
Span of Success
Read full article
CW Gold Benefits
- Weekly Industry Updates
- Industry Feature Stories
- Premium Newsletter Access
- Building Material Prices (weekly) + trends/analysis
- Best Stories from our sister publications - Indian Cement Review, Equipment India, Infrastructure Today
- Sector focused Research Reports
- Sector Wise Updates (infrastructure, cement, equipment & construction) + trend analysis
- Exclusive text & video interviews
- Digital Delivery
- Financial Data for publically listed companies + Analysis
- Preconceptual Projects in the pipeline PAN India
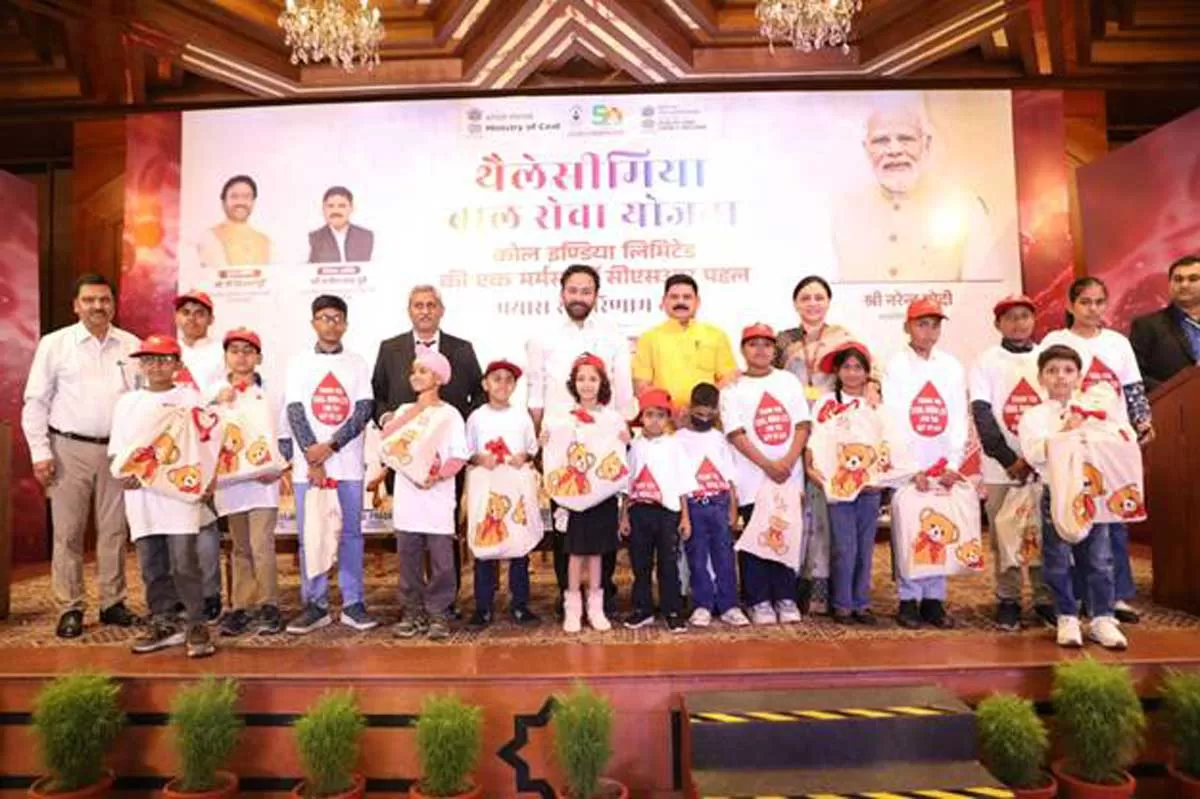
Coal India’s Thalassemia Scheme Hits Milestone, Minister Seeks Expansion
On the occasion of World Thalassemia Day 2025, Coal India (CIL), in collaboration with the Ministry of Coal and the Ministry of Health & Family Welfare, commemorated the remarkable success of its flagship CSR initiative, the Thalassemia Bal Sewa Yojana (TBSY), at a special event held at Hotel Ashok, New Delhi. The scheme, which supports free bone marrow transplants for children suffering from thalassemia and aplastic anemia, has emerged as a life-transforming initiative for hundreds of families across the country. Minister of Coal and Mines, G Kishan Reddy, graced the occasion as the Chief Gu..
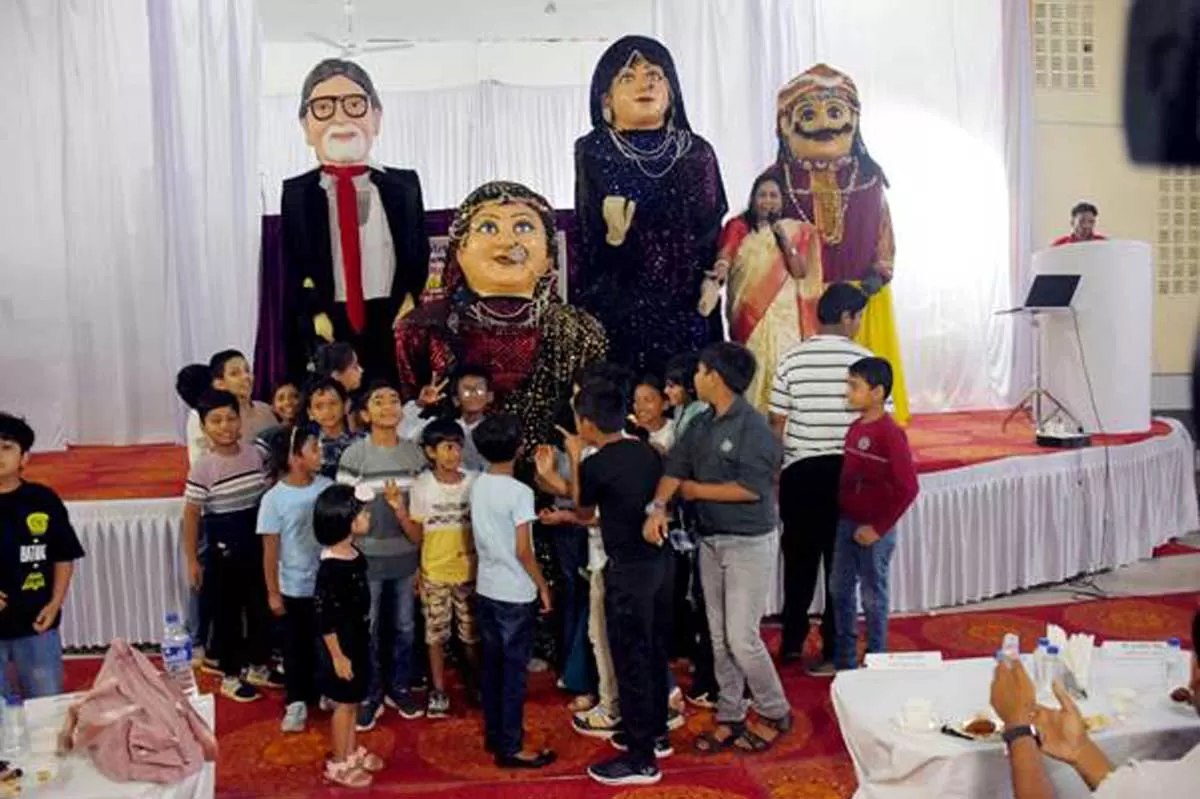
SECL Hosts First Sneh Milan Mela to Boost Community Ties
In a novel initiative to foster goodwill and deeper engagement with local communities, South Eastern Coalfields (SECL) recently organized its first-ever ‘Sneh Milan Mela’ in Surajpur district of Chhattisgarh under its Bhatgaon Area. The event, which brought together SECL employees, their families, and nearby villagers, is part of SECL’s broader approach to build trust and cooperation essential for smooth land acquisition to facilitate the expansion of mining operations. The vibrant gathering featured cultural performances, including songs, dances, and a highlight puppet act with the ..

Revised SHAKTI Policy Eases Coal Allocation for Power Sector
The Cabinet Committee on Economic Affairs (CCEA) in the meeting held on 07.05.2025, chaired by the Prime Minister Narendra Modi, has accorded its approval for the Revised SHAKTI (Scheme for Harnessing and Allocating Koyala Transparently in India) Policy for Coal Allocation to Power Sector. The Revised SHAKTI Policy adds to the series of coal sector reforms being undertaken by the Government. With the introduction of SHAKTI Policy in 2017, there was a paradigm shift of coal allocation mechanism from a nomination-based regime to a more transparent way of allocation of coal linkages through auct..