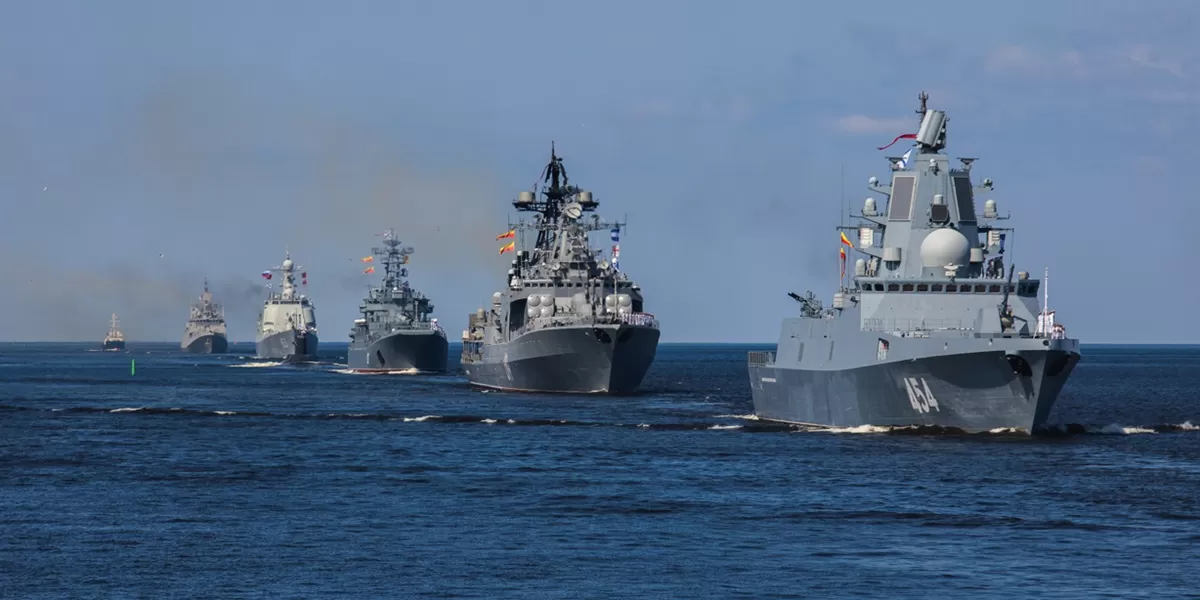
Cortec Delivers Corrosion Protection for Military Equipment and Infra
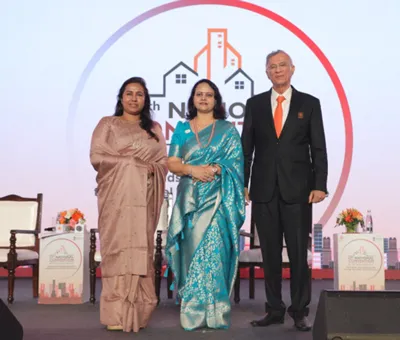
Maharashtra to Revise Infrastructure Policies
The Government of Maharashtra will make every possible effort to frame infrastructure-related policies, including those that promote housing in the state, in line with changing requirements. This assurance was given by Mrs. Meghana Sakore Bordikar, Minister of State, Government of Maharashtra, while addressing the two-day NAREDCO 17th National Convention, “India Builds: Reimagining Growth through Real Estate and Infrastructure”. At the convention, Dr Niranjan Hiranandani, Chairman of NAREDCO, called for a new blueprint for infrastructure policies in the present context.The Minister assured..
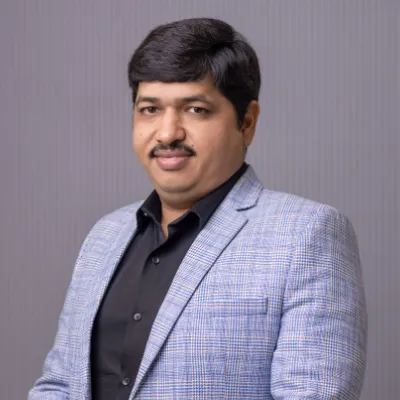
Agami Realty Enters Mumbai's Luxury Market
Agami Realty, a leading real estate developer with a legacy of over five decades, has marked its foray into Mumbai’s luxury residential market with two significant redevelopment projects in Bandra, valued at an estimated Rs 9.5 billion. The company, known for its boutique developments that blend sustainability, technology, and design excellence, has already received a strong response to its Bandra offering.Agami Eternity, the firm’s first completed premium redevelopment project in Mumbai, recently received its Occupancy Certificate. Located in Bandra East, the project was designed by inter..
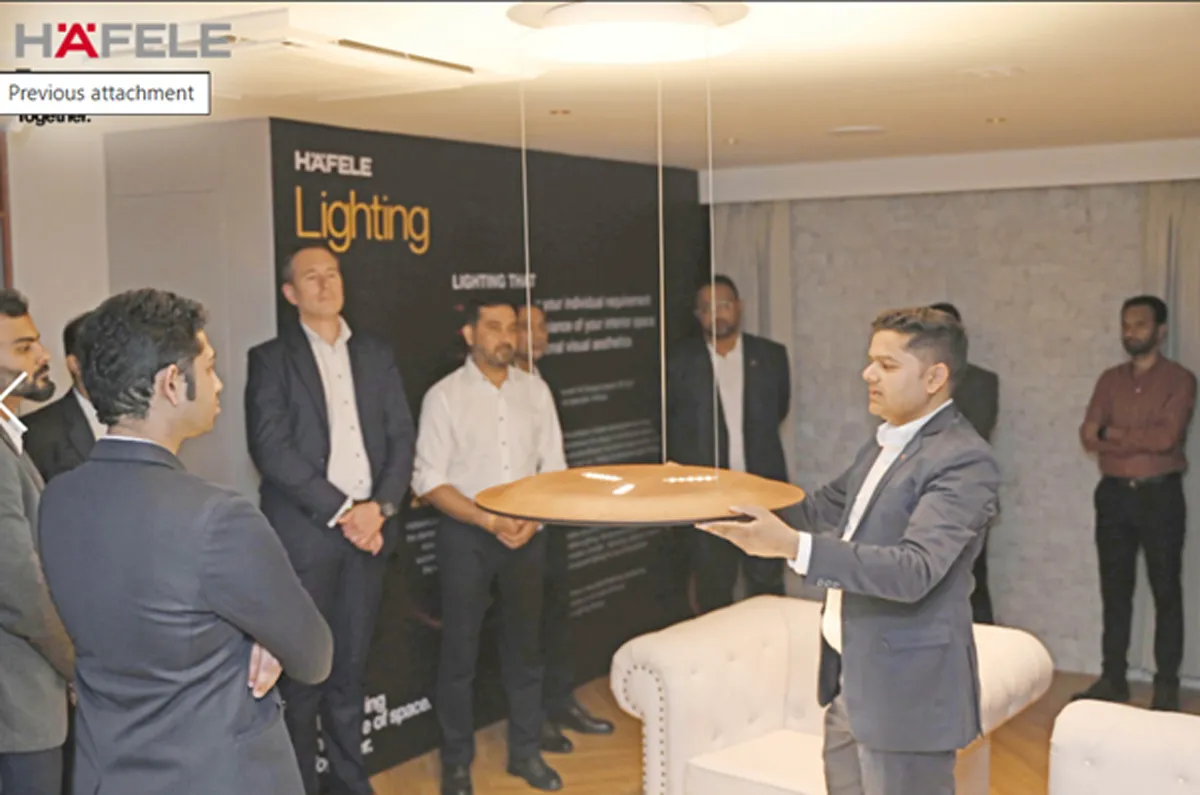
Hafele Launches Its Third Licht Experience Centre in India
Hafele, a global leader in interior solutions, has announced the launch of its third Licht Experience Centre in Ahmedabad. This new centre, located at 302, 31 Five, Opp. Palladium, Corporate Road, Makarba, follows the successful openings in Chandigarh and Indore, further strengthening Hafele's footprint in India. The name “Licht,” which means “light” in German, captures the essence of this experience, where technology meets aesthetics to redefine interior spaces.The Ahmedabad Licht Experience Centre was inaugurated by Mr Frank Schloeder, Managing Director of Hafele South Asia, and Mr P..