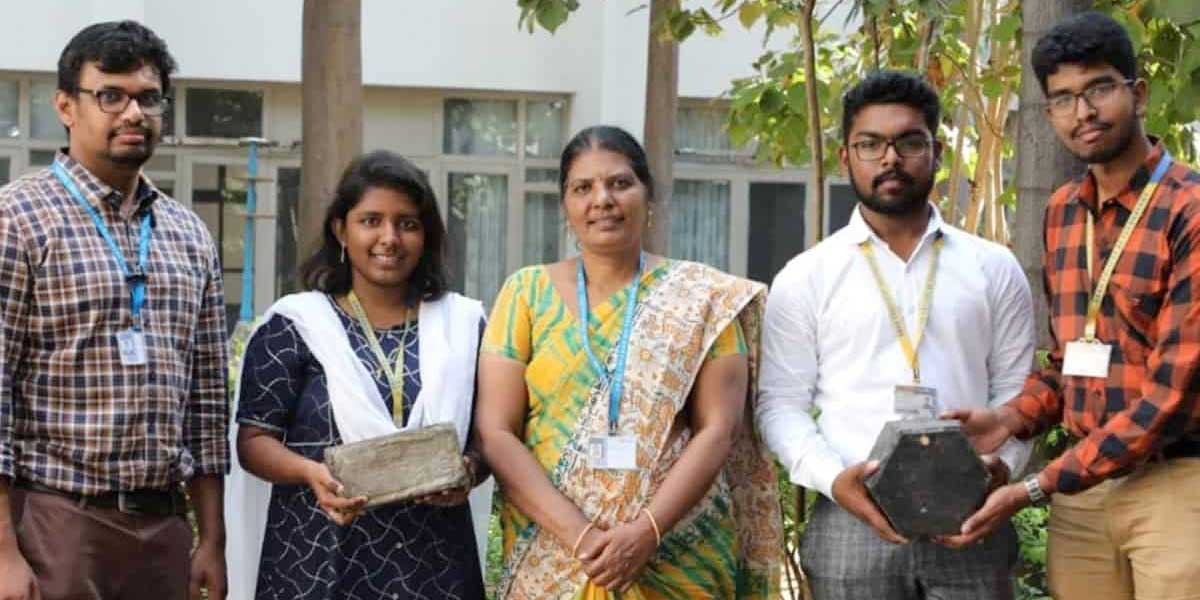
Making PPE waste into bricks without cement is now possible
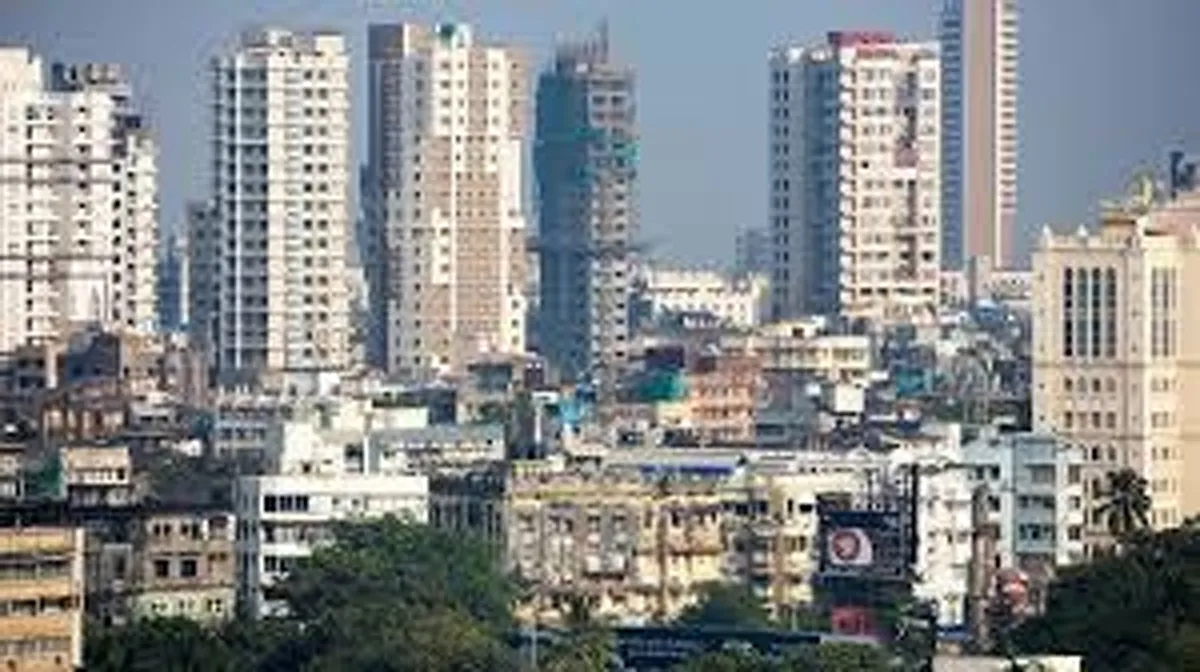
Mumbai Records 11,230 Property Deals in August 2025
Mumbai’s property market remained resilient in August 2025, with 11,230 property registrations recorded under the Brihanmumbai Municipal Corporation (BMC) jurisdiction, according to data released by Knight Frank India. While this marks a 3 per cent year-on-year (YoY) decline compared to 11,631 registrations in August 2024, activity stayed robust despite the marginal dip.On a month-on-month (MoM) basis, registrations fell 11 per cent from 12,579 deals in July 2025, indicating seasonal moderation. However, the city’s stamp duty collections still reached Rs 10 billion, reflecting a 6 per cent..
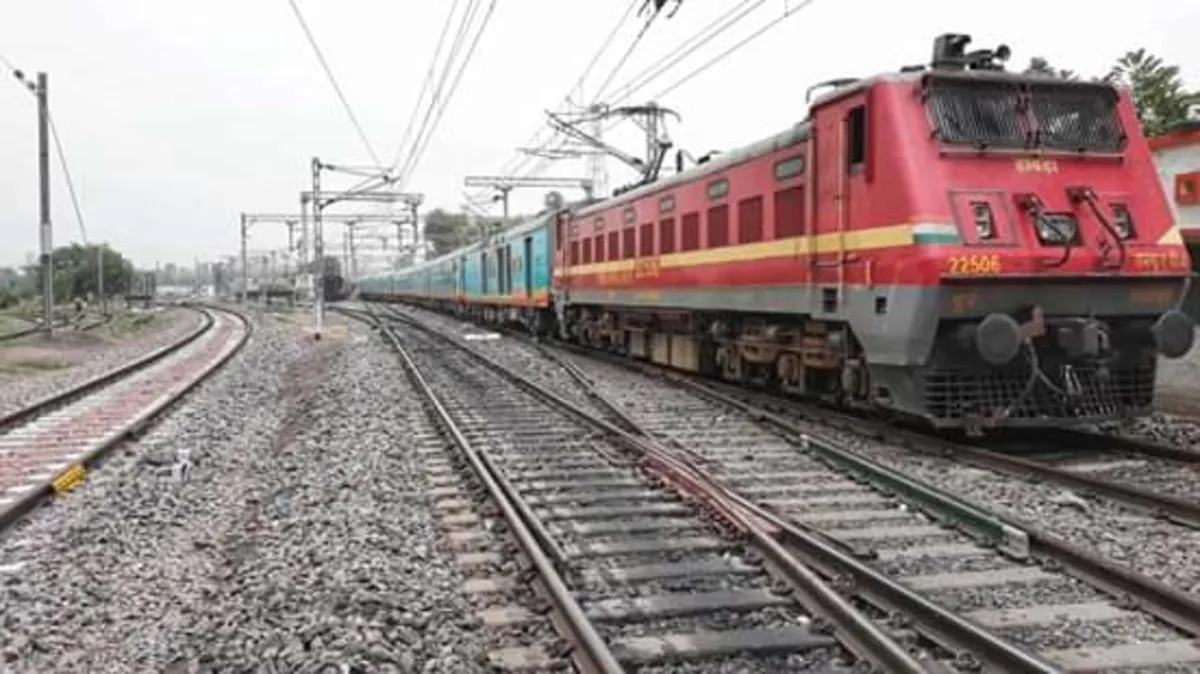
68 Jammu-Katra Trains Cancelled Amid Rain Damage
Jammu and Katra railway services remain severely affected as Northern Railway announced the cancellation of 68 trains—both incoming and outgoing—until 30 September, due to extensive track damage caused by heavy rains and flash floods. Meanwhile, 24 trains are scheduled to resume operations gradually.The Jammu railway division has experienced a complete halt in services for the past eight days, following track misalignment and breaches at several points along the Pathankot–Jammu section. Torrential rainfall since 26 August led to widespread flooding and damage, stranding hundreds of passe..
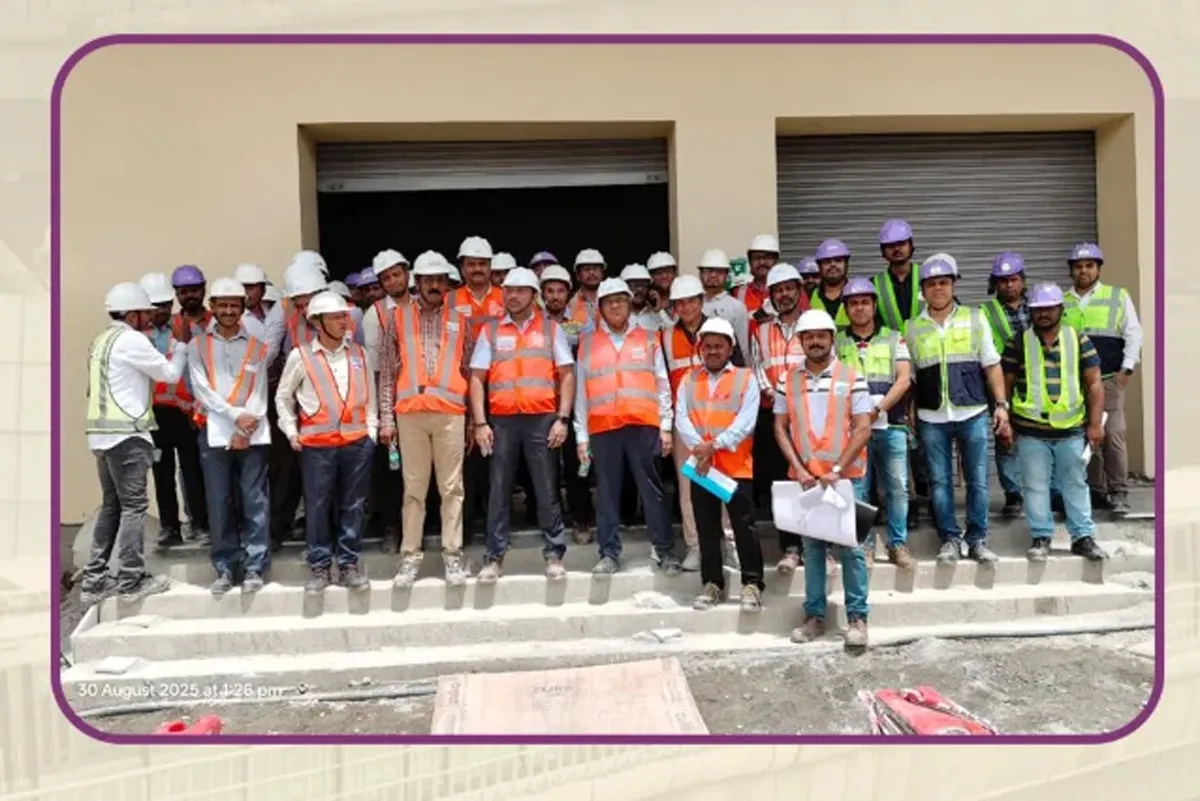
Bangalore Metro MD Reviews Reach 6 and Phase 2A Progress
Bangalore Metro Rail Corporation Limited (BMRCL) Managing Director, Dr J Ravishankar, IAS, conducted inspections of key metro corridors on 29 and 30 August, reviewing the progress of Reach 6 (Pink Line) and Phase 2A (Blue Line).On 30 August, the inspection covered Reach 6, a 21.39-km corridor stretching from Kalena Agrahara to Nagawara, with 18 stations. This stretch is part of Phase 2 of the Bangalore Metro project. Dr Ravishankar assessed the status of civil works, finishing, track laying, and system integration between Kalena Agrahara and MG Road.Earlier, on 29 August, the MD inspected Phas..