- Home
- Infrastructure Urban
- ECONOMY & POLICY
- Ban and bust
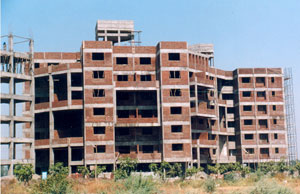
Ban and bust
The mining sector and brick industry seem to be in a limbo. Over the past two years, the Supreme Court has imposed a ban on sand mining in riverbeds in several states including Goa, Karnataka and Maharashtra. And for companies with construction work lined up in northern India, especially Punjab, brick kilns shut down for few months have led to an increase in brick prices.
Indeed, for a country like India, despite the fast clip of construction and the use of highly developed technologies, the availability of construction materials remains a bottleneck. As Arun Sahai, Executive Director, Ahluwalia Contracts (India) Ltd, tells us, "Materials incur 70-80 per cent of the cost in any construction project." In such a scenario, what is the impact material shortage can have on the overall project cost as well as growth of infrastructure?"
Ultimate impact
The availability of fundamental construction materials like stone aggregate, sand and bricks is crucial for the quality and timely construction of projects. "The paucity of these materials has led to cost and time overruns, plaguing the health of the sector and the growth of the country in general," says Mukul Kumar, Executive Director-Retail and Technical, Alpha G:Corp. While he agrees that a large number of states have taken strong measures to curb the sand mafia and the illegal procurement of sand from riverbanks, he says, "The paucity of sand leads to a direct demand-supply equation leading to cost escalations and delays in project delivery. Even where sand is available at higher prices, at times it contains higher than normal percentage of silt and organic impurities, which can be detrimental to the quality of construction."
Sudden implementation of the ban will definitely have an impact on ongoing projects, agrees B Seenaiah, National President, Builder's Association of India. "If a timeframe of six months to a year is given, the industry would look for alternatives accordingly." Sahai seconds Seenaiah on this. "A ban has been imposed without discussing substitutes for that material," he says. "Construction is one activity that has to go on. And if a ban is placed on mining of sand, stone or aggregate, from where will it be carted?" Along with mining being banned in most areas next to Delhi, brick manufacturing has been banned in Delhi, Uttar Pradesh and Haryana. For projects in Delhi, Sahai gets sand transported from places that are 300-500 km (as against 30-40 km earlier). This has further led to heavy material costs and scarcity.
The price tag
When the demand for a product is high, manufacturers inflate its cost as they feel they have a monopoly on the product. "Unplanned government policies can only bring inflation in the industry," Sahai points out. "In mining, for instance, steel industries had some captive mines and many companies in Bengaluru and Karnataka were affected because these mining rights were scrapped. Hence, steel prices increased. So prices may go up overnight; and even if things get back to normal, this price does not then come down to the original cost."
The uncertainty of the availability of a material severely affects the financial health of projects and this, in the case of real estate, eventually leads to an increase in property prices. Seenaiah gives us some figures here: "Following the Supreme Court's ban on excavating sand from river beds and nallas, the cost of sand had eventually increased to Rs 1,600 per tonne from Rs 150-200 per tonne." As for bricks, Kumar adds, "About a year ago, bricks were available at a unit price of Rs 3 per brick, which has risen to more than Rs 5 per brick today." To this, Sahai adds, ôIf I am executing a project at Kota in Rajasthan, where the cost of sand is Rs 12 per cu ft, the same material in Delhi would cost around Rs 36 per cu ft. This applies specifically to stone aggregate. In Kota, this material is easily available. Also, in some areas, there is definitely an advantage because government policies are not uniform."
An alternative
While one cannot deny the need for strong action to put an end to illegal mining of sand, the government cannot possibly ignore the shortage of these crucial fundamental construction materials. But, considering the present scenario, what solutions is the industry adopting?
Flyash brick is one option. However, it has its own shortcomings.
As Seenaiah explains, flyash is available where there are thermal plants. And then, transportation is a major issue - you need to travel 100-200 km to get it. Speaking from personal experience, Sahai adds, "Owing to environmental issues, Delhi has been prohibited from manufacturing bricks. Later, a condition was laid down that bricks could be manufactured, provided flyash, in a particular quantity, was mixed with clay. However, very little flyash has been generated to meet the high demand, making most brick manufacturers question the easy availability of flyash."
Delhi-based Alpha G:Corp has been using stone dust as an effective substitute to sand and flyash brick. "But here too, their vailability is limited," mentions Kumar. "Also, the use of stone dust escalates the cost of construction as it requires a higher percentage of cement (5-10 per cent)." Sahai proposes another substitute: AC (aerated concrete) blocks. "Compared to concrete, these are light in weight. However, in Delhi and NCR, where the requirement is 3,000 cu m, we get only 800 cu m a month," he adds. "Moreover, international products are also available. These are machine made and require volume. They can be a good substitute to our conservative construction material. But this has to be planned."
As for sand, Mumbai-based Hirco has developed a solution - though not a permanent one - for its Panvel site.
A crusher with a vertical shaft impactor has been installed to produce aggregate and crushed sand for the project. As Rustom Dadabhoy, Chief Technology Officer, Hirco and Chief Operating Officer-Panvel Project, Hirco, explains, "Rock is available in abundance at this site and we needed to excavate it for our basement and foundation construction. Hence, we decided to install a crusher and produce aggregate and sand for our building constructions." Hence, depending on site, developers can come up with such innovative techniques as well.
In the case of crushed sand, Seenaiah shares other options as well. "In Hyderabad, for instance, there are a lot of granite quarries and crushed sand can be made. It's similar in the case of Pune and Mumbai." However, this does not apply to Rajasthan and Uttar Pradesh as rock is not available there; dependence is greater on natural sand.
The policy level
This is the ground reality right now. If materials are available in one region, they are further transported to the next. In Hyderabad, for example, sand comes from 200-270 km away. When the Supreme Court imposes a ban without prior intimation, the results are self-evident: deficiency in quality, and increase in cost. The overall inflation impacts the industry. Therefore, immediate steps need to be taken to balance the supply of construction materials, also taking into account the need for environment conservation. Limited extraction of resources, based on scientific standards, along with ensuring availability and viability of substitute materials, seems to be the only way out of this problem.
To share your views on this report, write in at feedback@ASAPPmedia.com
Following the Supreme Court's ban on sand mining and shutting down of brick kilns in some parts of India, Shriyal Sethumadhavan examines the alternatives available and the concerns of the construction industry. The mining sector and brick industry seem to be in a limbo. Over the past two years, the Supreme Court has imposed a ban on sand mining in riverbeds in several states including Goa, Karnataka and Maharashtra. And for companies with construction work lined up in northern India, especially Punjab, brick kilns shut down for few months have led to an increase in brick prices. Indeed, for a country like India, despite the fast clip of construction and the use of highly developed technologies, the availability of construction materials remains a bottleneck. As Arun Sahai, Executive Director, Ahluwalia Contracts (India) Ltd, tells us, "Materials incur 70-80 per cent of the cost in any construction project." In such a scenario, what is the impact material shortage can have on the overall project cost as well as growth of infrastructure?" Ultimate impact The availability of fundamental construction materials like stone aggregate, sand and bricks is crucial for the quality and timely construction of projects. "The paucity of these materials has led to cost and time overruns, plaguing the health of the sector and the growth of the country in general," says Mukul Kumar, Executive Director-Retail and Technical, Alpha G:Corp. While he agrees that a large number of states have taken strong measures to curb the sand mafia and the illegal procurement of sand from riverbanks, he says, "The paucity of sand leads to a direct demand-supply equation leading to cost escalations and delays in project delivery. Even where sand is available at higher prices, at times it contains higher than normal percentage of silt and organic impurities, which can be detrimental to the quality of construction." Sudden implementation of the ban will definitely have an impact on ongoing projects, agrees B Seenaiah, National President, Builder's Association of India. "If a timeframe of six months to a year is given, the industry would look for alternatives accordingly." Sahai seconds Seenaiah on this. "A ban has been imposed without discussing substitutes for that material," he says. "Construction is one activity that has to go on. And if a ban is placed on mining of sand, stone or aggregate, from where will it be carted?" Along with mining being banned in most areas next to Delhi, brick manufacturing has been banned in Delhi, Uttar Pradesh and Haryana. For projects in Delhi, Sahai gets sand transported from places that are 300-500 km (as against 30-40 km earlier). This has further led to heavy material costs and scarcity. The price tag When the demand for a product is high, manufacturers inflate its cost as they feel they have a monopoly on the product. "Unplanned government policies can only bring inflation in the industry," Sahai points out. "In mining, for instance, steel industries had some captive mines and many companies in Bengaluru and Karnataka were affected because these mining rights were scrapped. Hence, steel prices increased. So prices may go up overnight; and even if things get back to normal, this price does not then come down to the original cost." The uncertainty of the availability of a material severely affects the financial health of projects and this, in the case of real estate, eventually leads to an increase in property prices. Seenaiah gives us some figures here: "Following the Supreme Court's ban on excavating sand from river beds and nallas, the cost of sand had eventually increased to Rs 1,600 per tonne from Rs 150-200 per tonne." As for bricks, Kumar adds, "About a year ago, bricks were available at a unit price of Rs 3 per brick, which has risen to more than Rs 5 per brick today." To this, Sahai adds, ôIf I am executing a project at Kota in Rajasthan, where the cost of sand is Rs 12 per cu ft, the same material in Delhi would cost around Rs 36 per cu ft. This applies specifically to stone aggregate. In Kota, this material is easily available. Also, in some areas, there is definitely an advantage because government policies are not uniform." An alternative While one cannot deny the need for strong action to put an end to illegal mining of sand, the government cannot possibly ignore the shortage of these crucial fundamental construction materials. But, considering the present scenario, what solutions is the industry adopting? Flyash brick is one option. However, it has its own shortcomings. As Seenaiah explains, flyash is available where there are thermal plants. And then, transportation is a major issue - you need to travel 100-200 km to get it. Speaking from personal experience, Sahai adds, "Owing to environmental issues, Delhi has been prohibited from manufacturing bricks. Later, a condition was laid down that bricks could be manufactured, provided flyash, in a particular quantity, was mixed with clay. However, very little flyash has been generated to meet the high demand, making most brick manufacturers question the easy availability of flyash." Delhi-based Alpha G:Corp has been using stone dust as an effective substitute to sand and flyash brick. "But here too, their vailability is limited," mentions Kumar. "Also, the use of stone dust escalates the cost of construction as it requires a higher percentage of cement (5-10 per cent)." Sahai proposes another substitute: AC (aerated concrete) blocks. "Compared to concrete, these are light in weight. However, in Delhi and NCR, where the requirement is 3,000 cu m, we get only 800 cu m a month," he adds. "Moreover, international products are also available. These are machine made and require volume. They can be a good substitute to our conservative construction material. But this has to be planned." As for sand, Mumbai-based Hirco has developed a solution - though not a permanent one - for its Panvel site. A crusher with a vertical shaft impactor has been installed to produce aggregate and crushed sand for the project. As Rustom Dadabhoy, Chief Technology Officer, Hirco and Chief Operating Officer-Panvel Project, Hirco, explains, "Rock is available in abundance at this site and we needed to excavate it for our basement and foundation construction. Hence, we decided to install a crusher and produce aggregate and sand for our building constructions." Hence, depending on site, developers can come up with such innovative techniques as well. In the case of crushed sand, Seenaiah shares other options as well. "In Hyderabad, for instance, there are a lot of granite quarries and crushed sand can be made. It's similar in the case of Pune and Mumbai." However, this does not apply to Rajasthan and Uttar Pradesh as rock is not available there; dependence is greater on natural sand. The policy level This is the ground reality right now. If materials are available in one region, they are further transported to the next. In Hyderabad, for example, sand comes from 200-270 km away. When the Supreme Court imposes a ban without prior intimation, the results are self-evident: deficiency in quality, and increase in cost. The overall inflation impacts the industry. Therefore, immediate steps need to be taken to balance the supply of construction materials, also taking into account the need for environment conservation. Limited extraction of resources, based on scientific standards, along with ensuring availability and viability of substitute materials, seems to be the only way out of this problem. To share your views on this report, write in at feedback@ASAPPmedia.com