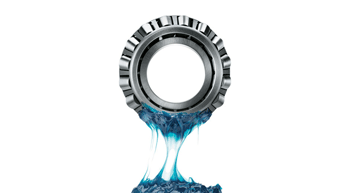
Improving Bearing Productivity
A recent joint study commissioned by consulting firm McKinsey and the Confederation of Indian Industry (CII) highlights India as the most favoured country to capitalise on emerging trends that increasingly favour global delivery models in automotive technology development and manufacturing, owing to a skilled workforce coupled with low-cost technology design and manufacturing capabilities. Following is an illustration of the case study on Swastik Pipes, of how the right industrial lubricant can improve performance, increase productivity and thereby, contribute to the bottom-line. Companies, for instance Swastik Pipes facing such issues as grease washout by coolant, increased bearing temperature and high re-greasing frequency have managed to come with solutions to overcome the problem. Paintal details on how the company launched a product to solve this common problem along with its advantages.
Background
One of India´s leading manufactures, Swastik Pipes Ltd, is an exporter of TT Swastik Band high quality mild steel and carbon steel ERW black and galvanised pipes and tubes since 1973. The company also manufactures line pipes as per APL Spec.5L since nine years. Moreover, its advanced state-of-the-art manufacturing facilities with ISO 9001:2000 and APIQ1 approvals has achieved national and international recognition. The company also is a leading manufacturer of ERW pipes and tubes, steel tubular poles, cold rolled sheets and strips in North India. The manufacturing facility for the same is located in Bahdurgarh, Haryana and is equipped with state-of-the-art equipment. Sophisticated machines producing CR coils, galvanised coil, ERW tubes, steel galvanised coil, CRCA coils and sheets and galvanised products in desired specifications and finishes are manufactured in this unit. The company manufactures CR coils and strips with an annual capacity of 1 lakh MT per annum in various sizes and thickness.
Challenges met
The CR production plant consists of two 4 HI and one 6 HI cold rolling mills along with bell furnaces, skin pass, slitting, cut to length and testing facilities. In the CRM rollers bearing lubrication, SPL earlier used lithium-thickener EP2 grease. It had to be re-greased or topped up frequently to avoid bearing failures and maintain the running temperature of the bearings. Moreover, the other issues encountered included getting the grease to dry, dust entering into the bearings, grease bleeding, etc. The main problem encountered by the SPL in CRMs was grease washout because of coolant used in the process. To encounter all these problems, Mobilgrease XHP 222 was suggested as a solution by Mobil FES team and NIS engineers.
Effective solutions
Application of Mobil Grease XHP 222 overcomes the problem of grease washout by coolant, increased bearing temperature, and high re-greasing frequency. The bearing life also increases substantially, which further results in considerable savings in total cost of ownership for the company leading to an annual saving of Rs 235,275. The product provides good sealing and intercepts dust from entering into bearings. It absorbs and holds its consistency for a long duration. Moreover, it can be efficient in temperatures as high as 100oC. This results in improvement in mill reliability, decrease in bearing failure and grease consumption by eight man days per annum. To add to it, a considerable increase in the duration of re-greasing intervals to approximately three times more than the competitor lithium thickener grease was observed. Previously, SPL used to top up on daily basis, which has now scheduled to after every third day with Mobilgrease XHP 222.
Benefits
- Improves productivity.
- Decreases bearing failure by 50 per cent.
- Decreases grease consumption by 33 per cent.
- Improved mill reliability.
- Increase in mill overhauling schedule and hence enhanced Mill availability by eight man days per annum.
Impact:
- Cut down mills stoppage by eight days by increasing overhauling schedule.
- US$ 10,000 savings achieved by reduction in bearing failure and grease consumption.
(Communication by the management of the company)
¨Right industrial lubricant can improve performance, increase productivity and thereby, contribute to the bottom line,¨ Rupinder Paintal, General Manager-Industrial, ExxonMobil Lubricants A recent joint study commissioned by consulting firm McKinsey and the Confederation of Indian Industry (CII) highlights India as the most favoured country to capitalise on emerging trends that increasingly favour global delivery models in automotive technology development and manufacturing, owing to a skilled workforce coupled with low-cost technology design and manufacturing capabilities. Following is an illustration of the case study on Swastik Pipes, of how the right industrial lubricant can improve performance, increase productivity and thereby, contribute to the bottom-line. Companies, for instance Swastik Pipes facing such issues as grease washout by coolant, increased bearing temperature and high re-greasing frequency have managed to come with solutions to overcome the problem. Paintal details on how the company launched a product to solve this common problem along with its advantages. Background One of India´s leading manufactures, Swastik Pipes Ltd, is an exporter of TT Swastik Band high quality mild steel and carbon steel ERW black and galvanised pipes and tubes since 1973. The company also manufactures line pipes as per APL Spec.5L since nine years. Moreover, its advanced state-of-the-art manufacturing facilities with ISO 9001:2000 and APIQ1 approvals has achieved national and international recognition. The company also is a leading manufacturer of ERW pipes and tubes, steel tubular poles, cold rolled sheets and strips in North India. The manufacturing facility for the same is located in Bahdurgarh, Haryana and is equipped with state-of-the-art equipment. Sophisticated machines producing CR coils, galvanised coil, ERW tubes, steel galvanised coil, CRCA coils and sheets and galvanised products in desired specifications and finishes are manufactured in this unit. The company manufactures CR coils and strips with an annual capacity of 1 lakh MT per annum in various sizes and thickness. Challenges met The CR production plant consists of two 4 HI and one 6 HI cold rolling mills along with bell furnaces, skin pass, slitting, cut to length and testing facilities. In the CRM rollers bearing lubrication, SPL earlier used lithium-thickener EP2 grease. It had to be re-greased or topped up frequently to avoid bearing failures and maintain the running temperature of the bearings. Moreover, the other issues encountered included getting the grease to dry, dust entering into the bearings, grease bleeding, etc. The main problem encountered by the SPL in CRMs was grease washout because of coolant used in the process. To encounter all these problems, Mobilgrease XHP 222 was suggested as a solution by Mobil FES team and NIS engineers. Effective solutions Application of Mobil Grease XHP 222 overcomes the problem of grease washout by coolant, increased bearing temperature, and high re-greasing frequency. The bearing life also increases substantially, which further results in considerable savings in total cost of ownership for the company leading to an annual saving of Rs 235,275. The product provides good sealing and intercepts dust from entering into bearings. It absorbs and holds its consistency for a long duration. Moreover, it can be efficient in temperatures as high as 100oC. This results in improvement in mill reliability, decrease in bearing failure and grease consumption by eight man days per annum. To add to it, a considerable increase in the duration of re-greasing intervals to approximately three times more than the competitor lithium thickener grease was observed. Previously, SPL used to top up on daily basis, which has now scheduled to after every third day with Mobilgrease XHP 222. Benefits Improves productivity. Decreases bearing failure by 50 per cent. Decreases grease consumption by 33 per cent. Improved mill reliability. Increase in mill overhauling schedule and hence enhanced Mill availability by eight man days per annum. Impact: Cut down mills stoppage by eight days by increasing overhauling schedule. US$ 10,000 savings achieved by reduction in bearing failure and grease consumption. (Communication by the management of the company)