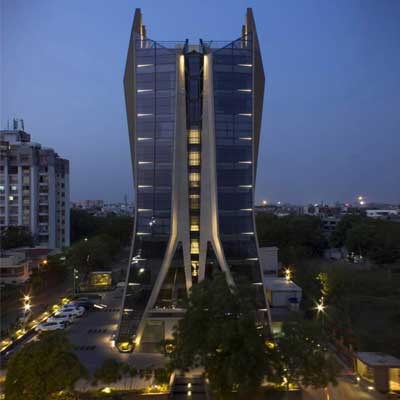
"Master the Art of Freelancing Success"">
Companies that upgrade their technologies will be able to tackle schedule delays, cost overruns and safety issues, says TARAL SHAH.
The rise of construction projects will see an increase acceptance of advanced construction technolo-gies, including AI, Internet of Things (IoT), smart machines and automation. Successful companies will be those that understand how and where IoT technologies and solutions will drive opportunities for operational improvements, new and enhanced products and services, and completely new business models.
In the past decade, the construction industry has seen many changes. However, the construction engineering sector is one of the least digitised worldwide and India is no exception. Right now, ac-cording to research on construction trends, only 9 per cent of construction firms believe they are ready for digital transformation—this could be owing to factors such as initial setup costs and hu-man acceptance. However, technology is essential for an energy-efficient and green industry that saves human effort and material wastage and creates smart, maintenance-free, durable structures.
India has potential to lead the world in technology. With digital computers bringing automation to tasks and processes, the construction industry has already seen a significant improvement in terms of project turnaround time, quality of products, safety of labour and cost-effectiveness of projects. In the past, the industry would make huge investments in construction equipment; now, it’s time to invest in superior technology like building information modelling (BIM), augmented reality (AR) and robotic innovation.
The technology journey
In the past, construction companies faced the challenges of creating and sharing design information in real time to engineers. It was a difficult job for consultants to draw up a sketch and project out-lines but then AutoCAD came along and made it easy. Since AutoCAD, a lot of software has been developed for architectural and structural designs.
Over time, the construction industry began to see the need for precise planning and network and resource management prior to onsite execution. When AI began to enter various industries with the promise of lucrative commercial applications, the potential benefits in terms of productivity for the construction sector, too, became apparent.
Now, technologies such as BIM and AR are assisting the construction industry to see the future. These technologies represent buildings digitally, allowing the visualisation of architecture as well as the structural grid and elevation integrated with services so that projects can be executed without error. This reduces the number of man hours and can cut down the overall project duration.
3D for tomorrow
While IoT and BIM will continue to see steady growth, the next decade will see the development of 3D printing and expansion of blockchain and robotics.
3D construction printing refers to various technologies that use 3D printing as a core method to fab-ricate buildings or construction components. Alternative terms used include autonomous robotic construction system (ARCS), large-scale additive manufacturing (LSAM) or freeform construction (FC); there are also subgroups, such as 3D Concrete, which refers to concrete extrusion technolo-gies.
The variety of 3D printing methods used for construction include extrusion (concrete/cement, wax, foam, polymers), powder bonding (polymer bond, reactive bond, sintering) and additive welding. 3D printing at the construction scale will have a wide variety of applications within the private, commercial, industrial and public sectors. Further, this technology also ensures that the built struc-ture remains crack-free for 100 years or more. The composition used in the premix is so solid that the US uses this technology to make military bunkers. This technology is eco-friendly as well. The general usage of water while curing a house during construction is very high. But with this technol-ogy, water is added to the premix and is not needed for curing. This saves a lot of water. Indeed, concrete 3D printing helps save time, effort and material compared to traditional construction methods. And while 3D printers are not capable of creating a fully functional building (only the frame and walls), they can be used to print bridges, small houses, benches and so on.
All considered, digitisation is the future of the construction industry. Companies that quickly move to upgrade their technologies will gain a distinct advantage and be able to tackle the problems of low profitability rate, schedule delays, cost overruns and safety issues. At Shivalik, we are exploring opportunities to implement innovations to optimise time and deliver our projects 30 per cent faster. Being a frontrunner in Gujarat real estate, we have upgraded ourselves with smart technologies, advanced monitoring system, BIM and best construction practices.About the Author: Taral Shah, Managing Director, Shivalik Group, is a leader who believes in precision and has high hopes for the Indian real estate and infrastructure sectors. “What India has done in the past four decades, we have to do in the next 10 years,” he firmly believes.