
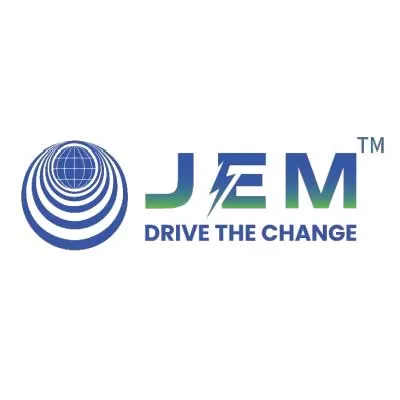
Jupiter Opens First EV Showroom in Hyderabad
Jupiter Electric Mobility Pvt Ltd (JEM), the electric commercial vehicle arm of Jupiter Wagons Ltd, has inaugurated its first showroom in New Bowenpally, Secunderabad, Hyderabad. The launch also marks the introduction of its 1.05-tonne four-wheeler electric light commercial vehicle (eLCV), JEM TEZ, to Telangana’s growing logistics and intra-city freight market. This expansion underscores JEM’s commitment to delivering purpose-built sustainable mobility solutions and accelerating the electrification of India’s logistics sector.The new showroom, operated by Arven Motors Pvt Ltd, offers cus..
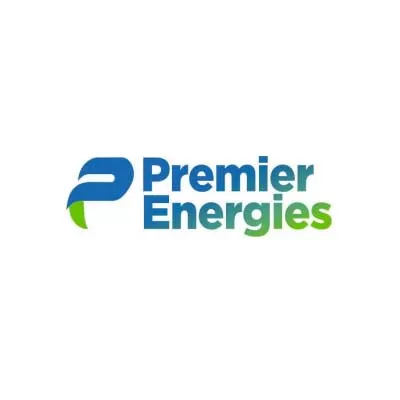
Premier Energies Launches 620W DCR Solar Modules in India
Premier Energies Limited, one of India’s largest integrated solar manufacturers, has launched its next-generation 620W DCR solar modules using G12R TOPCon technology, now among the most powerful large-format panels available in the country.The new modules, built with Tunnel Oxide Passivated Contact (TOPCon) architecture, deliver superior power density, improved temperature coefficients, and enhanced low-light performance. The rectangular G12R N-type cell design enables higher string power and balance-of-system optimisation, making the panels suitable for utility-scale projects as well as com..
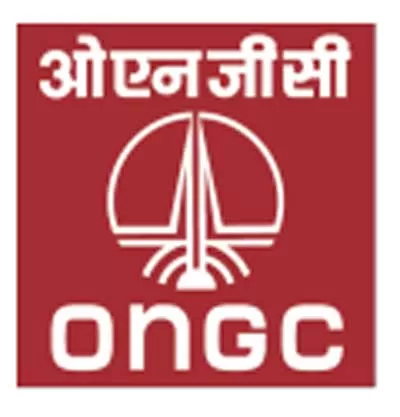
ONGC Starts Gas Sales from Rajasthan Chinnewala Tibba Block
Oil and Natural Gas Corporation Limited (ONGC) has commenced natural gas sales from the Discovered Small Field (DSF-II) Block RJ/ONDSF/Chinnewala/2018, marking the successful monetisation of the Chinnewala Tibba field in the Rajasthan Kutch Onland Exploratory Asset (RKOEA). Gas sales officially began on 25 August 2025.This development highlights ONGC’s commitment to boosting domestic energy production and strengthening India’s energy security under the guidance of the Ministry of Petroleum and Natural Gas. Located in western Rajasthan, close to the Indo-Pakistan border, the Chinnewala Tibb..