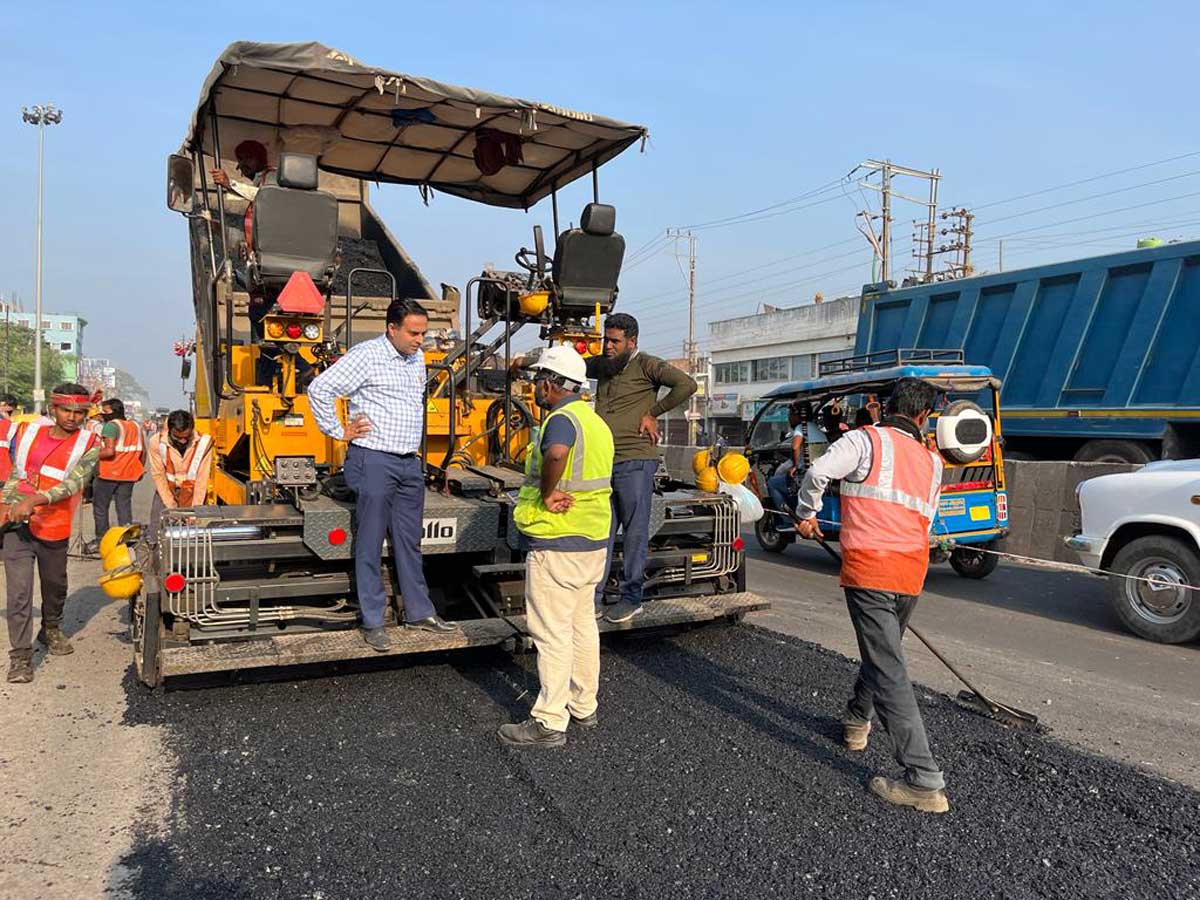
"Revolutionizing Solar Energy Technology: Sustainable Power's Breakthrough Innovation"
Read full article
CW Gold Benefits
- Weekly Industry Updates
- Industry Feature Stories
- Premium Newsletter Access
- Building Material Prices (weekly) + trends/analysis
- Best Stories from our sister publications - Indian Cement Review, Equipment India, Infrastructure Today
- Sector focused Research Reports
- Sector Wise Updates (infrastructure, cement, equipment & construction) + trend analysis
- Exclusive text & video interviews
- Digital Delivery
- Financial Data for publically listed companies + Analysis
- Preconceptual Projects in the pipeline PAN India
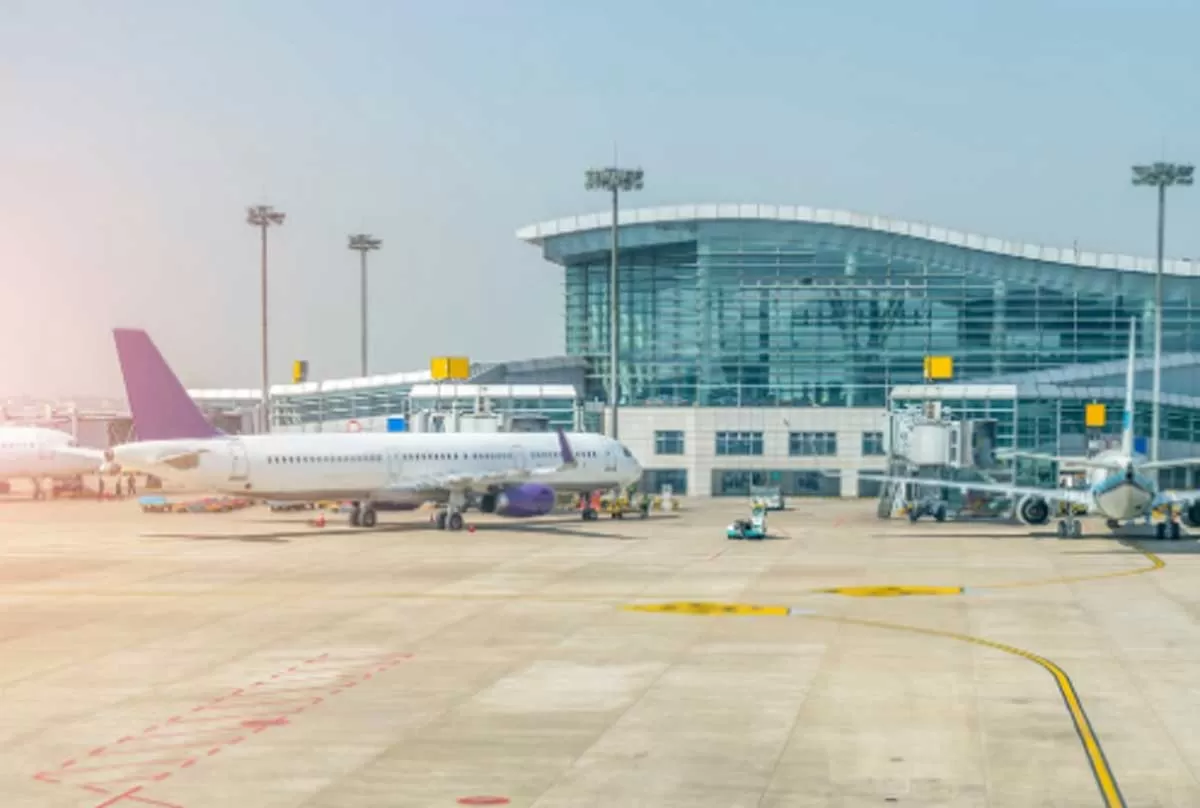
Cabinet Clears Rs 15.07 Bn Greenfield Airport Project in Kota-Bundi
The Cabinet Committee on Economic Affairs, chaired by Prime Minister Narendra Modi, has approved the Airports Authority of India’s (AAI) proposal for the development of a Greenfield Airport at Kota-Bundi, Rajasthan, at an estimated cost of Rs 15.07 billion.Kota, located on the banks of the Chambal River, is widely recognised as the industrial capital of Rajasthan and a prominent educational coaching hub. To support the region’s growing needs, the Government of Rajasthan has handed over 440.06 hectares of land to AAI for the project.The new Greenfield Airport will be designed to handle oper..
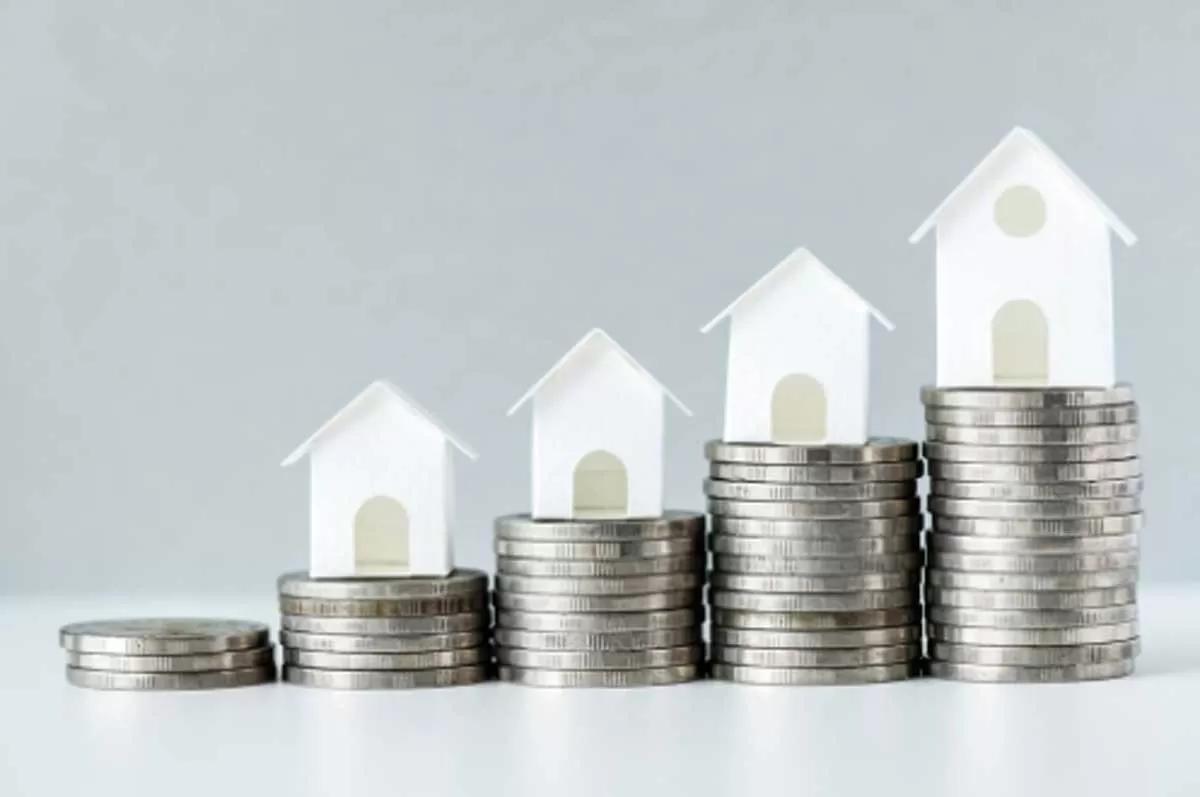
Govt may extend MSME NPA classification period to 180 days
The Union government is considering a proposal to extend the non-performing asset (NPA) classification period for loans to micro, small and medium enterprises (MSMEs) from the existing 90 days to 180 days, according to a senior government official who requested anonymity.“The proposal to extend the loan default period for MSMEs from 90 days to 180 days is likely to be taken up by the Cabinet soon,” the official said.The move is expected to provide relief to cash-strapped MSMEs, especially against the backdrop of steep US tariffs, giving them more time to regularise their loan repayments.Ne..
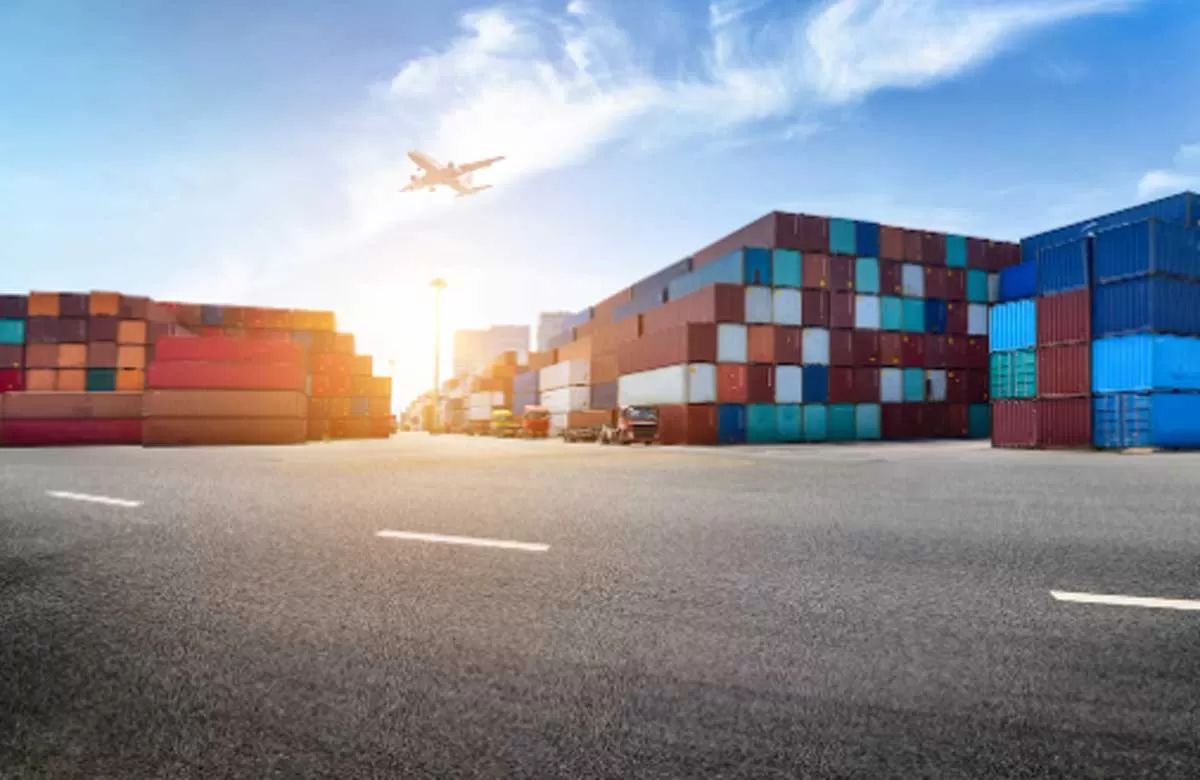
FedEx, IIT Madras Launch SMART Centre for Sustainable, AI-led Logistics
FedEx has partnered with the Indian Institute of Technology (IIT) Madras to inaugurate the SMART Centre (Supply Chain Modelling, Algorithms, Research and Technology Centre) on the institute’s campus. The facility will drive innovation in sustainable and AI-driven logistics solutions. Backed by a five-year $5 million grant from FedEx, the SMART Centre aims to combine advanced research, digital technologies, and industry expertise to transform supply chains with a focus on agility, resilience, and environmental responsibility.The centre will also spearhead interdisciplinary projects in ar..