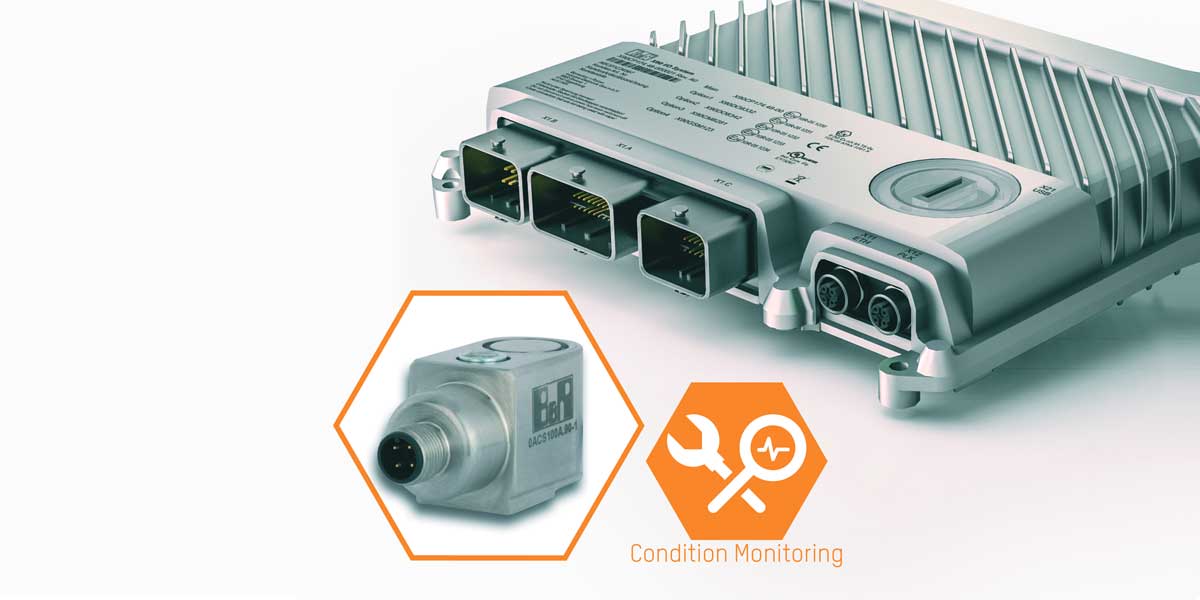
"Revolutionary Eco Vaults Provide Secure Sustainable Storage"
Read full article
CW Gold Benefits
- Weekly Industry Updates
- Industry Feature Stories
- Premium Newsletter Access
- Building Material Prices (weekly) + trends/analysis
- Best Stories from our sister publications - Indian Cement Review, Equipment India, Infrastructure Today
- Sector focused Research Reports
- Sector Wise Updates (infrastructure, cement, equipment & construction) + trend analysis
- Exclusive text & video interviews
- Digital Delivery
- Financial Data for publically listed companies + Analysis
- Preconceptual Projects in the pipeline PAN India
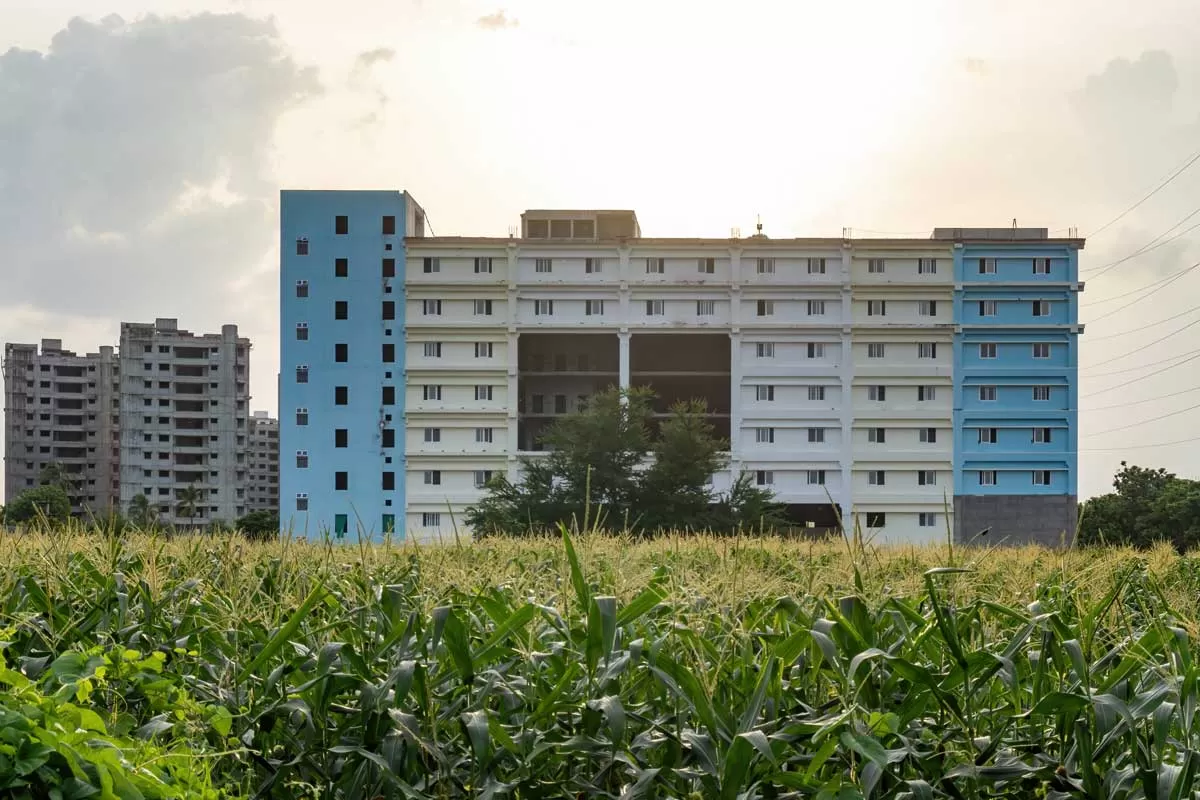
APCRDA Approves Rs 9.04 Bn to Upgrade Infrastructure in 29 Amaravati Villages
The Andhra Pradesh Capital Region Development Authority (APCRDA), chaired by Chief Minister N Chandrababu Naidu, has approved Rs 9.04 billion for addressing key infrastructure gaps in 29 villages within Amaravati’s greenfield capital area, announced Municipal Administration Minister P. Narayana at the 51st CRDA meeting.The funds will be used to upgrade critical facilities including roads, drains, drinking water supply, sewerage systems, and street lighting. A detailed assessment revealed a 30 per cent shortfall in water supply, a total absence of sewerage infrastructure, a 40 per cent defici..
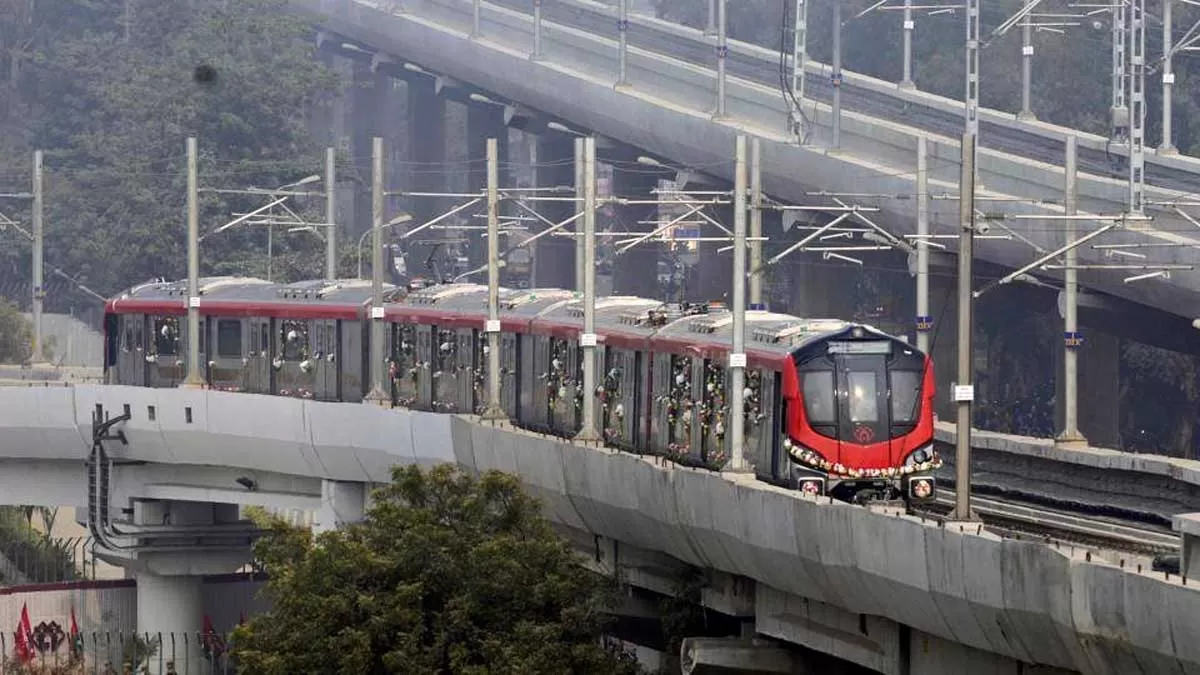
Cabinet Approves Phase-1B of Lucknow Metro Rail Project Worth Rs 58.01 Bn
The Union Cabinet, led by Prime Minister Narendra Modi, has approved Phase-1B of the Lucknow Metro Rail Project in Uttar Pradesh. This phase covers an 11.165 km corridor with 12 stations—7 underground and 5 elevated—extending the city’s metro network to 34 km upon completion.Phase-1B targets the dense, historic parts of Lucknow, enhancing connectivity across key commercial, healthcare, tourist, and culinary hubs. Important areas served include Aminabad, Yahiyaganj, Pandeyganj, Chowk, King George’s Medical University, and landmarks like Bara Imambara and Rumi Darwaza.This expansion prom..
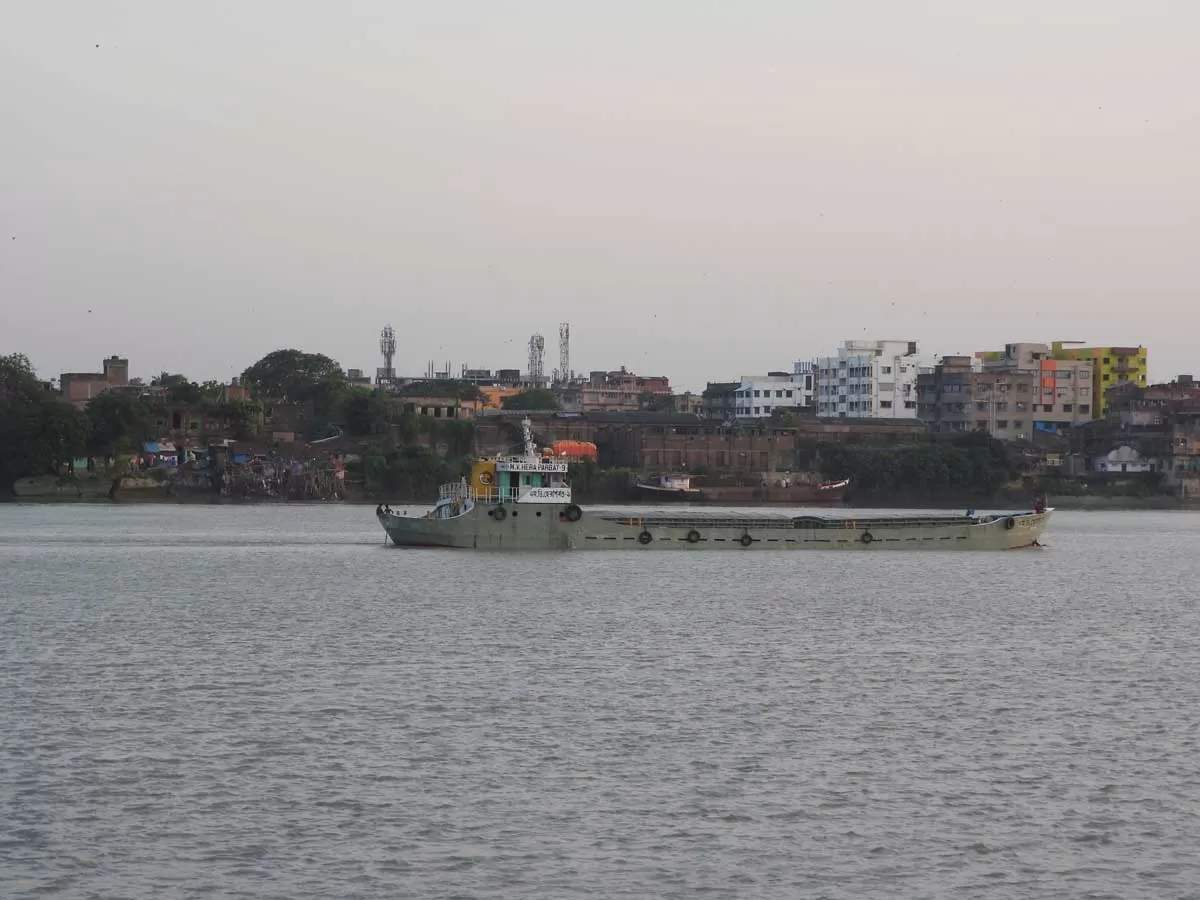
Major Upgrades Planned for Tamil Nadu’s National Waterways
Tamil Nadu is poised for significant infrastructure upgrades across its National Waterways (NWs), with a focus on developing jetties, cargo hubs, and cruise tourism circuits, according to the Ministry of Ports, Shipping and Waterways. These projects aim to promote sustainable inland water transport and boost regional economic activity.Key projects include the development of Buckingham Canal (part of NW-4), with jetties planned at the following locations:Mahabalipuram to Ediyur BridgeCooum River near Marina BeachPulicat LakeEnnore Port to ETPS, specifically for cargo operationsOther National Wa..