Road structures can necessitate horizontal and vertical formwork
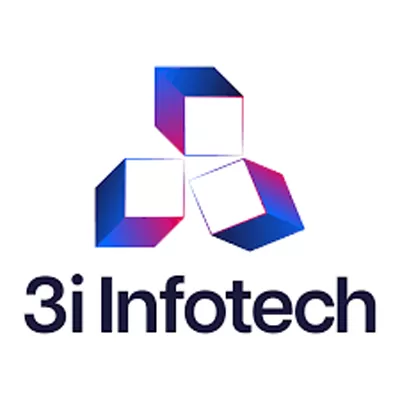
3i Infotech Reports Rs 7.25 Bn Revenue for FY25
3i Infotech, a leading provider of digital transformation, technology services and technology solutions, announced its consolidated financial results for the fourth quarter and full year FY25, ended on March 31st, 2025. The company maintained its growth momentum, displaying consistent progress for the 3rd consecutive quarter.In Q4 FY25, 3i Infotech reported revenue of Rs 1.87 billion, reflecting steady performance compared to Rs 1.81 billion in Q3 FY25 and Rs 1.97 billion in Q4 FY24. The company delivered strong profitability improvements, with gross margin growing by 14.8 per cent Q-o-Q and 1..
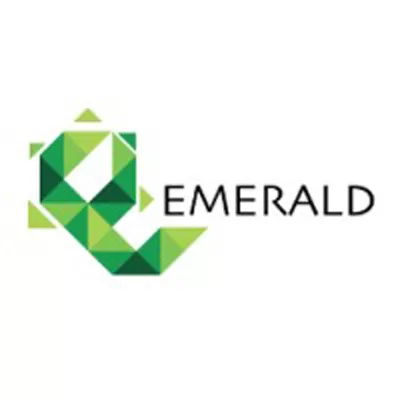
Emerald Finance Joins Baya PTE to Boost SME Bill Discounting
Emerald Finance is a dynamic company offering a spectrum of financial products and services including its flagship Earned Wage Access (EWA) in India, has entered into a strategic partnership with Singapore-based Baya PTE through its Indian subsidiary. This collaboration aims to strengthen bill discounting services for Small and Medium Enterprises (SMEs), enabling faster access to working capital and improved cash flow management.The initiative is designed to support SMEs that supply to large corporates such as JSW Steel, Delhivery, and PVR INOX, among others. By facilitating timely invoice dis..
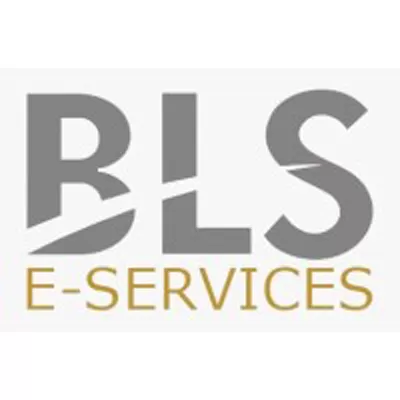
BLS E-Services Crosses Rs 5 Bn Revenue Mark in FY25
BLS E-Services, a technology-enabled digital service provider, announced its audited consolidated financial results for the quarter and full year period ended 31 March 2025.Speaking about the performance and recent updates, Shikhar Aggarwal, Chairman, BLS E- Services said, “We are delighted to report a remarkable performance in FY25, as we achieved several milestones during the fiscal year. FY25 marked our highest-ever financial performance, as we surpassed Rs 5 billion milestone in Total Income during the year, which was reported at Rs 5.45 billion, a notable YoY growth of 76 per cent. The ..