- Home
- Infrastructure Transport
- ROADS & HIGHWAYS
- On the High Road
On the High Road
Newer technologies and methods are gaining acceptance by road contractors even as equipment vendors double up their efforts to serve the industry, discovers Charu Bahri.
The Indian market for road construction equipment has seen a meteoric rise in the past few years mainly owing to the Government's thrust on expanding the national highways and state and rural roads networks. Road construction equipment of every kind, from crushing and screening plants to asphalt plants, asphalt and concrete pavers, compactors and motor graders, is being increasingly sought by contractors executing road construction projects. MM Shahane, Executive Vice-President and COO, Engineering Products and Services Business Group, Voltas, which offers crushing and screening equipment and concrete pavers, estimates the total market for such equipment to have been worth Rs 3,000 crore last year. “At the rate investments are being made in the road sector, this will grow steadily at 10 to 15 per cent per annum,” he says.
Contractors also see the market for road construction equipment widening for quite some time to come. “India offers plenty of scope for BOT road projects and this is likely to continue for the next 20 years,” opines NG Thatte, Executive Director, PBA Infrastructure Ltd. “Public resistance to too much tolling builds slowly, but it is inevitable over time. People will slowly realise that roads are an amenity expected from a welfare state. For now, though, BOT is an excellent concept.”
Soil stabilisation
Soil is a key ingredient in the making of good roads. As SV Vaidya, President, Gayatri Projects Ltd, explains, “Utilising the best available soil helps avoid problems of compaction and future settlements that are associated with poor soil quality.” Further, Thatte observes, “Fortunately, India by and large has good soil even if rising land prices and royalties have seen its cost increase by about 50 times in the past 30 years. But black cotton soils and plastic soils must be avoided at all costs."
The analysis of soil characteristics helps identify suitable varieties to use for embankments and reinforced earth fills. Though some contractors tend to rely on the visible inspection of soil based on their experience, Thatte believes this should be avoided, “Nothing can replace scientific investigations conducted in a laboratory.”
Appropriate compactors used to stabilise soil also ensure better outcomes; it also helps if the product is backed by useful services. Volvo India offers a range of compactors especially designed for soil stabilisation. “As our equipment is backed by core expertise, we're also able to offer soil stabilisation technical consultancy through our Resource Centre for Asphalt and Soil Training Academy or RASTA initiative,” says AM Muralidharan, Managing Director, Volvo India. “That means we study the soil at the customers' site and suggest solutions to improve soil stabilisation for better outcomes. We also offer similar services for asphalt roads.”
Paving equipment
Pavers should ideally assist the exact implementation of road designs. For that, Muralidharan believes they need special screeds to ensure the slope and grade finish meet the design. “Our screeds have a tamping unit followed by a vibratory screed that gives good density and finish for asphalt layers,” he adds.
Vogele pavers are hailed globally for their performance. Ramesh Palagiri, CEO & Managing Director, Wirtgen India, attributes this to the patented TP2 high compaction technology that helps achieve compaction (up to 98 per cent) faster than comparable machines. “Overall, needing fewer roller passes delivers operational efficiencies and results in a better ride quality as the mix compacts better when it is hot,” he says.
With concrete roads being preferred for sectors with high traffic density, for their much longer life compared to asphalt roads; concrete pavers based on better technologies are also in focus. “Modern concrete pavers help improve the outcome of concrete roads as they include electronic controls and software offering better control in forming concrete,” elaborates Shahane. “Electronic controls mix cement and aggregates more accurately thereby producing more consistent concrete. This in turn extends the life of the road surface and reduces its need for maintenance. So, such features also improve the economics of concrete roads.”
Better efficiencies
Nowadays, road construction equipment runs on latest engines complying with new emission standards, thereby lowering fuel consumption and optimising energy. In this context, Shahane cites BS3 norms (equivalent of Euro III norms) as being the preferred standard.
As far as fuel efficiency is concerned, Muralidharan endorses a holistic approach to the subject as practised by Volvo. “Volvo meets environmental standards set by the Government of India,” he says. “We deliver fuel efficiency across all elements of our machines via our engines, systems, operator behaviour and future technologies, while increasing productivity for our customers. Hybrid technology is also under development as one part of this wider range of fuel-saving solutions. Buses and trucks are leading this technology within the Volvo group and other product groups will take advantage of the knowledge too.”
Efficiencies not only stem from making the best use of equipment but from getting the right asphalt mix and imparting training in operating the machine and in application engineering. Wirtgen India offers these services for its Vogele pavers. An application engineering team helps its clients achieve desired outcomes. “Contractors like L&T, HCC, KMC Constructions and Ashoka Buildcon have used our services,” shares Palagiri.
Under its RASTA initiative, Volvo India also educates end users about ways to optimise the usage of Volvo equipment and in the process of road building. “Such training ultimately helps the government, the owner of the road who invests in infrastructure, as well as consultants who design and supervise the process and contractors implementing the designs,” emphasises Muralidharan. “Knowhow is the key to meet international standards.”
Maintenance by recycling
One kilometre of a virgin one/two-lane road costs several crores of rupees. Multiplying this with the thousands of kilometres of already constructed and upcoming road length gives a fairly good idea of the huge investment that is being made to improve the country's road network. But making roads is not enough. Roads must also be maintained to get the most out of these newly created assets. If constructed well, in most instances, it's the top layer of roads (not lower depths) that wear out and must be refurbished to restore drive-ability.
The government can do a lot to prevent the mechanical failure of roads. Road surfaces are designed to be strong enough to withstand the density of vehicles plying on them and the cumulative weight of vehicles passing at any point in time. Over-laden trucks significantly burden roads for which reason they shouldn't be allowed. The Bihar government has shown definite will in disallowing overloaded trucks; indeed, a positive step.
In instances where the roughness index (measure of loss of ride comfort) of the road mandates resurfacing, it is cost-effective and faster to resurface the road using recycling technology. Top layer corrections conducted using recycling yield significant cost benefits. The cost of hot in place recycling is about 10 per cent less than conventional overlays at current market rates (see case study). Telcon Ecoroad Resurfaces Pvt Ltd (TERPL), a Telcon initiative, has been spearheading the goodness of recycling of bituminous road.
Road consultants also endorse recycling. Aseem Prabhakar, HOD (Highways), Intercontinental Consultants and Technocrats Pvt Ltd, says, “As consultants, we recommend the use of eco-friendly materials like recycled aggregates. We recommended used bituminous milled material of existing damaged pavement as one of the components (15 per cent) in granular base course (wet mix macadam) materials for the NH-2 (Agra-Sikohabad) project. We also recommended using dismantled material of the existing pavement in the pavement construction of the NH-43 (Raipur-Dhamtari) project.”
Contractors' take
Ideally, contractors should take up the mantle of responsible road engineering before being forced to do so. Some, however, are reluctant, as they are under the impression that recycling road surfaces isn't legally permissible. To contractors who desist from adopting recycling, believing it isn't legally permissible, HK Sehgal, COO, TERPL says, “The process finds mention and acceptance in the MoRT&H's publication of Specification of Roads & Bridge Works (Revision 4), also called Yellow/Orange Book, under Section 517.”
“Nothing stops a contractor from using a recycled material if he can demonstrate to the engineer its use according to the specifications laid down in the tender,” adds Prabhakar. “It is particularly relevant for Design Build Finance and Operate (DBFO) projects where there is flexibility in design and the concessionaire also has to maintain the road for the concession period of 10 to 20 years.”
Recognising the benefits of recycling last year, the National Highways Authority of India (NHAI) declared that it would encourage the use of recycling the existing bituminous material (reclaimed asphalt pavement or RAP) to upgrade an existing bituminous pavement. Such recycling has been made mandatory in all projects where the process will yield cost savings. Possibly as a result, contractors are now thinking in terms of recycling. “Although we have not utilised recycling technologies for any of our road projects so far, we may use them for the maintenance of our BOT roads during the O&M phase in future,” says Vaidya.
Contractors are also open to accept the benefits of recycling even if complacent to change their ways. “Recycling is certainly a better way of going about road resurfacing, especially in places where road construction materials need to be transported over great distances, say more than 20 to 25 km,” says Thatte. “Then, it yields significant economic advantages. But some old roads are seen to be very hungry for fresh bitumen that conventional methods appeal more. Contractors also tend to adopt the path of least resistance; changing techniques always calls for more effort.” That's why he believes that government intervention would help make the industry more responsive towards reusing available materials. “When the government made the use of fly ash compulsory, contractors were left with no option but to follow the mandatory specifications, and we've now realised the benefits,” he adds. “So far, contractors only recycle when it is compulsory, like we did in a small project because it was mandated by the project terms.”
At the end of the day, Thatte believes the better quality of road infrastructure being created today is an outcome of superior and more readily available machinery and higher expectations of the government and its people. Rising public demands for good quality also spur change for the better. Palagiri observes, “The durability and the ride quality of roads tends to depend on the intent of the owner – the NHAI, a local municipality, or PWD – to demand quality,” even as he emphasises that Indian contractors possess the necessary technology and know how. With the right ingredients in place, the road ahead should be far smoother than ever before.
Case Study: Road recycling in Delhi
By: Telcon Ecoroad Resurfaces Pvt Ltd (TERPL), a company that takes up recycling contracts on its own; performs recycling for BOT concessionaires, as subcontractor to NHAI's prime contractor; and sells AR2000 trains used for recycling.
Method adopted: Hot in place (hot-in-situ) recycling. This involves heating the existing road, scarifying it, mixing virgin mix as decided by pre-engineering investigations to upgrade (recycle) the existing mix to current MoRT&H standards, and relaying it for compaction all in real-time without taking any material away from the road site.
Length recycled: About 1.5 million sq m of bituminous pavement (around 1 million of which is in Delhi alone, mostly on major roads like the Ring Road, part of the NHDP).
Equipment used: AR2000 Super Recycler, an 80-m-long train of equipment (end-to-end). The train comprising pre-heaters 1 and 2, heater miller and heater mixer all heat the road or the milled (reclaimed asphalt pavement) or mixed (recycled asphalt pavement) material depending upon which part of the site the train is working on at a given point of time.
Speed of work: A good working speed is between one to two single lane km per shift of eight to 10 hours. In cities, the speed may be curtailed by traffic, encroachments on the roads and the straightness (or otherwise) of the road.
Technical specifications: The depth of milling and/or final compaction thickness is 50 mm though 60 mm; may also be achieved. As the existing road, milled road, milled asphalt mix, hot mix and freshly recycled asphalt mix are all heated, there is hot to hot bonding of the recycled mix with the heated road surface, leading to better durability of the road. Finish compaction is usually over by the time the material cools to 90° C. The road is delivered to the user as soon as it cools to 50° C.
Durability: Roads recycled by TERPL have lasted between three and five years without needing any further maintenance.
Benefits: The environmental benefits obviously include the preservation of energy and an increasingly expensive finite resource, bitumen, a derivative of oil. By weight, bitumen accounts for a minimum of 5 per cent of the hot mix that goes into making the top layer (wearing course) of a road. Recycling helps avoid burying the remaining old, weathered, brittle bitumen left after the service life of the wearing course under a fresh layer. At best, only about 2 per cent more fresh bitumen is needed to rejuvenate the old mix. Some say that a trillion rupees lie buried in city roads. Engineering benefits include the preservation and correction of road geometry, and not needing to raise elements of the roads' profile such as footpaths, signals, lamp posts, culverts, etc. Maintaining the height of the road is much safer for structures by its side. Recycling also increases roads' resistance to rutting, scuffing and ravelling. As the hot mix is maintained at an optimum temperature throughout the process, the resulting surface is more durable and assures superior ride quality.
Case Study: Waterproofing courses on bridge decks
Project: Surat-Dahisar (NH-8) Highway Project (BOT); the proposed mat was used on all bridges with approaches on high embankments
Contractor: IRB Ltd
Consultant: Intercontinental Consultants and Technocrats Pvt Ltd
Equipment used: No specialised equipment is required to lay the mat.
Conventional method: The conventional material specified in MOSRT&H for the purpose is mastic asphalt. Laying and compaction of mastic is a non-mechanised operation and can lead to significant variation in thickness and compaction in a small area.
Technology proposed: "Latest technology like hybrid geosynthetic paving mat may be used for waterproofing courses on bridge decks," says Aseem Prabhakar, HOD (Highways), Intercontinental Consultants and Technocrats Pvt Ltd. "We have recently recommended such a geosynthetic paving mat [with a tack coat application of 1 kg/sq m] conforming to ASTM D 7239 in lieu of conventional 12/25 mm thick mastic asphalt for Surat-Dahisar [NH-8] Highway Project [BOT]."
Benefits: The geosynthetic mat helps reduce long-term maintenance and rehabilitation costs. It improves fatigue resistance and improves flexural pavement performance under loading.
Cautionary note: This technology still needs to be tested in our environment and there are no codal provisions available as of now for its use.
Alternate usage by industry: S V Vaidya, President, Gayatri Projects Ltd, cites the use of a bituminous sheet-Tikitar-as an effective replacement for the laborious and time-consuming mastic asphalt over the bridge decks of a bridge project before laying bituminous concrete.
Consultants' response: Bituminous sheets aren't better than mastic as these are brittle in nature and susceptible to ing which nullifies the very purpose of water proofing.
Quick Bytes
• The road equipment market is likely to grow at a rate of 10-15 per cent per annum.
• Soil is the key ingredient in the making of good roads.
• Appropriate compactors used to stabilise soil also ensure better outcomes.
• Imparting adequate training is important for efficient use of road equipment
• Contractors should take up the mantle of responsible road engineering before being forced to do so.
- Construction
- Update
- Portal
- Magazine
- CW-India
- May
- 2011
- India
- road contractors
- equipment
- Government
- crushing
- screening
- asphalt plants
- MM Shahane
- Voltas
- concrete pavers
- investment
- NG Thatte
- PBA Infrastructure Ltd
- SV Vaidya
- Gayatri Projects Ltd
- Volvo India
- soil stabilisation
- AM Muralidharan
- RASTA
- Ramesh Palagiri
- Wirtgen India
- concrete roads
- BS3 norms
- Hybrid technology
- Vogele pavers
- L&T
- HCC
- Bihar
- TERPL
- Aseem Prabhakar
- HK Sehgal
- MoRT&H
- NHAI
- O&M
- NHDP
- Waterproofing
Newer technologies and methods are gaining acceptance by road contractors even as equipment vendors double up their efforts to serve the industry, discovers Charu Bahri. The Indian market for road construction equipment has seen a meteoric rise in the past few years mainly owing to the Government's thrust on expanding the national highways and state and rural roads networks. Road construction equipment of every kind, from crushing and screening plants to asphalt plants, asphalt and concrete pavers, compactors and motor graders, is being increasingly sought by contractors executing road construction projects. MM Shahane, Executive Vice-President and COO, Engineering Products and Services Business Group, Voltas, which offers crushing and screening equipment and concrete pavers, estimates the total market for such equipment to have been worth Rs 3,000 crore last year. “At the rate investments are being made in the road sector, this will grow steadily at 10 to 15 per cent per annum,” he says. Contractors also see the market for road construction equipment widening for quite some time to come. “India offers plenty of scope for BOT road projects and this is likely to continue for the next 20 years,” opines NG Thatte, Executive Director, PBA Infrastructure Ltd. “Public resistance to too much tolling builds slowly, but it is inevitable over time. People will slowly realise that roads are an amenity expected from a welfare state. For now, though, BOT is an excellent concept.” Soil stabilisation Soil is a key ingredient in the making of good roads. As SV Vaidya, President, Gayatri Projects Ltd, explains, “Utilising the best available soil helps avoid problems of compaction and future settlements that are associated with poor soil quality.” Further, Thatte observes, “Fortunately, India by and large has good soil even if rising land prices and royalties have seen its cost increase by about 50 times in the past 30 years. But black cotton soils and plastic soils must be avoided at all costs. The analysis of soil characteristics helps identify suitable varieties to use for embankments and reinforced earth fills. Though some contractors tend to rely on the visible inspection of soil based on their experience, Thatte believes this should be avoided, “Nothing can replace scientific investigations conducted in a laboratory.” Appropriate compactors used to stabilise soil also ensure better outcomes; it also helps if the product is backed by useful services. Volvo India offers a range of compactors especially designed for soil stabilisation. “As our equipment is backed by core expertise, we're also able to offer soil stabilisation technical consultancy through our Resource Centre for Asphalt and Soil Training Academy or RASTA initiative,” says AM Muralidharan, Managing Director, Volvo India. “That means we study the soil at the customers' site and suggest solutions to improve soil stabilisation for better outcomes. We also offer similar services for asphalt roads.” Paving equipment Pavers should ideally assist the exact implementation of road designs. For that, Muralidharan believes they need special screeds to ensure the slope and grade finish meet the design. “Our screeds have a tamping unit followed by a vibratory screed that gives good density and finish for asphalt layers,” he adds. Vogele pavers are hailed globally for their performance. Ramesh Palagiri, CEO & Managing Director, Wirtgen India, attributes this to the patented TP2 high compaction technology that helps achieve compaction (up to 98 per cent) faster than comparable machines. “Overall, needing fewer roller passes delivers operational efficiencies and results in a better ride quality as the mix compacts better when it is hot,” he says. With concrete roads being preferred for sectors with high traffic density, for their much longer life compared to asphalt roads; concrete pavers based on better technologies are also in focus. “Modern concrete pavers help improve the outcome of concrete roads as they include electronic controls and software offering better control in forming concrete,” elaborates Shahane. “Electronic controls mix cement and aggregates more accurately thereby producing more consistent concrete. This in turn extends the life of the road surface and reduces its need for maintenance. So, such features also improve the economics of concrete roads.” Better efficiencies Nowadays, road construction equipment runs on latest engines complying with new emission standards, thereby lowering fuel consumption and optimising energy. In this context, Shahane cites BS3 norms (equivalent of Euro III norms) as being the preferred standard. As far as fuel efficiency is concerned, Muralidharan endorses a holistic approach to the subject as practised by Volvo. “Volvo meets environmental standards set by the Government of India,” he says. “We deliver fuel efficiency across all elements of our machines via our engines, systems, operator behaviour and future technologies, while increasing productivity for our customers. Hybrid technology is also under development as one part of this wider range of fuel-saving solutions. Buses and trucks are leading this technology within the Volvo group and other product groups will take advantage of the knowledge too.” Efficiencies not only stem from making the best use of equipment but from getting the right asphalt mix and imparting training in operating the machine and in application engineering. Wirtgen India offers these services for its Vogele pavers. An application engineering team helps its clients achieve desired outcomes. “Contractors like L&T, HCC, KMC Constructions and Ashoka Buildcon have used our services,” shares Palagiri. Under its RASTA initiative, Volvo India also educates end users about ways to optimise the usage of Volvo equipment and in the process of road building. “Such training ultimately helps the government, the owner of the road who invests in infrastructure, as well as consultants who design and supervise the process and contractors implementing the designs,” emphasises Muralidharan. “Knowhow is the key to meet international standards.” Maintenance by recycling One kilometre of a virgin one/two-lane road costs several crores of rupees. Multiplying this with the thousands of kilometres of already constructed and upcoming road length gives a fairly good idea of the huge investment that is being made to improve the country's road network. But making roads is not enough. Roads must also be maintained to get the most out of these newly created assets. If constructed well, in most instances, it's the top layer of roads (not lower depths) that wear out and must be refurbished to restore drive-ability. The government can do a lot to prevent the mechanical failure of roads. Road surfaces are designed to be strong enough to withstand the density of vehicles plying on them and the cumulative weight of vehicles passing at any point in time. Over-laden trucks significantly burden roads for which reason they shouldn't be allowed. The Bihar government has shown definite will in disallowing overloaded trucks; indeed, a positive step. In instances where the roughness index (measure of loss of ride comfort) of the road mandates resurfacing, it is cost-effective and faster to resurface the road using recycling technology. Top layer corrections conducted using recycling yield significant cost benefits. The cost of hot in place recycling is about 10 per cent less than conventional overlays at current market rates (see case study). Telcon Ecoroad Resurfaces Pvt Ltd (TERPL), a Telcon initiative, has been spearheading the goodness of recycling of bituminous road. Road consultants also endorse recycling. Aseem Prabhakar, HOD (Highways), Intercontinental Consultants and Technocrats Pvt Ltd, says, “As consultants, we recommend the use of eco-friendly materials like recycled aggregates. We recommended used bituminous milled material of existing damaged pavement as one of the components (15 per cent) in granular base course (wet mix macadam) materials for the NH-2 (Agra-Sikohabad) project. We also recommended using dismantled material of the existing pavement in the pavement construction of the NH-43 (Raipur-Dhamtari) project.” Contractors' take Ideally, contractors should take up the mantle of responsible road engineering before being forced to do so. Some, however, are reluctant, as they are under the impression that recycling road surfaces isn't legally permissible. To contractors who desist from adopting recycling, believing it isn't legally permissible, HK Sehgal, COO, TERPL says, “The process finds mention and acceptance in the MoRT&H's publication of Specification of Roads & Bridge Works (Revision 4), also called Yellow/Orange Book, under Section 517.” “Nothing stops a contractor from using a recycled material if he can demonstrate to the engineer its use according to the specifications laid down in the tender,” adds Prabhakar. “It is particularly relevant for Design Build Finance and Operate (DBFO) projects where there is flexibility in design and the concessionaire also has to maintain the road for the concession period of 10 to 20 years.” Recognising the benefits of recycling last year, the National Highways Authority of India (NHAI) declared that it would encourage the use of recycling the existing bituminous material (reclaimed asphalt pavement or RAP) to upgrade an existing bituminous pavement. Such recycling has been made mandatory in all projects where the process will yield cost savings. Possibly as a result, contractors are now thinking in terms of recycling. “Although we have not utilised recycling technologies for any of our road projects so far, we may use them for the maintenance of our BOT roads during the O&M phase in future,” says Vaidya. Contractors are also open to accept the benefits of recycling even if complacent to change their ways. “Recycling is certainly a better way of going about road resurfacing, especially in places where road construction materials need to be transported over great distances, say more than 20 to 25 km,” says Thatte. “Then, it yields significant economic advantages. But some old roads are seen to be very hungry for fresh bitumen that conventional methods appeal more. Contractors also tend to adopt the path of least resistance; changing techniques always calls for more effort.” That's why he believes that government intervention would help make the industry more responsive towards reusing available materials. “When the government made the use of fly ash compulsory, contractors were left with no option but to follow the mandatory specifications, and we've now realised the benefits,” he adds. “So far, contractors only recycle when it is compulsory, like we did in a small project because it was mandated by the project terms.” At the end of the day, Thatte believes the better quality of road infrastructure being created today is an outcome of superior and more readily available machinery and higher expectations of the government and its people. Rising public demands for good quality also spur change for the better. Palagiri observes, “The durability and the ride quality of roads tends to depend on the intent of the owner – the NHAI, a local municipality, or PWD – to demand quality,” even as he emphasises that Indian contractors possess the necessary technology and know how. With the right ingredients in place, the road ahead should be far smoother than ever before. Case Study: Road recycling in Delhi By: Telcon Ecoroad Resurfaces Pvt Ltd (TERPL), a company that takes up recycling contracts on its own; performs recycling for BOT concessionaires, as subcontractor to NHAI's prime contractor; and sells AR2000 trains used for recycling.Method adopted: Hot in place (hot-in-situ) recycling. This involves heating the existing road, scarifying it, mixing virgin mix as decided by pre-engineering investigations to upgrade (recycle) the existing mix to current MoRT&H standards, and relaying it for compaction all in real-time without taking any material away from the road site.Length recycled: About 1.5 million sq m of bituminous pavement (around 1 million of which is in Delhi alone, mostly on major roads like the Ring Road, part of the NHDP).Equipment used: AR2000 Super Recycler, an 80-m-long train of equipment (end-to-end). The train comprising pre-heaters 1 and 2, heater miller and heater mixer all heat the road or the milled (reclaimed asphalt pavement) or mixed (recycled asphalt pavement) material depending upon which part of the site the train is working on at a given point of time. Speed of work: A good working speed is between one to two single lane km per shift of eight to 10 hours. In cities, the speed may be curtailed by traffic, encroachments on the roads and the straightness (or otherwise) of the road. Technical specifications: The depth of milling and/or final compaction thickness is 50 mm though 60 mm; may also be achieved. As the existing road, milled road, milled asphalt mix, hot mix and freshly recycled asphalt mix are all heated, there is hot to hot bonding of the recycled mix with the heated road surface, leading to better durability of the road. Finish compaction is usually over by the time the material cools to 90° C. The road is delivered to the user as soon as it cools to 50° C.Durability: Roads recycled by TERPL have lasted between three and five years without needing any further maintenance.Benefits: The environmental benefits obviously include the preservation of energy and an increasingly expensive finite resource, bitumen, a derivative of oil. By weight, bitumen accounts for a minimum of 5 per cent of the hot mix that goes into making the top layer (wearing course) of a road. Recycling helps avoid burying the remaining old, weathered, brittle bitumen left after the service life of the wearing course under a fresh layer. At best, only about 2 per cent more fresh bitumen is needed to rejuvenate the old mix. Some say that a trillion rupees lie buried in city roads. Engineering benefits include the preservation and correction of road geometry, and not needing to raise elements of the roads' profile such as footpaths, signals, lamp posts, culverts, etc. Maintaining the height of the road is much safer for structures by its side. Recycling also increases roads' resistance to rutting, scuffing and ravelling. As the hot mix is maintained at an optimum temperature throughout the process, the resulting surface is more durable and assures superior ride quality. Case Study: Waterproofing courses on bridge decks Project: Surat-Dahisar (NH-8) Highway Project (BOT); the proposed mat was used on all bridges with approaches on high embankmentsContractor: IRB Ltd Consultant: Intercontinental Consultants and Technocrats Pvt LtdEquipment used: No specialised equipment is required to lay the mat.Conventional method: The conventional material specified in MOSRT&H for the purpose is mastic asphalt. Laying and compaction of mastic is a non-mechanised operation and can lead to significant variation in thickness and compaction in a small area.Technology proposed: Latest technology like hybrid geosynthetic paving mat may be used for waterproofing courses on bridge decks, says Aseem Prabhakar, HOD (Highways), Intercontinental Consultants and Technocrats Pvt Ltd. We have recently recommended such a geosynthetic paving mat [with a tack coat application of 1 kg/sq m] conforming to ASTM D 7239 in lieu of conventional 12/25 mm thick mastic asphalt for Surat-Dahisar [NH-8] Highway Project [BOT]. Benefits: The geosynthetic mat helps reduce long-term maintenance and rehabilitation costs. It improves fatigue resistance and improves flexural pavement performance under loading. Cautionary note: This technology still needs to be tested in our environment and there are no codal provisions available as of now for its use.Alternate usage by industry: S V Vaidya, President, Gayatri Projects Ltd, cites the use of a bituminous sheet-Tikitar-as an effective replacement for the laborious and time-consuming mastic asphalt over the bridge decks of a bridge project before laying bituminous concrete.Consultants' response: Bituminous sheets aren't better than mastic as these are brittle in nature and susceptible to ing which nullifies the very purpose of water proofing. Quick Bytes • The road equipment market is likely to grow at a rate of 10-15 per cent per annum.• Soil is the key ingredient in the making of good roads.• Appropriate compactors used to stabilise soil also ensure better outcomes.• Imparting adequate training is important for efficient use of road equipment • Contractors should take up the mantle of responsible road engineering before being forced to do so.
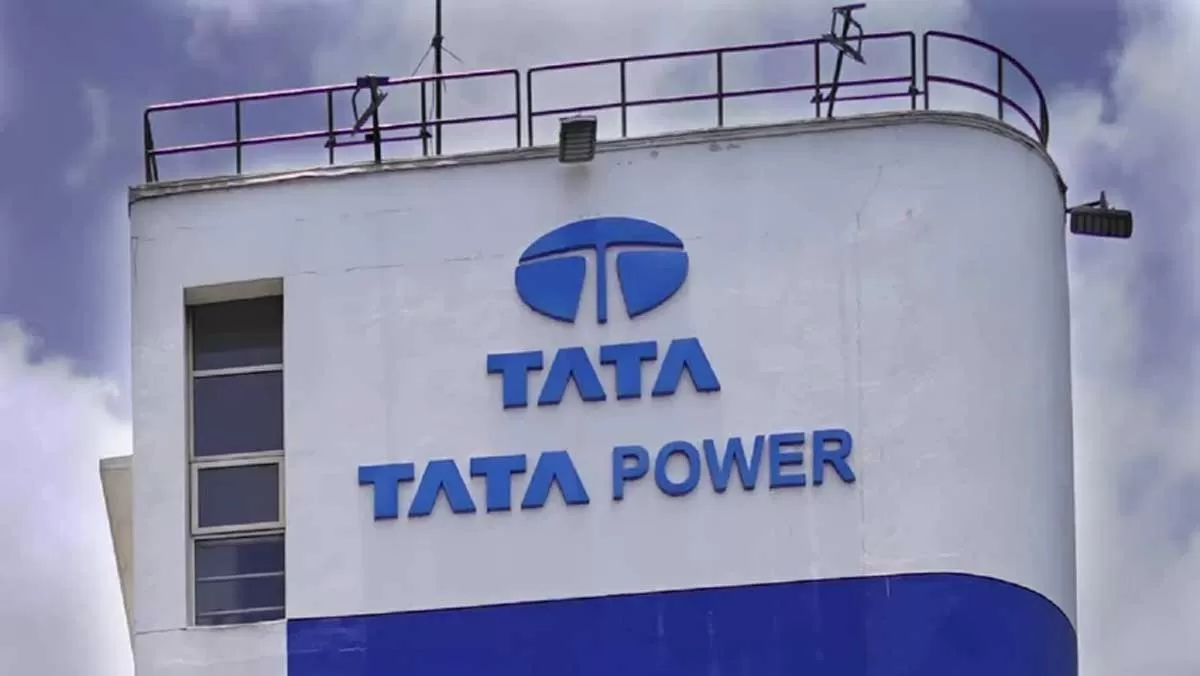
Tata Power, Suzlon Ink Rs 60 Billion Wind Energy Deal in Andhra
Tata Power has signed an agreement with Suzlon Energy to develop, construct, and supply 700 megawatt (MW) wind turbines in Andhra Pradesh. The Rs 60 billion project forms part of a 7 gigawatt (GW) renewable energy plan announced by Tata Power Renewable Energy (TPREL) and the state government in March 2025.This marks the first wind energy project in the state since 2019. The larger 7 GW programme, covering solar, wind, and hybrid projects with or without storage, is expected to attract investments of around Rs 490 billion, making it one of the state’s largest clean energy commitments.The turb..
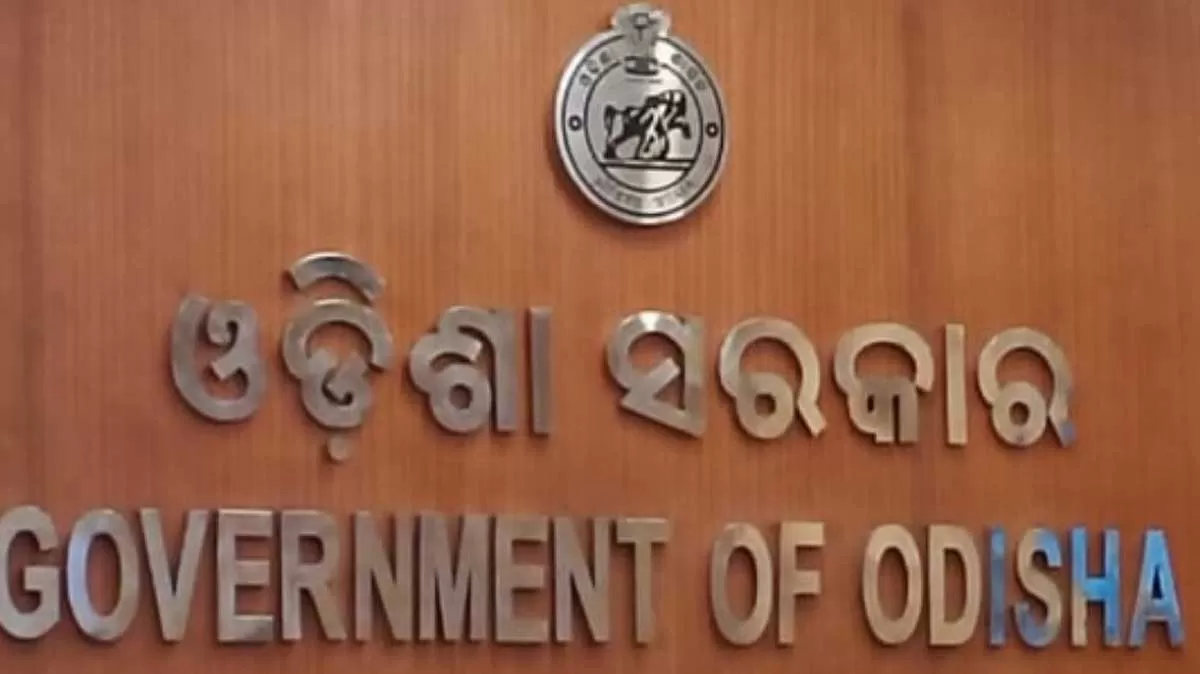
Odisha Approves Rs 12.6 Billion For 32 New Bridges
Odisha is set for a major infrastructure boost with the approval of 32 new bridges under the Setu Bandhan Yojana for FY 2025–26. The project, valued at Rs 12.6 billion, is aimed at improving road connectivity across ten districts, enhancing mobility and driving local development.The bridges will be constructed in Bolangir, Subarnapur, Nayagarh, Sambalpur, Malkangiri, Bargarh, Koraput, Jagatsinghpur, Cuttack, and Puri. Many of these areas are rural or located in difficult terrains, where improved accessibility will greatly benefit the transportation of goods and public mobility.Setu Bandhan Y..
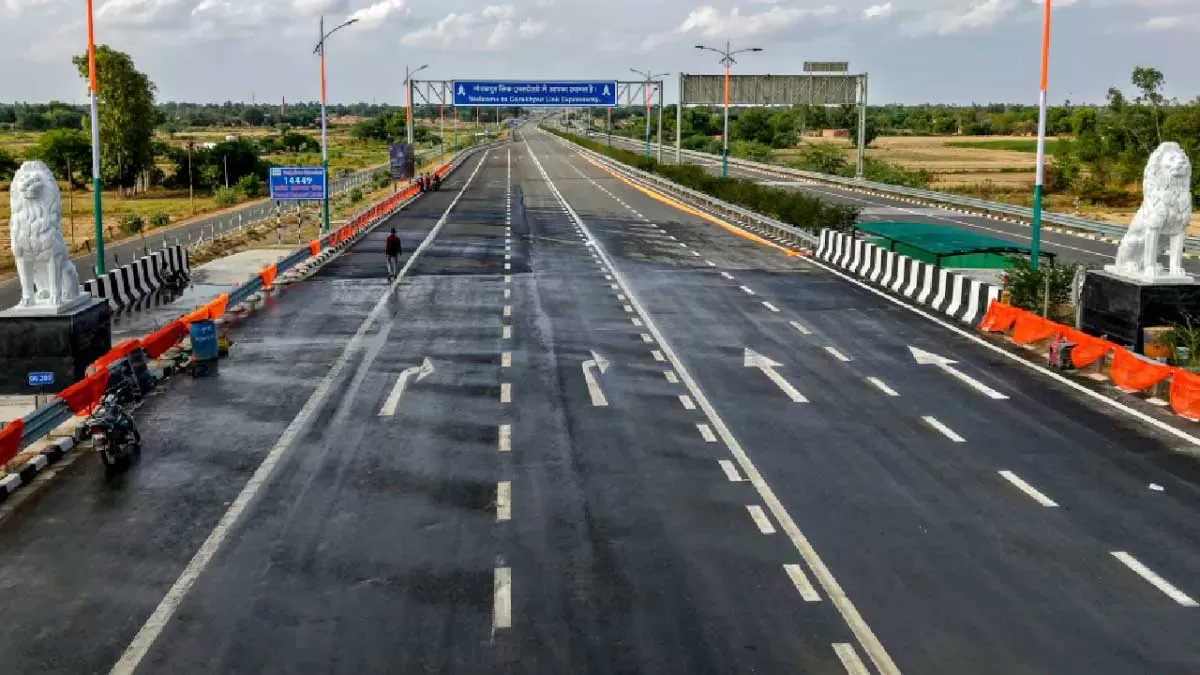
UP Plans Rs 350 Billion Gorakhpur–Shamli Expressway
Uttar Pradesh is preparing to build its largest expressway, a 700-km six-lane project that will surpass the 570-km Ganga Expressway from Meerut to Prayagraj. Designed as a greenfield project, the Gorakhpur–Shamli Expressway will cut travel time between eastern and western Uttar Pradesh to just six hours, transforming regional connectivity.The expressway will pass through 22 districts and 37 tehsils, bringing faster travel and significant economic benefits, including higher land values for farmers and employment opportunities during and after construction. A drone survey to map the route is e..
Latest Updates
Recommended for you
Advertisement
Subscribe to Our Newsletter
Get daily newsletters around different themes from Construction world.
Advertisement
subscribe to the newsletter
Don't miss out on valuable insights and opportunities
to connect with like minded professionals