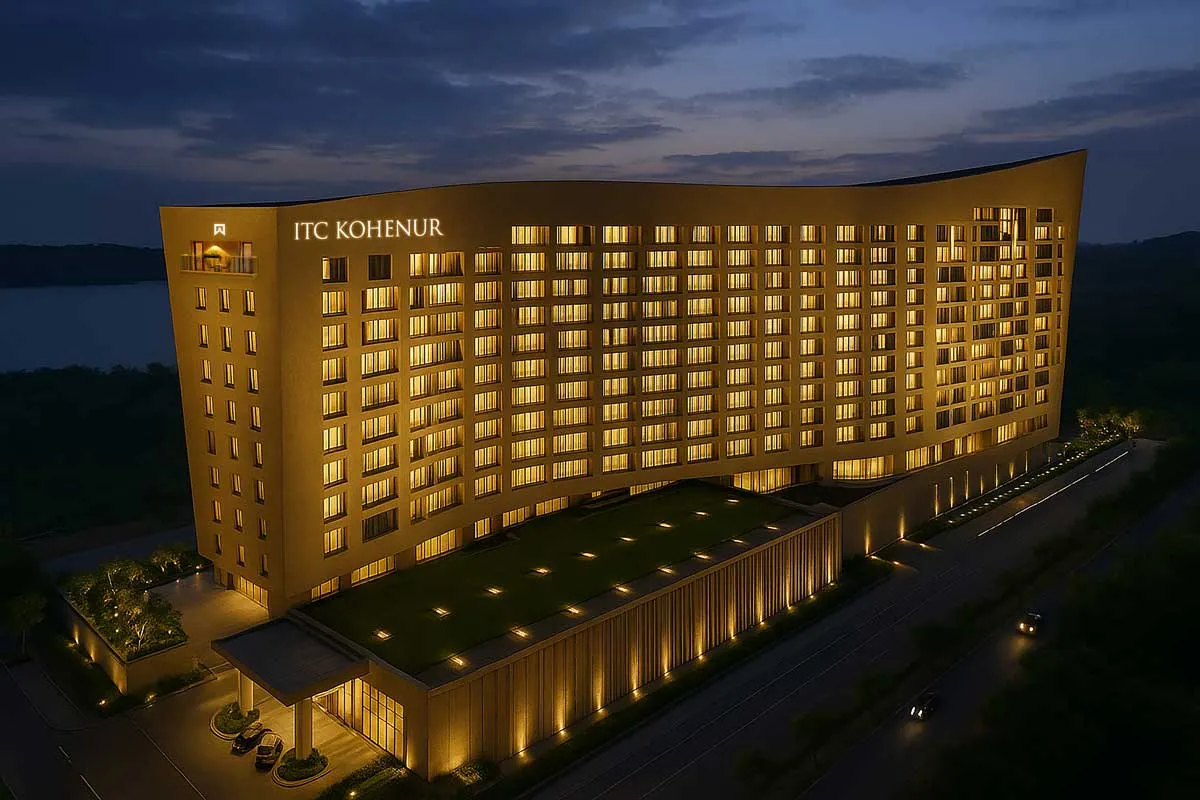
Pidilite PPS Sets New Standards in Hospitality Construction
In the fast-paced world of hospitality, where every surface tells a story and every detail impacts the guest experience, Pidilite Professional Solutions (PPS) is emerging as a trusted partner for performance-driven construction. Built on Pidilite’s legacy of customer-centric innovation, PPS offers tailored solutions that go far beyond materials—delivering expertise, accountability, and assurance from design to execution.PPS is a natural extension of how Pidilite has always worked—through deep insight into customer needs and by designing fit-for-purpose solutions. Pidilite’s brands..
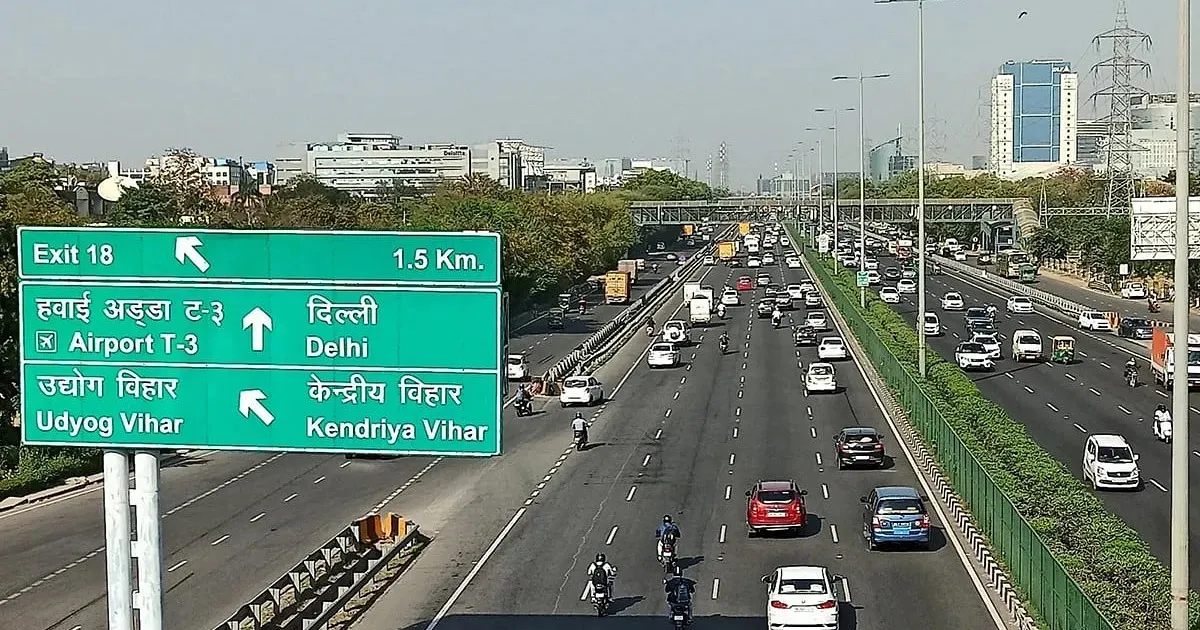
Rs 2.82 Billion Approved for NH-48 Flyovers, Footbridges
Gurugram’s section of National Highway 48 is set for a significant infrastructure upgrade, with the Central Government approving Rs 2.82 billion for the construction of four flyovers and nine foot overbridges along the Gurgaon–Kotputli–Jaipur corridor. This initiative aims to ease congestion, improve commuter safety, and boost regional connectivity, according to officials.The planned flyovers will be built at Panchgaon Chowk, Rathiwas, near the Hero Company, and Sahlawas. The nine foot overbridges will be constructed at Shikhopur, Manesar, Binola, Rathiwas, Malpura, Jaisinghpurkhera, Sid..
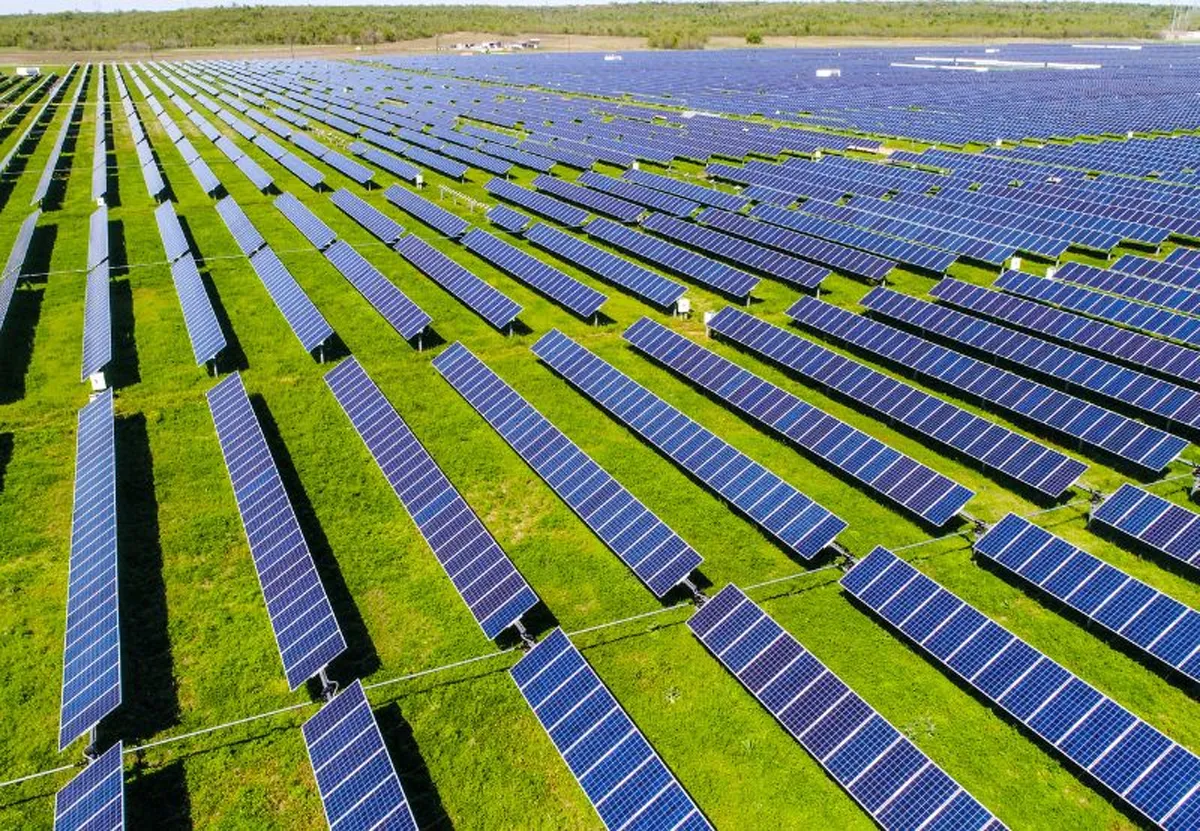
VSL Wins Rs 810-Cr O&M Deal for 810 MWp NGEL Solar Assets
VSL Renewable Services has secured a Rs 810 crore operation and maintenance (O&M) contract for 810 MWp of NTPC Green Energy’s (NGEL) solar power projects spread across Andhra Pradesh, Madhya Pradesh, and Rajasthan. The contract duration is 36 months.The tender, issued in January 2025, was divided into two lots: Lot 1 for 1,054 MWp and Lot 2 for 810 MWp. VSL emerged as the lowest bidder in both categories, but was awarded only Lot 2 in accordance with NTPC’s tender guidelines.Advanced Monitoring and Tailored StrategiesThe O&M scope will employ artificial intelligence and Internet of..