Progress on Structural Technologies for Affordable Housing
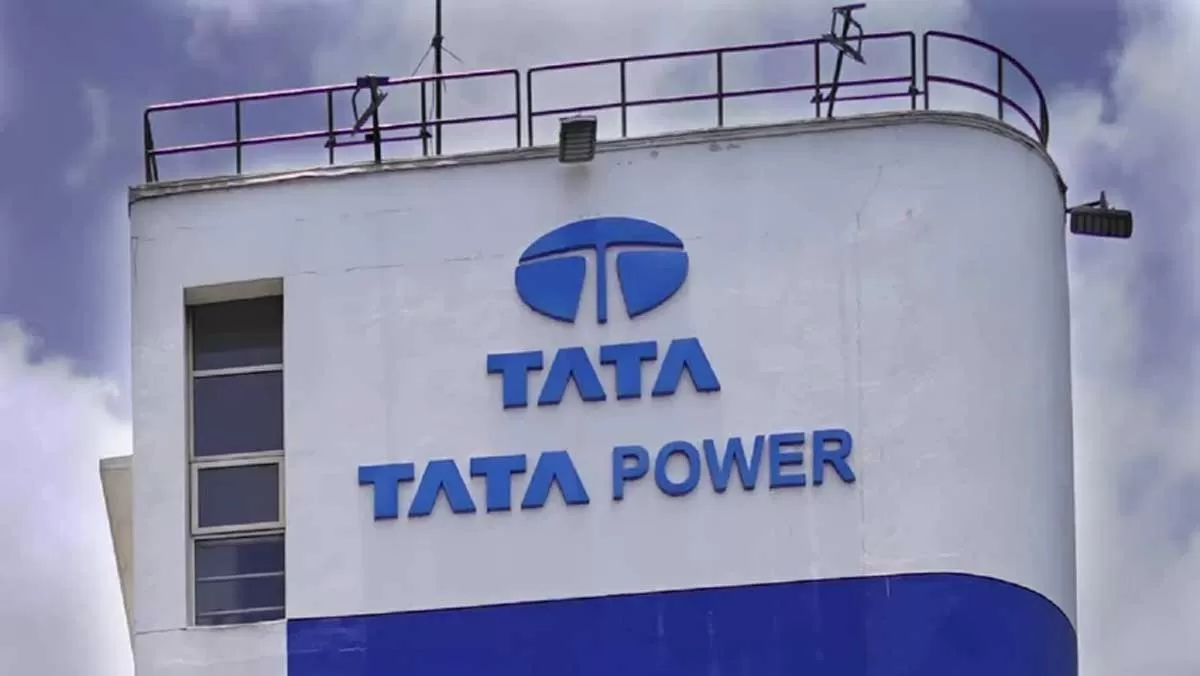
Tata Power, Suzlon Ink Rs 60 Billion Wind Energy Deal in Andhra
Tata Power has signed an agreement with Suzlon Energy to develop, construct, and supply 700 megawatt (MW) wind turbines in Andhra Pradesh. The Rs 60 billion project forms part of a 7 gigawatt (GW) renewable energy plan announced by Tata Power Renewable Energy (TPREL) and the state government in March 2025.This marks the first wind energy project in the state since 2019. The larger 7 GW programme, covering solar, wind, and hybrid projects with or without storage, is expected to attract investments of around Rs 490 billion, making it one of the state’s largest clean energy commitments.The turb..
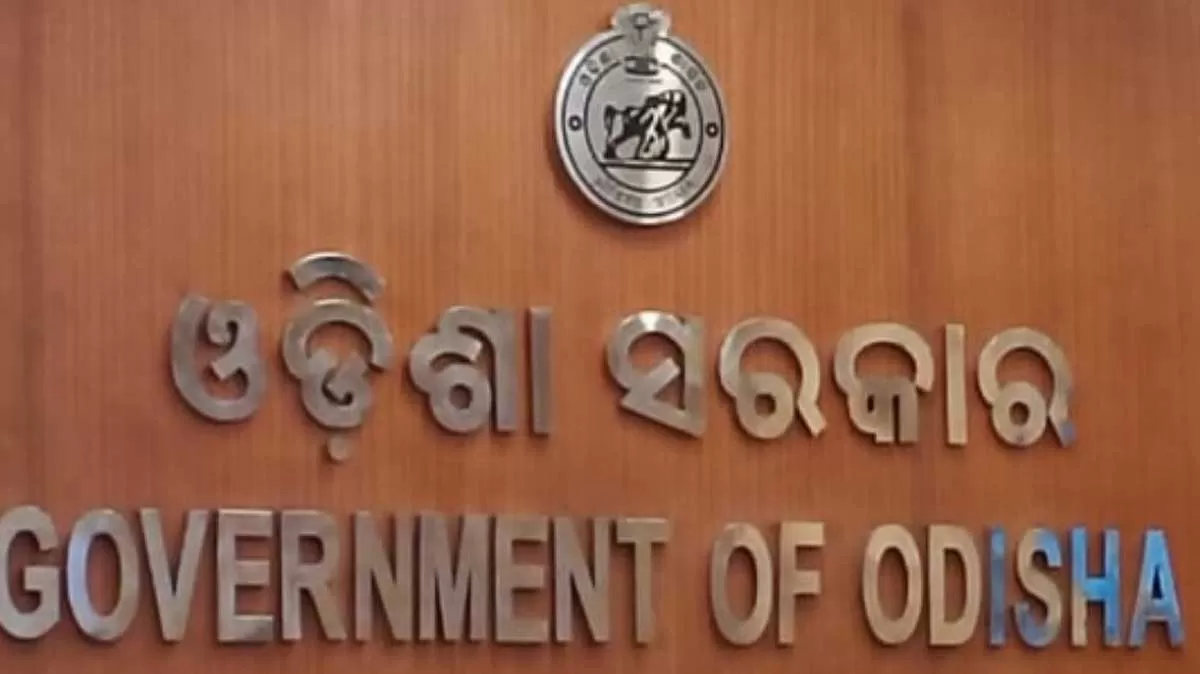
Odisha Approves Rs 12.6 Billion For 32 New Bridges
Odisha is set for a major infrastructure boost with the approval of 32 new bridges under the Setu Bandhan Yojana for FY 2025–26. The project, valued at Rs 12.6 billion, is aimed at improving road connectivity across ten districts, enhancing mobility and driving local development.The bridges will be constructed in Bolangir, Subarnapur, Nayagarh, Sambalpur, Malkangiri, Bargarh, Koraput, Jagatsinghpur, Cuttack, and Puri. Many of these areas are rural or located in difficult terrains, where improved accessibility will greatly benefit the transportation of goods and public mobility.Setu Bandhan Y..
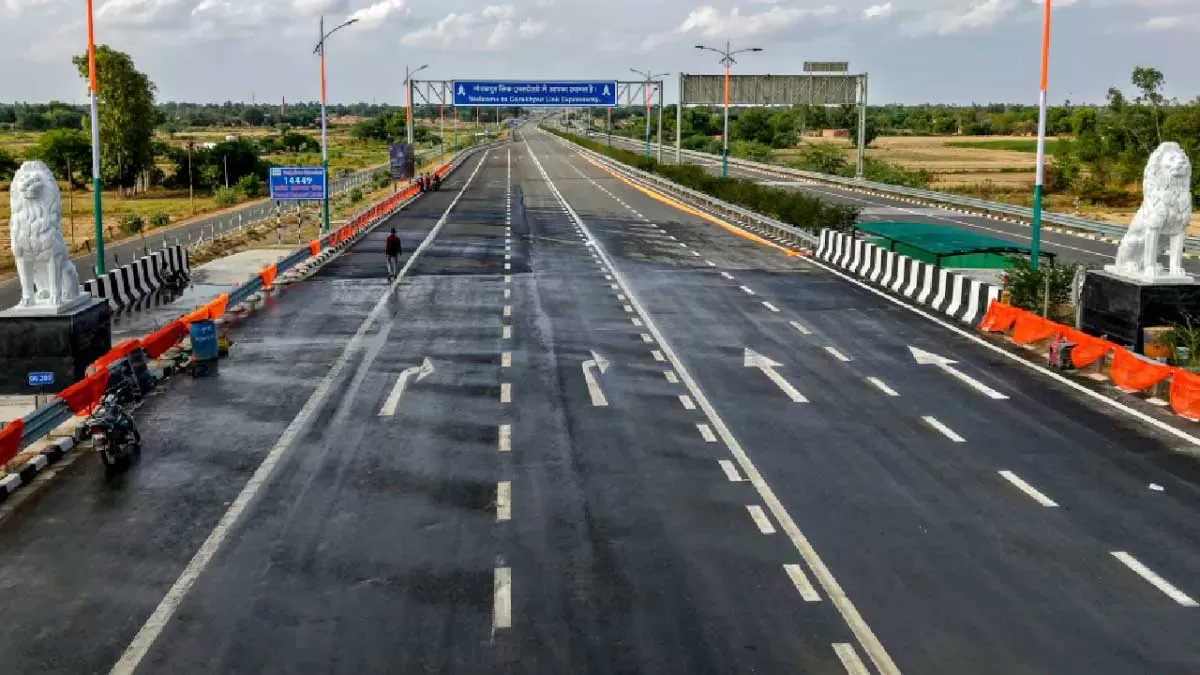
UP Plans Rs 350 Billion Gorakhpur–Shamli Expressway
Uttar Pradesh is preparing to build its largest expressway, a 700-km six-lane project that will surpass the 570-km Ganga Expressway from Meerut to Prayagraj. Designed as a greenfield project, the Gorakhpur–Shamli Expressway will cut travel time between eastern and western Uttar Pradesh to just six hours, transforming regional connectivity.The expressway will pass through 22 districts and 37 tehsils, bringing faster travel and significant economic benefits, including higher land values for farmers and employment opportunities during and after construction. A drone survey to map the route is e..