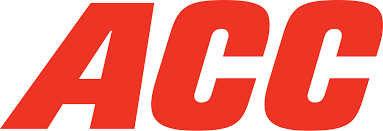
ACC promotes sustainable living with 100 Green Building Centres

Delivering metals in 24 hours with AI
India’s metal supply chain has long struggled with delays, fragmentation and lack of transparency, forcing purchase teams to chase vendors and juggle uncertain stock. Enlight Metals is tackling these inefficiencies with an AI-powered aggregation platform, multilingual voice-enabled procurement and strategically located dark stores that enable 24-hour delivery – transforming how OEMs, EPCs and infrastructure players source their metals. In a conversation with CW, Dhananjay Goel, Director, and Vedant Goel, Director, shares how the company is reshaping procurement. What problem..

Silvin's CPVC Additive Gets NSF® Certification for Safety
Silvin Additives, a prominent manufacturer of PVC and CPVC additives, has secured the NSF® Guideline 533 certification for its CPVC Super1Pack formulation. This certification affirms the additive’s compliance with stringent international health and safety standards for products intended for drinking water applications.Awarded by NSF, a globally respected public health and safety authority based in Michigan, United States, the certification is granted only after rigorous product testing and inspection. NSF® Guideline 533 specifically assesses the safety of chemical ingredients used in produ..

Mitsubishi Halts Offshore Wind Projects in Japan
Mitsubishi Corporation (MC) has announced its decision to withdraw from three major offshore wind projects off the coast of Japan due to a significant shift in global business conditions. The projects were being developed through a consortium led by its subsidiary, Mitsubishi Corporation Offshore Wind Ltd., and were located off the shores of Noshiro City, Mitane Town, and Oga City in Akita Prefecture; Yurihonjo City in Akita Prefecture; and Choshi City in Chiba Prefecture.The company stated that following a review initiated in February 2025, it concluded the projects were no longer viable. The..