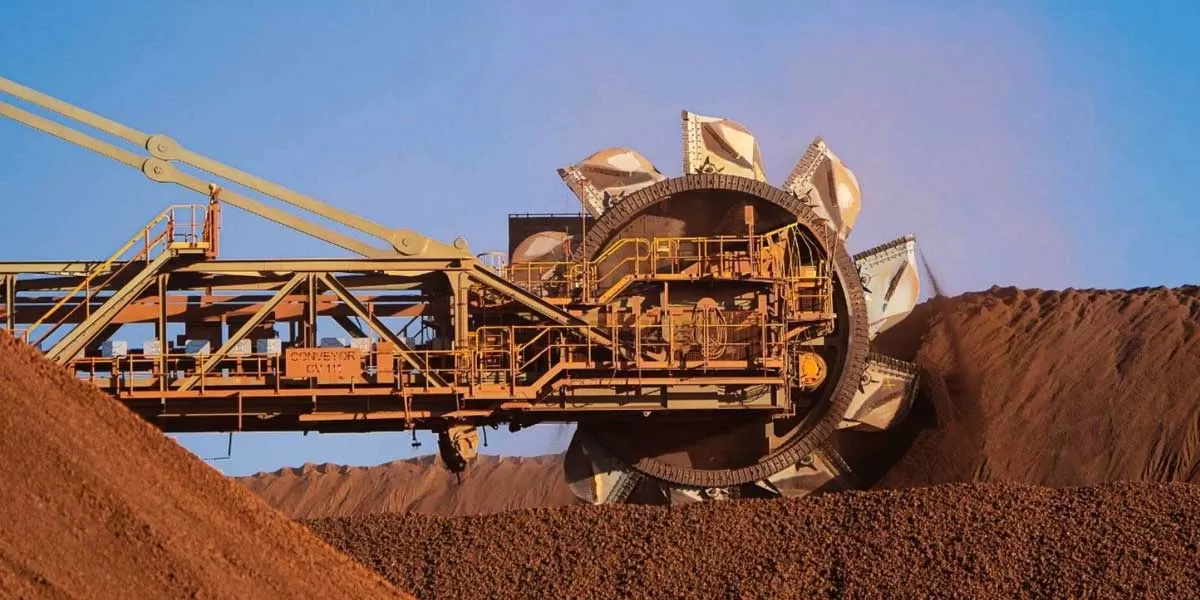
Mining Remanufacturing Market Rises on Precision & Sustainability
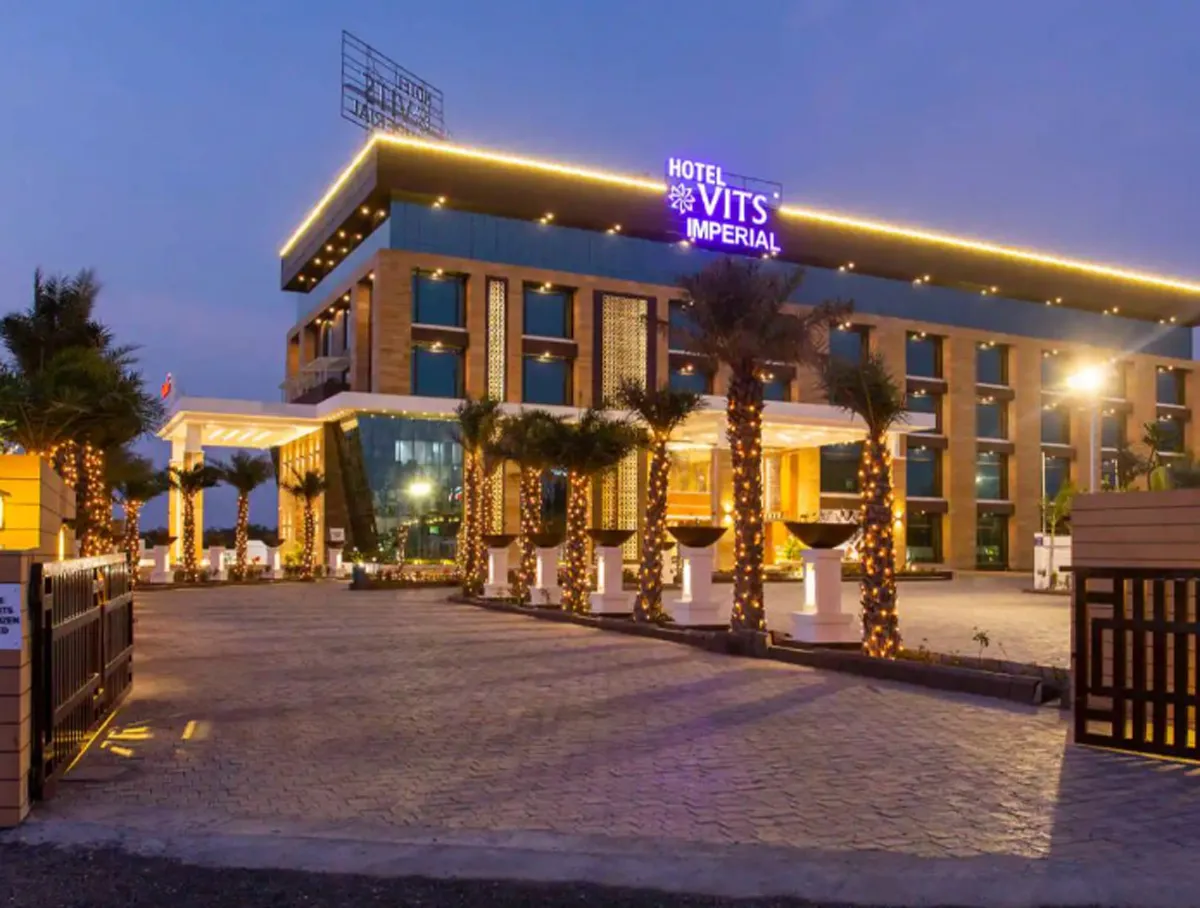
Vitizen Hotels Signs Deal at Manyata Tech Park
Vikram Kamats Hospitality, as part of its ongoing expansion in key metropolitan markets, announced that its material subsidiary, Vitizen Hotels, has signed a long-term lease agreement for a 45-key hotel property at Manyata Tech Park, Bengaluru.Strategically located in the city’s prominent IT hub, the property is well-positioned to serve corporate travelers, business professionals, and long-stay guests. The addition aligns with the company’s asset-light growth model, leveraging long-term leases to expand its footprint in high-demand urban markets.The hotel is expected to strengthen the comp..
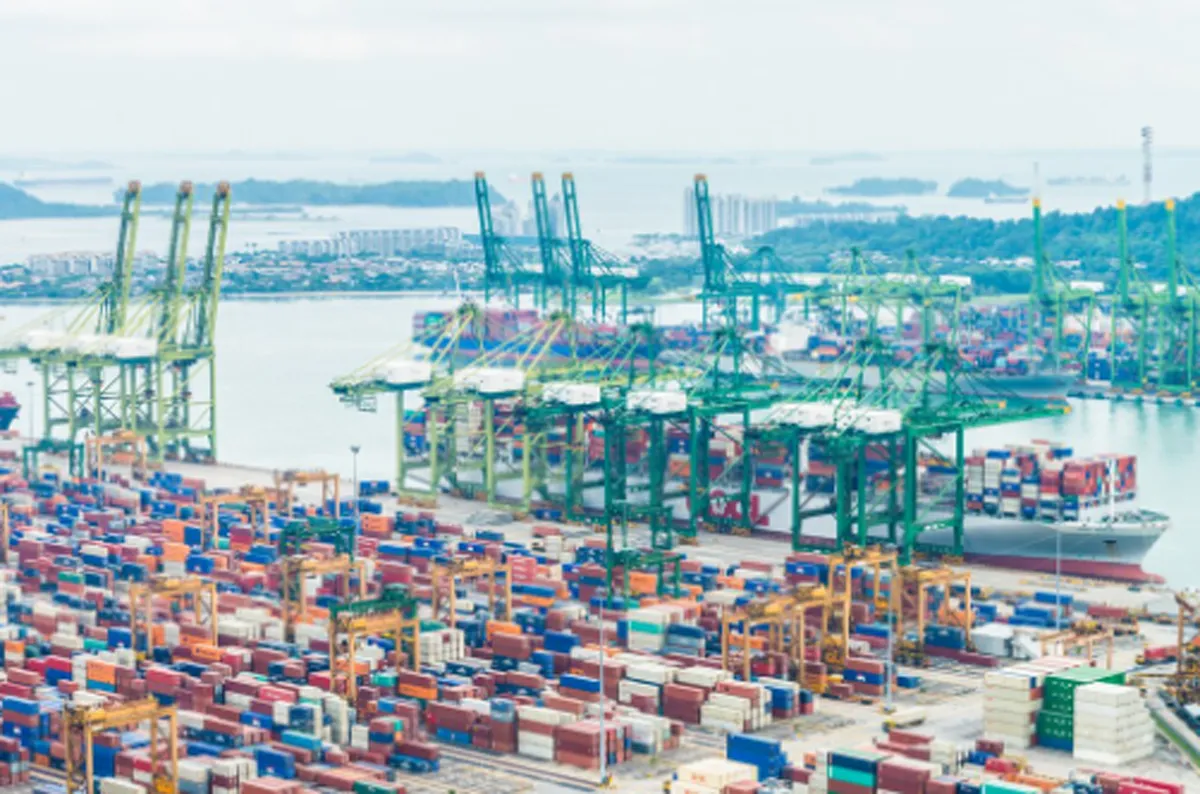
CONCOR Signs MoU with BPIPL to Operate Container Terminal at Bhavnagar Port
Container Corporation of India (CONCOR) has signed a Memorandum of Understanding (MoU) with Bhavnagar Port Infrastructure (BPIPL) on September 4, 2025, in New Delhi to operate and maintain the upcoming container terminal at the northside of Bhavnagar Port, Gujarat.BPIPL had earlier entered into an agreement with the Gujarat Maritime Board (GMB) in September 2024 for the port’s development. Under this arrangement, 235 hectares of land has been leased to BPIPL for 30 years, with provision for expansion by an additional 250 hectares.The new terminal is expected to significantly enhance logistic..
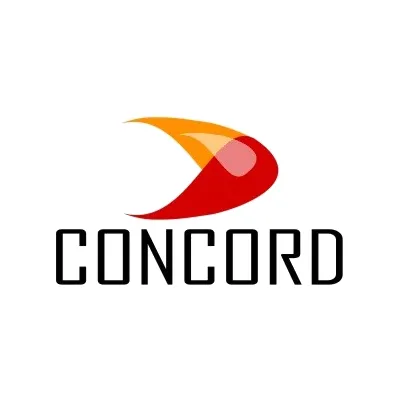
Concord Launches India’s First Indigenous Zero-Emission Rail Propulsion
Concord Control Systems (CCSL), a leader in embedded electronics and critical rail technologies, has announced the development of India’s first fully indigenous zero-emission propulsion system, marking a significant step toward the country’s railway electrification and net-zero goals for 2030.Powered by Lithium Iron Phosphate (LFP) batteries and featuring a DC chopper-based drive, the propulsion system eliminates idling losses common in diesel engines, offering higher efficiency, lower costs, and zero emissions.What sets this innovation apart is its completely indigenous design. Except for..