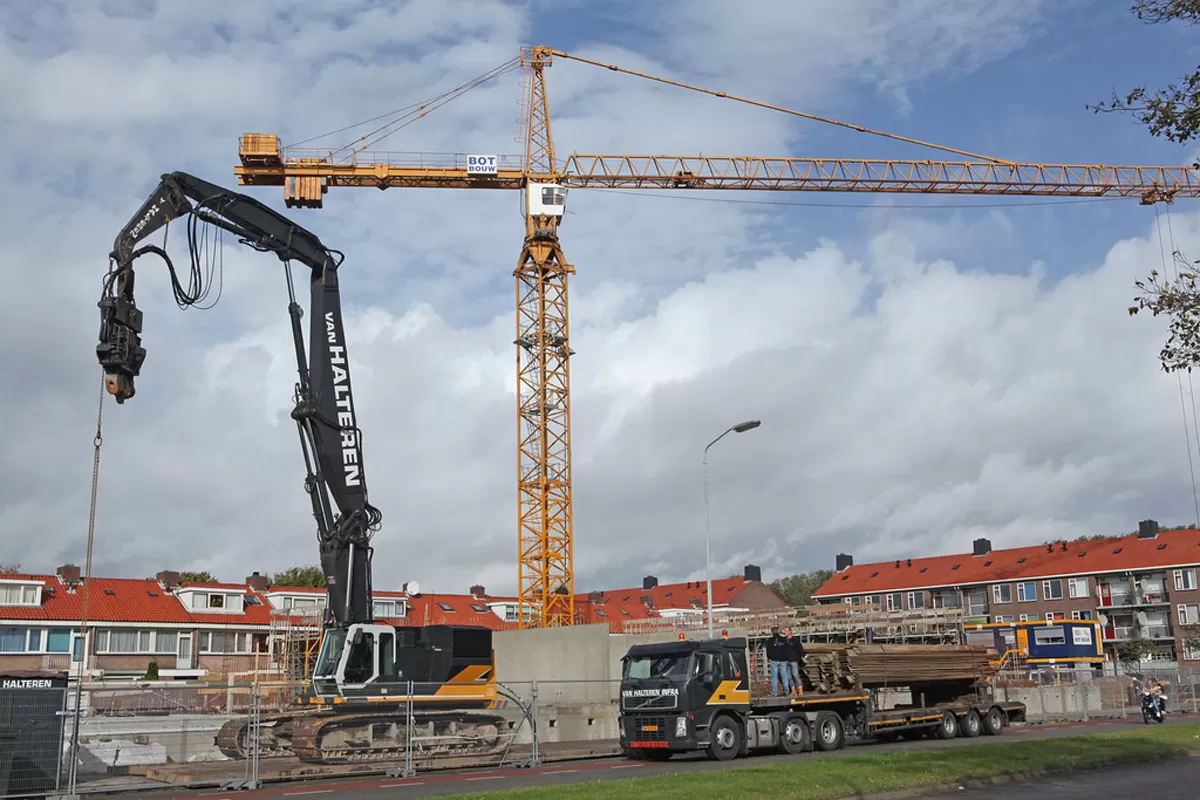
CRDA Approves Rs 17.32 Bn Tenders for Housing and Infra
The Capital Region Development Authority (CRDA), during its forty-seventh meeting chaired by Chief Minister N. Chandrababu Naidu, approved tenders worth Rs 17.32 billion to develop key infrastructure in Amaravati’s core capital area.Municipal Administration and Urban Development Minister Ponguru Narayana announced that Rs 5.14 billion was sanctioned for completing gazetted officers’ towers initiated between 2014 and 2019. In addition, Rs 1.94 billion was approved for external infrastructure, Rs 5.07 billion for nine towers for non-gazetted employees, and Rs 5.17 billion for twelve new towe..
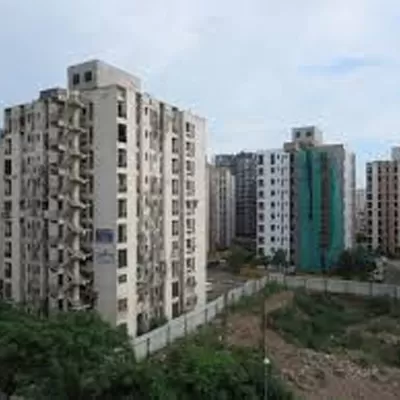
Prestige Estates Nets Rs 30 Bn in NCR Debut Launch
Prestige Estates Projects Limited has recorded sales of over Rs 30 billion within one week of launching its first residential project in the National Capital Region (NCR). The project, The Prestige City, located in Indirapuram Extension on National Highway twenty-four, sold one thousand two hundred units during its initial launch phase.This marks the Bengaluru-based developer’s maiden entry into NCR’s residential real estate market. The company attributes the strong response to brand trust, strategic location, and rising demand for premium, planned communities.The launch covered two reside..
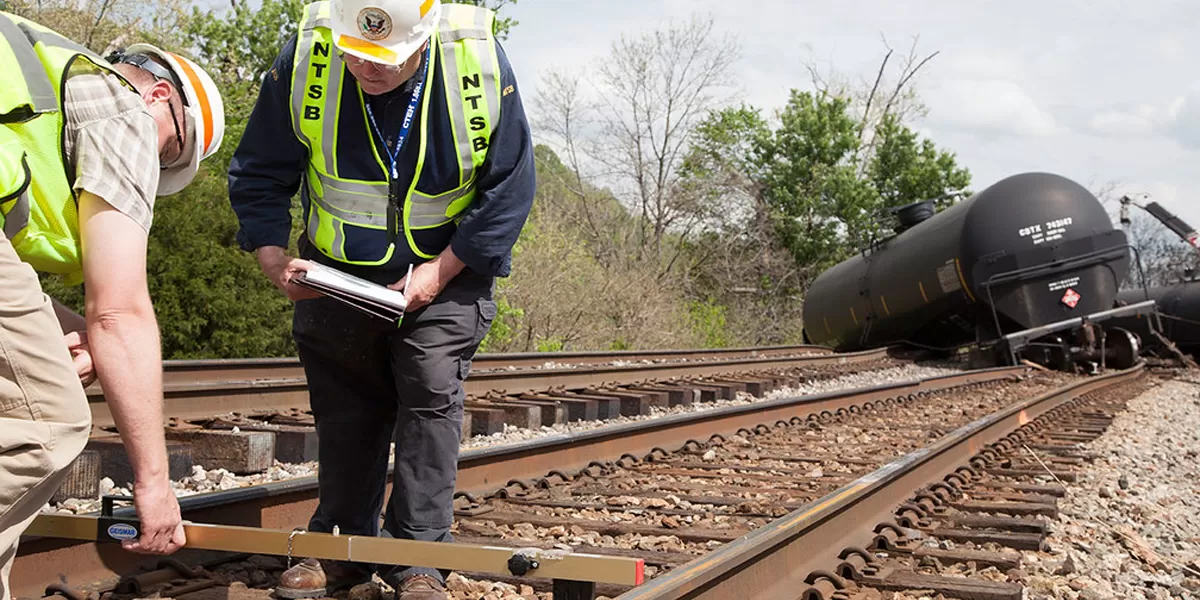
Palakkad Railway Division Upgrades Turnouts for Safety
The Southern Railway’s Palakkad Division has implemented a series of infrastructure upgrades to enhance train safety and operational efficiency. Over the past one year, the division has replaced one hundred thirty-three ageing fifty-two kilogram turnouts with robust sixty kilogram Thick Web Switches, engineered for high-speed durability and increased strength.Seventy-seven track layouts were corrected using advanced computer-based geometry solutions, involving precise longitudinal and lateral alignment with the aid of the T-28 Track Relaying Machine. These corrections improve track stability..