
Delivering thousands of homes is possible only with the right technology
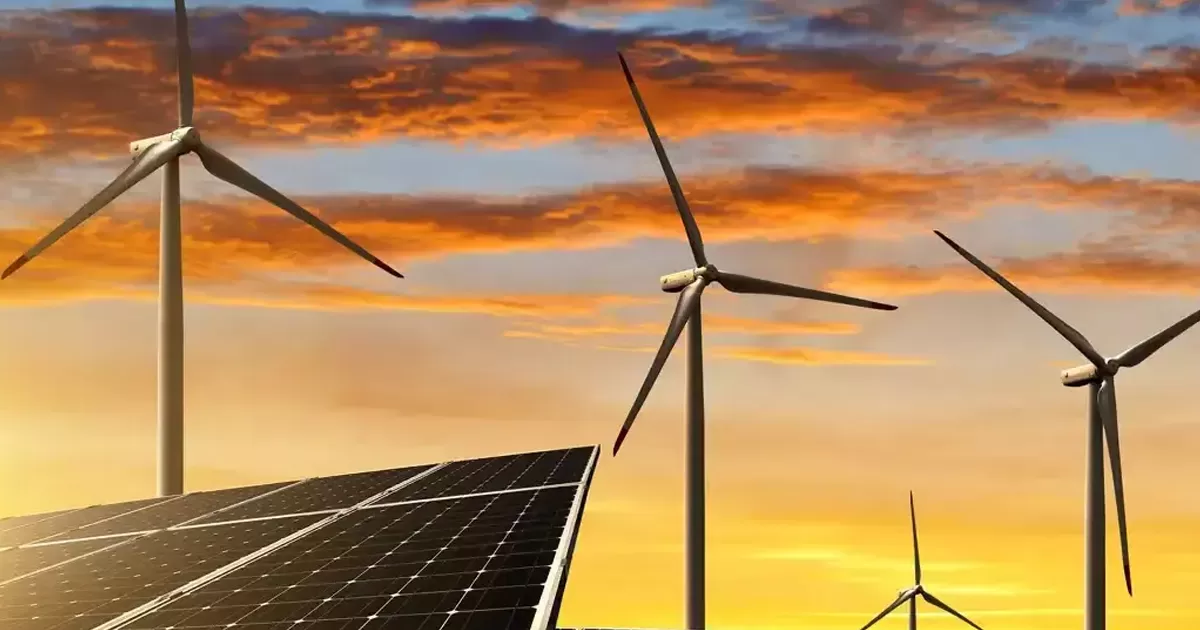
Reliable Energy Storage Vital for 24/7 Renewable Power: TKIL
Reliable, scalable, and efficient energy storage systems are essential to ensuring uninterrupted renewable energy supply, said engineering firm TKIL Industries at the India Energy Storage Week (IESW) 2025.India aims to achieve 500 GW of renewable energy capacity within the next five years.Speaking at IESW, organised by the India Energy Storage Alliance (IESA), Vivek Bhatia, Managing Director and CEO of TKIL Industries, emphasised that the country’s energy sector is experiencing a major transformation. This shift is being driven by innovations in storage technology, aimed at improving grid re..
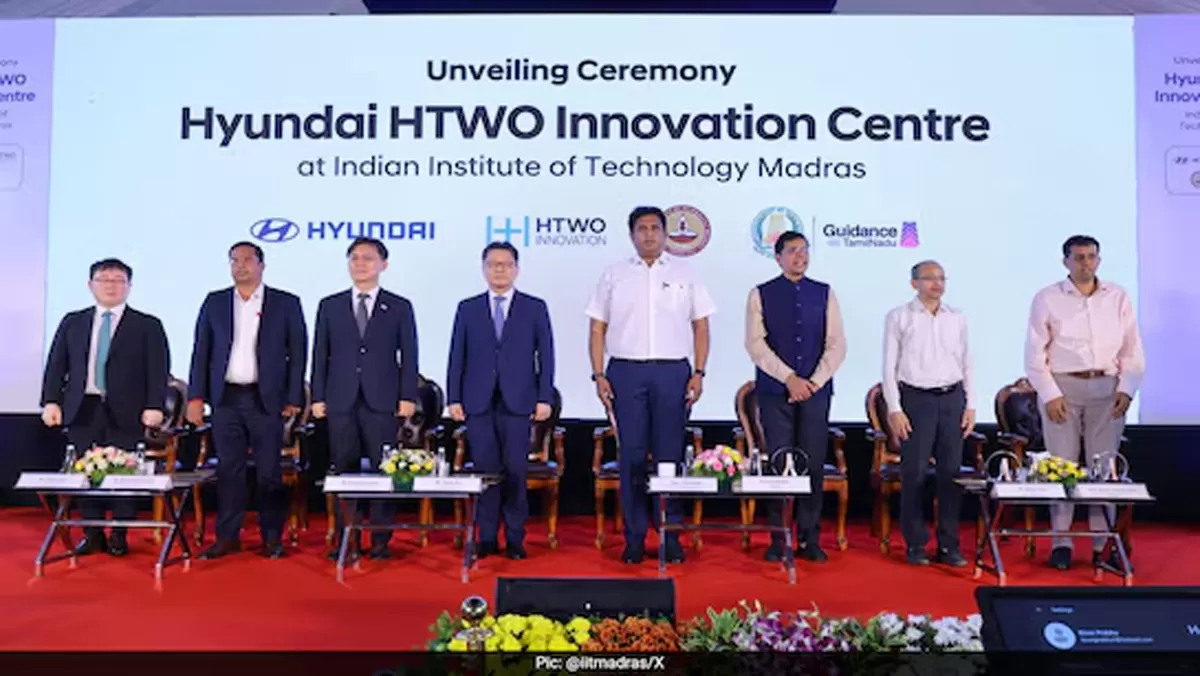
IIT Madras, Hyundai Launch £17m Hydrogen Research Centre
The Indian Institute of Technology Madras (IIT Madras) and Hyundai Motor India Ltd (HMIL) have announced the establishment of the Hyundai HTWO Innovation Centre, a cutting-edge hydrogen research facility set to begin operations by 2026.The Rs 180 crore (approx. £17 million or USD 21.5 million) project will be located at IIT Madras' Discovery Campus in Thaiyur, near Chennai. Of the total, Rs 100 crore (approx. £9.4 million) has been committed by HMIL and its philanthropic arm, Hyundai Motor India Foundation (HMIF), with support from the Government of Tamil Nadu and its investment promotion ag..
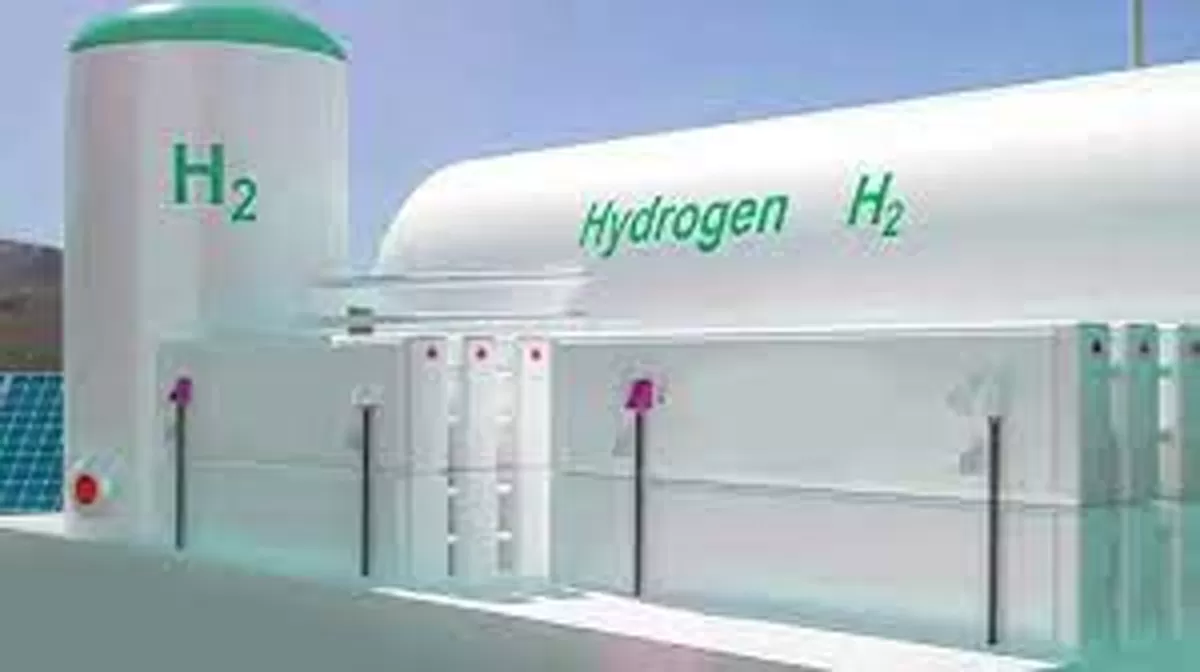
India’s Hydrogen Demand to Hit 8.8 MTPA by 2032: IESA Report
India’s hydrogen demand is projected to grow at a compound annual growth rate (CAGR) of 3 per cent, reaching 8.8 million tonnes per annum (MTPA) by 2032, according to a report released by the India Energy Storage Alliance (IESA).Unveiled on the first day of the India Energy Storage Week (IESW) 2025, the report points out a gap between ambitious project announcements and actual progress. While green hydrogen (GH₂) projects totalling 9.2 MTPA have been announced, only a limited number have reached Final Investment Decision (FID) or secured long-term domestic or international offtake agreemen..