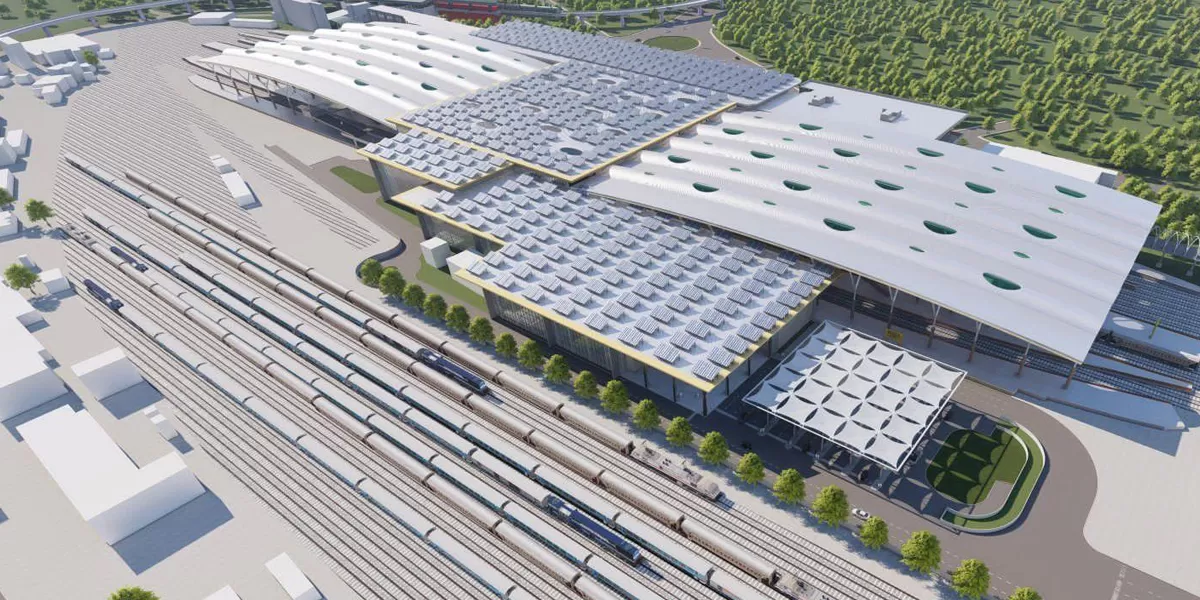
Secunderabad Station Redevelopment Moves Ahead Swiftly
Redevelopment of Secunderabad railway station is progressing rapidly, with the new Railway Protection Force (RPF) building already completed. Construction is actively underway on several key components, including the air concourse, multi-level car parking (MLCP), foot over bridges (FOBs), elevators, the north-side main building, and an electric sub-station on the south side.The RPF building, along with a temporary booking office, is among the early completed elements of the project. Work is advancing steadily on the basement construction on the southern side, foundation work, and the new foot ..
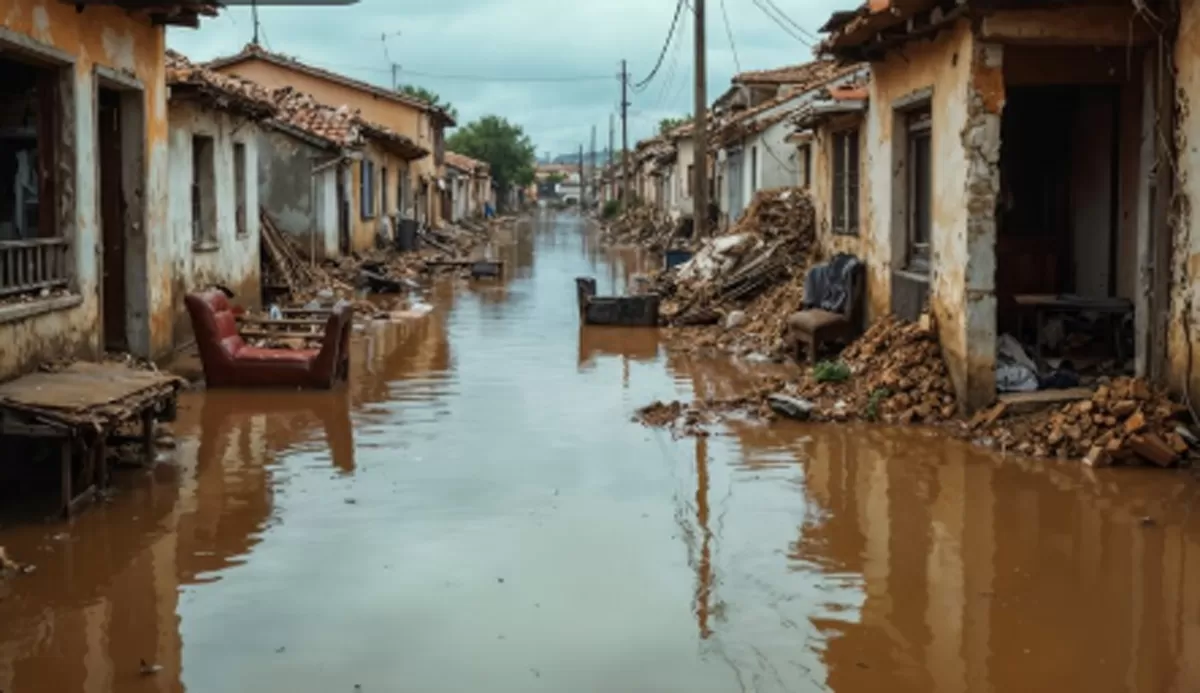
Tamil Nadu Allocates Rs 3.38 Bn for Flood Relief in Three Districts
The Tamil Nadu government has allocated Rs 3.38 billion for flood mitigation projects across Chennai, Tiruvallur, and Kancheepuram for the financial year 2025–26. The initiative, part of an integrated flood management strategy, aims to address persistent waterlogging in urban and semi-urban areas.In the southern parts of Chennai, work has begun in the suburbs with an estimated budget of Rs 27o million. A substantial portion of the total allocation—Rs 2.60 billion—has been designated for Chennai. This includes a specific flood relief project for the Ambattur Industrial Estate, which frequ..
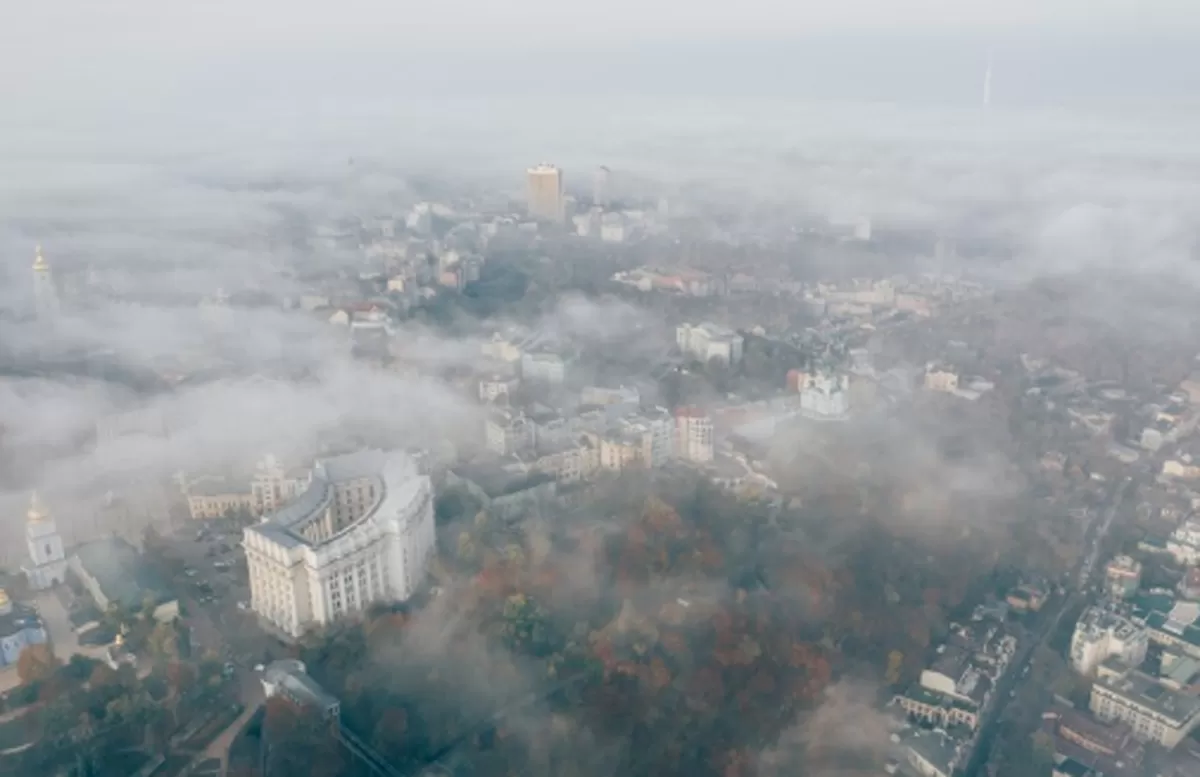
Patna Plans Green Zones to Tackle Rising Pollution Levels
Authorities have emphasised the urgent need for developing more green zones in Patna, which is increasingly becoming a heat-stressed urban area dominated by concrete structures. Expanding green spaces, such as the Tarumitra bio-reserve, is seen as a way to improve the environment and reduce temperatures.Plans under consideration include planting medicinal plants, implementing rainwater harvesting systems, constructing eco-friendly homes, and promoting solar energy usage. If implemented effectively, these measures are anticipated to help reduce both air and water pollution.In a collaborative ef..