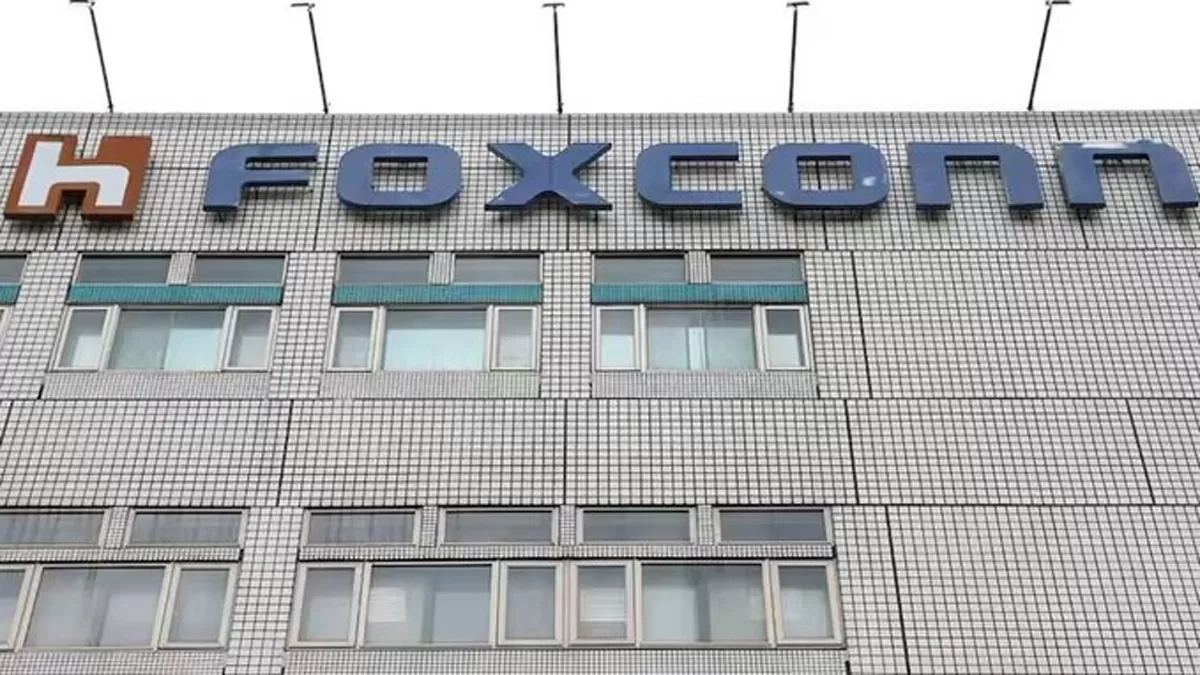
HCL-Foxconn to invest Rs 37 billion in chip plant near Jewar airport
The Union Cabinet has approved the establishment of a new semiconductor unit near Jewar airport in Uttar Pradesh under the India Semiconductor Mission. This sixth plant, a joint venture between HCL and Foxconn, marks further progress in India’s semiconductor journey. The project will see an investment of Rs 37 billion.The facility will produce display driver chips for mobile phones, laptops, automobiles, PCs, and other digital devices. It is designed for a monthly capacity of 20,000 wafers and an output of 36 million units.Five semiconductor units are already in advanced stages of constructi..
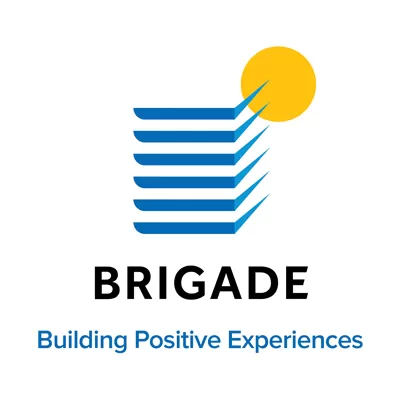
Brigade acquires Velachery land for Rs 16-billion project
Brigade Enterprises has acquired a 5.41-acre land parcel on Velachery Road, Chennai, through an outright purchase for Rs 4.417 billion. Located next to Phoenix Market City, the site will be developed into a premium residential project with a gross development value of approximately Rs 16 billion and a development potential of 0.8 million square feet.The project offers strategic access to both the OMR IT Corridor and Chennai’s Central Business District, promising strong connectivity and premium lifestyle offerings. Brigade plans to create signature residences focused on aesthetics, functional..
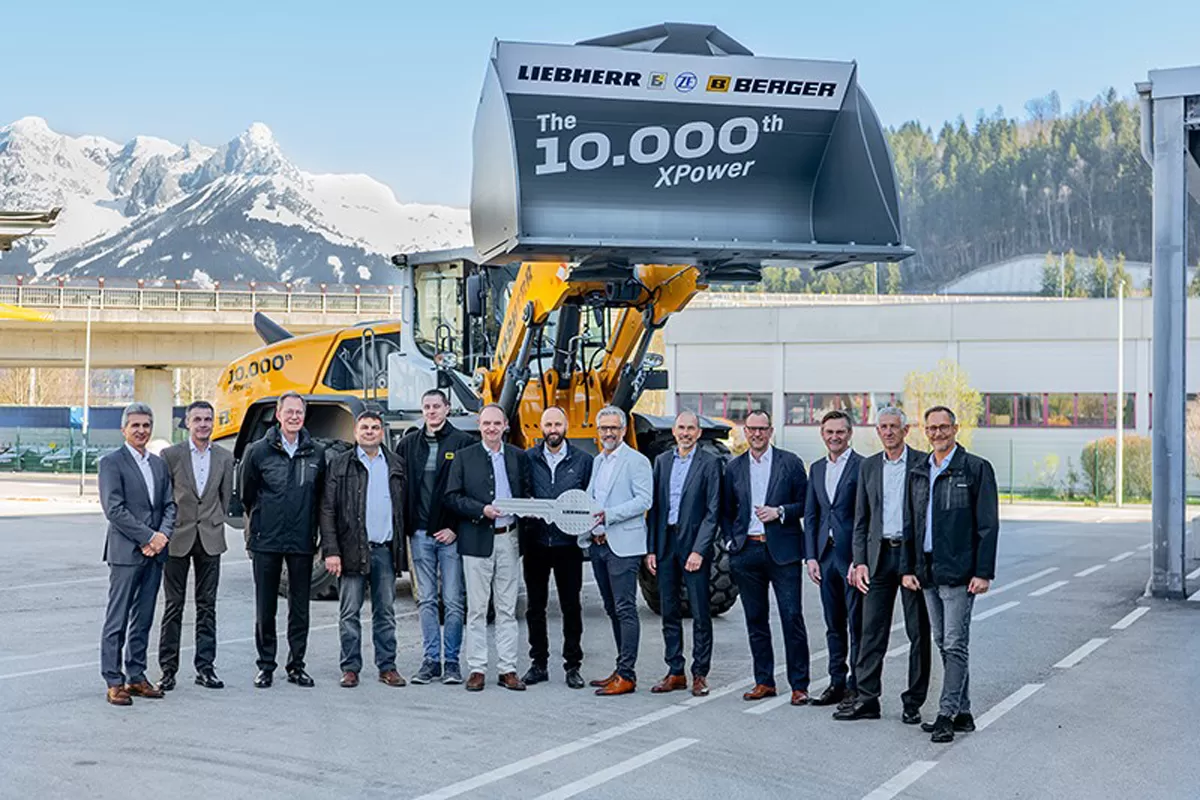
Liebherr marks 10,000th XPower wheel loader milestone
Liebherr-Werk Bischofshofen has rolled out its 10,000th XPower wheel loader, marking a major production milestone. The anniversary L 580 XPower model, featuring a power-split travel drive developed with ZF Friedrichshafen AG, was handed over to the BERGER Group in Passau.“The transmission from our partner ZF is a key component of the drivetrain in our XPower wheel loaders,” said Gerhard Pirnbacher, Head of Quality Management at Liebherr. “With an impressive total of around 64 million operating hours already clocked up by XPower models, this transmission has proven its exceptional robustn..