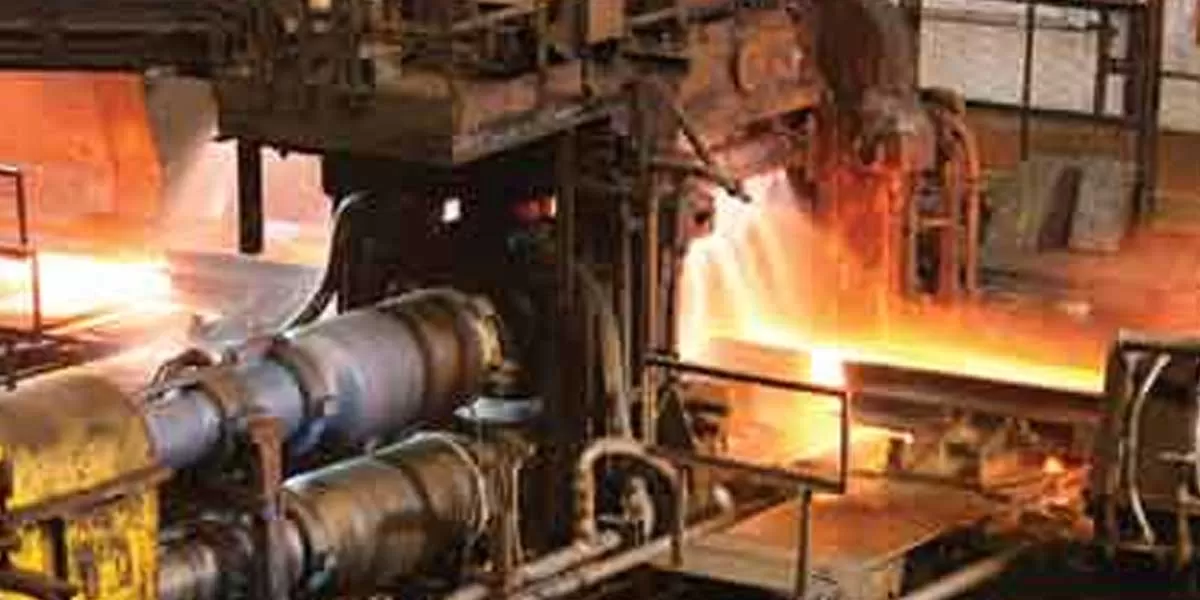
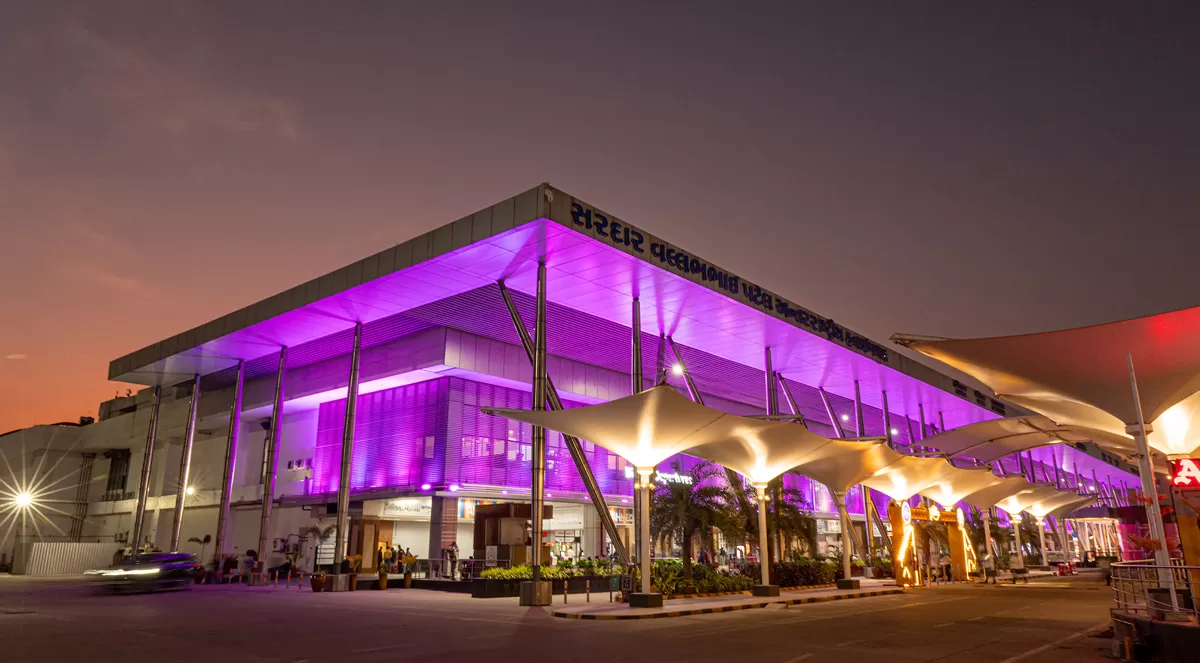
Gujarat AAI Airports Report Rs 818 Cr Loss Over 10 Years
Eight Airports Authority of India (AAI)-operated airports in Gujarat have collectively recorded losses of Rs 818 crore over the past decade, with Rajkot airport accounting for more than half the amount. The losses span from the fiscal year 2015–16 to 2024–25, as per a report from the Union Ministry of Civil Aviation.Rajkot airport posted the highest loss at Rs 418.67 crore, followed by Bhavnagar at Rs 122.08 crore. Porbandar, Bhuj, Diu, Kandla, Keshod, and Deesa also reported significant deficits. Deesa airport is currently non-operational, along with 21 other airports nationwide.Notably, ..
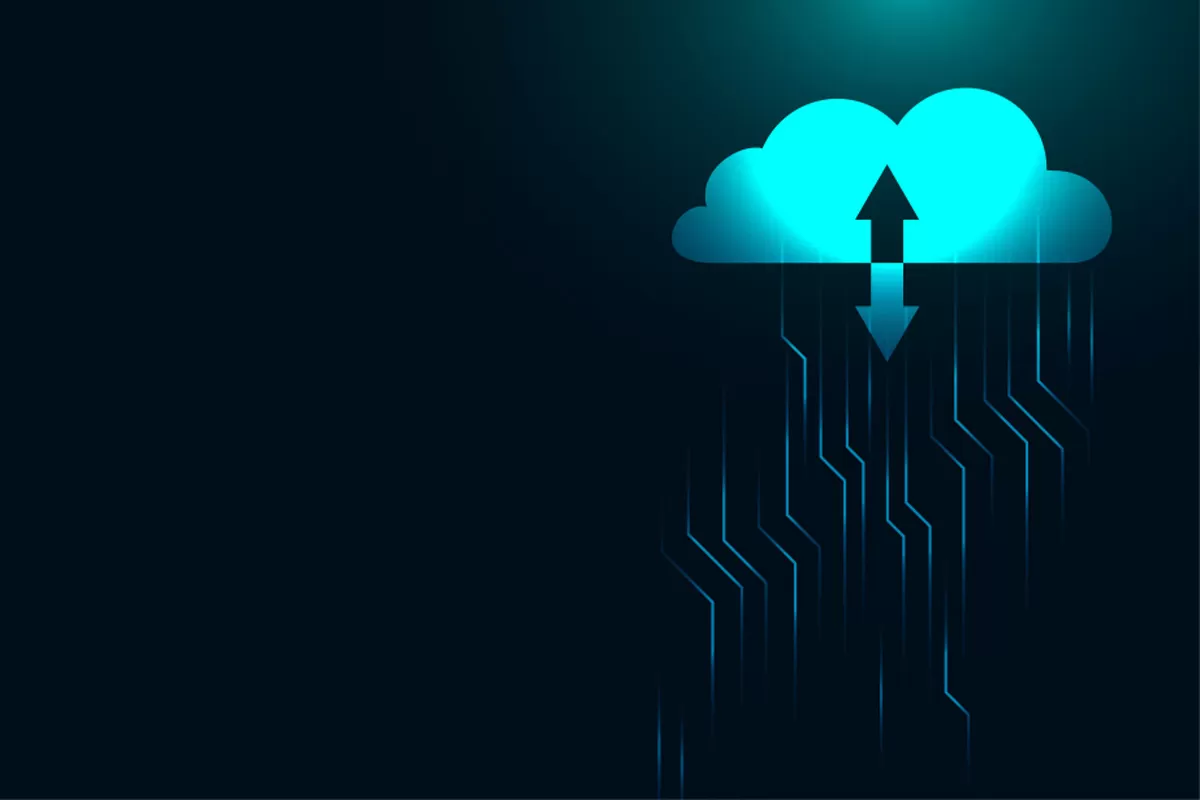
Autodesk Launches India-Based Cloud Data Storage for AECO Sector
Autodesk has expanded its regional offerings to include India, enabling businesses to store and manage project data locally. This strategic move supports the Government of India’s Viksit Bharat vision by empowering regulated sectors such as infrastructure, utilities, and government with secure, high-performance cloud collaboration capabilities. With this launch, AECO (architecture, engineering, construction, and operations) customers can now select India as their primary data storage location for Autodesk Docs, BIM Collaborate, and BIM Collaborate Pro. The offering ensures enterprise-gr..
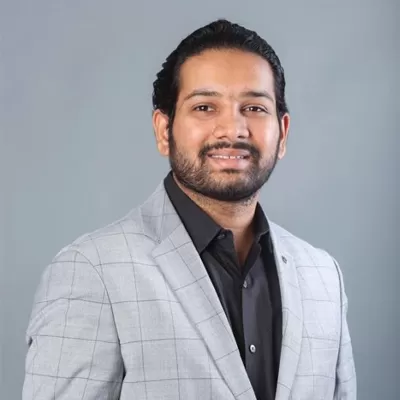
Enlight Metals Enters Cable Tray Business with Rs 50 Million Plan
Enlight Metals, a leading metal aggregator based in Pune, has announced its entry into the cable tray aggregation business. This strategic move supports its transition from a raw material supplier to a provider of value-added, project-ready steel solutions for industrial and infrastructure sectors across India. With strong sourcing expertise and established OEM relationships, Enlight Metals aims to simplify cable tray procurement for EPC contractors, renewable energy firms, and automation companies. The company will cater to high-demand states including Maharashtra, Gujarat, Karnataka, an..