- Home
- Real Estate
- Quick Fix
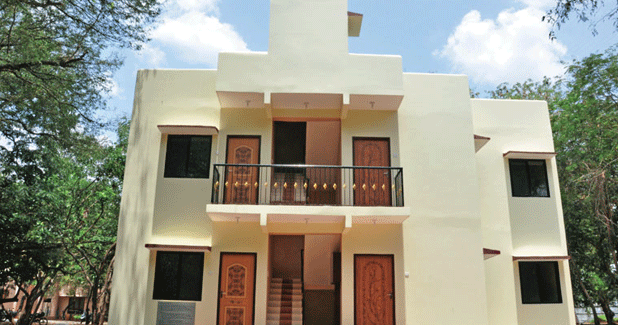
Quick Fix
IIT-Madras is playing host to a house on campus made with Rapidwall technology. Such panel-made houses have been adopted by many countries; in India, IIT-M is the pioneer. Innovation comes through by researching and trying to match needs, believes Prof Meher Prasad, HOD, Civil Engineering, IIT-Madras, as he elaborates on the process of rapid construction and its benefits.
The beginning
Rapidwall panels were developed by RBS Australia for rapid erection of walls in buildings to carry gravity loads. These panels are 12 m long, 3 m high and 124 mm thick with hollow cavities. The technology uses industrial waste gypsum and glass fibres in hollow panels, called glass fibre-reinforced gypsum (GFRG) panels. The demo building in the IIT-M campus comprises four flats in two storeys and was built within a month. The wall panels are integrated to provide more load carrying capacity for structural efficiency. The superstructure of GFRG construction is entirely based on prefabricated panels. The procedure mainly includes fixing wall panels and roof panels using mechanical means, preferably a crane, and filling the required joints with reinforced cement concrete as per structural design.
Construction process
The foundation used in this construction is conventional. It depends on the soil condition of the particular site and the number of storeys of the structure. Generally, strip footing is used as the superstructure consists of load bearing walls. The following steps are involved in the construction:
- Excavation of earth.
- Levelling or ramming of base.
- Laying of PCC.
- Waterproofing layer over the entire PCC.
- Footing (generally strip, but varies according to building type, size and soil conditions).
- Waterproofing on three sides (exposed sides of footing and plinth beam).
- Plinth beam over the footing with start-up rods from foundation for connectivity of building with foundation.
- Filling inner depressions in footing. using excavated earth and ramming it well.
- Filling up the top with quarry dust (or any inert waste material) 200 mm thick.
- Laying of PCC layer (100 mm) over the filled up area upto plinth beam top.
- Final layer of waterproofing over the entire floor area.
- The process is more complicated than conventional construction but material consumption comes down. It is not more difficult than precast.
Success meter
The demo building was constructed at a finished cost of Rs 1,250 per sq ft. It has attracted a lot of visitors. We are trying to scale up a large number of flats. You get dimensional accuracy if you follow the principles of modularity. Some individual houses have already been constructed. Kerala housing has taken up a three-storey building; some of these buildings have already been executed. Currently there are only two plants that can produce 1.5 million sq m, one at Rashtriya Chemicals & Fertilizers (RCF) in Mumbai, and another at FACT, Kochi. We hope big players will come into the picture in the near future. As we have just two plants manufacturing the panels, transportation costs will add up if the construction site is not near these plants. A fit-to-stay house can be prepared within a week once the ground floor is constructed.
Countless benefits
The structural cost is reduced by 20 per cent. The taller the building, more the benefits. Efficient use brings down consumption. In the slab, there is a 50-mm gap to be filled with concrete. Even without concrete, it can take 16 tonne per m. Gypsum and water do not go together and the calcination and formulation process helps this. Because of the glass fibre, more strength is added to the panels. The waterless formulation of these panels makes it waterproof. Gypsum sets within an hour after it is calcinated. We have addressed seismic issues and used it as a slab. You need skilled labour to work with such panels but the skill can be taught. Engineers have to do a good job as with any precast material. Correcting mistakes would add more to the cost. Assembling is easy and there is no problem in the process.
Production is faster than easy cast; it is much lighter through glass fibres that are implemented. It weighs only 43 kg per sq m. These panels can be used as walls, floors, roofs and staircases. You can apply the paint after drying. The hollow spaces are around 250 mm and can be easily assembled. These panels can be used to build eight storeys by increasing the thickness of the panels manufactured. They can be cut according to the requirement at the plant, which saves construction time.
The future
Gypsum is one of the variants available. But we have to ensure wide availability of these panels. If more manufacturing plants are created, they can compete in the market, which is a key issue. As with all new technologies, you need proper training to make these panels that require dimensional consistencies. If we work closely with the architect, we can also see variations. Right now, the width of the panel is 1.64 mm; if you make it 150 mm, you can add more storeys.
The big picture
The government has a vision of ´Housing for All by 2022´. The requirement is nearly 30 million and this is one piece in the big puzzle. The technology we have used in the GFRG demo building has the potential to meet this challenge of providing rapid affordable mass housing. We will have to use mechanised construction to realise this vision. One single technology cannot solve everything. Every place will have its own unique technology. People will always play with opportunity costs. We have to make people compete.
Points to remember
Architects or engineers should consider some points before drawing the building plan.
- The shorter span of a slab (floor or roof) should be restricted to 5 m.
- Ideally, the same floor plan should be replicated for all floors in a multi-storied structure. (Variations can be done after discussion with a licensed structural engineer.)
- Curved walls or domes should be avoided. In case it is essential, use masonry or concrete for that particular area.
- The electrical or plumbing drawings should be such that most of the pipes go through the cavities (in order to facilitate minimum cutting of panels).
- The building drawings should be checked and designed by a licensed structural engineer who has prior experience in GFRG building works.
The Rapidwall technique comprises a superstructure of glass fibre-reinforced gypsum construction that is entirely based on prefabricated panels. IIT-Madras is playing host to a house on campus made with Rapidwall technology. Such panel-made houses have been adopted by many countries; in India, IIT-M is the pioneer. Innovation comes through by researching and trying to match needs, believes Prof Meher Prasad, HOD, Civil Engineering, IIT-Madras, as he elaborates on the process of rapid construction and its benefits. The beginning Rapidwall panels were developed by RBS Australia for rapid erection of walls in buildings to carry gravity loads. These panels are 12 m long, 3 m high and 124 mm thick with hollow cavities. The technology uses industrial waste gypsum and glass fibres in hollow panels, called glass fibre-reinforced gypsum (GFRG) panels. The demo building in the IIT-M campus comprises four flats in two storeys and was built within a month. The wall panels are integrated to provide more load carrying capacity for structural efficiency. The superstructure of GFRG construction is entirely based on prefabricated panels. The procedure mainly includes fixing wall panels and roof panels using mechanical means, preferably a crane, and filling the required joints with reinforced cement concrete as per structural design. Construction process The foundation used in this construction is conventional. It depends on the soil condition of the particular site and the number of storeys of the structure. Generally, strip footing is used as the superstructure consists of load bearing walls. The following steps are involved in the construction: Excavation of earth. Levelling or ramming of base. Laying of PCC. Waterproofing layer over the entire PCC. Footing (generally strip, but varies according to building type, size and soil conditions). Waterproofing on three sides (exposed sides of footing and plinth beam). Plinth beam over the footing with start-up rods from foundation for connectivity of building with foundation. Filling inner depressions in footing. using excavated earth and ramming it well. Filling up the top with quarry dust (or any inert waste material) 200 mm thick. Laying of PCC layer (100 mm) over the filled up area upto plinth beam top. Final layer of waterproofing over the entire floor area. The process is more complicated than conventional construction but material consumption comes down. It is not more difficult than precast. Success meter The demo building was constructed at a finished cost of Rs 1,250 per sq ft. It has attracted a lot of visitors. We are trying to scale up a large number of flats. You get dimensional accuracy if you follow the principles of modularity. Some individual houses have already been constructed. Kerala housing has taken up a three-storey building; some of these buildings have already been executed. Currently there are only two plants that can produce 1.5 million sq m, one at Rashtriya Chemicals & Fertilizers (RCF) in Mumbai, and another at FACT, Kochi. We hope big players will come into the picture in the near future. As we have just two plants manufacturing the panels, transportation costs will add up if the construction site is not near these plants. A fit-to-stay house can be prepared within a week once the ground floor is constructed. Countless benefits The structural cost is reduced by 20 per cent. The taller the building, more the benefits. Efficient use brings down consumption. In the slab, there is a 50-mm gap to be filled with concrete. Even without concrete, it can take 16 tonne per m. Gypsum and water do not go together and the calcination and formulation process helps this. Because of the glass fibre, more strength is added to the panels. The waterless formulation of these panels makes it waterproof. Gypsum sets within an hour after it is calcinated. We have addressed seismic issues and used it as a slab. You need skilled labour to work with such panels but the skill can be taught. Engineers have to do a good job as with any precast material. Correcting mistakes would add more to the cost. Assembling is easy and there is no problem in the process. Production is faster than easy cast; it is much lighter through glass fibres that are implemented. It weighs only 43 kg per sq m. These panels can be used as walls, floors, roofs and staircases. You can apply the paint after drying. The hollow spaces are around 250 mm and can be easily assembled. These panels can be used to build eight storeys by increasing the thickness of the panels manufactured. They can be cut according to the requirement at the plant, which saves construction time. The future Gypsum is one of the variants available. But we have to ensure wide availability of these panels. If more manufacturing plants are created, they can compete in the market, which is a key issue. As with all new technologies, you need proper training to make these panels that require dimensional consistencies. If we work closely with the architect, we can also see variations. Right now, the width of the panel is 1.64 mm; if you make it 150 mm, you can add more storeys. The big picture The government has a vision of ´Housing for All by 2022´. The requirement is nearly 30 million and this is one piece in the big puzzle. The technology we have used in the GFRG demo building has the potential to meet this challenge of providing rapid affordable mass housing. We will have to use mechanised construction to realise this vision. One single technology cannot solve everything. Every place will have its own unique technology. People will always play with opportunity costs. We have to make people compete. Points to remember Architects or engineers should consider some points before drawing the building plan. The shorter span of a slab (floor or roof) should be restricted to 5 m. Ideally, the same floor plan should be replicated for all floors in a multi-storied structure. (Variations can be done after discussion with a licensed structural engineer.) Curved walls or domes should be avoided. In case it is essential, use masonry or concrete for that particular area. The electrical or plumbing drawings should be such that most of the pipes go through the cavities (in order to facilitate minimum cutting of panels). The building drawings should be checked and designed by a licensed structural engineer who has prior experience in GFRG building works.