- Home
- Infrastructure Energy
- POWER & RENEWABLE ENERGY
- Tunnelling Success
Tunnelling Success
There's a lot happening beneath the surface, thanks to burgeoning construction opportunities and superior equipment and expertise on offer, finds Charu Bahri.
The action has shifted underground. A spate of opportunities for underground construction, in the shape of hydropower and irrigation projects, metro rail tubes, and micro tunnelling for urban sewerage and storm water drainage projects, is driving the market for tunnelling equipment to unprecedented heights.
Debabrata Sain, Tunnelling Manager – West Asia, Sandvik Asia Pvt Ltd, Sandvik Mining and Construction, sees the year 2005 as the industry's turning point. "Prior to this, underground construction was typically restricted to hydropower projects in the public sector, and no more than one such opportunity presented itself every year," he says. "After 2005, owing to the government's accelerated efforts for the development of hydropower, a three-stage clearance system was introduced thanks to which we saw a dramatic reduction in planning to the clearance time of hydro projects and the opening up of the sector to private players. Fortunately, enterprising private promoters saw merit in putting their money into clean and sustainable energy projects."
Sain also cites the government's emphasis on connecting Jammu & Kashmir and the Northeast to the mainland by rail, constructing crude storage caverns in coastal areas anticipating supply disruption and constructing lift irrigation tunnels as a boon for the tunnelling equipment industry. "Now, the Austrians, Norwegians, Australians, and Germans are bringing new, better and faster technology to the Indian market, which is already worth Rs 4 billion annually," he adds.
Industry forecast
Going forward, the prospects look bright for the entire range of tunnelling equipment on offer. "In the near future, we expect highway projects to spur forward demand for tunnelling equipment, specifically for tunnel boring machines [TBMs]," opines Shyam Chengalath, Managing Director, Robbins Tunnelling and Trenchless Technology (India) Pvt Ltd. "We expect a 25 to 30 per cent increase in the number of machines sold on a year-on-year basis." He believes the removal of subsidies for TBMs intended to be used for hydro and highway projects will increase the use of mechanised tunnelling in these areas in the short to medium term. As it is, India has fallen short of its current five-year plan deadlines for hydro and underground/mountain road projects. "We specialise in manufacturing machines used for the drill and blast tunnelling method," says Anirban Sen, Business Manager, Underground Rock Excavation, Atlas Copco Construction and Mining Sales. "We estimate the market size for such machines to range between Rs 120 crore to Rs 140 crore per annum. This market is growing steadily, driven by the government's bullish plans for investment in the construction and power sectors. We expect it to grow by 10 to 15 per cent, if not more, in the next three to four years. Equipment for other methods involving mechanical cutting, like TBM, also has a sizeable presence in the country."
Expanding horizons
Growing prospects are encouraging multinational players to set foot in the country and this, in turn, is helping Indian contractors to execute path-breaking projects. Robbins, for instance, offers TBMs of various kinds – shield TBMs, open gripper TBMs, earth pressure balanced TBMs, horizontal auger boring machines, etc – and diameters ranging from 1.6 m to 10 m. It is currently operating the largest TBM in India, with a diameter of 10 m, to bore the world's longest tunnel for JP Associates. Robbins is also going to start boring a 12-km tunnel for a JV of Patel, SEW and Coastal Projects in Madhya Pradesh. This project will make use of a special hybrid machine that can run in soft ground in earth pressure balanced (EPB) mode as well as in hard rock, in open mode.
Sandvik offers a range of time and cost-saving equipment aimed at helping contractors to rapidly mobilise resources and start operations using reliable machines backed by on-site support. Its fully automated 'intelligent' drill jumbo, featuring an inbuilt capability to check the area of influence of an explosive while designing the drill pattern, will be used for the construction of the Punatsangchhu II hydropower project. Sandvik also expects its state-of-the-art road headers, which are capable of cutting rock up to 180 mpa to be put to use in the near future, thereby eliminating the blasting damage to rock in sensitive hydropower projects while retaining an inbuilt contingency measure to cut hard rock in case it is encountered in variable Himalayan geology. "As most underground projects are required to be executed in the Himalayas and often in difficult geological conditions made worse by extreme hydrological events, contractors need versatile drilling machines capable of performing various activities in a drill and blast cycle," says Sain. "In places where mechanical excavation is desired, contractors opt for machines that can cut soft to hard rock up to 150 mpa. These facts coupled with reliability and low operational costs are driving the demand for our equipment."
Atlas Copco has more than 140 boomers working across India and Bhutan in hydropower, road and railway projects that necessitate tunnelling. Sen shares that Atlas Copco drill rigs helped create the 23 km-long, 6.8-m finished diameter, 50-sq-m modified horseshoe-shaped, concrete-lined headrace tunnel (HRT) carrying the intake water to the turbines of the Tata hydro scheme in Bhutan. This HRT was excavated at 7.5-m diameter under a minimum rock cover of 60 m and a maximum of nearly 1 km.
Computer-driven equipment
The range of high-tech tunnelling equipment on offer also includes computer-controlled machines proven to deliver cost efficiencies to the process. Speaking about how Atlas Copco's computer-based control systems facilitate the construction of tunnels, Sen says, "Our high-precision tunnelling concept allows raw data such as rock hardness, zones and other relevant rock mass characteristics to be continuously picked up by the drill rig and translated, in real-time, into instructions to fine-tune the tunnelling process to improve safety, efficiency and economy. It delivers cost efficiencies by enabling the rig to be navigated in no more than five minutes (compared to the 10-30 minutes for manual methods) into precisely the right position, with accuracy levels better than 1 cm compared to the usual 10 cm. More precise navigation and appropriate drill plan handling helps to reduce under-break and over-break costs in terms of concrete and man hours."
Contractors are hugely benefiting from the widening range of tunnelling equipment. According to Satish Suneja, Project Manager, Alpine-Samsung-HCC JV, Design and Construct contractor for the Airport Express Line, such machines offer useful features that help speed up activities. "We used two EPB TBM of a Herrrenknecht-make equipped with 32 cutters to help get through the mixed soil conditions to bore a 2.2-km stretch of tunnel for package C1 of the Airport Express Line project," he reveals. "The remaining 1.1-km stretch and two large stations modelled like city airport terminals were constructed using the cut-and-cover method. For package C6, comprising a 2.6 km stretch, we applied the New Austrian Tunnelling Method (NATM) using Atlas Copco computerised boomers (L2C), tele-handlers of Merlo make and fully articulated Volvo haulers. There was no way we could have completed the job in the given circumstances and timeframe (nearly one year) without using these machines."
Comparing the two methods used for the C1 section of the express line, Anuj Dayal, PRO, Delhi Metro Rail Corporation, shares, "TBM tunnelling was much faster than the cut-and-cover method, especially in busy areas and where the alignment was very deep, that is, the Connaught Place area and on the New Delhi Railway Station road."
Suneja also points out that the economics of using expensive high-tech tunnelling equipment kicks in only when long stretches of tunnels are constructed. "You don't break even in shorter stretches, but being involved in the sector for the long haul, we hope to utilise our investment in equipment for future projects," he adds.
High-tech equipment is not only useful from the point of view of enhancing productivity. Tony Simmonds, Plant Manager, Leighton Contractors India, explains how it also helps to give more flexibility with manpower, especially in areas where skill shortages are present. "We use highly computerised top-of-the-line equipment incorporating the most recent innovations," he says. "Not only does automated and semi-automated equipment help increase productivity, but it is also easier to teach operators using high-tech equipment wherein you need to control a minimal number of input functions rather than having to take total control of a machine and trying to make it perform to its optimum. Computerised machines also provide real-time accurate operational data, and long-term cost savings, and the software they use tracks many variables in an operation. This data helps estimate ground conditions and thus, has huge potential to save time and costs."
Contractorspeak
Leading global contractors are looking at establishing a long-term presence in the country. "We foresee many opportunities to construct tunnels in India, especially looking at the dynamics of the transportation and hydro project sectors," says Simmonds. "Leighton has been awarded a $500 million contract to construct the Chenani-Nashri Tunnel in Jammu & Kashmir. This 9 km, two-lane (13.3 m diameter) main tunnel along with a parallel escape tunnel (5 m diameter) in the lower Himalayan mountain range will help link the northern state to the rest of India. The tunnel, located at an elevation of 1,200 m, will be constructed using the NATM of sequential excavation and support. When it is completed, the tunnel and its approach roads will provide a 10 km alternative all-weather route for 41 km of the existing NH1A, which passes through steep mountainous terrain and has significant geometrical, weather and safety issues."
Do global contractors engaged in the tunnel construction sector in India feel the lack of any equipment? According to Simmonds, "There is a lot of quality equipment available in the current market scenario, but there are major gaps as far as specialised tunnelling equipment such as tunnelling jumbo drills, road headers, and TBMs is concerned. Leading equipment companies like Robbins, Sandvik and Atlas Copco have representation in the country but the long waiting time following an order for new tunnelling equipment poses a challenge. Having said that, it's not as though this situation is typical only to emerging economies like India or China. Tunnelling equipment is in general very specialised and manufactured in few places in the world. At an average of 30 weeks from the factories, the lead times in India may be four weeks more than in developed nations. Thus, in turn, if contractors desire to start an awarded project without delay, they are compelled to take on a huge risk in pre-ordering such equipments."
Reducing lead times
Long lead times stem from almost all the tunnelling equipment deployed in the import country. Besides, unlike other sectors of the construction industry where products are bought readymade, TBMs are successful only when they are purpose-built for specific projects. "Factors such as tunnel diameter, lining design, geology, groundwater levels and groundcover must be taken into account prior to designing a tailor-made machine to exactly suit the application," says Chengalath. "This entails a waiting period of about eight to 12 months, from the date an order for a brand new TBM is placed to the time of starting work on a project. This isn't typical of India or because the equipment is imported; it's more or less the same anywhere else in the world; however, the OFTA (on-site first-time assembly) process and local value-added manufacturing can greatly improve on these start-up times."
In order to reduce waiting time, Robbins has adopted OFTA for its machines imported in knocked-down condition. "This means machines are not assembled and tested in factories as that would consume more time," adds Chengalath. "Modular assemblies are produced and tested in different locations worldwide and then directly shipped to jobsite locations, where they are assembled and the completed TBM directly put to work. This procedure saves about one to two months of start-up time, which in turn greatly benefits in regularising cash flow to the contractor. In future, we're also actively considering setting up a
manufacturing base in India, as this will help save another four to six weeks of shipping time."
Operational matters
Tunnelling equipment is highly specialised and necessitates a thorough understanding of different technologies that are effective for different kinds of rock or ground conditions. According to Chengalath, "Projects in the hydro and irrigation sectors mostly necessitate hard rock technology, while most urban projects need soft ground technology." For some projects, it also helps if a vendor has the capability to design hybrid machines for special applications and difficult ground conditions. As expertise is critical to successfully using sophisticated equipment like TBMs, providers are necessitated to maintain their own operational and service staff. At present, Robbins has a team of over 250 people in India, where the company has 100 km of tunnels under construction, second only to China. "No other country has as much potential for TBMs at the present time and in the near future," he adds.
Leading contractors are making use of these services by contracting out tunnelling construction to the specialists. For instance, Hindustan Construction Company (HCC) Ltd has contracted out tunnelling activities for a water project at Veligonda in Andhra Pradesh to Robbins, the supplier for the TBM, who is also responsible for its operation and maintenance. For its Kishanganga hydroelectric project, similar responsibility has been given to SELI. Both these sites mandate the use of TBMs for boring tunnels of about 7-10 m diameter. "Tunnelling is a highly specialised aspect of construction," says Shankar Srivastava, Vice-President - Equipment, HCC Ltd. "Larger TBMs cost around $40 million and can't be used without the right skill sets. Contracting out such work to experts who have decades of experience behind them ensures no compromise in productivity or quality of outcome. You need to apply the right expertise at the right time and at the right place."
Still, HCC is operating a Wirth TBM itself, for its Maroshi-Ruparel water supply tunnel project. This Mumbai-based project consists of the construction of a 12.24-km-long tunnel with 3.60-m diameter in three phases: Maroshi to Vakola (5.83 km), Vakola to Mahim (4.55 km) and Mahim to Ruparel College (1.86 km). Sain adds, "For this project, HCC also used a Sandvik probe drill machine as a guide for the TBM to operate without eventualities. The Sandvik probe drill gives the contractor an idea of what lies ahead in the unexcavated tunnel, thereby allowing HCC to mitigate risks."
Not all tunnelling equipment is being operated by vendors. Atlas Copco has already received orders for 20 computerised E-Series boomers in India, for which the delivery period varies between 25 and 35 weeks from the date of receiving a confirmed order depending on the size of the machine. Of these, 13 rigs will be deployed for the expansion of the Jammu-Srinagar highway by Navayuga Engineering Co and Leighton Contractors (India) Pvt Ltd. Six machines will be deployed in Punatsangchhu II HEP in Bhutan and one machine for the Rohtang Tunnel project by Afcons Strabag JV. The boomers are operated by the respective clients. However, Atlas Copco offers training not only to operators but also to the maintenance crew, at site and in a full-fledged training centre at Pune where regular courses on operation and maintenance are conducted. "We also conduct tailor-made programmes for our clients if requested," adds Sen. "Atlas Copco India has invested in a simulator to impart training to operators for E-Series boomers."
With the right training and investments by leading tunnelling specialists, there's no doubt that India's underground construction will look up in days to come.
To share your views on this article, write in at feedback@ASAPPmedia.com
- Construction
- Update
- Portal
- Magazine
- CW-India
- April
- 2011
- India
- equipment
- hydropower
- irrigation
- micro tunnelling
- sewerage
- storm water drainage projects
- Debabrata Sain
- Sandvik Asia Pvt Ltd
- Mining
- Jammu & Kashmir
- TBMs
- Shyam Chengalath
- Robbins Tunnelling and Trenchless Technology (India) Pvt Ltd
- Anirban Sen
- Atlas Copco
- investment
- Coastal Projects
- Madhya Pradesh
- EPB
- Punatsangchhu II hydropower project
- Bhutan
- HRT
- Tata hydro scheme
- Satish Suneja
- Airport Express Line
- NATM
- Anuj Dayal
- Delhi Metro Rail Corporation
- Tony Simmonds
- Leighton Contractors India
- China
- HCC
- Shankar Srivastava
- Veligonda
- Andhra Pradesh
- Mumbai
- Pune
There's a lot happening beneath the surface, thanks to burgeoning construction opportunities and superior equipment and expertise on offer, finds Charu Bahri. The action has shifted underground. A spate of opportunities for underground construction, in the shape of hydropower and irrigation projects, metro rail tubes, and micro tunnelling for urban sewerage and storm water drainage projects, is driving the market for tunnelling equipment to unprecedented heights. Debabrata Sain, Tunnelling Manager – West Asia, Sandvik Asia Pvt Ltd, Sandvik Mining and Construction, sees the year 2005 as the industry's turning point. Prior to this, underground construction was typically restricted to hydropower projects in the public sector, and no more than one such opportunity presented itself every year, he says. After 2005, owing to the government's accelerated efforts for the development of hydropower, a three-stage clearance system was introduced thanks to which we saw a dramatic reduction in planning to the clearance time of hydro projects and the opening up of the sector to private players. Fortunately, enterprising private promoters saw merit in putting their money into clean and sustainable energy projects. Sain also cites the government's emphasis on connecting Jammu & Kashmir and the Northeast to the mainland by rail, constructing crude storage caverns in coastal areas anticipating supply disruption and constructing lift irrigation tunnels as a boon for the tunnelling equipment industry. Now, the Austrians, Norwegians, Australians, and Germans are bringing new, better and faster technology to the Indian market, which is already worth Rs 4 billion annually, he adds. Industry forecast Going forward, the prospects look bright for the entire range of tunnelling equipment on offer. In the near future, we expect highway projects to spur forward demand for tunnelling equipment, specifically for tunnel boring machines [TBMs], opines Shyam Chengalath, Managing Director, Robbins Tunnelling and Trenchless Technology (India) Pvt Ltd. We expect a 25 to 30 per cent increase in the number of machines sold on a year-on-year basis. He believes the removal of subsidies for TBMs intended to be used for hydro and highway projects will increase the use of mechanised tunnelling in these areas in the short to medium term. As it is, India has fallen short of its current five-year plan deadlines for hydro and underground/mountain road projects. We specialise in manufacturing machines used for the drill and blast tunnelling method, says Anirban Sen, Business Manager, Underground Rock Excavation, Atlas Copco Construction and Mining Sales. We estimate the market size for such machines to range between Rs 120 crore to Rs 140 crore per annum. This market is growing steadily, driven by the government's bullish plans for investment in the construction and power sectors. We expect it to grow by 10 to 15 per cent, if not more, in the next three to four years. Equipment for other methods involving mechanical cutting, like TBM, also has a sizeable presence in the country. Expanding horizons Growing prospects are encouraging multinational players to set foot in the country and this, in turn, is helping Indian contractors to execute path-breaking projects. Robbins, for instance, offers TBMs of various kinds – shield TBMs, open gripper TBMs, earth pressure balanced TBMs, horizontal auger boring machines, etc – and diameters ranging from 1.6 m to 10 m. It is currently operating the largest TBM in India, with a diameter of 10 m, to bore the world's longest tunnel for JP Associates. Robbins is also going to start boring a 12-km tunnel for a JV of Patel, SEW and Coastal Projects in Madhya Pradesh. This project will make use of a special hybrid machine that can run in soft ground in earth pressure balanced (EPB) mode as well as in hard rock, in open mode. Sandvik offers a range of time and cost-saving equipment aimed at helping contractors to rapidly mobilise resources and start operations using reliable machines backed by on-site support. Its fully automated 'intelligent' drill jumbo, featuring an inbuilt capability to check the area of influence of an explosive while designing the drill pattern, will be used for the construction of the Punatsangchhu II hydropower project. Sandvik also expects its state-of-the-art road headers, which are capable of cutting rock up to 180 mpa to be put to use in the near future, thereby eliminating the blasting damage to rock in sensitive hydropower projects while retaining an inbuilt contingency measure to cut hard rock in case it is encountered in variable Himalayan geology. As most underground projects are required to be executed in the Himalayas and often in difficult geological conditions made worse by extreme hydrological events, contractors need versatile drilling machines capable of performing various activities in a drill and blast cycle, says Sain. In places where mechanical excavation is desired, contractors opt for machines that can cut soft to hard rock up to 150 mpa. These facts coupled with reliability and low operational costs are driving the demand for our equipment. Atlas Copco has more than 140 boomers working across India and Bhutan in hydropower, road and railway projects that necessitate tunnelling. Sen shares that Atlas Copco drill rigs helped create the 23 km-long, 6.8-m finished diameter, 50-sq-m modified horseshoe-shaped, concrete-lined headrace tunnel (HRT) carrying the intake water to the turbines of the Tata hydro scheme in Bhutan. This HRT was excavated at 7.5-m diameter under a minimum rock cover of 60 m and a maximum of nearly 1 km. Computer-driven equipment The range of high-tech tunnelling equipment on offer also includes computer-controlled machines proven to deliver cost efficiencies to the process. Speaking about how Atlas Copco's computer-based control systems facilitate the construction of tunnels, Sen says, Our high-precision tunnelling concept allows raw data such as rock hardness, zones and other relevant rock mass characteristics to be continuously picked up by the drill rig and translated, in real-time, into instructions to fine-tune the tunnelling process to improve safety, efficiency and economy. It delivers cost efficiencies by enabling the rig to be navigated in no more than five minutes (compared to the 10-30 minutes for manual methods) into precisely the right position, with accuracy levels better than 1 cm compared to the usual 10 cm. More precise navigation and appropriate drill plan handling helps to reduce under-break and over-break costs in terms of concrete and man hours. Contractors are hugely benefiting from the widening range of tunnelling equipment. According to Satish Suneja, Project Manager, Alpine-Samsung-HCC JV, Design and Construct contractor for the Airport Express Line, such machines offer useful features that help speed up activities. We used two EPB TBM of a Herrrenknecht-make equipped with 32 cutters to help get through the mixed soil conditions to bore a 2.2-km stretch of tunnel for package C1 of the Airport Express Line project, he reveals. The remaining 1.1-km stretch and two large stations modelled like city airport terminals were constructed using the cut-and-cover method. For package C6, comprising a 2.6 km stretch, we applied the New Austrian Tunnelling Method (NATM) using Atlas Copco computerised boomers (L2C), tele-handlers of Merlo make and fully articulated Volvo haulers. There was no way we could have completed the job in the given circumstances and timeframe (nearly one year) without using these machines. Comparing the two methods used for the C1 section of the express line, Anuj Dayal, PRO, Delhi Metro Rail Corporation, shares, TBM tunnelling was much faster than the cut-and-cover method, especially in busy areas and where the alignment was very deep, that is, the Connaught Place area and on the New Delhi Railway Station road. Suneja also points out that the economics of using expensive high-tech tunnelling equipment kicks in only when long stretches of tunnels are constructed. You don't break even in shorter stretches, but being involved in the sector for the long haul, we hope to utilise our investment in equipment for future projects, he adds. High-tech equipment is not only useful from the point of view of enhancing productivity. Tony Simmonds, Plant Manager, Leighton Contractors India, explains how it also helps to give more flexibility with manpower, especially in areas where skill shortages are present. We use highly computerised top-of-the-line equipment incorporating the most recent innovations, he says. Not only does automated and semi-automated equipment help increase productivity, but it is also easier to teach operators using high-tech equipment wherein you need to control a minimal number of input functions rather than having to take total control of a machine and trying to make it perform to its optimum. Computerised machines also provide real-time accurate operational data, and long-term cost savings, and the software they use tracks many variables in an operation. This data helps estimate ground conditions and thus, has huge potential to save time and costs. Contractorspeak Leading global contractors are looking at establishing a long-term presence in the country. We foresee many opportunities to construct tunnels in India, especially looking at the dynamics of the transportation and hydro project sectors, says Simmonds. Leighton has been awarded a $500 million contract to construct the Chenani-Nashri Tunnel in Jammu & Kashmir. This 9 km, two-lane (13.3 m diameter) main tunnel along with a parallel escape tunnel (5 m diameter) in the lower Himalayan mountain range will help link the northern state to the rest of India. The tunnel, located at an elevation of 1,200 m, will be constructed using the NATM of sequential excavation and support. When it is completed, the tunnel and its approach roads will provide a 10 km alternative all-weather route for 41 km of the existing NH1A, which passes through steep mountainous terrain and has significant geometrical, weather and safety issues. Do global contractors engaged in the tunnel construction sector in India feel the lack of any equipment? According to Simmonds, There is a lot of quality equipment available in the current market scenario, but there are major gaps as far as specialised tunnelling equipment such as tunnelling jumbo drills, road headers, and TBMs is concerned. Leading equipment companies like Robbins, Sandvik and Atlas Copco have representation in the country but the long waiting time following an order for new tunnelling equipment poses a challenge. Having said that, it's not as though this situation is typical only to emerging economies like India or China. Tunnelling equipment is in general very specialised and manufactured in few places in the world. At an average of 30 weeks from the factories, the lead times in India may be four weeks more than in developed nations. Thus, in turn, if contractors desire to start an awarded project without delay, they are compelled to take on a huge risk in pre-ordering such equipments. Reducing lead times Long lead times stem from almost all the tunnelling equipment deployed in the import country. Besides, unlike other sectors of the construction industry where products are bought readymade, TBMs are successful only when they are purpose-built for specific projects. Factors such as tunnel diameter, lining design, geology, groundwater levels and groundcover must be taken into account prior to designing a tailor-made machine to exactly suit the application, says Chengalath. This entails a waiting period of about eight to 12 months, from the date an order for a brand new TBM is placed to the time of starting work on a project. This isn't typical of India or because the equipment is imported; it's more or less the same anywhere else in the world; however, the OFTA (on-site first-time assembly) process and local value-added manufacturing can greatly improve on these start-up times. In order to reduce waiting time, Robbins has adopted OFTA for its machines imported in knocked-down condition. This means machines are not assembled and tested in factories as that would consume more time, adds Chengalath. Modular assemblies are produced and tested in different locations worldwide and then directly shipped to jobsite locations, where they are assembled and the completed TBM directly put to work. This procedure saves about one to two months of start-up time, which in turn greatly benefits in regularising cash flow to the contractor. In future, we're also actively considering setting up a manufacturing base in India, as this will help save another four to six weeks of shipping time. Operational matters Tunnelling equipment is highly specialised and necessitates a thorough understanding of different technologies that are effective for different kinds of rock or ground conditions. According to Chengalath, Projects in the hydro and irrigation sectors mostly necessitate hard rock technology, while most urban projects need soft ground technology. For some projects, it also helps if a vendor has the capability to design hybrid machines for special applications and difficult ground conditions. As expertise is critical to successfully using sophisticated equipment like TBMs, providers are necessitated to maintain their own operational and service staff. At present, Robbins has a team of over 250 people in India, where the company has 100 km of tunnels under construction, second only to China. No other country has as much potential for TBMs at the present time and in the near future, he adds. Leading contractors are making use of these services by contracting out tunnelling construction to the specialists. For instance, Hindustan Construction Company (HCC) Ltd has contracted out tunnelling activities for a water project at Veligonda in Andhra Pradesh to Robbins, the supplier for the TBM, who is also responsible for its operation and maintenance. For its Kishanganga hydroelectric project, similar responsibility has been given to SELI. Both these sites mandate the use of TBMs for boring tunnels of about 7-10 m diameter. Tunnelling is a highly specialised aspect of construction, says Shankar Srivastava, Vice-President - Equipment, HCC Ltd. Larger TBMs cost around $40 million and can't be used without the right skill sets. Contracting out such work to experts who have decades of experience behind them ensures no compromise in productivity or quality of outcome. You need to apply the right expertise at the right time and at the right place. Still, HCC is operating a Wirth TBM itself, for its Maroshi-Ruparel water supply tunnel project. This Mumbai-based project consists of the construction of a 12.24-km-long tunnel with 3.60-m diameter in three phases: Maroshi to Vakola (5.83 km), Vakola to Mahim (4.55 km) and Mahim to Ruparel College (1.86 km). Sain adds, For this project, HCC also used a Sandvik probe drill machine as a guide for the TBM to operate without eventualities. The Sandvik probe drill gives the contractor an idea of what lies ahead in the unexcavated tunnel, thereby allowing HCC to mitigate risks. Not all tunnelling equipment is being operated by vendors. Atlas Copco has already received orders for 20 computerised E-Series boomers in India, for which the delivery period varies between 25 and 35 weeks from the date of receiving a confirmed order depending on the size of the machine. Of these, 13 rigs will be deployed for the expansion of the Jammu-Srinagar highway by Navayuga Engineering Co and Leighton Contractors (India) Pvt Ltd. Six machines will be deployed in Punatsangchhu II HEP in Bhutan and one machine for the Rohtang Tunnel project by Afcons Strabag JV. The boomers are operated by the respective clients. However, Atlas Copco offers training not only to operators but also to the maintenance crew, at site and in a full-fledged training centre at Pune where regular courses on operation and maintenance are conducted. We also conduct tailor-made programmes for our clients if requested, adds Sen. Atlas Copco India has invested in a simulator to impart training to operators for E-Series boomers. With the right training and investments by leading tunnelling specialists, there's no doubt that India's underground construction will look up in days to come. To share your views on this article, write in at feedback@ASAPPmedia.com
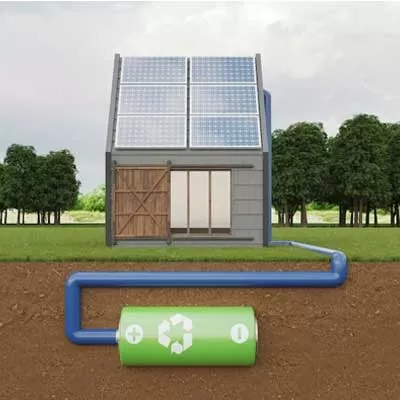
NTPC Floats Tender for 1,000 MWh Battery Storage in Kerala
NTPC Green Energy Limited has issued an engineering, procurement, and construction (EPC) tender for a 250 MW/1,000 MWh battery energy storage system (BESS) at its Kayamkulam facility in Kerala. The project is split into two segments: Block-1 includes 125 MW/500 MWh connected to the existing 33 kV solar pooling switchgear, while Block-2 comprises 125 MW/500 MWh to be integrated with the 220 kV switchyard.As per the tender guidelines, the scope includes complete design, engineering, packaging, transportation, unloading, construction, erection, testing, and commissioning of the BESS on a turnkey ..
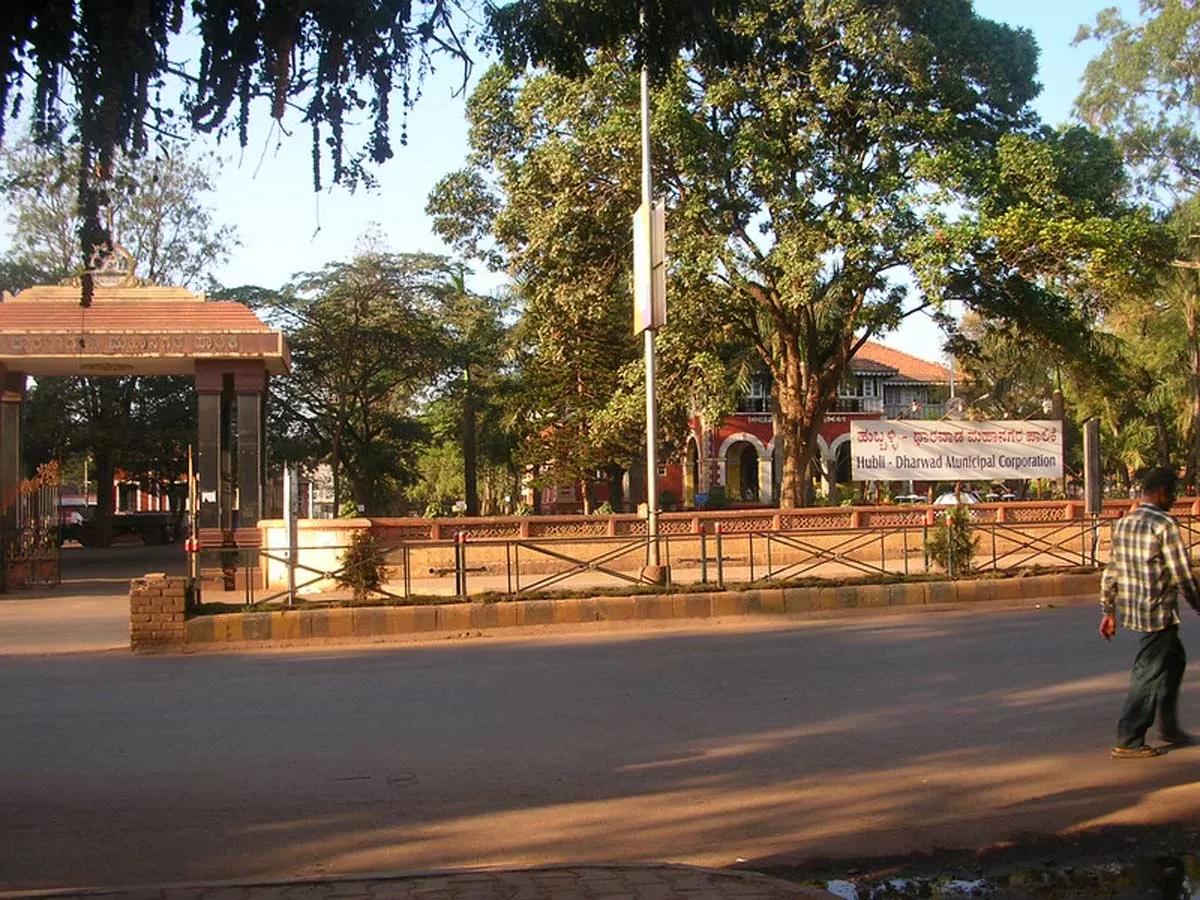
Plastic Waste Used to Build Roads in Hubballi-Dharwad
In a notable step towards sustainability, the Hubballi-Dharwad Municipal Corporation (HDMC) has shown that single-use plastic waste—often considered a severe environmental threat—can be converted into a valuable resource for infrastructure development.Under an innovative pilot project, plastic waste is being used in the construction of asphalt roads in Lingarajnagar, Hubballi. By merging waste management with infrastructure planning, HDMC is transforming discarded plastic into a sustainable solution that benefits both the urban landscape and the environment.The process begins with daily ho..
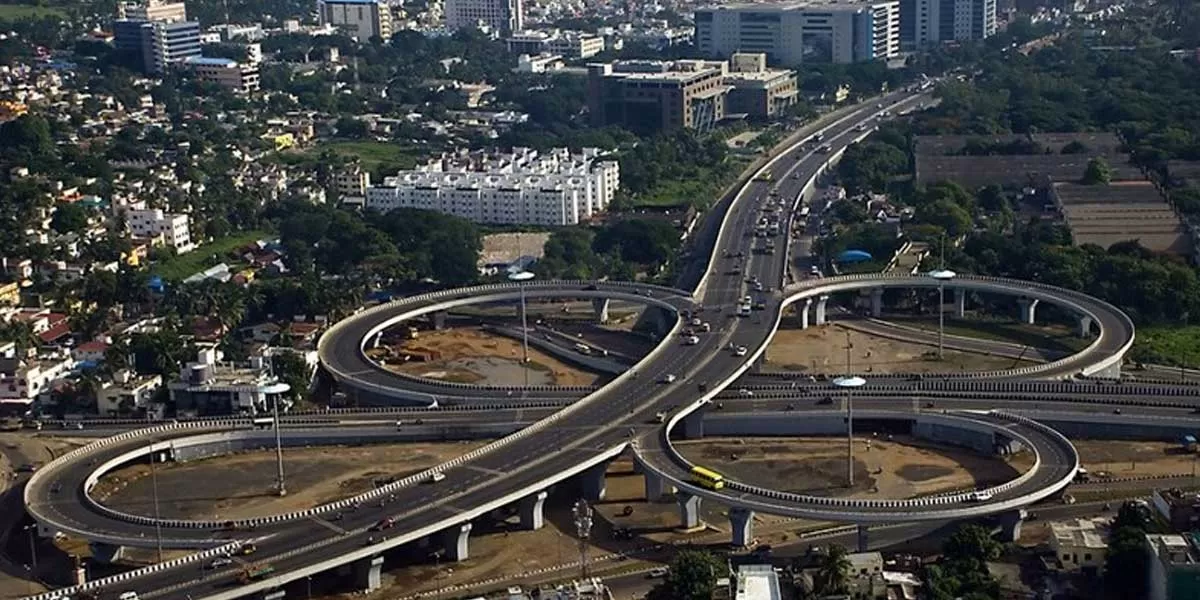
Chennai Peripheral Ring Road Nears 2025 Completion
Spanning 132.87 kilometres, the Chennai Peripheral Ring Road (CPRR) is set to transform regional connectivity across Tamil Nadu. The six-lane, access-controlled expressway will link Ennore Port to Mahabalipuram, joining several key national highways. With an estimated cost of Rs 123 billion, the project is scheduled for completion by the end of 2025. The Tamil Nadu Road Development Company (TNRDC) is overseeing its implementation.The CPRR will pass through seven major urban areas including Singaperumalkoil, Sriperumbudur, Tiruvallur, Tamaraipakkam, Periyapalayam, Puduvoyal, and Kattupalli. Onc..
Latest Updates
Advertisement
Recommended for you
Advertisement
Subscribe to Our Newsletter
Get daily newsletters around different themes from Construction world.
Advertisement
Advertisement
Advertisement
subscribe to the newsletter
Don't miss out on valuable insights and opportunities
to connect with like minded professionals