- Home
- Real Estate
- The Cost Crunch
The Cost Crunch
Suddenly and silently, the price of construction has gone up dramatically in India. Construction World speaks to contractors, developers and building material majors to find out why and assess the implications for the industry and end-users.
Fact: Construction is not just more prolific than ever before, it's also much more expensive.
Figure: The cost of construction increased 8.4 per cent in 2010-11 as against just 4 per cent in 2009-10.
Now that we've grabbed your attention, let's look at the whys of it all.
The prices of cement and steel, the key raw materials for construction, have shot up sharply in recent months. Steel prices have risen by 10 per cent while retail numbers of cement have shot up 34 per cent since the beginning of 2011; these have been joined by other construction essentials, such as sand, aggregates and bricks. Even more significant, labour, freight and transportation costs have also spiked (see ‘Under Pressure', on page 90).
An upward spiral
The industry is feeling the pinch. “Inflation in India has seen a drastic rise over the past few years,” rues BK Vinayak, CEO, Omaxe Infrastructure. “There are many reasons; most important is the rising demand for goods and services owing to the fast growing economy, leading to unsystematic inflation resulting in high prices. Rise in global inflation levels owing to shortfall in supply to meet the demand of growing economies, growing money supply because of increase in government spending and the pressure to meet deficit financing, increasing in wages and tax rates, also lead to increase in overall prices for goods and services, among others.” Speaking specifically of construction, he points out how there is overall scarcity of skilled labour on account of tremendous infrastructure development in the country. “Further, rise in steel, cement, sand, aggregate and brick prices may jack up construction costs by 20 per cent,” he adds. “Steel accounts for 20-35 per cent of cost of construction, depending on the project, and cement accounts for 15-20 per cent of costs.”
“Prices of construction materials such as steel and cement have increased significantly from the past few quarters, thus exerting great pressure on our project execution and procurement teams to keep our margins intact,” affirms AK Misra, Executive Director and Chief Operating Officer, Tata Projects Ltd. “The increases have primarily been because of high global demand for commodities, manufactured goods, higher production and transportation costs, partly owing to high fuel prices. Diesel prices have gone up significantly over the past few months, increasing overall project cost. Also, in the past decade, the cost of construction labour has gone up by about 25 per cent, higher than the general inflation rate. Increased labour costs are also a major contributor to increased utility construction costs because of rise in demand for specialised and skilled labour over current or projected supply.”
Harshavardhan Neotia, Chairman, Ambuja Realty, couldn't agree more. “Generally there has been a cost increase across the board,” he says. “Prices of all basic raw materials such as steel, cement, sand, aggregates and bricks have gone up in the past year owing to a combination of increase in fuel costs and general increase in costs of inputs and labour. All this has a direct impact on the cost of construction.”
“The construction industry is reeling under the increasing cost of building materials,” admits Suresh Kumar, Managing Director, Vijay Shanthi Builders Ltd. “This is truly the age of construction in India, with the industry recording a consistent growth of 35-40 per cent over the past two years. But this growth has come at a cost: the increasing cost of raw material, labour, transportation and acquisition of land. Several supply-side constraints are responsible for inflationary pressure on the building materials sector, where the rate of raw materials has increased by about 45-50 per cent in the past year. Some of these are industry-related, such as the shortage of raw materials, rising energy costs, low productivity of the industry, distribution and marketing problems, while others are exogenous in character. Most important among the exogenous factors is the economic and regulatory environment in which the building materials industry operates.”
For his part, Sushil Mantri, Chairman and Managing Director, Mantri Developers Pvt Ltd, offers a cause-and-effect analysis for rising costs across several verticals. As for steel, while pointing out the increase in demand arising out of additional requirement in public works, he draws our attention to the increase of coking coal prices following the floods in Australia that put many mines out of operation as well as the volatility in raw material prices and power cut and local disturbances in Hyderabad. The result: “Escalation in construction costs by Rs 40 per sq ft and a slowdown in procurement.” Moving on to cement, he attributed the price rise to cartels formed by cement manufacturers to create artificial shortage through underproduction and asserted that it has led to climbing construction costs by Rs 130 per sq ft as well as a slowdown in construction activity owing to non-availability.
Mantri blames the recent government restrictions in sand scooping and mining for sand prices doubling, which has escalated construction cost by Rs 35 per sq ft and once again led to slowdown. And a hike in petro-product prices has led to a rise in freight and transport prices, further escalating construction costs. As for labour, he says, “Inflationary pressures leading to an abnormal price rise in food and other basic living costs have pushed the price of labour upward. Additionally, the depletion of the migratory workforce owing to improved locally generated employment opportunity from government welfare schemes has led to scarcity of labour and increased costs.” This, according to Mantri, has led to escalation in construction cost by at least
Rs 75 per sq ft and slowdown of work because of labour shortage.
Here, and there
Making confusion worse confounded – at least in terms of working out strategies to deal with increased costs – is the fact that building material costs vary from region to region.
“While steel prices do not vary much over a period of time as well as over a region, as prices are controlled by only a few manufacturers, cement prices vary a lot over regions and over time,” says Misra. “Cement manufacturers are present in almost every state, so they try to drive their own prices. Hence, state governments need to take stock of a situation where cement manufacturers try to form a cartel, which would make a price check very difficult. Moreover, states that have production capability enjoy slightly lower prices because of the cost of logistics.”
To this Vinayak adds, “The cost rise across the country may not be uniform owing to geographical reasons and availability of resou-rces. For example, prices for cement in Mumbai have gone up twice last month and are ruling at Rs 270 per bag for Grade A cement. Prices in Hyderabad have increased to Rs 250-255 per bag; the reason cited is increase in the cost of raw materials such as coal and freight. Prices of ordinary Portland cement (OPC) shot up from Rs 190 for a 50 kg bag,
45 days ago, to Rs 255 per bag. And prices in Jammu & Kashmir shot up from Rs 190 to over Rs 300 per bag
in the past three months.” Kumar affirms that there is a large difference in cost in different regions as each material is specifically region-based. “For example, river sand, which is about Rs 30 to 35 per cu ft in Chennai is Rs 130-150 per cu ft in Kerala. This variation in cost is owing to excessive sand mining and transportation. Also, the variation in construction techniques across the country is also an important factor for cost variation.”
The other side
Considering that much of the rising costs of construction are attributed to them, how do major players in the building materials industry respond?
“The major reason for rising steel prices is an unprecedented increase in steelmaking inputs like iron ore and coal,” asserts Vikram Amin, Executive Director (Sales & Marketing), Essar Steel. “The cost of iron ore and coal has nearly doubled in the past year. Hence, steel companies are forced to raise prices. Earlier, companies used to contract raw materials annually; this has now moved to a quarterly basis and brought volatility in prices.” To this Hemant M Nerurkar, Managing Director, Tata Steel, adds, “Driven by a cost push from coking coal, price rises were already in effect in January-March quarter this year. Further increases have typically not been announced in April by any major player.”
The implications for the steel industry in his view are clear. “Real-estate prices have moved up more sharply than steel prices since the depression of 2008,” says Nerurkar. “If at all, demand has been relatively better in the past four to five months. Unless extraneous factors are brought into play, the demand outlook for construction materials looks robust. Driven by the rally in real estate prices and the fundamentals of the construction industry being strong owing to growth in infrastructure, the demand outlook for construction projects also looks positive.”
Amin takes a different tack, however. “The volatility in input costs not only affects steel companies; it also affects steel users,” he points out. “This is not good for the economy. It affects infrastructure projects to no end as it is difficult to estimate steel prices at the time of bidding for these projects. Thus, in the long run, it will have a negative impact on projects and other products made out of steel. It is advisable to revert to the earlier method of pricing raw materials on an annual basis.”
As far as cement goes, Deepak Sogani, Executive Director, Strategy and Corporate Finance, Dalmia Bharat Enterprises Ltd, says, “Growth of consumption in FY11 at the rate of 5 per cent has been an aberration compared to previous long-term trends observed in the industry. This is lower than GDP growth and is on account of lower off-take from the infrastructure space, prolonged monsoons and comparatively unstable political environment in some of the traditionally high consumption states for cement in India. Consumption is expected to get back on track from FY12 onwards, riding on increased infrastructure spending by the government. On account of aggressive capacity build-up, pan-India effective utilisation of the industry has dropped to 77 per cent. Addition in cement capacity in FY12 and FY13 is expected to slow down considerably to sustain 9-10 per cent growth over a longer period of time.”
The implications of this trend are apparent. “On account of weak industry demands in FY11, the new capacities added could not be stabilised with industry utilisation levels,' explains Sogani. “Most players will now look to stabilise capacities added in the past few years before going ahead with the next phase of expansion plans. Delays in capex plans are very likely, especially by new entrants. After the industry's unsatisfactory performance in FY11, most smaller and marginal players will now have to reconsider and revise expansion plans. With slow capacity additions, industry utilisation is expected to improve, leading to sustained average pan-India prices."
A few good men
Now, for human capital. As Mantri pointed out earlier, welfare schemes like the Mahatma Gandhi NREGA (National Rural Employment Guarantee Act) have stemmed the migration of labour from rural to urban areas. While this has benefited scores of rural workers, it has had a definite impact on urban contractors - their employee pool is running dry - with an inevitable consequence on construction costs.
According to Vinayak, the higher NREGA wages could have a definite impact on the market for unskilled construction workers, who are now typically paid about Rs 100 per day, often at locations outside their villages and even in towns. “They may find local employment opportunities afforded by NREGA at similar or higher wages,” he points out. “There could be a consequent upward pressure on construction wages.”
Asking out loud whether NREGA can be the answer to the country's skill-starved construction industry, Kumar answers his own question: “Yes, and no!” He explains further. “NREGA is among the largest social welfare schemes implemented anywhere in the world and provides for at least 100 days of wage employment to at least one adult member of a rural household who is ready to do unskilled manual work. But though it has provided employment, it has also pushed farm labour shortage and rising farming costs. High labour costs have a double impact: making agriculture unviable and driving up the cost of food. At another level, the country's infrastructure sector is booming but the construction industry is in dire need of a skilled workforce. The paucity not only delays projects but affects the quality of workmanship. There is hardly a channel of supply of skilled and certified masons, bar-benders, carpenters, etc, on the scale required, so that a person serving as unskilled labour till the other day at one site may declare himself a mason at another site, the next day. Hence, the scheme has a dual impact.”
“It is true that NREGA has been a big boon to many workers,” concedes Neotia. “They are able to find productive employment close to their homes. Hence, in cities such as Kolkata where there was a lot of migrant labour, we have been facing difficulty in finding people to do the construction work. This has also pushed up the wages of workers resulting in higher costs of construction. I believe a lot of other workers, such as those engaged in farm activity, who found it unproductive to come to construction sites may now consider doing so in view of the increased wages being paid at construction sites. Also, I think there will be a gradual shift to mechanisation to reduce dependence on large amounts of labour.” Mantri echoes this sentiment when he says, “NREGA has resulted in a steep fall in the availability of labour for construction and this has resulted in delays and rising costs. There is a strong need for more technology that requires less labour.”
For his part, Misra says, “As a majority of our projects are located in rural parts of the country, we are yet to see any adverse effects. However, for project sites located in urban and semi-urban areas, availability of bulk labour is becoming an issue. We have to pay more to hire skilled labour in these areas which may shrink the margins further for these projects.”
Sudden impact
It's evident that developers and contractors have no option but to come to terms with the rising costs of materials and men. But will these have an impact on the quality, delivery and number of projects being executed?
Misra's response is emphatic. “Rising input costs have led companies to use raw materials of a slightly lower, but passable, grade. Such material, commonly called de-rolled material, is being used by many market players to protect their margins in case of price escalation. But we have a stringent quality policy and we would not water down our quality standards,” he assures. “The rise in construction cost will also be a disincentive for utility providers considering expansion plans. Moreover, owing to price escalation, companies are forced to move to secondary markets to save costs. This leads to a beating on delivery of projects. The Planning Commission of India has already revisited its Eleventh Five Year Plan because of a rise in commodity prices. The number of projects on offer may dwindle. But for us, when it comes to delivery, there will not be any compromise.”
Neotia too is quick to assert that there will be no adverse impact on quality as long as the builder is reputed. But he concedes that delivery of projects may be hampered owing to non-availability of labourers. “It is true that for newer projects builders will have to rework their financials to see the viability,” he adds. “In some areas there is just a lot of built-up space without adequate buyers. Builders will be more cautious before launching projects. With rising costs, there is an increase in price in some markets. Wherever the prices have moved up, the bottom line should remain protected. However, in those markets that have remained stagnant, this increase in costs will certainly adversely impact the bottomline.”
And what of the burden on the consumer? “The customer's pricing is basically based on demand and supply of the product,” he replies. “The cost as an input is certainly important but it is not the sole or prime determinant of pricing. Land price is a very important part of the price calculation for urban projects, particularly in central areas. There have been occasions when costs have moved up and prices have remained stagnant, sometimes even reduced. At other times, prices of flats have moved up without any significant increase in costs. So, in a sense, they are not very directly proportional.”
In Vinayak's view, however, any increase in the cost of the project ultimately reaches the consumer. “The government should evolve a policy to have an effective control on prices to check inflation.” While warning that builders of lesser repute may be tempted to compromise on quality, he says rising costs can also hamper project deadlines owing to deficit of fund and low margins. However, he feels the number of projects will not be impacted by rising construction costs as the demand in the realty market is end-user driven. “Because of increase in costs, the majority of companies are very careful at the design stage and try for economical design with a lot of value engineering to bring down costs,” he shares. “CREDAI Karnataka is taking a lead to make the customer also bear the escalated cost if it is beyond control or there is an abnormal jump in the rate of the material.”
As for Kumar, he firmly believes that there will be a direct impact on the quality, delivery and number of projects coming up each year as construction cost is the key factor deciding them. “The increased cost of construction has to be seen in the context of economic growth of the country and affordability for buyers,” he argues. “The increased cost of the materials will lead to a decline in the construction of more projects and increase in the cost of an individual home. The aspiration of owning a house for the middle income group will henceforth become a dream. This will impact both real estate and the infrastructure development of the country, thus bringing down our GDP. The government has to support these industries by controlling the prices of construction materials.”
Budget bulletin
Talking of the government, the Budget too has a decisive impact on the construction and infrastructure sectors. So what did this year's offering have in store, especially as far as costs are concerned?
“The Union Budget 2011-12 continued to lay stress on infrastructure development, as the allocation for the sector has been increased by 23 per cent year-on-year to Rs 2,140 billion, which is about 50 per cent of planned expenditure,” elaborates Misra. “The FM has been silent on the specific demand by a few domestic construction manufacturers to increase import duty on foreign equipment, which denies them a level playing field. However, excise duty exemption for domestic suppliers producing capital goods needed for expansion of existing mega or ultra mega power projects has been granted. A mandatory imposition of 1 per cent excise duty on coal has come into effect triggering a further spike in cement prices. Immediately after this announcement, in various parts of our country, cement manufacturers increased prices by around Rs 30 per bag. Overall, construction expenditure is likely to double over the next five years to Rs16,800 billion as against Rs8,895 billion in the past five years. Full exemption from basic customs duty for specific machinery to be used in the construction of national highways is a welcome measure. Foreign institutional investment (FII) has been increased by $ 20 billion for investment in corporate infrastructure bonds. Further, tax free bonds amounting to Rs 300 billion can be issued in roads, ports, railways and housing sectors. All these proposals are expected to address the funding needs of the infrastructure sector and could lead to faster project implementation.”
Meanwhile, Kumar informs us, “Towards the construction industry, the government has introduced a reduction on the basic customs duty on pet coke and gypsum by 2.5 per cent to give relief to the cement industry. Also, excise has been replaced with ad valorem duty on cement. However, given that most other construction raw materials have not been touched by the Budget, these measures are expected to have a negligible impact on the pricing of cement and overall construction costs. It would be a great relief if the service tax levied upon construction would be abolished or reduced so ‘affordable housing' would really be affordable and not just in name.”
Neotia pulls no punches when he delivers his opinion. “There was not much joy in Budget 2011 as far as the construction industry is concerned,” he says succinctly. “I can also say it was not a bad Budget in an overall sense. Hence, there is not much reason to be disappointed either.
Players in the building materials sector have their own concerns. Is the fact that Budget 2011 didn't grant infrastructure status to the steel industry one of them? “Investment in the infrastructure industry will definitely boost steel demand in the country and most segments catering to infrastructure growth in the country will need steel in large quantities,” responds Nerurkar. “By not categorising steel as an infrastructure industry, it may not affect any fund flow to the industry as investors might still look at steel as an attractive option. However, the cost of funds could have potentially reduced owing to tax sops to infrastructure bonds.”
Meanwhile, Amin adds, “The government's focus on infrastructure spending is a welcome move as it will trigger steel demand. But it is more important to address the issues of the steel industry so more capacity gets created. Current capacity is evenly balanced in terms of demand and supply. If we do not create capacity, India will have to depend on imported steel to meet its infrastructure growth while exporting cheaper iron ore.”
He also addresses another issue: the industry's demand for a reduction in the import duty of coal, besides removal of customs duty on non-coking coal to counter the price rise. “This is a step in the right direction as India does not produce coal required for the steel industry. This will help reduce the cost of imported coal marginally.” To this Nerurkar adds, “While removal of customs duty on non-coking coal will reduce the cost of sponge iron and power, and consequently cost of steel made through induction furnaces and EAF, reduction in import duty on coking coal will ease the cost pressure on domestic steel manufacturers producing hot metal through the blast furnace route.”
Future watch
So, all considered, what is the outlook for the industry looking ahead, especially for the next year?
“The market size of the global construction industry is $3.4 trillion and India accounts for about 2 per cent of total market size, ranking 12th in the world,” says Misra. “Construction spending is expected to increase to $370 billion by the end of 2013. This represents a CAGR of 13.3 per cent. As per the Eleventh Plan, it is proposed to add 78,500 mw of power, modernise four metro and 35 non-metro airports, add about 8,000 km of new rail, modernise 22 stations and add four-lane roads of over 20,000 km. The government is trying to achieve these targets through public-sector companies as well as PPP. The total projected investment by the Planning Commission of India has been set at $1,000 billion in the Twelfth Plan [2013-17]. Quarter 1 of the current financial year will open new opportunities and challenges. The government has made a bold attempt to provide impetus to the infrastructure sector by rolling out several initiatives such as additional allocation to the infrastructure sector for FY 2011-12, clearly suggesting the significance of the sector to the Indian economy.”
Getting down to specifics, Neotia says, “Good projects done by developers with good track record will continue to find buyers. Margins will be a bit under the squeeze but good projects will be viable whereas projects that have been poorly conceptualised or where the builder has no track record will be under financing pressure.”
Speaking of manpower trends, Vinayak emphasises that job opportunities will be excellent in the construction industry, “especially for workers with training and experience in construction occupations, owing largely to the numerous openings arising each year as experienced workers leave their jobs. The number of wage and salary jobs in the construction industry is expected to grow about 15 per cent through the year 2012, compared to the 18 per cent projected for all industries combined. Employment growth in the various segments of the construction industry will vary depending on the demand for various types of construction. Though the demand for residential construction, care institutions and schools is expected to continue to grow, remodelling, which tends to be more labour-intensive than new construction, will be the fastest growing sector of the housing industry.”
Kumar points out that along with the rising cost of materials this past year, there has also been a tremendous increase in the cost of land, thus reducing the percentage of acquisition of land for a project. “This will affect the total growth of the construction industry,” he warns. “The same will be continued in the following year or may even be higher unless there is an intervention from the government to control the cost.”
Nerurkar is firm in his belief that steel prices will be sustained keeping in mind cost increases on the raw material front and demand pull. “The last quarter of FY2011-12 may, however, witness a further surge in prices given the trend of the previous two years,” he predicts, adding, “Globally, Tata Steel is well placed to capture the demand growth in Asian countries and meet the requirement of quality steels in developed nations. It is not rising steel prices but demand drivers that affect our operations globally. However, we have to keep a close watch on the price and cost gap to maintain a healthy bottom line.” Amin adds, “Steel prices will entirely depend on the behaviour of raw material prices. They continue to rule firm and hence there is no reason why steel prices should soften.”
Thus, considering that costs will be stretched to their limits and there will be aninevitable pressure on margins, profitability will undoubtedly be a challenge this year. Nevertheless, Mantri is wont to strike a note of optimism. “2011 will witness more wealth being created across sectors and industries that will have a positive impact of the demand for residential and commercial real estate in the country,” he says. “Though rising construction costs will eat into profit margins for developers, we are positive for a year of growth for the industry.”
You can almost hear the chorus in response: ‘Amen'.
Quick Bytes
• Increase in the cost of raw materials by 45-50 per cent has resulted in increase in costs of building materials.
• Recent government restrictions in sand scooping and mining has escalated construction cost by Rs 35 per sq ft.
• Price escalation is forcing many companies to move to secondary markets.
• Construction expenditure is likely to double over the next five years to Rs 16,800 billion.
- Construction
- Update
- Portal
- Magazine
- CW-India
- May
- 2011
- India
- cost of construction
- Cement
- Steel
- prices
- freight
- transportation costs
- Inflation
- BK Vinayak
- Omaxe Infrastructure
- infrastructure
- deficit financing
- AK Misra
- Tata Projects Ltd
- Diesel prices
- Harshavardhan Neotia
- Ambuja Realty
- building materials
- Suresh Kumar
- Vijay Shanthi Builders Ltd
- raw materials
- Sushil Mantri
- Mantri Developers Pvt Ltd
- Hyderabad
- Austratlia
- employment
- sand scooping
- Mining
- Portland cement
- Jammu & Kashmir
- Chennai
- Kerala
- Vikram Amin
- Essar Steel
- Hemant M Nerurkar
- Tata Steel
- Real estate
- Deepak Sogani
- Dalmia Bharat Enterprises Ltd
- GDP
- NREGA
- Planning Commission
- Eleventh Five Year Plan
- CREDAI
- Union Budget 2011-12
- investment
- CAGR
Suddenly and silently, the price of construction has gone up dramatically in India. Construction World speaks to contractors, developers and building material majors to find out why and assess the implications for the industry and end-users. Fact: Construction is not just more prolific than ever before, it's also much more expensive. Figure: The cost of construction increased 8.4 per cent in 2010-11 as against just 4 per cent in 2009-10. Now that we've grabbed your attention, let's look at the whys of it all. The prices of cement and steel, the key raw materials for construction, have shot up sharply in recent months. Steel prices have risen by 10 per cent while retail numbers of cement have shot up 34 per cent since the beginning of 2011; these have been joined by other construction essentials, such as sand, aggregates and bricks. Even more significant, labour, freight and transportation costs have also spiked (see ‘Under Pressure', on page 90). An upward spiral The industry is feeling the pinch. “Inflation in India has seen a drastic rise over the past few years,” rues BK Vinayak, CEO, Omaxe Infrastructure. “There are many reasons; most important is the rising demand for goods and services owing to the fast growing economy, leading to unsystematic inflation resulting in high prices. Rise in global inflation levels owing to shortfall in supply to meet the demand of growing economies, growing money supply because of increase in government spending and the pressure to meet deficit financing, increasing in wages and tax rates, also lead to increase in overall prices for goods and services, among others.” Speaking specifically of construction, he points out how there is overall scarcity of skilled labour on account of tremendous infrastructure development in the country. “Further, rise in steel, cement, sand, aggregate and brick prices may jack up construction costs by 20 per cent,” he adds. “Steel accounts for 20-35 per cent of cost of construction, depending on the project, and cement accounts for 15-20 per cent of costs.” “Prices of construction materials such as steel and cement have increased significantly from the past few quarters, thus exerting great pressure on our project execution and procurement teams to keep our margins intact,” affirms AK Misra, Executive Director and Chief Operating Officer, Tata Projects Ltd. “The increases have primarily been because of high global demand for commodities, manufactured goods, higher production and transportation costs, partly owing to high fuel prices. Diesel prices have gone up significantly over the past few months, increasing overall project cost. Also, in the past decade, the cost of construction labour has gone up by about 25 per cent, higher than the general inflation rate. Increased labour costs are also a major contributor to increased utility construction costs because of rise in demand for specialised and skilled labour over current or projected supply.” Harshavardhan Neotia, Chairman, Ambuja Realty, couldn't agree more. “Generally there has been a cost increase across the board,” he says. “Prices of all basic raw materials such as steel, cement, sand, aggregates and bricks have gone up in the past year owing to a combination of increase in fuel costs and general increase in costs of inputs and labour. All this has a direct impact on the cost of construction.” “The construction industry is reeling under the increasing cost of building materials,” admits Suresh Kumar, Managing Director, Vijay Shanthi Builders Ltd. “This is truly the age of construction in India, with the industry recording a consistent growth of 35-40 per cent over the past two years. But this growth has come at a cost: the increasing cost of raw material, labour, transportation and acquisition of land. Several supply-side constraints are responsible for inflationary pressure on the building materials sector, where the rate of raw materials has increased by about 45-50 per cent in the past year. Some of these are industry-related, such as the shortage of raw materials, rising energy costs, low productivity of the industry, distribution and marketing problems, while others are exogenous in character. Most important among the exogenous factors is the economic and regulatory environment in which the building materials industry operates.” For his part, Sushil Mantri, Chairman and Managing Director, Mantri Developers Pvt Ltd, offers a cause-and-effect analysis for rising costs across several verticals. As for steel, while pointing out the increase in demand arising out of additional requirement in public works, he draws our attention to the increase of coking coal prices following the floods in Australia that put many mines out of operation as well as the volatility in raw material prices and power cut and local disturbances in Hyderabad. The result: “Escalation in construction costs by Rs 40 per sq ft and a slowdown in procurement.” Moving on to cement, he attributed the price rise to cartels formed by cement manufacturers to create artificial shortage through underproduction and asserted that it has led to climbing construction costs by Rs 130 per sq ft as well as a slowdown in construction activity owing to non-availability. Mantri blames the recent government restrictions in sand scooping and mining for sand prices doubling, which has escalated construction cost by Rs 35 per sq ft and once again led to slowdown. And a hike in petro-product prices has led to a rise in freight and transport prices, further escalating construction costs. As for labour, he says, “Inflationary pressures leading to an abnormal price rise in food and other basic living costs have pushed the price of labour upward. Additionally, the depletion of the migratory workforce owing to improved locally generated employment opportunity from government welfare schemes has led to scarcity of labour and increased costs.” This, according to Mantri, has led to escalation in construction cost by at least Rs 75 per sq ft and slowdown of work because of labour shortage. Here, and there Making confusion worse confounded – at least in terms of working out strategies to deal with increased costs – is the fact that building material costs vary from region to region. “While steel prices do not vary much over a period of time as well as over a region, as prices are controlled by only a few manufacturers, cement prices vary a lot over regions and over time,” says Misra. “Cement manufacturers are present in almost every state, so they try to drive their own prices. Hence, state governments need to take stock of a situation where cement manufacturers try to form a cartel, which would make a price check very difficult. Moreover, states that have production capability enjoy slightly lower prices because of the cost of logistics.” To this Vinayak adds, “The cost rise across the country may not be uniform owing to geographical reasons and availability of resou-rces. For example, prices for cement in Mumbai have gone up twice last month and are ruling at Rs 270 per bag for Grade A cement. Prices in Hyderabad have increased to Rs 250-255 per bag; the reason cited is increase in the cost of raw materials such as coal and freight. Prices of ordinary Portland cement (OPC) shot up from Rs 190 for a 50 kg bag, 45 days ago, to Rs 255 per bag. And prices in Jammu & Kashmir shot up from Rs 190 to over Rs 300 per bag in the past three months.” Kumar affirms that there is a large difference in cost in different regions as each material is specifically region-based. “For example, river sand, which is about Rs 30 to 35 per cu ft in Chennai is Rs 130-150 per cu ft in Kerala. This variation in cost is owing to excessive sand mining and transportation. Also, the variation in construction techniques across the country is also an important factor for cost variation.” The other side Considering that much of the rising costs of construction are attributed to them, how do major players in the building materials industry respond? “The major reason for rising steel prices is an unprecedented increase in steelmaking inputs like iron ore and coal,” asserts Vikram Amin, Executive Director (Sales & Marketing), Essar Steel. “The cost of iron ore and coal has nearly doubled in the past year. Hence, steel companies are forced to raise prices. Earlier, companies used to contract raw materials annually; this has now moved to a quarterly basis and brought volatility in prices.” To this Hemant M Nerurkar, Managing Director, Tata Steel, adds, “Driven by a cost push from coking coal, price rises were already in effect in January-March quarter this year. Further increases have typically not been announced in April by any major player.” The implications for the steel industry in his view are clear. “Real-estate prices have moved up more sharply than steel prices since the depression of 2008,” says Nerurkar. “If at all, demand has been relatively better in the past four to five months. Unless extraneous factors are brought into play, the demand outlook for construction materials looks robust. Driven by the rally in real estate prices and the fundamentals of the construction industry being strong owing to growth in infrastructure, the demand outlook for construction projects also looks positive.” Amin takes a different tack, however. “The volatility in input costs not only affects steel companies; it also affects steel users,” he points out. “This is not good for the economy. It affects infrastructure projects to no end as it is difficult to estimate steel prices at the time of bidding for these projects. Thus, in the long run, it will have a negative impact on projects and other products made out of steel. It is advisable to revert to the earlier method of pricing raw materials on an annual basis.” As far as cement goes, Deepak Sogani, Executive Director, Strategy and Corporate Finance, Dalmia Bharat Enterprises Ltd, says, “Growth of consumption in FY11 at the rate of 5 per cent has been an aberration compared to previous long-term trends observed in the industry. This is lower than GDP growth and is on account of lower off-take from the infrastructure space, prolonged monsoons and comparatively unstable political environment in some of the traditionally high consumption states for cement in India. Consumption is expected to get back on track from FY12 onwards, riding on increased infrastructure spending by the government. On account of aggressive capacity build-up, pan-India effective utilisation of the industry has dropped to 77 per cent. Addition in cement capacity in FY12 and FY13 is expected to slow down considerably to sustain 9-10 per cent growth over a longer period of time.” The implications of this trend are apparent. “On account of weak industry demands in FY11, the new capacities added could not be stabilised with industry utilisation levels,' explains Sogani. “Most players will now look to stabilise capacities added in the past few years before going ahead with the next phase of expansion plans. Delays in capex plans are very likely, especially by new entrants. After the industry's unsatisfactory performance in FY11, most smaller and marginal players will now have to reconsider and revise expansion plans. With slow capacity additions, industry utilisation is expected to improve, leading to sustained average pan-India prices. A few good men Now, for human capital. As Mantri pointed out earlier, welfare schemes like the Mahatma Gandhi NREGA (National Rural Employment Guarantee Act) have stemmed the migration of labour from rural to urban areas. While this has benefited scores of rural workers, it has had a definite impact on urban contractors - their employee pool is running dry - with an inevitable consequence on construction costs. According to Vinayak, the higher NREGA wages could have a definite impact on the market for unskilled construction workers, who are now typically paid about Rs 100 per day, often at locations outside their villages and even in towns. “They may find local employment opportunities afforded by NREGA at similar or higher wages,” he points out. “There could be a consequent upward pressure on construction wages.” Asking out loud whether NREGA can be the answer to the country's skill-starved construction industry, Kumar answers his own question: “Yes, and no!” He explains further. “NREGA is among the largest social welfare schemes implemented anywhere in the world and provides for at least 100 days of wage employment to at least one adult member of a rural household who is ready to do unskilled manual work. But though it has provided employment, it has also pushed farm labour shortage and rising farming costs. High labour costs have a double impact: making agriculture unviable and driving up the cost of food. At another level, the country's infrastructure sector is booming but the construction industry is in dire need of a skilled workforce. The paucity not only delays projects but affects the quality of workmanship. There is hardly a channel of supply of skilled and certified masons, bar-benders, carpenters, etc, on the scale required, so that a person serving as unskilled labour till the other day at one site may declare himself a mason at another site, the next day. Hence, the scheme has a dual impact.” “It is true that NREGA has been a big boon to many workers,” concedes Neotia. “They are able to find productive employment close to their homes. Hence, in cities such as Kolkata where there was a lot of migrant labour, we have been facing difficulty in finding people to do the construction work. This has also pushed up the wages of workers resulting in higher costs of construction. I believe a lot of other workers, such as those engaged in farm activity, who found it unproductive to come to construction sites may now consider doing so in view of the increased wages being paid at construction sites. Also, I think there will be a gradual shift to mechanisation to reduce dependence on large amounts of labour.” Mantri echoes this sentiment when he says, “NREGA has resulted in a steep fall in the availability of labour for construction and this has resulted in delays and rising costs. There is a strong need for more technology that requires less labour.” For his part, Misra says, “As a majority of our projects are located in rural parts of the country, we are yet to see any adverse effects. However, for project sites located in urban and semi-urban areas, availability of bulk labour is becoming an issue. We have to pay more to hire skilled labour in these areas which may shrink the margins further for these projects.” Sudden impact It's evident that developers and contractors have no option but to come to terms with the rising costs of materials and men. But will these have an impact on the quality, delivery and number of projects being executed? Misra's response is emphatic. “Rising input costs have led companies to use raw materials of a slightly lower, but passable, grade. Such material, commonly called de-rolled material, is being used by many market players to protect their margins in case of price escalation. But we have a stringent quality policy and we would not water down our quality standards,” he assures. “The rise in construction cost will also be a disincentive for utility providers considering expansion plans. Moreover, owing to price escalation, companies are forced to move to secondary markets to save costs. This leads to a beating on delivery of projects. The Planning Commission of India has already revisited its Eleventh Five Year Plan because of a rise in commodity prices. The number of projects on offer may dwindle. But for us, when it comes to delivery, there will not be any compromise.” Neotia too is quick to assert that there will be no adverse impact on quality as long as the builder is reputed. But he concedes that delivery of projects may be hampered owing to non-availability of labourers. “It is true that for newer projects builders will have to rework their financials to see the viability,” he adds. “In some areas there is just a lot of built-up space without adequate buyers. Builders will be more cautious before launching projects. With rising costs, there is an increase in price in some markets. Wherever the prices have moved up, the bottom line should remain protected. However, in those markets that have remained stagnant, this increase in costs will certainly adversely impact the bottomline.” And what of the burden on the consumer? “The customer's pricing is basically based on demand and supply of the product,” he replies. “The cost as an input is certainly important but it is not the sole or prime determinant of pricing. Land price is a very important part of the price calculation for urban projects, particularly in central areas. There have been occasions when costs have moved up and prices have remained stagnant, sometimes even reduced. At other times, prices of flats have moved up without any significant increase in costs. So, in a sense, they are not very directly proportional.” In Vinayak's view, however, any increase in the cost of the project ultimately reaches the consumer. “The government should evolve a policy to have an effective control on prices to check inflation.” While warning that builders of lesser repute may be tempted to compromise on quality, he says rising costs can also hamper project deadlines owing to deficit of fund and low margins. However, he feels the number of projects will not be impacted by rising construction costs as the demand in the realty market is end-user driven. “Because of increase in costs, the majority of companies are very careful at the design stage and try for economical design with a lot of value engineering to bring down costs,” he shares. “CREDAI Karnataka is taking a lead to make the customer also bear the escalated cost if it is beyond control or there is an abnormal jump in the rate of the material.” As for Kumar, he firmly believes that there will be a direct impact on the quality, delivery and number of projects coming up each year as construction cost is the key factor deciding them. “The increased cost of construction has to be seen in the context of economic growth of the country and affordability for buyers,” he argues. “The increased cost of the materials will lead to a decline in the construction of more projects and increase in the cost of an individual home. The aspiration of owning a house for the middle income group will henceforth become a dream. This will impact both real estate and the infrastructure development of the country, thus bringing down our GDP. The government has to support these industries by controlling the prices of construction materials.” Budget bulletin Talking of the government, the Budget too has a decisive impact on the construction and infrastructure sectors. So what did this year's offering have in store, especially as far as costs are concerned? “The Union Budget 2011-12 continued to lay stress on infrastructure development, as the allocation for the sector has been increased by 23 per cent year-on-year to Rs 2,140 billion, which is about 50 per cent of planned expenditure,” elaborates Misra. “The FM has been silent on the specific demand by a few domestic construction manufacturers to increase import duty on foreign equipment, which denies them a level playing field. However, excise duty exemption for domestic suppliers producing capital goods needed for expansion of existing mega or ultra mega power projects has been granted. A mandatory imposition of 1 per cent excise duty on coal has come into effect triggering a further spike in cement prices. Immediately after this announcement, in various parts of our country, cement manufacturers increased prices by around Rs 30 per bag. Overall, construction expenditure is likely to double over the next five years to Rs16,800 billion as against Rs8,895 billion in the past five years. Full exemption from basic customs duty for specific machinery to be used in the construction of national highways is a welcome measure. Foreign institutional investment (FII) has been increased by $ 20 billion for investment in corporate infrastructure bonds. Further, tax free bonds amounting to Rs 300 billion can be issued in roads, ports, railways and housing sectors. All these proposals are expected to address the funding needs of the infrastructure sector and could lead to faster project implementation.” Meanwhile, Kumar informs us, “Towards the construction industry, the government has introduced a reduction on the basic customs duty on pet coke and gypsum by 2.5 per cent to give relief to the cement industry. Also, excise has been replaced with ad valorem duty on cement. However, given that most other construction raw materials have not been touched by the Budget, these measures are expected to have a negligible impact on the pricing of cement and overall construction costs. It would be a great relief if the service tax levied upon construction would be abolished or reduced so ‘affordable housing' would really be affordable and not just in name.” Neotia pulls no punches when he delivers his opinion. “There was not much joy in Budget 2011 as far as the construction industry is concerned,” he says succinctly. “I can also say it was not a bad Budget in an overall sense. Hence, there is not much reason to be disappointed either. Players in the building materials sector have their own concerns. Is the fact that Budget 2011 didn't grant infrastructure status to the steel industry one of them? “Investment in the infrastructure industry will definitely boost steel demand in the country and most segments catering to infrastructure growth in the country will need steel in large quantities,” responds Nerurkar. “By not categorising steel as an infrastructure industry, it may not affect any fund flow to the industry as investors might still look at steel as an attractive option. However, the cost of funds could have potentially reduced owing to tax sops to infrastructure bonds.” Meanwhile, Amin adds, “The government's focus on infrastructure spending is a welcome move as it will trigger steel demand. But it is more important to address the issues of the steel industry so more capacity gets created. Current capacity is evenly balanced in terms of demand and supply. If we do not create capacity, India will have to depend on imported steel to meet its infrastructure growth while exporting cheaper iron ore.” He also addresses another issue: the industry's demand for a reduction in the import duty of coal, besides removal of customs duty on non-coking coal to counter the price rise. “This is a step in the right direction as India does not produce coal required for the steel industry. This will help reduce the cost of imported coal marginally.” To this Nerurkar adds, “While removal of customs duty on non-coking coal will reduce the cost of sponge iron and power, and consequently cost of steel made through induction furnaces and EAF, reduction in import duty on coking coal will ease the cost pressure on domestic steel manufacturers producing hot metal through the blast furnace route.” Future watch So, all considered, what is the outlook for the industry looking ahead, especially for the next year? “The market size of the global construction industry is $3.4 trillion and India accounts for about 2 per cent of total market size, ranking 12th in the world,” says Misra. “Construction spending is expected to increase to $370 billion by the end of 2013. This represents a CAGR of 13.3 per cent. As per the Eleventh Plan, it is proposed to add 78,500 mw of power, modernise four metro and 35 non-metro airports, add about 8,000 km of new rail, modernise 22 stations and add four-lane roads of over 20,000 km. The government is trying to achieve these targets through public-sector companies as well as PPP. The total projected investment by the Planning Commission of India has been set at $1,000 billion in the Twelfth Plan [2013-17]. Quarter 1 of the current financial year will open new opportunities and challenges. The government has made a bold attempt to provide impetus to the infrastructure sector by rolling out several initiatives such as additional allocation to the infrastructure sector for FY 2011-12, clearly suggesting the significance of the sector to the Indian economy.” Getting down to specifics, Neotia says, “Good projects done by developers with good track record will continue to find buyers. Margins will be a bit under the squeeze but good projects will be viable whereas projects that have been poorly conceptualised or where the builder has no track record will be under financing pressure.” Speaking of manpower trends, Vinayak emphasises that job opportunities will be excellent in the construction industry, “especially for workers with training and experience in construction occupations, owing largely to the numerous openings arising each year as experienced workers leave their jobs. The number of wage and salary jobs in the construction industry is expected to grow about 15 per cent through the year 2012, compared to the 18 per cent projected for all industries combined. Employment growth in the various segments of the construction industry will vary depending on the demand for various types of construction. Though the demand for residential construction, care institutions and schools is expected to continue to grow, remodelling, which tends to be more labour-intensive than new construction, will be the fastest growing sector of the housing industry.” Kumar points out that along with the rising cost of materials this past year, there has also been a tremendous increase in the cost of land, thus reducing the percentage of acquisition of land for a project. “This will affect the total growth of the construction industry,” he warns. “The same will be continued in the following year or may even be higher unless there is an intervention from the government to control the cost.” Nerurkar is firm in his belief that steel prices will be sustained keeping in mind cost increases on the raw material front and demand pull. “The last quarter of FY2011-12 may, however, witness a further surge in prices given the trend of the previous two years,” he predicts, adding, “Globally, Tata Steel is well placed to capture the demand growth in Asian countries and meet the requirement of quality steels in developed nations. It is not rising steel prices but demand drivers that affect our operations globally. However, we have to keep a close watch on the price and cost gap to maintain a healthy bottom line.” Amin adds, “Steel prices will entirely depend on the behaviour of raw material prices. They continue to rule firm and hence there is no reason why steel prices should soften.” Thus, considering that costs will be stretched to their limits and there will be aninevitable pressure on margins, profitability will undoubtedly be a challenge this year. Nevertheless, Mantri is wont to strike a note of optimism. “2011 will witness more wealth being created across sectors and industries that will have a positive impact of the demand for residential and commercial real estate in the country,” he says. “Though rising construction costs will eat into profit margins for developers, we are positive for a year of growth for the industry.” You can almost hear the chorus in response: ‘Amen'. Quick Bytes • Increase in the cost of raw materials by 45-50 per cent has resulted in increase in costs of building materials.• Recent government restrictions in sand scooping and mining has escalated construction cost by Rs 35 per sq ft.• Price escalation is forcing many companies to move to secondary markets.• Construction expenditure is likely to double over the next five years to Rs 16,800 billion.
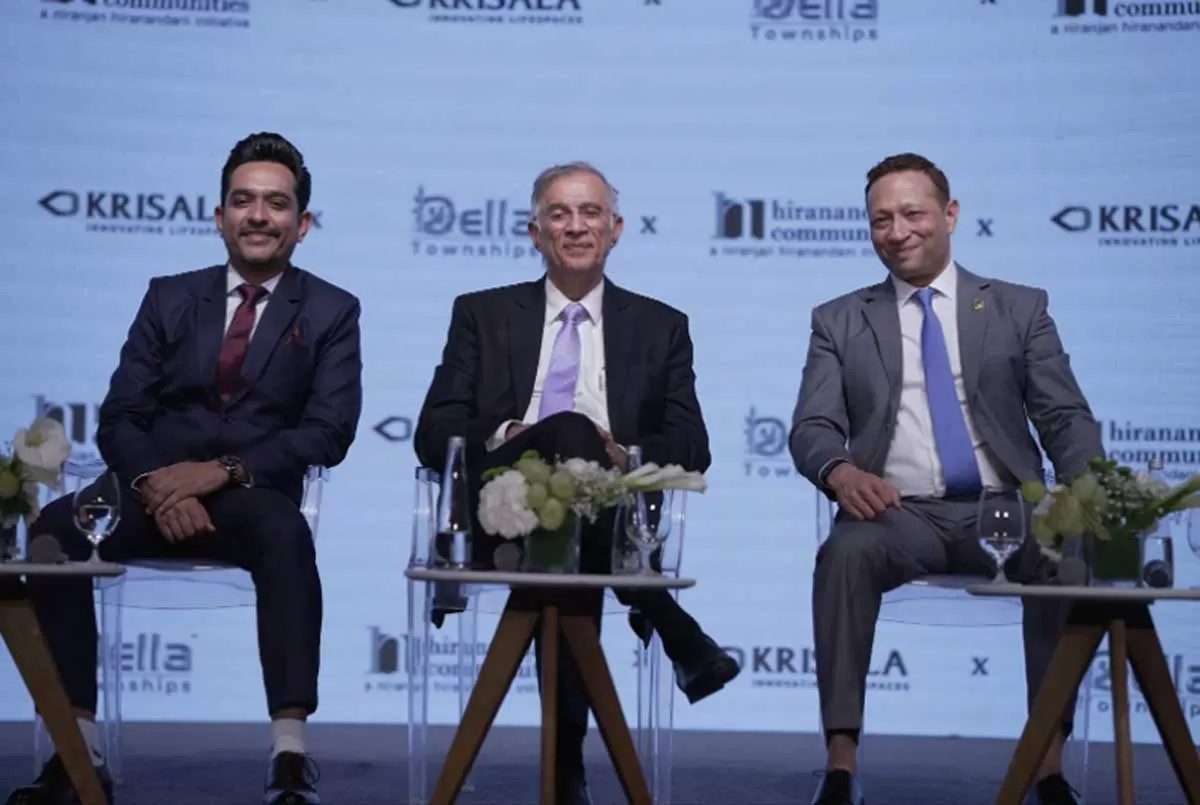
Della, Hiranandani & Krisala unveil Rs 11 billion themed township in Pune
In a first-of-its-kind initiative, Della Resorts & Adventure has partnered with Hiranandani Communities and Krisala Developers to develop a Rs 11 billion racecourse-themed township in North Hinjewadi, Pune. Based on Della’s proprietary CDDMO™ model, the hospitality-led, design-driven project aims to deliver up to 9 per cent returns—significantly higher than the typical 3 per cent in residential real estate.Spanning 40 acres within a 105-acre master plan, the mega township will feature an 8-acre racecourse and international polo club, 128 private villa plots, 112 resort residences, a ..
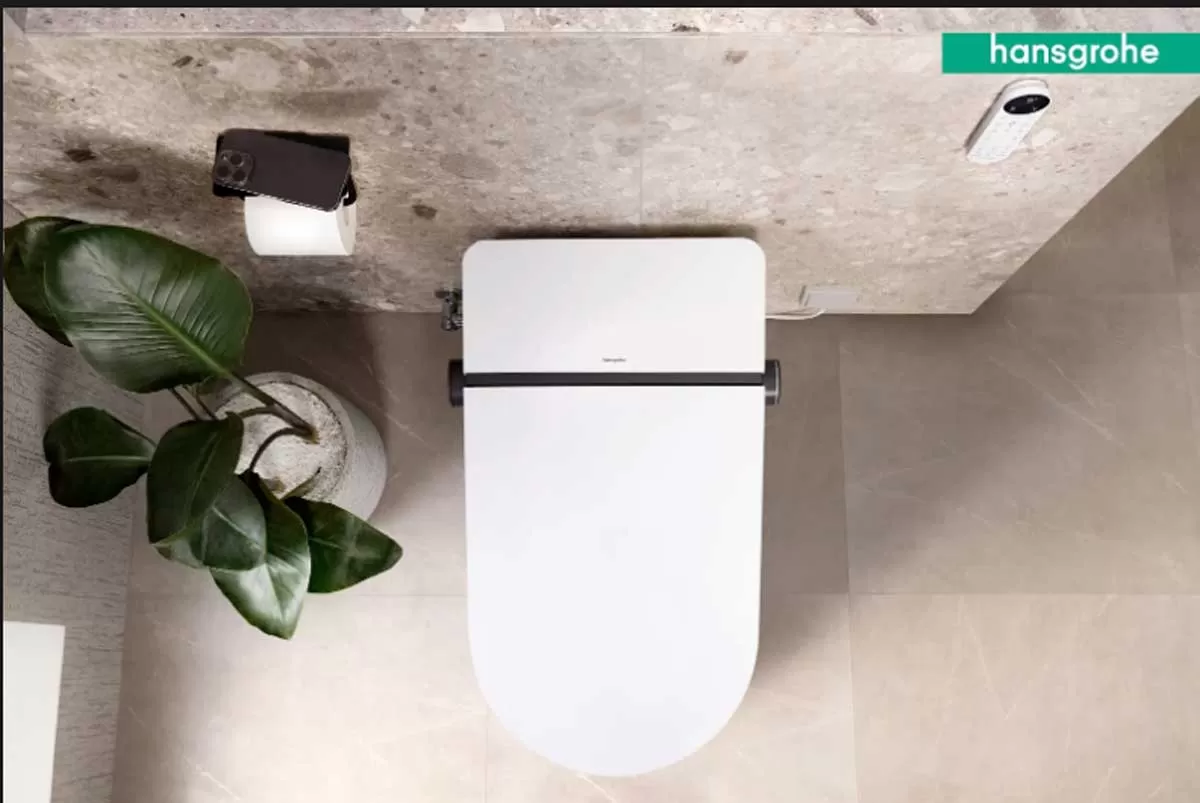
Hansgrohe unveils LavaPura Element S e-toilets in India
Hansgrohe India has launched its latest innovation, the LavaPura Element S e-toilet series, introducing a new standard in hygiene-focused, smart bathroom solutions tailored for Indian homes and high-end hospitality spaces.Blending German engineering with minimalist aesthetics, the LavaPura Element S combines intuitive features with advanced hygiene technology. The series is designed for easy installation and optimal performance under Indian conditions, reinforcing the brand’s focus on functional elegance and modern convenience.“With evolving consumer preferences, smart bathrooms are no lon..
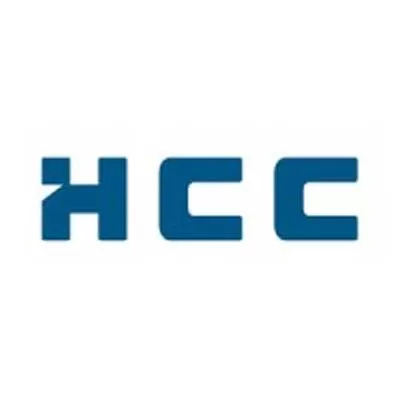
HCC Net Profit Stands at Rs 2.28 Billion for Q4 FY25
Hindustan Construction Company (HCC) reported a standalone net profit of Rs 2.28 billion in Q4 FY25, a sharp increase from Rs 388 million in Q4 FY24. Standalone revenue for the quarter stood at Rs 13.30 billion, compared to Rs 14.28 billion in Q4 FY24. For the full fiscal year, the company reported a standalone net profit of Rs 849 million, down from Rs 1.79 billion in FY24. Standalone revenue for FY25 was Rs 48.01 billion, compared to Rs 50.43 billion in the previous year.Consolidated revenue for Q4 FY25 stood at Rs 13.74 billion, and for FY25 at Rs 56.03 billion, down from Rs 17.73 billion i..
Latest Updates
Advertisement
Recommended for you
Advertisement
Subscribe to Our Newsletter
Get daily newsletters around different themes from Construction world.
Advertisement
Advertisement
Advertisement
subscribe to the newsletter
Don't miss out on valuable insights and opportunities
to connect with like minded professionals