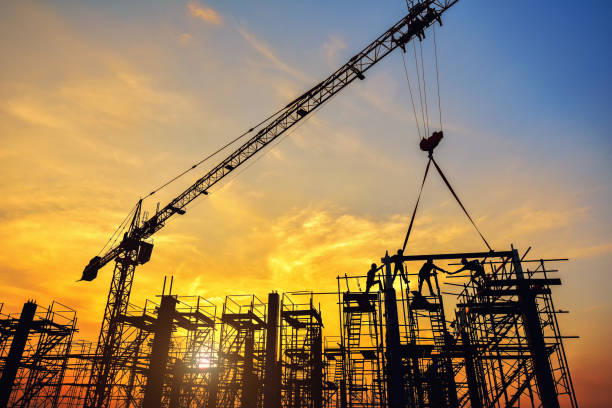
Buildings can now be developed within a year using new tech
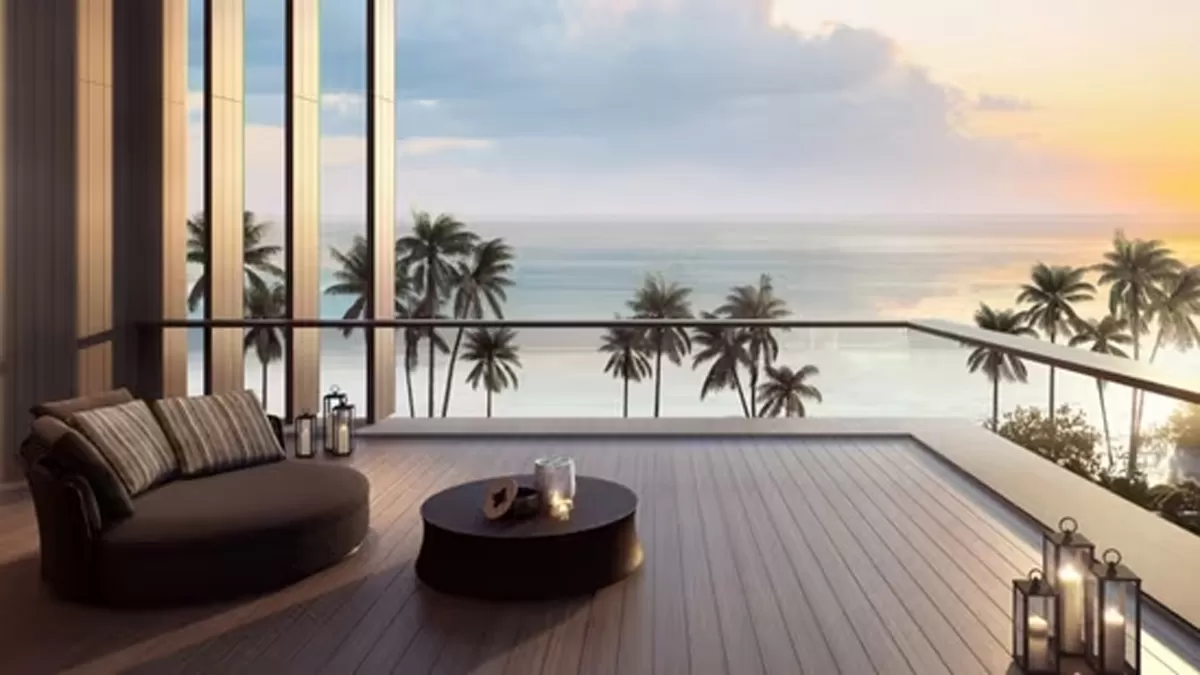
Heena Lalwani Buys Rs 1.13 Billion Juhu Apartment
Heena Lalwani, promoter of Aatman Innovations Private Limited, has purchased a luxury apartment worth Rs 1.13 billion in Mumbai’s upscale Juhu locality, according to property registration documents accessed by Zapkey.com.The 9,862 sq ft apartment, located on the 10th floor of Lodha Developers’ Avalon Tower, was acquired at Rs 115,000 per sq ft and comes with five car parking spaces. The deal, registered on 18 August 2025, also included the payment of Rs 68 million in stamp duty and a Rs 30,000 registration fee.Lodha Developers did not respond to queries regarding the transaction, while the..

Godrej Buys KPHB Land for Rs 7 Billion in E-Auction
An acre of prime land in Kukatpally Housing Board (KPHB), Hyderabad, was auctioned for Rs 7 billion, with the Telangana Housing Board generating Rs 5.47 billion from the sale of 7.8 acres through e-auction on 20 August 2025.The auction notification was issued last month, attracting bids from Godrej Properties, Aurobindo Realty, Prestige Estates, and Ashoka Builders, according to Board vice-chairman V.P. Gautham. With an offset price of Rs 4 billion per acre, the three-hour auction saw 46 bid increases, before Godrej Properties acquired the land.Revenue generated from the auction will be utilis..
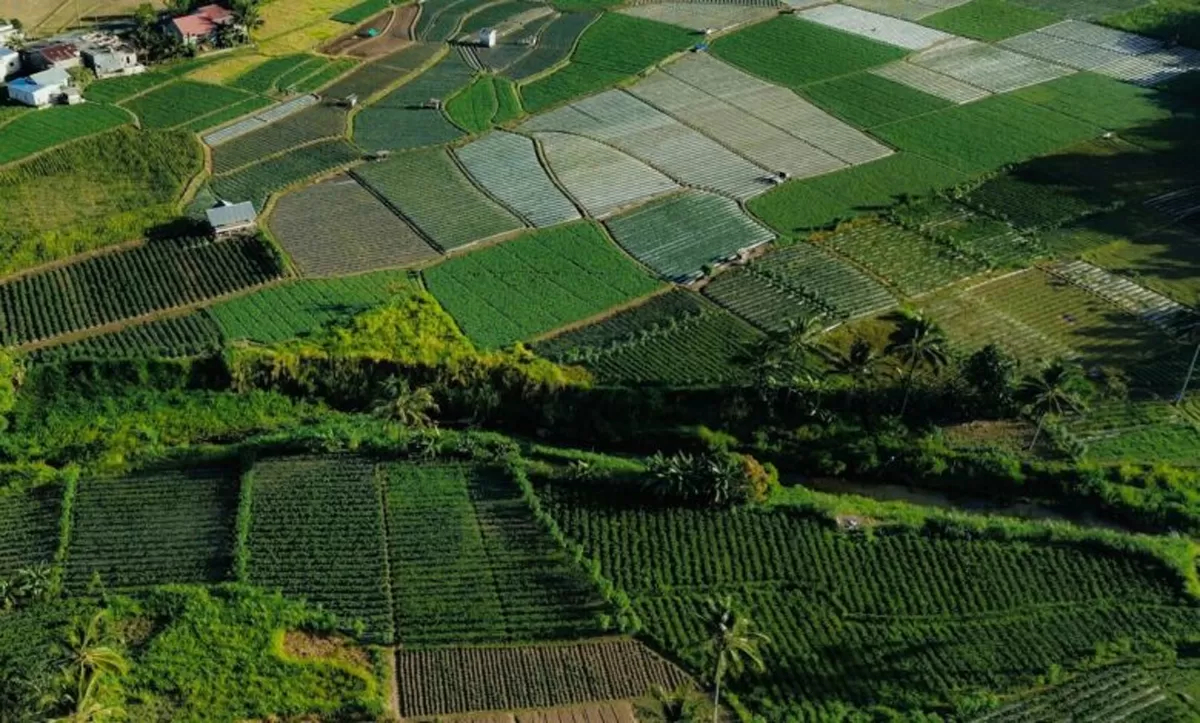
HMDA to Auction 93 Prime Plots in September
The Hyderabad Metropolitan Development Authority (HMDA) is preparing to conduct a three-day auction of prime open plots across Hyderabad, Rangareddy, and Medchal-Malkajgiri districts this September.According to official reports, the e-auction will take place on 17, 18, and 19 September, offering 93 plots. Of these, 70 are located in the Bachupally HMDA layout, with the remainder spread across Turkayamjal, Kokapet, Poppalguda, Chandanagar, Bairagiguda, Gandi Maisamma, Suraram, Medipally, and Bachupally village.The highest upset price has been fixed at Rs 175,000 per square yard for a land parce..