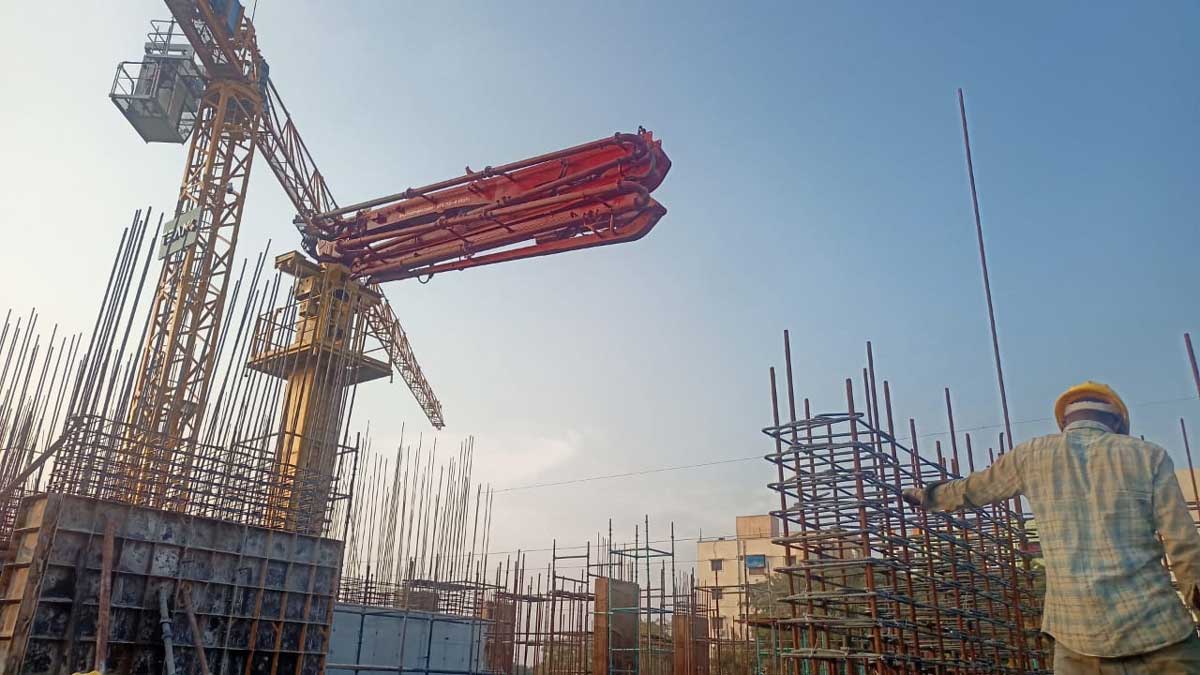
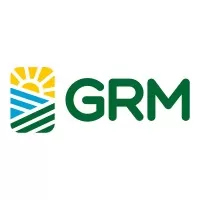
GRM Overseas Reports Q1 FY26 Results; Strengthens Global & Domestic Presence
GRM Overseas has announced its unaudited financial results for the quarter ended 30 June 2025. The company reported a positive performance in terms of margins and profitability, despite topline pressures from global geopolitical challenges.Atul Garg, Managing Director, said:"We have maintained healthy margins and profitability while navigating short-term headwinds. Our focus remains on expanding our product portfolio, enhancing brand visibility, and deepening our distribution network. Internationally, we continue to hold a strong position in the Basmati rice export market, particularly in the ..
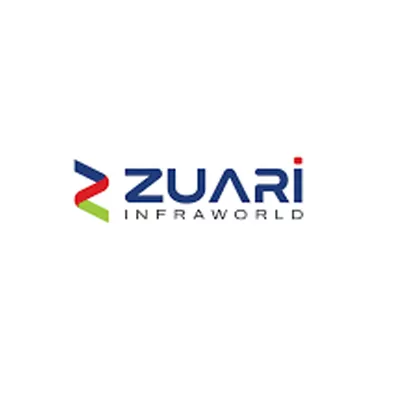
Zuari Industries Posts Q1 FY26 Revenue Growth; PAT Turns Positive
Zuari Industries has announced its audited financial results for the quarter ended 30 June 2025.On a standalone basis, the company reported Revenue from Operations of Rs 2.10 billion and Operating EBITDA of Rs 220.4 million. Standalone Profit Before Tax (PBT), before exceptional items, stood at Rs 90 million.On a consolidated basis, Revenue rose 10.5 per cent year-on-year to Rs 2.67 billion, while Profit After Tax (PAT) stood at Rs 50 million compared to a loss of Rs 330.6 million in Q1 FY25.Segment HighlightsSugar, Power & Ethanol: Operations were impacted by an early mill closure due to ..
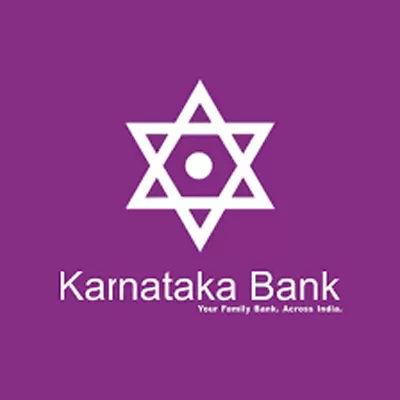
Karnataka Bank Reports Q1 FY26 Net Profit of Rs 2.92 Bn
Karnataka Bank has announced a net profit of Rs 2.92 billion for the first quarter of FY26, compared to Rs 4 billion in Q1 FY25. The results were approved at the Board of Directors meeting held on 13 August 2025 at the Bank’s headquarters in Mangaluru.Asset Quality & Capital AdequacyGross NPA: 3.46 per cent, improved from 3.54 per cent in Q1 FY25.Net NPA: 1.44 per cent, down from 1.66 per cent in Q1 FY25.Capital Adequacy Ratio (CAR): 20.46 per cent, up from 17.64 per cent in Q1 FY25.Announcing the results, Raghavendra S Bhat, Managing Director & CEO, said:"The Bank has registered a m..