- Home
- Real Estate
- A case for industrialised construction
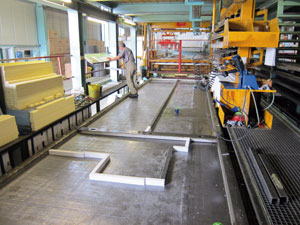
A case for industrialised construction
Is the adoption of these gathering momentum in India? Charu Bahri explores further.
Offsite technologies present one of the biggest opportunities to the construction industry world over. Prefabricated offsite technology involves the factory production of various kinds of building materials, which can then be transported to site and used as is in construction.
Precast structural components made of cement and steel, composites, aluminium and steel grids, parts made of timber and PVC, cement fibre boards, galvanised iron sheets and EPS sandwich sheet panels are amongst a few prefabricated materials that have been successfully used in developed nations.
Pre-engineered offsite technology involves the meticulous engineering of buildings in offsite design centres and their erection using prefabricated components made of steel alloys and other materials.
A paradigm shift
Offsite pre-fabricated and pre-engineering technologies represent a paradigm shift from conventional site-based brick-and-mortar construction methods. Speed is the biggest advantage of using such materials and most likely to strengthen the case for offsite technologies. "As the cost of borrowing rises and developers face a liquidity crunch, there is a higher likelihood of adopting technologies that could add to their revenue stream," avers Sachin Sandhir, Managing Director, RICS South Asia (RICS).
Prefabricated components also conform to high standards by virtue of being made in strictly controlled conditions in plants, and they can be more cost-effective, especially in the light of rising costs of inputs mandated in traditional construction. Structures made of prefabricated components have lower maintenance needs vis-a-vis conventional structures and perform better over their long life.
"Yet another plus point of such building solutions is that they can incorporate the use of leading or cutting edge eco-friendly technology, which is completely in-sync with building codes," adds Sandhir.
Growth deterrents
A lack of awareness of offsite technologies here, in comparison to other world markets, has limited the growth of this construction format in India to about 10-15 per cent annually.
Some developers shy away from pre-engineered structures because this technology brings limitations of site modifications and multiple on-site changes. Pre-engineered structures require better pre-planning and, where applicable, interfaces with other fatade, MEP, and other building interfaces are to be designed and finalised before manufacturing.
"Resistance by a predominantly labour-intensive industry and the high levy of taxes and duties imposed on pre-assembled or prefabricated construction components have been other deterrents to the growth of 'industrialised construction'," opines Sandhir.
A paucity of expertise in engineering heavy structures is holding back adoption of this technology as well. According to Arvind Nanda, CEO and Founder Director, Interarch, "Whereas medium and light pre-engineered buildings in India are on a par with the rest of the world, augmenting the available expertise in heavy structures, possibly by securing international talent to increase the offerings in the Indian market, would help expand their scope."
Changing fortunes
Despite the hurdles in the path of adoption, avenues for pre-engineered structures and prefabricated technologies are expected to grow in the next few years. Speedy construction activity has a strong correlation with economic growth. In this context, Nanda says, "Crucial government reforms and policy changes recently ushered in will hopefully boost economic sentiment and growth, which is good for us. We can meet the need of various industries for high-speed construction that does not compromise on quality."
Nanda also sees immense scope for pre-engineered steel construction in the infrastructure sector. "Public and urban facilities are likely to be upgraded and revamped in the next few years," he points out. "Additional capacity for power and urban support networks, transport and communication, etc, will be created. Steel construction is the only way to meet the tight deadlines of such projects."
Ports and airports have successfully tested the possibilities of pre-engineered buildings.
Manish Garg, President, Steel Building Solutions, Everest Industries, cites the example of New Delhi's T3 Terminal roof as being an outstanding pre-engineered steel structure. Industrial pre-engineered steel structures, remarkable for their sheer size, include the automotive plants of Tata in Anand and Renault-Nissan in Chennai.
Real-estate opportunities
Clearly, the will to innovate exists. Nanda is sure that interest in offsite technologies from the residential and commercial building segments will pick up. Whereas steel-based pre-engineered buildings are currently considered an option for buildings of height up to 20 m, mostly the likes of factories, warehouses and multi-level car parks, Garg is hopeful that potential customers will gradually think beyond such mundane uses.
Change is happening in pockets across India. "Pre-engineered buildings can be designed up to four to five levels and this is being done largely overseas but a few in India as well," says Venugopal K, Head-Sales & Marketing, Zamil Steel. Zamil Steel's more than 55,000 PEBs, a few as old as 35 years, across 90 countries, include five-storey-high commercial centres, G+3 school buildings and hypermarkets created without compromising on the architectural aesthetic commonly adopted in such buildings. "Aesthetics are mainly an outcome of the panelling used for the fatade and sides, which can easily be integrated with a pre-engineered steel frame," he explains. "Two early examples of innovative steel pre-engineered buildings in India are an office building in Hyderabad, multilevel car parking in Lavasa and a school in Kolkata. These help in educating users about the immense potential of such structures. Our rich experience and strong engineering background encourages us to take up design challenges in the PEB system." Meanwhile, BCC Infrastructures is using German precast technology for Phase-II of its Bharat City project. According to Kumar Bharat, Director, BCC Infrastructures, "We're following the lead of Europe and the Middle East, where precast technology has been successfully put to myriad uses. No doubt India has applied this technology for large construction projects like bridges, metro rail and commercial buildings, but now it's time for housing projects to reap the benefits of faster and eco-friendly construction with no compromise on quality."
Sandhir sees a huge opportunity for offsite technologies to help the Indian Government meet the existing shortfall of ~27 million affordable housing units in the country. To this end, RICS in partnership with Sam Circle Venture, KieranTimberlake and ProjectWell are working on a framework supporting a concrete panel based integrated system for a single dwelling unit. 'India Concept House', as it's called, is sustainable, affordable and quick to erect. "Targeting clients for affordable housing in Tier-II and -III cities, these units will help reduce construction time by up to 90 per cent with construction costs pegged at Rs 900-1,200 per sq ft," he explains. "Cost savings will kick in both in the short term and over the life of the structure. Substantial savings in material will also be achieved."
Clearly, offsite technologies are available in the Indian market. It remains to be seen to what extent the industry adopts them. Let it not be said that offsite technologies were the Indian construction industry's biggest missed opportunity.
Case I
Precast Structural Components in a Residential Building
Execution by: BCC Infrastructures Client: Phase 2, Bharat City
Location: Bharat City, Indra Prastha Yojana Ghaziabad, Uttar Pradesh
Design features: Wall elements produced by battery moulds, floor slabs produced by stationary beds, wall and floor slabs produced by tilting tables, and precast stairways and balconies feature in these apartments. Weckenmann is the precast component supplier for Bharat City. Other comparable vendors are Vollert and Somer precast. Precast structural components such as slabs, columns, beams, walls, etc, are made of cement and steel and conform to high standards as a result of being produced in controlled environments in off-site plants. Using such components drastically reduces manpower needs, wastage and time, thus making projects easier to manage and less risky. It's also an environment-friendly construction method. Buildings made of precast structural components are more spacious because they can be made without columns and beams.
Cost: Same or cheaper than conventional construction methods.
Case II
Prefabricated Eco-friendly Cottage
Execution by: Loom Crafts Client: Panoramic Resorts
Location: Old Goa Highway, Panvel
Design features: A robust framework made of aerospace grade aluminium and stainless steel forms the core structure of the modular building. Interlocking square panels are fastened to adjoining sections by a patented locking system designed to withstand enormous pressure. The roof is made of maintenance-free, fire-retardant, tensile, PVC-coated fabric membrane. Both the roof and sides are insulated. An extensive selection of ancillary modules is available for interior fittings such as eco-friendly solar power, cloakroom and bathtub, wooden deck flooring and aluminium doors and windows powder-coated in a wide choice of colours.
Cost: Rs 3,000 per sq ft (area of each cottage is 550 sq ft)
Case III
Pre-Engineered Building
Execution by: Interarch Client: Tata Motors
Location: Dharwad, Maharashtra
Design features: Pre-engineered building conforming to green building norms, such as the use of low-VOC paint on buildings, white-roofed plant buildings (SRI =78), special glazing and sun shade for windows, ventilation system for optimum indoor air flow and temperature control, and 4 per cent of total roof and 4 per cent of wall as skylights to reduce the need for artificial lighting. Multilevel mezzanines with heavy collateral load are part of the design and allow for paint equipment installations. Safe construction practices and zero accidents are standout features. At peak time, 500 semiskilled and unskilled workmen were employed. Stringent safety norms were followed throughout.
Cost: Rs 86 crore
Case IV
Pre-Engineered Factory Building
Execution by: Alfa Steel Building Solutions
Client: Lloyds Line Pipes Location: Mumbai
Design features: The client needed a heavy structure, big enough to operate a 15 mt capacity crane. The building has a widest span length of 22 m and a height of 12 m. Its walls are made of colour-coated steel sheets and its roof comprises bare galvalume-coated sheets that minimise heat absorption. Insulation wasn't deemed necessary for this building. Satisfactory building performance has led to the client asking Alfa Steel Building Solutions to extend the structure to 200,000 sq ft. Alfa Steel Building Solution provides its customers with tailored designs that meet their exact specifications, for the best possible solution and price points. Its advantage lies in being a one-stop shop, offering design, manufacturing of roofing and wall cladding components and erection of building systems.
Cost: Rs 9.5 crore
To share your feedback on this feature, write in at feedback@ASAPPmedia.com
Offsite technologies facilitating industrialised construction are immensely popular overseas. Is the adoption of these gathering momentum in India? Charu Bahri explores further. Offsite technologies present one of the biggest opportunities to the construction industry world over. Prefabricated offsite technology involves the factory production of various kinds of building materials, which can then be transported to site and used as is in construction. Precast structural components made of cement and steel, composites, aluminium and steel grids, parts made of timber and PVC, cement fibre boards, galvanised iron sheets and EPS sandwich sheet panels are amongst a few prefabricated materials that have been successfully used in developed nations. Pre-engineered offsite technology involves the meticulous engineering of buildings in offsite design centres and their erection using prefabricated components made of steel alloys and other materials. A paradigm shift Offsite pre-fabricated and pre-engineering technologies represent a paradigm shift from conventional site-based brick-and-mortar construction methods. Speed is the biggest advantage of using such materials and most likely to strengthen the case for offsite technologies. "As the cost of borrowing rises and developers face a liquidity crunch, there is a higher likelihood of adopting technologies that could add to their revenue stream," avers Sachin Sandhir, Managing Director, RICS South Asia (RICS). Prefabricated components also conform to high standards by virtue of being made in strictly controlled conditions in plants, and they can be more cost-effective, especially in the light of rising costs of inputs mandated in traditional construction. Structures made of prefabricated components have lower maintenance needs vis-a-vis conventional structures and perform better over their long life. "Yet another plus point of such building solutions is that they can incorporate the use of leading or cutting edge eco-friendly technology, which is completely in-sync with building codes," adds Sandhir. Growth deterrents A lack of awareness of offsite technologies here, in comparison to other world markets, has limited the growth of this construction format in India to about 10-15 per cent annually. Some developers shy away from pre-engineered structures because this technology brings limitations of site modifications and multiple on-site changes. Pre-engineered structures require better pre-planning and, where applicable, interfaces with other fatade, MEP, and other building interfaces are to be designed and finalised before manufacturing. "Resistance by a predominantly labour-intensive industry and the high levy of taxes and duties imposed on pre-assembled or prefabricated construction components have been other deterrents to the growth of 'industrialised construction'," opines Sandhir. A paucity of expertise in engineering heavy structures is holding back adoption of this technology as well. According to Arvind Nanda, CEO and Founder Director, Interarch, "Whereas medium and light pre-engineered buildings in India are on a par with the rest of the world, augmenting the available expertise in heavy structures, possibly by securing international talent to increase the offerings in the Indian market, would help expand their scope." Changing fortunes Despite the hurdles in the path of adoption, avenues for pre-engineered structures and prefabricated technologies are expected to grow in the next few years. Speedy construction activity has a strong correlation with economic growth. In this context, Nanda says, "Crucial government reforms and policy changes recently ushered in will hopefully boost economic sentiment and growth, which is good for us. We can meet the need of various industries for high-speed construction that does not compromise on quality." Nanda also sees immense scope for pre-engineered steel construction in the infrastructure sector. "Public and urban facilities are likely to be upgraded and revamped in the next few years," he points out. "Additional capacity for power and urban support networks, transport and communication, etc, will be created. Steel construction is the only way to meet the tight deadlines of such projects." Ports and airports have successfully tested the possibilities of pre-engineered buildings. Manish Garg, President, Steel Building Solutions, Everest Industries, cites the example of New Delhi's T3 Terminal roof as being an outstanding pre-engineered steel structure. Industrial pre-engineered steel structures, remarkable for their sheer size, include the automotive plants of Tata in Anand and Renault-Nissan in Chennai. Real-estate opportunities Clearly, the will to innovate exists. Nanda is sure that interest in offsite technologies from the residential and commercial building segments will pick up. Whereas steel-based pre-engineered buildings are currently considered an option for buildings of height up to 20 m, mostly the likes of factories, warehouses and multi-level car parks, Garg is hopeful that potential customers will gradually think beyond such mundane uses. Change is happening in pockets across India. "Pre-engineered buildings can be designed up to four to five levels and this is being done largely overseas but a few in India as well," says Venugopal K, Head-Sales & Marketing, Zamil Steel. Zamil Steel's more than 55,000 PEBs, a few as old as 35 years, across 90 countries, include five-storey-high commercial centres, G+3 school buildings and hypermarkets created without compromising on the architectural aesthetic commonly adopted in such buildings. "Aesthetics are mainly an outcome of the panelling used for the fatade and sides, which can easily be integrated with a pre-engineered steel frame," he explains. "Two early examples of innovative steel pre-engineered buildings in India are an office building in Hyderabad, multilevel car parking in Lavasa and a school in Kolkata. These help in educating users about the immense potential of such structures. Our rich experience and strong engineering background encourages us to take up design challenges in the PEB system." Meanwhile, BCC Infrastructures is using German precast technology for Phase-II of its Bharat City project. According to Kumar Bharat, Director, BCC Infrastructures, "We're following the lead of Europe and the Middle East, where precast technology has been successfully put to myriad uses. No doubt India has applied this technology for large construction projects like bridges, metro rail and commercial buildings, but now it's time for housing projects to reap the benefits of faster and eco-friendly construction with no compromise on quality." Sandhir sees a huge opportunity for offsite technologies to help the Indian Government meet the existing shortfall of ~27 million affordable housing units in the country. To this end, RICS in partnership with Sam Circle Venture, KieranTimberlake and ProjectWell are working on a framework supporting a concrete panel based integrated system for a single dwelling unit. 'India Concept House', as it's called, is sustainable, affordable and quick to erect. "Targeting clients for affordable housing in Tier-II and -III cities, these units will help reduce construction time by up to 90 per cent with construction costs pegged at Rs 900-1,200 per sq ft," he explains. "Cost savings will kick in both in the short term and over the life of the structure. Substantial savings in material will also be achieved." Clearly, offsite technologies are available in the Indian market. It remains to be seen to what extent the industry adopts them. Let it not be said that offsite technologies were the Indian construction industry's biggest missed opportunity. Case I Precast Structural Components in a Residential Building Execution by: BCC Infrastructures Client: Phase 2, Bharat City Location: Bharat City, Indra Prastha Yojana Ghaziabad, Uttar Pradesh Design features: Wall elements produced by battery moulds, floor slabs produced by stationary beds, wall and floor slabs produced by tilting tables, and precast stairways and balconies feature in these apartments. Weckenmann is the precast component supplier for Bharat City. Other comparable vendors are Vollert and Somer precast. Precast structural components such as slabs, columns, beams, walls, etc, are made of cement and steel and conform to high standards as a result of being produced in controlled environments in off-site plants. Using such components drastically reduces manpower needs, wastage and time, thus making projects easier to manage and less risky. It's also an environment-friendly construction method. Buildings made of precast structural components are more spacious because they can be made without columns and beams. Cost: Same or cheaper than conventional construction methods. Case II Prefabricated Eco-friendly Cottage Execution by: Loom Crafts Client: Panoramic Resorts Location: Old Goa Highway, Panvel Design features: A robust framework made of aerospace grade aluminium and stainless steel forms the core structure of the modular building. Interlocking square panels are fastened to adjoining sections by a patented locking system designed to withstand enormous pressure. The roof is made of maintenance-free, fire-retardant, tensile, PVC-coated fabric membrane. Both the roof and sides are insulated. An extensive selection of ancillary modules is available for interior fittings such as eco-friendly solar power, cloakroom and bathtub, wooden deck flooring and aluminium doors and windows powder-coated in a wide choice of colours. Cost: Rs 3,000 per sq ft (area of each cottage is 550 sq ft) Case III Pre-Engineered Building Execution by: Interarch Client: Tata Motors Location: Dharwad, Maharashtra Design features: Pre-engineered building conforming to green building norms, such as the use of low-VOC paint on buildings, white-roofed plant buildings (SRI =78), special glazing and sun shade for windows, ventilation system for optimum indoor air flow and temperature control, and 4 per cent of total roof and 4 per cent of wall as skylights to reduce the need for artificial lighting. Multilevel mezzanines with heavy collateral load are part of the design and allow for paint equipment installations. Safe construction practices and zero accidents are standout features. At peak time, 500 semiskilled and unskilled workmen were employed. Stringent safety norms were followed throughout. Cost: Rs 86 crore Case IV Pre-Engineered Factory Building Execution by: Alfa Steel Building Solutions Client: Lloyds Line Pipes Location: Mumbai Design features: The client needed a heavy structure, big enough to operate a 15 mt capacity crane. The building has a widest span length of 22 m and a height of 12 m. Its walls are made of colour-coated steel sheets and its roof comprises bare galvalume-coated sheets that minimise heat absorption. Insulation wasn't deemed necessary for this building. Satisfactory building performance has led to the client asking Alfa Steel Building Solutions to extend the structure to 200,000 sq ft. Alfa Steel Building Solution provides its customers with tailored designs that meet their exact specifications, for the best possible solution and price points. Its advantage lies in being a one-stop shop, offering design, manufacturing of roofing and wall cladding components and erection of building systems. Cost: Rs 9.5 crore To share your feedback on this feature, write in at feedback@ASAPPmedia.com