- Home
- Real Estate
- Rugged pavers
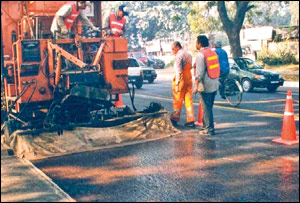
Rugged pavers
Flexible pavements constitute over 90 per cent of the total road network in India. Hot mix asphalt (HMA) is generally used for the construction of the base, binder and wearing courses of these pavements. Here, a high amount of energy is required to heat the aggregates and bituminous binder, which further releases a significant amount of greenhouse gases, thereby polluting the environment.
However, also rapidly growing in use is another type of bituminous binder: bitumen emulsion. This liquid product (at ambient temperature) is prepared by the microscopic dispersion of solid or semisolid bitumen in water medium using chemical emulsifiers. In recent years, some innovative bitumen-based emulsion technologies have demonstrated their ability to meet the challenges of carbon credit, economy and environmental concerns and, consequently, various standards and specifications have also been brought out on these aspects.
Composition of bitumen emulsion
Bitumen emulsion is a two-phase system consisting of bitumen, water and one or more additives, which assist in its formation and stabilisation and in modifying its properties. The bitumen is dispersed throughout the water phase in the form of discrete globules, typically 0.1 to 20 ¦m in diameter, which are held in suspension by electrostatic charge stabilised by an emulsifier. The raw materials that go into bitumen emulsion may include bitumen, water, emulsifier, acid or caustic, polymers, salts, solvents, bitumen additives, and emulsion stabilisers. Bitumen emulsions are normally of the oil-in-water (O/W) type where the continuous phase is water and disperse (droplet) phase is a water-insoluble 'oily' liquid. One gram of bitumen emulsion (a volume roughly equal to a sugar cube) can contain over 1 billion bitumen droplets, each having a total surface area of about 1 sq m.
Application areas
Bitumen emulsions are used for a wide range of applications. Major uses of bitumen emulsions in various types of applications are given in 'Table 1'.
The table indicates that bitumen emulsions can be used for almost all types of applications, including dense mixes with satisfactory performance, provided the correct grade of emulsion is chosen. The choice of emulsion for each application is a question of matching the reactivity of the emulsion with the reactivity of the aggregate and the environmental conditions. Aggregate reactivity is mostly associated with the finest-size fractions, which make the highest contribution to the surface area.
Patching mixes
The most time-consuming and neglected maintenance activities include patching, filling potholes and repairing failed areas of a pavement. In most cases, hot mix is preferred. However, it is not available throughout the year in areas of cold climate and high rainfall. In such a scenario, cold mix is preferable. Cold-mix patching materials are typically classified in three groups: 'everyday' cold mixes; user agency specified cold mixes; and proprietary or ready-to-use patching mixes. 'Everyday' or locally produced cold mixes may include materials prepared with no specifications or quality control whereas user-agency-specified cold mixes are generally well-designed and tested to assure adherence to the specifications set by the agency.
The third group is proprietary or ready-to-use patching mixes, also referred to as high-performance cold mix, typically use a brand name and are produced by the manufacturer to adhere to proprietary specifications. It is very effective for the instant repair of potholes on roads under inclement weather and operating conditions. These mixes are expected to contain 5-6 per cent of residual bitumen and continuously graded aggregates.
Central Road Research Institute, a constituent of Council of Scientific and Industrial Research (CSIR-CRRI) has evaluated a number of ready-to-use patching mixes in the recent past. The efficacy of such proprietary patching mixes in the field was investigated through limited field trials, particularly under heavy traffic conditions. The field studies conducted were limited to different locations on PWD (Public Works Department) and MCD (Municipal Corporation of Delhi) roads in Delhi. The performance of these mixes was found to be satisfactory to repair potholes and utility cuts on urban roads.
Microsurfacing
Microsurfacing consists of a mixture of modified (polymer or rubber latex) bitumen emulsion, well-graded mineral aggregate, water, filler and additive. It is proportioned, mixed and uniformly spread over a properly prepared surface. The finally laid microsurfacing will have a homogeneous mat and adhere firmly to the prepared surface and provide friction-resistant surface texture throughout its service life. The mix is a quick setting system; it requires very little time for application and once set, it should be able to receive traffic after a short period of time, preferably within about one hour of laying, depending upon weather conditions.
Microsurfacing helps preserve pavement strength and can be used both as preventive maintenance treatment or periodic renewal treatment on preferably low, medium or heavy traffic.
It can be used for pavements in urban and rural areas, primary and interstate routes, residential streets, highways and toll roads. It can also be used on top of single-coat surface dressing (cape seal), on open-graded premix carpet without seal coat and on dense bituminous macadam or bituminous macadam. Various types of microsurfacing can be used for different applications; the quantity of microsurfacing mix and the residual binder content in each type are presented in 'Table 2'.
The major benefits of microsurfacing include quick application (one lane-km in 35 minutes); minimum traffic holdup (work is done lane-wise), so quick opening to traffic; non-polluting as no heating or hot paving is required; waterproof surface protection from rains; ideal for surface sealing treatment as it improves skid resistance and provides surface durability; cost-effective compared to hot mix (almost 40 per cent saving in cost); reduces noise caused by movement of traffic; and environment-friendly (reduced emissions). Microsurfacing has been successfully applied on a number of roads in Delhi.
Cold mixes
A cold mix is defined as a mixture of bitumen emulsion and aggregate mixed together at ambient temperature. It is useful in areas where there is a considerable amount of distance between the job site and mixing, and the climate is low and moderate (<40°C). Further, the versatility of cold mix allows it to be mixed in place at the job site as well as at a plant site and then subsequently transported to the job site. Suitable for bituminous base (BM), binder course (BM/SDBC) as well as wearing course (SDBC) of a flexible pavement, it should be designed to meet the performance requirements for the job, which include workability, coating, strength development, and other applicable targets. Also, the quality of residual bitumen, aggregate and climatic conditions should be taken into account. The design requirements of cold-mixed bituminous macadam (CMBM) and cold-mixed, semi-dense bituminous concrete (CMSDBC) are given in 'Table 3' and 'Table 4'.
Achieving good performance
The following precautions should be taken to ensure the successful laying of cold mixes (CMBM or CMSDBC) to achieve good performance:
- Cold mixes generally have good resistance to water's detrimental effects during construction. However, if it rains before the mixture is cured, then traffic should be kept off until the mix is cured and the necessary compaction is accomplished.
- The mixing water content should be sufficient to adequately disperse the emulsion and achieve good workability.
- Mixtures should be mixed only enough to properly disperse the emulsion. Excessive mixing may cause the emulsion to break prematurely or strip from the mineral aggregates.
- For faster curing, place the cold mix in several thin layers rather than in a single thick layer.
- If case ravelling is observed owing to traffic, the loose material should be broomed off as soon as possible to prevent further damage to the surface. If the ravelling continues, the surface should be fog sealed with a light application of a slow-setting emulsion (SS - 2) diluted with soft water in 1:1 ratio.
- CSIR-CRRI has been involved with the laying of cold mixes at various locations in the Northeast. The performance of the same has been satisfactory.
Half-warm mixes
Half-warm mixes are mixes where the bituminous binder is either a bitumen emulsion or foamed bitumen, which is manufactured and mixed with warm aggregates (100 + 10 °C), laid and compacted in a temperature between 80 °C to 90 °C. The prime advantages of producing half warm mixes (DBM, SDBC and BC) using warm aggregate and cationic bitumen emulsions include reduced mixing time, ability to coat large-size aggregate at lower temperature, and reduction of bitumen hardening during mixing.
The half-warm mixed dense bituminous macadam, semi-dense or dense bituminous concrete shall consist of coarse aggregate, fine aggregate and filler in suitable proportion mixed with sufficient quantity of cationic bitumen emulsion. Representative samples of the aggregates proposed to be used for the specific job shall be tested in the laboratory and a proper blend of the aggregate shall be worked out so that the gradation of final aggregate mix will satisfy specified aggregate gradations of DBM, SDBC and BC.
The bitumen emulsion should be cationic SS-2 grade confirming to IS: 8887 specifications or tailor-made for the aggregate to be used in construction. Design of half-warm, aggregate-based warm mix prepared with bitumen emulsion should be done by the Marshall method.
CSIR-CRRI has recently been involved with the laying of half-warm mix bituminous concrete using bitumen emulsion between161 to 162 km of NH-8B (Rajkot to Gondal Jaitpur) in Gujarat.
Code of practice
One of the major handicaps regarding the widespread usage of bitumen emulsion is the lack of information regarding the proper selection of bitumen emulsion grade for different applications. In this regard, we need a comprehensive document, specification or code of practice detailing the usage of bitumen emulsions for different applications that would be of great importance for the road fraternity.
About the authors:
Dr PK Jain, Professor and Coordinator, Academy of Scientific and Innovation Research (CSIR-CRRI Campus), has over 35 years of research experience. His main area of working is pavement materials.
Abhishek Mittal, Scientist, CSIR-CRRI, New Delhi, has been working for the past seven years at the institute. His areas of interest include bituminous materials, pavement design and failure investigations.
To share your technology with us, write in at feedback@ASAPPmedia.com
PK JAIN and ABHISHEK MITTAL elaborate on the growing use of bitumen emulsion technologies for the construction and maintenance of roads. Flexible pavements constitute over 90 per cent of the total road network in India. Hot mix asphalt (HMA) is generally used for the construction of the base, binder and wearing courses of these pavements. Here, a high amount of energy is required to heat the aggregates and bituminous binder, which further releases a significant amount of greenhouse gases, thereby polluting the environment. However, also rapidly growing in use is another type of bituminous binder: bitumen emulsion. This liquid product (at ambient temperature) is prepared by the microscopic dispersion of solid or semisolid bitumen in water medium using chemical emulsifiers. In recent years, some innovative bitumen-based emulsion technologies have demonstrated their ability to meet the challenges of carbon credit, economy and environmental concerns and, consequently, various standards and specifications have also been brought out on these aspects. Composition of bitumen emulsion Bitumen emulsion is a two-phase system consisting of bitumen, water and one or more additives, which assist in its formation and stabilisation and in modifying its properties. The bitumen is dispersed throughout the water phase in the form of discrete globules, typically 0.1 to 20 ¦m in diameter, which are held in suspension by electrostatic charge stabilised by an emulsifier. The raw materials that go into bitumen emulsion may include bitumen, water, emulsifier, acid or caustic, polymers, salts, solvents, bitumen additives, and emulsion stabilisers. Bitumen emulsions are normally of the oil-in-water (O/W) type where the continuous phase is water and disperse (droplet) phase is a water-insoluble 'oily' liquid. One gram of bitumen emulsion (a volume roughly equal to a sugar cube) can contain over 1 billion bitumen droplets, each having a total surface area of about 1 sq m. Application areas Bitumen emulsions are used for a wide range of applications. Major uses of bitumen emulsions in various types of applications are given in 'Table 1'. The table indicates that bitumen emulsions can be used for almost all types of applications, including dense mixes with satisfactory performance, provided the correct grade of emulsion is chosen. The choice of emulsion for each application is a question of matching the reactivity of the emulsion with the reactivity of the aggregate and the environmental conditions. Aggregate reactivity is mostly associated with the finest-size fractions, which make the highest contribution to the surface area. Patching mixes The most time-consuming and neglected maintenance activities include patching, filling potholes and repairing failed areas of a pavement. In most cases, hot mix is preferred. However, it is not available throughout the year in areas of cold climate and high rainfall. In such a scenario, cold mix is preferable. Cold-mix patching materials are typically classified in three groups: 'everyday' cold mixes; user agency specified cold mixes; and proprietary or ready-to-use patching mixes. 'Everyday' or locally produced cold mixes may include materials prepared with no specifications or quality control whereas user-agency-specified cold mixes are generally well-designed and tested to assure adherence to the specifications set by the agency. The third group is proprietary or ready-to-use patching mixes, also referred to as high-performance cold mix, typically use a brand name and are produced by the manufacturer to adhere to proprietary specifications. It is very effective for the instant repair of potholes on roads under inclement weather and operating conditions. These mixes are expected to contain 5-6 per cent of residual bitumen and continuously graded aggregates. Central Road Research Institute, a constituent of Council of Scientific and Industrial Research (CSIR-CRRI) has evaluated a number of ready-to-use patching mixes in the recent past. The efficacy of such proprietary patching mixes in the field was investigated through limited field trials, particularly under heavy traffic conditions. The field studies conducted were limited to different locations on PWD (Public Works Department) and MCD (Municipal Corporation of Delhi) roads in Delhi. The performance of these mixes was found to be satisfactory to repair potholes and utility cuts on urban roads. Microsurfacing Microsurfacing consists of a mixture of modified (polymer or rubber latex) bitumen emulsion, well-graded mineral aggregate, water, filler and additive. It is proportioned, mixed and uniformly spread over a properly prepared surface. The finally laid microsurfacing will have a homogeneous mat and adhere firmly to the prepared surface and provide friction-resistant surface texture throughout its service life. The mix is a quick setting system; it requires very little time for application and once set, it should be able to receive traffic after a short period of time, preferably within about one hour of laying, depending upon weather conditions. Microsurfacing helps preserve pavement strength and can be used both as preventive maintenance treatment or periodic renewal treatment on preferably low, medium or heavy traffic. It can be used for pavements in urban and rural areas, primary and interstate routes, residential streets, highways and toll roads. It can also be used on top of single-coat surface dressing (cape seal), on open-graded premix carpet without seal coat and on dense bituminous macadam or bituminous macadam. Various types of microsurfacing can be used for different applications; the quantity of microsurfacing mix and the residual binder content in each type are presented in 'Table 2'. The major benefits of microsurfacing include quick application (one lane-km in 35 minutes); minimum traffic holdup (work is done lane-wise), so quick opening to traffic; non-polluting as no heating or hot paving is required; waterproof surface protection from rains; ideal for surface sealing treatment as it improves skid resistance and provides surface durability; cost-effective compared to hot mix (almost 40 per cent saving in cost); reduces noise caused by movement of traffic; and environment-friendly (reduced emissions). Microsurfacing has been successfully applied on a number of roads in Delhi. Cold mixes A cold mix is defined as a mixture of bitumen emulsion and aggregate mixed together at ambient temperature. It is useful in areas where there is a considerable amount of distance between the job site and mixing, and the climate is low and moderate (<40°C). Further, the versatility of cold mix allows it to be mixed in place at the job site as well as at a plant site and then subsequently transported to the job site. Suitable for bituminous base (BM), binder course (BM/SDBC) as well as wearing course (SDBC) of a flexible pavement, it should be designed to meet the performance requirements for the job, which include workability, coating, strength development, and other applicable targets. Also, the quality of residual bitumen, aggregate and climatic conditions should be taken into account. The design requirements of cold-mixed bituminous macadam (CMBM) and cold-mixed, semi-dense bituminous concrete (CMSDBC) are given in 'Table 3' and 'Table 4'. Achieving good performance The following precautions should be taken to ensure the successful laying of cold mixes (CMBM or CMSDBC) to achieve good performance: Cold mixes generally have good resistance to water's detrimental effects during construction. However, if it rains before the mixture is cured, then traffic should be kept off until the mix is cured and the necessary compaction is accomplished. The mixing water content should be sufficient to adequately disperse the emulsion and achieve good workability. Mixtures should be mixed only enough to properly disperse the emulsion. Excessive mixing may cause the emulsion to break prematurely or strip from the mineral aggregates. For faster curing, place the cold mix in several thin layers rather than in a single thick layer. If case ravelling is observed owing to traffic, the loose material should be broomed off as soon as possible to prevent further damage to the surface. If the ravelling continues, the surface should be fog sealed with a light application of a slow-setting emulsion (SS - 2) diluted with soft water in 1:1 ratio. CSIR-CRRI has been involved with the laying of cold mixes at various locations in the Northeast. The performance of the same has been satisfactory. Half-warm mixes Half-warm mixes are mixes where the bituminous binder is either a bitumen emulsion or foamed bitumen, which is manufactured and mixed with warm aggregates (100 + 10 °C), laid and compacted in a temperature between 80 °C to 90 °C. The prime advantages of producing half warm mixes (DBM, SDBC and BC) using warm aggregate and cationic bitumen emulsions include reduced mixing time, ability to coat large-size aggregate at lower temperature, and reduction of bitumen hardening during mixing. The half-warm mixed dense bituminous macadam, semi-dense or dense bituminous concrete shall consist of coarse aggregate, fine aggregate and filler in suitable proportion mixed with sufficient quantity of cationic bitumen emulsion. Representative samples of the aggregates proposed to be used for the specific job shall be tested in the laboratory and a proper blend of the aggregate shall be worked out so that the gradation of final aggregate mix will satisfy specified aggregate gradations of DBM, SDBC and BC. The bitumen emulsion should be cationic SS-2 grade confirming to IS: 8887 specifications or tailor-made for the aggregate to be used in construction. Design of half-warm, aggregate-based warm mix prepared with bitumen emulsion should be done by the Marshall method. CSIR-CRRI has recently been involved with the laying of half-warm mix bituminous concrete using bitumen emulsion between161 to 162 km of NH-8B (Rajkot to Gondal Jaitpur) in Gujarat. Code of practice One of the major handicaps regarding the widespread usage of bitumen emulsion is the lack of information regarding the proper selection of bitumen emulsion grade for different applications. In this regard, we need a comprehensive document, specification or code of practice detailing the usage of bitumen emulsions for different applications that would be of great importance for the road fraternity. About the authors: Dr PK Jain, Professor and Coordinator, Academy of Scientific and Innovation Research (CSIR-CRRI Campus), has over 35 years of research experience. His main area of working is pavement materials. Abhishek Mittal, Scientist, CSIR-CRRI, New Delhi, has been working for the past seven years at the institute. His areas of interest include bituminous materials, pavement design and failure investigations. To share your technology with us, write in at feedback@ASAPPmedia.com