- Home
- Infrastructure Urban
- WATER & WASTE
- The future of waterproofing
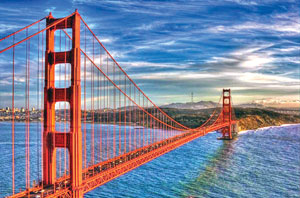
The future of waterproofing
Polymer rubber gel technology from The RE-Systems Group is the future of waterproofing for underground structures. This technology has been proven to meet the unique challenges of underground construction. It has excelled in the requirements for successful waterproofing of below-grade construction for cut-and-cover applications. The key characteristics for polymer rubber gel waterproofing systems are adhesion to the substrate, responsiveness to substrate movement, non-curing, self-healing and chemical resistance.
Cut-and-cover waterproofing poses distinct challenges in design and application. Proper selection of the waterproofing system and appropriate engineering details are essential to the success of this application. Two distinct methods of application are used for waterproofing a cut-and-cover structure. The first is the positive side application, which involves the application of the waterproofing membrane directly to the surface of a concrete substrate. The second is the blind side application, which involves the application of waterproofing to the soil support of excavation, i.e. sheet pile wall, secant pile wall, CDSM, etc.
For blind side applications, the structural wall is formed against the waterproofing membrane. Polymer rubber gel waterproofing systems have excelled in meeting the requirements of challenging cut-and-cover waterproofing applications. Developed specifically for the waterproofing industry, polymer rubber gel comprises a modified rubberised asphalt emulsion. However, unlike typical rubberised asphalt materials, polymer rubber gel´s polymers never completely cross link, which helps retain the gel in a semi-cured state. This innovation enables polymer rubber gel to act as an exceptionally flexible, adhesive, continuously self-healing membrane. Composite waterproofing systems, a new concept in waterproofing, utilise a polymer rubber gel component that exhibits superior elongation properties, adhesion and self-healing ability.
The components
A polymer rubber gel waterproofing system comprises a layer of polymer rubber gel at a minimum thickness of 2.5 mm +/-.5 mm combined with a sheet membrane laminate such as LLDPE or HDPE. Viscosities of polymer rubber gel allow for multiple delivery methods, including application by spray, trowel and preformed waterproofing sheet. The flexible, non-curing, highly adhesive polymer rubber gel and the durable, chemical-resistant, hydrostatic pressure resistant LLDPE or HDPE sheet are combined to create a dynamically responsive, high-performance waterproofing system for cut-and-cover construction. Application of a polymer rubber gel system is efficient and economical.
Vital features
Polymer rubber gel exhibits numerous unique physical characteristics that make it an ideal component to a composite waterproofing system. The physical characteristics that are distinctive to polymer rubber gel are principally the gel´s ability to remain in an uncured state and its extreme cohesion and adhesion attributes. The gel´s elongation to break is greater than 350 per cent (ASTM C1135). Polymer rubber gel´s adhesion to concrete is rated as one for excellent (ASTM D412-98). Its self-healing ability has been tested to 3.0 bar of direct hydrostatic head (2-mm thickness of polymer rubber gel membrane).
Plus points
The shear force of the waterproofing membrane against the concrete substrate caused by seismic activity, foundation settlement, vibration, thermal expansion and contraction or shrinkage cracks in concrete can cause traditional waterproofing membranes to de-bond from the substrate and fail. As polymer rubber gel is a non-cured flexible gel, it effectively creates a ball bearing effect that allows it to dynamically respond to the movement of two substrates moving independently of one another. This non-cured, flexible bond retains the integrity of the waterproofing envelope better than the traditionally fully adhered, cured waterproofing systems.
Owing to polymer rubber gel´s non-curing characteristic, it has the exclusive ability to repeatedly self-heal under direct hydrostatic pressure. This helps mitigate some common pre-construction waterproofing system damages such as accidental form work penetrations, construction site debris (nails, fasteners, etc) or applicator installation mistakes. This allows for a greater ´margin of error´ in the waterproofing system, resulting in a system that achieves a higher level of predictable performance.
Case study
Polymer rubber gel was able to help seismic, structural and traffic safety leading to the Golden Gate Bridge in San Francisco. On one of the most iconic roadways in the US, major improvements in design will open up enhanced views of San Francisco Bay, support rehabilitation of endangered tidal marshlands and improve pedestrian networks throughout the Presidio of San Francisco.
The replacement of Doyle Drive with the Presidio Parkway is a collaborative effort led by the California Department of Transportation, the San Francisco County Transportation Authority, and the Federal Highway Administration. Segregated into two phases, Phase-1 was completed in April 2012. The first phase included the construction of a seismically stable replacement viaduct and tunnel. Phase-2 began in the fall of 2012 and is scheduled for completion in 2016.
A polymer rubber gel waterproofing system has been specified for use on all tunnels within the scope of work. The project design calls for the construction of four highway tunnels, constructed utilising the open cut method. Phase-1 (tunnel portion) was designed by Parsons Brinckerhoff and Arup. HNTB is responsible for the design of Phase-2. Phase-1 consisted of the South Bound Battery Tunnel, a substation building beneath the tunnel, southbound high viaduct and other structures and roadway work. The total square footage for the installed waterproofing is greater than 1,000,000 sq ft. Because of the significance of this particular project and the first-time use of this product on the State Highway System, a pre-evaluation was completed and construction evaluation is ongoing of the polymer rubber gel waterproofing system by the California Department of Transportation.
Many waterproofing systems were evaluated for the specification of the Presidio Parkway project including typical bentonite panel and pressure adhesive systems. However, known limitations with these systems in seismic areas precluded their use. Structural engineers were particularly concerned with improving seismic performance of the construction. Indeed, polymer rubber gel´s superior flexibility and self-healing characteristics help ensure that the tunnel waterproofing system can better withstand seismic events.
Polymer rubber gel technology finds its application in some of the world´s most challenging infrastructure projects highlights, JOHN HUH. Polymer rubber gel technology from The RE-Systems Group is the future of waterproofing for underground structures. This technology has been proven to meet the unique challenges of underground construction. It has excelled in the requirements for successful waterproofing of below-grade construction for cut-and-cover applications. The key characteristics for polymer rubber gel waterproofing systems are adhesion to the substrate, responsiveness to substrate movement, non-curing, self-healing and chemical resistance. Cut-and-cover waterproofing poses distinct challenges in design and application. Proper selection of the waterproofing system and appropriate engineering details are essential to the success of this application. Two distinct methods of application are used for waterproofing a cut-and-cover structure. The first is the positive side application, which involves the application of the waterproofing membrane directly to the surface of a concrete substrate. The second is the blind side application, which involves the application of waterproofing to the soil support of excavation, i.e. sheet pile wall, secant pile wall, CDSM, etc. For blind side applications, the structural wall is formed against the waterproofing membrane. Polymer rubber gel waterproofing systems have excelled in meeting the requirements of challenging cut-and-cover waterproofing applications. Developed specifically for the waterproofing industry, polymer rubber gel comprises a modified rubberised asphalt emulsion. However, unlike typical rubberised asphalt materials, polymer rubber gel´s polymers never completely cross link, which helps retain the gel in a semi-cured state. This innovation enables polymer rubber gel to act as an exceptionally flexible, adhesive, continuously self-healing membrane. Composite waterproofing systems, a new concept in waterproofing, utilise a polymer rubber gel component that exhibits superior elongation properties, adhesion and self-healing ability. The components A polymer rubber gel waterproofing system comprises a layer of polymer rubber gel at a minimum thickness of 2.5 mm +/-.5 mm combined with a sheet membrane laminate such as LLDPE or HDPE. Viscosities of polymer rubber gel allow for multiple delivery methods, including application by spray, trowel and preformed waterproofing sheet. The flexible, non-curing, highly adhesive polymer rubber gel and the durable, chemical-resistant, hydrostatic pressure resistant LLDPE or HDPE sheet are combined to create a dynamically responsive, high-performance waterproofing system for cut-and-cover construction. Application of a polymer rubber gel system is efficient and economical. Vital features Polymer rubber gel exhibits numerous unique physical characteristics that make it an ideal component to a composite waterproofing system. The physical characteristics that are distinctive to polymer rubber gel are principally the gel´s ability to remain in an uncured state and its extreme cohesion and adhesion attributes. The gel´s elongation to break is greater than 350 per cent (ASTM C1135). Polymer rubber gel´s adhesion to concrete is rated as one for excellent (ASTM D412-98). Its self-healing ability has been tested to 3.0 bar of direct hydrostatic head (2-mm thickness of polymer rubber gel membrane). Plus points The shear force of the waterproofing membrane against the concrete substrate caused by seismic activity, foundation settlement, vibration, thermal expansion and contraction or shrinkage cracks in concrete can cause traditional waterproofing membranes to de-bond from the substrate and fail. As polymer rubber gel is a non-cured flexible gel, it effectively creates a ball bearing effect that allows it to dynamically respond to the movement of two substrates moving independently of one another. This non-cured, flexible bond retains the integrity of the waterproofing envelope better than the traditionally fully adhered, cured waterproofing systems. Owing to polymer rubber gel´s non-curing characteristic, it has the exclusive ability to repeatedly self-heal under direct hydrostatic pressure. This helps mitigate some common pre-construction waterproofing system damages such as accidental form work penetrations, construction site debris (nails, fasteners, etc) or applicator installation mistakes. This allows for a greater ´margin of error´ in the waterproofing system, resulting in a system that achieves a higher level of predictable performance. Case study Polymer rubber gel was able to help seismic, structural and traffic safety leading to the Golden Gate Bridge in San Francisco. On one of the most iconic roadways in the US, major improvements in design will open up enhanced views of San Francisco Bay, support rehabilitation of endangered tidal marshlands and improve pedestrian networks throughout the Presidio of San Francisco. The replacement of Doyle Drive with the Presidio Parkway is a collaborative effort led by the California Department of Transportation, the San Francisco County Transportation Authority, and the Federal Highway Administration. Segregated into two phases, Phase-1 was completed in April 2012. The first phase included the construction of a seismically stable replacement viaduct and tunnel. Phase-2 began in the fall of 2012 and is scheduled for completion in 2016. A polymer rubber gel waterproofing system has been specified for use on all tunnels within the scope of work. The project design calls for the construction of four highway tunnels, constructed utilising the open cut method. Phase-1 (tunnel portion) was designed by Parsons Brinckerhoff and Arup. HNTB is responsible for the design of Phase-2. Phase-1 consisted of the South Bound Battery Tunnel, a substation building beneath the tunnel, southbound high viaduct and other structures and roadway work. The total square footage for the installed waterproofing is greater than 1,000,000 sq ft. Because of the significance of this particular project and the first-time use of this product on the State Highway System, a pre-evaluation was completed and construction evaluation is ongoing of the polymer rubber gel waterproofing system by the California Department of Transportation. Many waterproofing systems were evaluated for the specification of the Presidio Parkway project including typical bentonite panel and pressure adhesive systems. However, known limitations with these systems in seismic areas precluded their use. Structural engineers were particularly concerned with improving seismic performance of the construction. Indeed, polymer rubber gel´s superior flexibility and self-healing characteristics help ensure that the tunnel waterproofing system can better withstand seismic events.