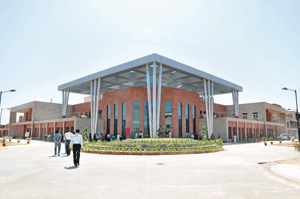
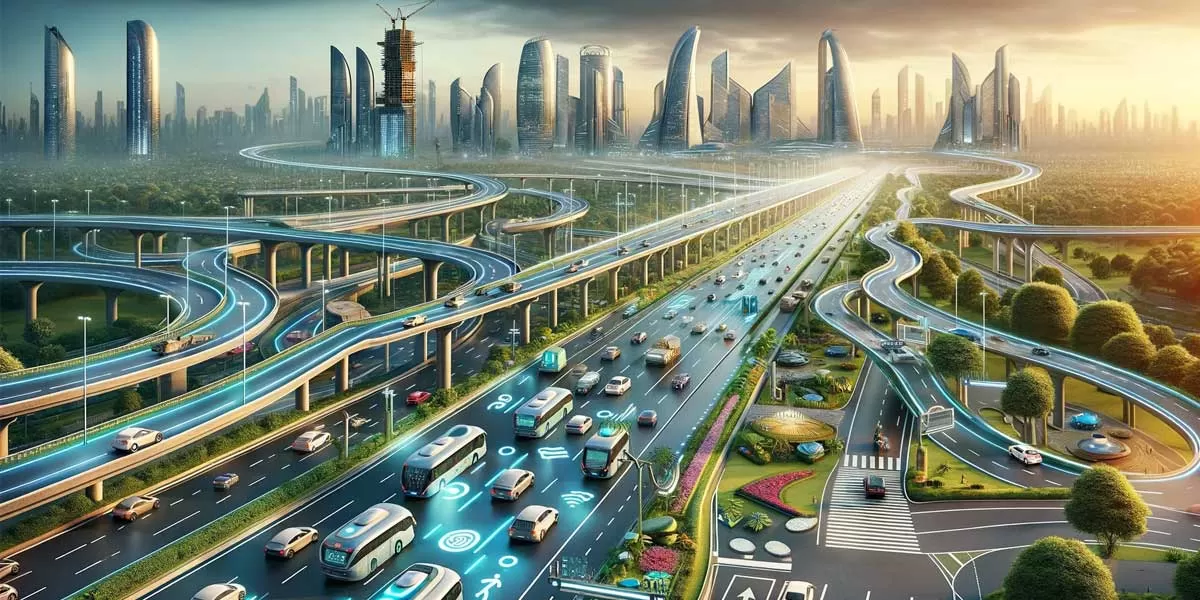
Does India have the 2nd largest road network in the world?
Here are some truths…Pratap Padode, President, FIRST Construction Council unravels some disturbing facts…
Recently there was a lot of chest thumping around India having the second longest road network in the world. Union Minister Nitin Gadkari informed the Lok Sabha that India had the second largest road network in the world, with about 63.32 lakh km of roads as of March 2019. I dug further and found an update from the Ministry of Road Transport & Highways that India has about 66.71 lakh km of road network, which is the second largest in the world. True. But the categories..
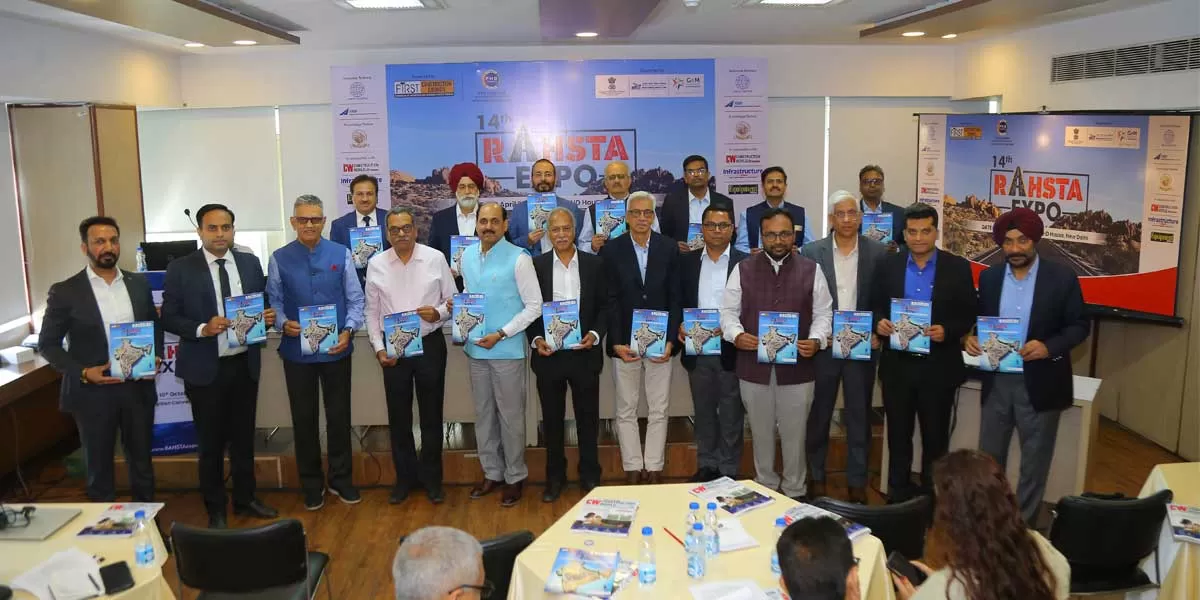
RAHSTA Expo 2024 launched
“The Ministry of Road Transport & Highways has constructed 12,349 km of national highways in 2023-24 - the second highest achievement! In 2020-21 a record 13,327 kms were constructed, the highest so far. The experience of a well-constructed road is no accident but a badly constructed one can cause many,” said Pratap Padode, Founder, FIRST Construction Council (FCC), at the launch of a road show - 14th Roads and Highways Sustainable Technologies and Advancement [RAHSTA] Expo, which will be held from 9-10 October 2024 at Jio Convention Ce..
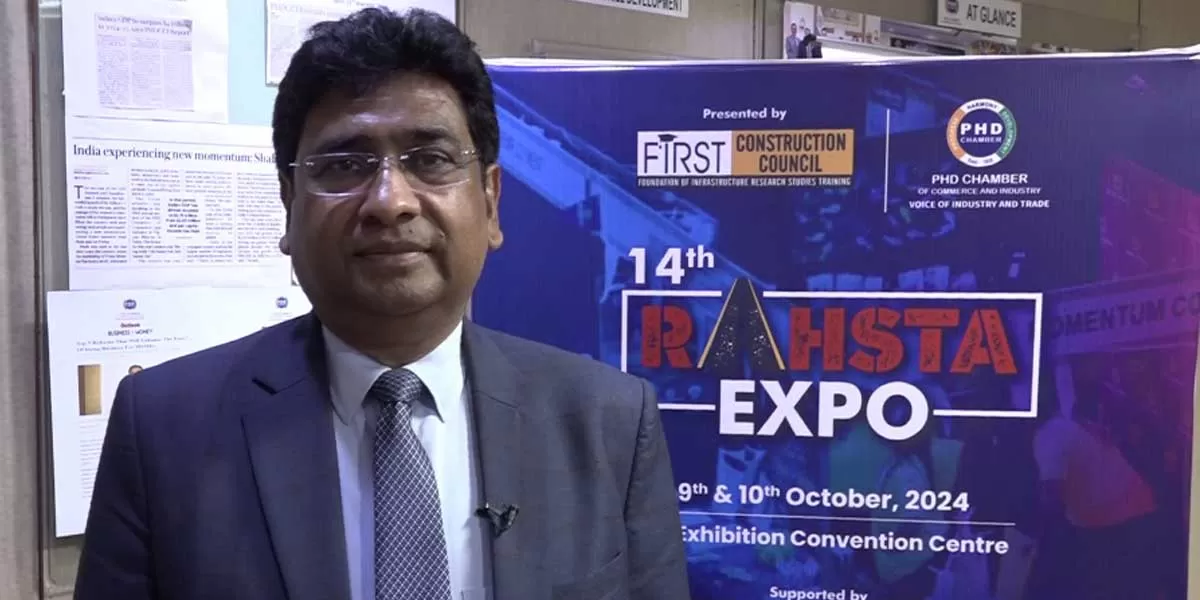
RAHSTA to showcase cutting-edge road construction tech, says NCC Director
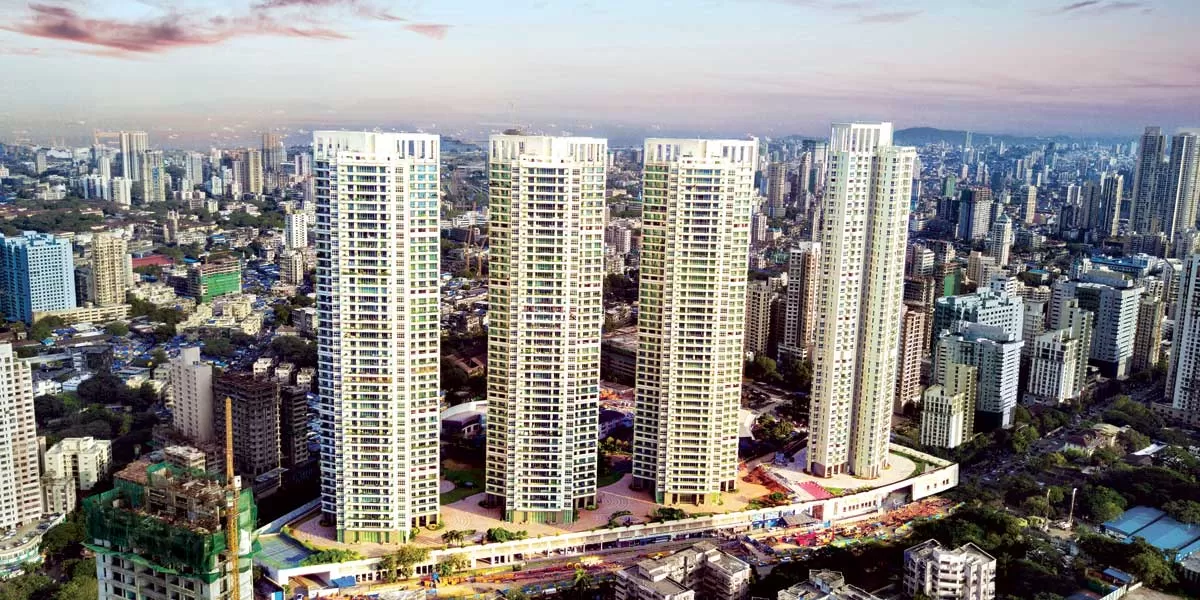
Residents Sceptical of Sahastradhara Road Widening
Residents in Dehradun have raised questions and expressed scepticism regarding the proposed widening project for Sahastradhara Road. The project, aimed at widening the road to accommodate increased traffic, has faced criticism and scrutiny from local residents concerned about its potential impact on the environment and surrounding areas.
The Sahastradhara Road widening project has sparked debate among residents, with some questioning the necessity and feasibility of the initiative. Critics argue that widening the road may lead to the loss of trees, green spaces, and heritage structures ..
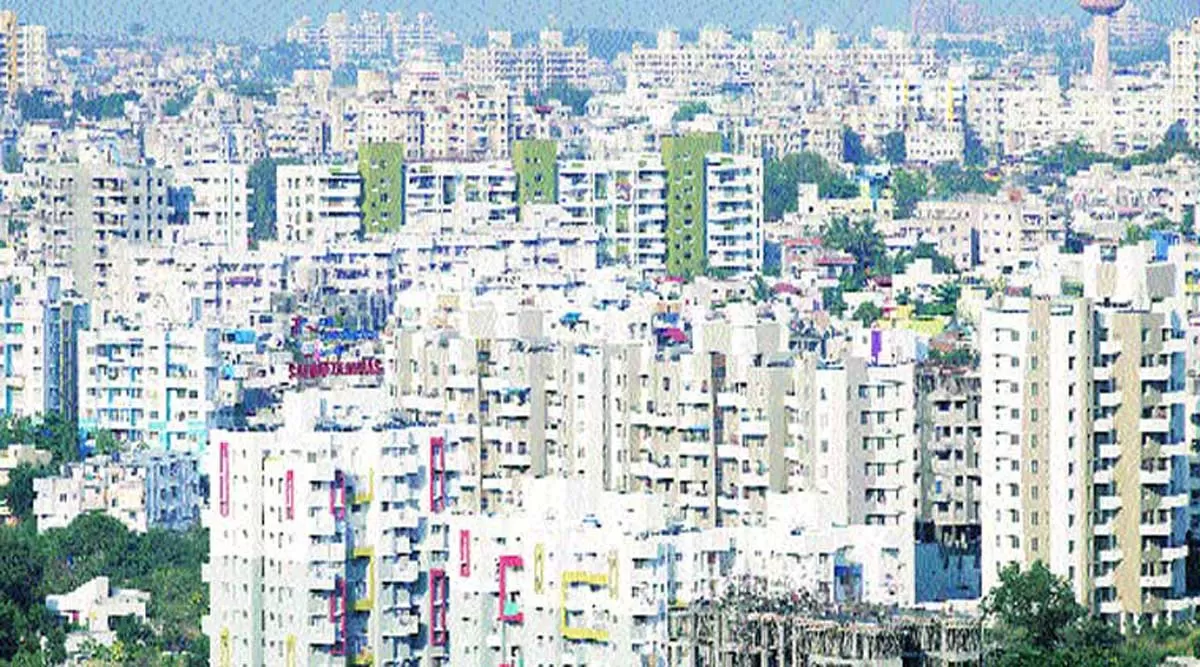
Warburg Pincus Acquires Shriram Housing Finance
Warburg Pincus, a leading global private equity firm, has announced its acquisition of Shriram Housing Finance for an impressive sum of Rs 4,630 crore. This strategic move underscores Warburg Pincus' commitment to expanding its presence in the Indian financial sector and capitalizing on the growing demand for housing finance solutions in the country.
Shriram Housing Finance, a subsidiary of Shriram City Union Finance, has established itself as a key player in the affordable housing finance segment, catering to the needs of millions of aspiring homeowners across India. The acquisition b..