
Modern formwork system is designed to minimise the operation
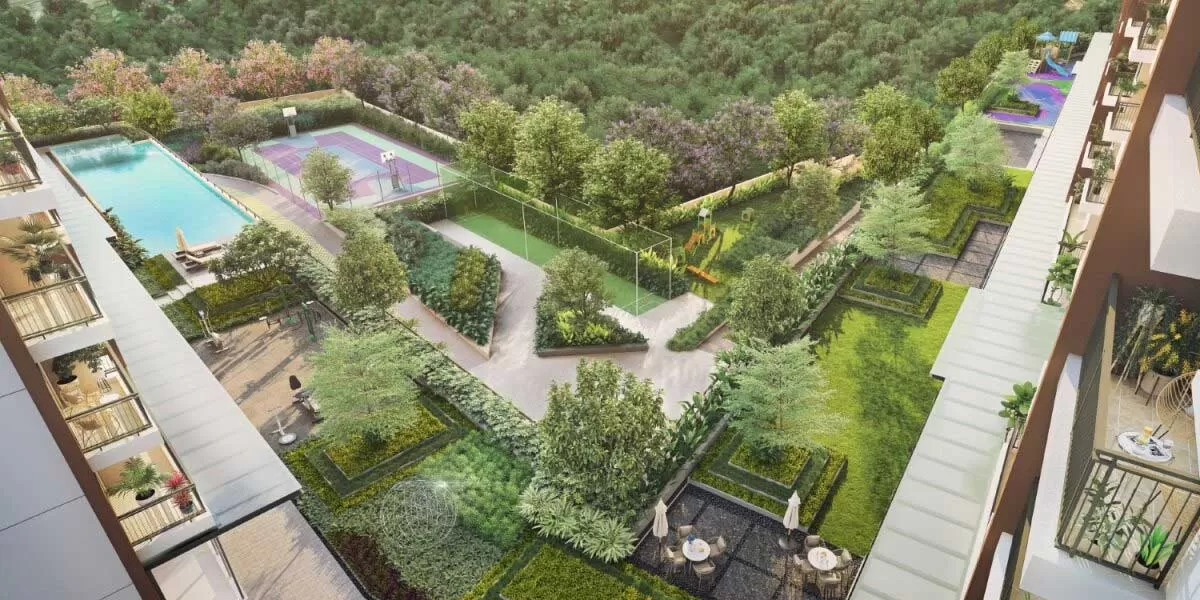
Shapoorji Pallonji Real Estate Launches Premium Residential Project VANAHA Verdant in Pune
Shapoorji Pallonji Real Estate (SPRE), one of India’s most respected real estate developers, has announced the launch of VANAHA Verdant, a premium residential project located within its flagship 1000-acre integrated township, VANAHA, near Bavdhan, Pune. Spread over approximately 5 acre, the new development is expected to offer nearly 10 lakh square feet of saleable area, with projected revenue potential of around Rs 8 billion. Following the success of earlier phases within the township, VANAHA Verdant reinforces SPRE’s vision of providing thoughtfully designed homes that align with ev..
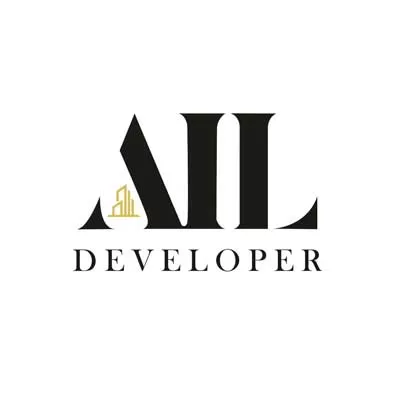
AIL Developer Announces 250-Acre Gated Township Near Shiroda Beach in North of Goa
AIL Developer, one of India’s fastest-growing real estate firms, has announced a 250-acre gated township project in the North of Goa region, minutes from Shiroda Beach. Touted as the area’s first large-scale, master-planned residential community, the project will offer clear-title plots with premium infrastructure and high-end lifestyle amenities. Strategically located 6–8 minutes from Shiroda Beach and 20 minutes from MOPA Airport, the site is also near Arambol and Malewad Junction, ensuring seamless access to Goa’s northern coastline while avoiding congestion and legal complexit..
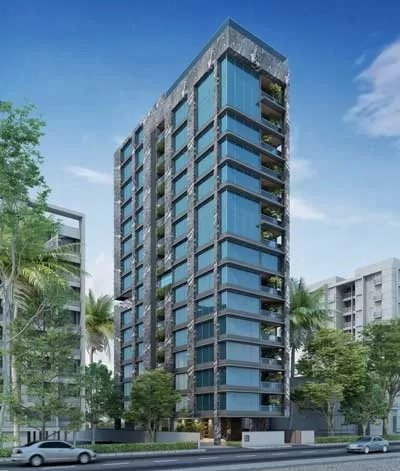
Notandas Realty Invests Rs 4.5 billion in Two Juhu Projects
Notandas Realty has launched two luxury residential projects—Notan Tides and Notan DC—in Juhu, Mumbai, with a combined investment of Rs 4.5 billion. Notan Tides, a larger redevelopment project designed by ARA Designs, will receive Rs 3 billion. The smaller, high-end Notan DC, led by SEZA, will see Rs 1.5 billion in investment. Both projects have secured regulatory approvals and are expected to be completed within 30 months. This expansion brings Notandas Realty’s total Juhu portfolio to four developments, reinforcing its commitment to upscale residential offerings in one of Mumbai’s..