- Home
- Real Estate
- Chemical Invasion
Chemical Invasion
Buoyed by the prospect of tremendous growth, the construction chemicals industry in India is gearing up to meet the challenges ahead, writes Janaki Krishnamoorthi.
Here’s a prediction that is cause for cheer for the construction chemicals industry. Speaking at an international conference on construction chemicals held in February in Mumbai, Himanshu Kapadia, President, Construction Chemicals Manufacturers Association (CCMA), a recently formed body, pronounced: “The construction chemicals industry (CCI) in India, which stands today at Rs 1,700 crore, has the potential to reach Rs 5,000 crore in the next five years.”
If his predictions come true, it will be a big leap for the industry that has been moving forward at a snail’s pace. At present, the industry has several players in the organised sector and a substantially large unorganised sector offering a wide range of products. Yet a large bulk of the users in the construction industry are reportedly unaware of the utility and benefits of construction chemicals. Little wonder then, that the industry has been growing at a rate of only about 15 per cent in the past five years, though some maintain the pace has been higher.
The pace of growth
“Market research reports by leading firms suggest that the construction chemicals sector has grown at a CAGR (compound annual growth rate) of over 19 per cent from 2003 to 2009,” avers Sanjoy Dasgupta, Vice-President - Marketing, CICO Technologies Ltd. “The projected growth rate for the sector would be a CAGR of 22 per cent from 2010 to 2013. The recent recessionary slump could see the growth rate getting affected, but indications are strong that it would not go below 20 per cent.”
Kapadia, who is also Chief Executive, BASF Construction Chemicals (India) Pvt Ltd, however subscribes to a higher growth level: “The industry has been growing at 25 to 30 per cent in the past five years,” he says. “This is my personal assessment based on the pace with which some chemical manufacturing companies like us have grown in the same period.” Either way, it is clear that there is a large dormant market yet to be tapped.
The market for construction chemicals largely encompasses construction of buildings and infrastructure projects like roads, bridges, dams and ports. In both segments, there is new construction as well as repair and renovation.
Construction technology in all these areas has undergone a sea change in the past decade and one cannot deny the significant role construction chemicals have played as evinced by Subu Venkataraman, Managing Director, Sika India Pvt Ltd. “Construction chemicals have brought about drastic changes in the Indian construction industry in the past decade,” he affirms. “Speedy, durable construction owing to advanced admixtures, curing compounds and mould release agents, manufacturing of higher grades of concrete resulting in structures once considered impossible, high quality repair and retrofitting, advanced watertight structures like metro railway tunnels and hydel project tunnels, and advanced range of industrial flooring have all been made possible today.” Venkataraman was recently elected Vice-President of CCMA.
Growth drivers
Rising awareness has been one of the factors that have made it possible. “Awareness has been one of the key growth drivers for construction chemicals,” reiterates Dasgupta. “Besides awareness, technological innovativeness, mechanisation of facilities, ability to provide detailed solutions, upgrades in the SCM processes, establishment of secondary blending units, training imparted to influencers and intermediaries by manufacturers and the government’s initiative to boost infrastructure, realty and construction activities have enhanced the growth of the sector.”
Trends over the past few years indicate that growth areas are admixtures and repair system products. The increased acceptance of ready-mix concrete (RMC) in metros has definitely spurred the growth in admixture usage as has the government’s large-scale housing development and infrastructure projects. An increase in manufacturing activities and industrial growth is expected to trigger higher usage of floor treatment compounds too.
Renovation and repair make up a substantial volume of construction chemical sales in India as the country has a large number of buildings and infrastructure projects that are over 50 years old. This is another factor likely to fuel growth of construction chemicals. Evidently, there are exciting prospects ahead.
The challenges
Much of this, though, will hinge on how manufacturers address stumbling blocks like low awareness and resistance to change among the older generation and government bodies.
“The subject of construction chemicals is not taught at many engineering courses resulting in few practising engineers and architects passing out with knowledge of them,” elaborates Venkataraman. “There is resistance from sections of the older generation of practising architects and engineers not exposed to advanced construction techniques, especially in smaller towns. There is hardly any representation of people from the construction chemical field in professional private and government bodies related to construction.”
Lack of trained personnel at various levels - from technical marketing professionals to skilled labour - is yet another major dampener. Application of construction chemicals requires technical expertise and special skills. However, a large chunk of construction industry labourers and end-users are unskilled, leading to fears of work being executed in a sloppy manner. There are also substandard substitutes floating around, which are likely to create unfavourable perceptions in the mind of consumers.
“Entry barriers to the construction chemicals sector in India are practically non-existent,” states Dasgupta. “As a result, a large number of fly-by-night operators start manufacturing and selling construction chemicals with highly inadequate or no technical and technological base. After a while, unable to meet the requirements, they quit the sector. But by then they have created a big dent and a bad name for the sector.”
It’s apparent that there are several challenges ahead but manufacturers in the organised sector are geared up to counter them under the umbrella of the CCMA. “As the industry was small and not consolidated, there was not enough force to tackle the various problems plaguing us,” says Kapadia. “We will now pool our resources and tackle every issue, including creating awareness, training artisans, and liaising with government, industrial and public bodies.” We like it!
The Gamut of Construction Chemicals
Construction chemicals are niche products used to impart the desired characteristics to structures like durability, strength, additional protection from environmental hazards, faster completion of work and minimising quantities of cement and water. They can be broadly classified as follows:
Admixtures: Added to concrete or mortar to impart desired properties, water reduction for better quality, acceleration of strength development, etc.
Water-proofing compounds: Prevent leakages.
Grouts: A two-part grout system consisting of epoxy resin and epoxy hardener, especially formulated to have impervious qualities, stain and chemical resistance; used to fill joints between tile units.
Repair and protection: Includes bonding agents, repair mortars and other special systems such as injection resins.
Commercial and industrial flooring: Systems that exhibit exceptional resistance to chemicals, steam cleaning and mechanical loads.
Floor hardeners: Harden and dust-proof concrete surfaces, reduce permeability of concrete to water and oils, improve floors in warehouses, factories and industrial locations, car parks, etc.
Protective coating: Defined by protective rather than aesthetic properties though it can provide both. Commonly used for corrosion control of steel or concrete.
Specialised FRP strengthening system: Epoxy resins (or simply resins) are a class of polymers used traditionally as a matrix material for fibre-reinforced composites (FRP/FDRP); strengthening existing and new structures. An appropriate combination of reinforcement and matrix material can produce properties that fit with requirements for a particular project.
Source: Information sheet supplied at international conference on construction chemicals held in Mumbai on February 11 and 12, 2010.
Sika India Pvt Ltd.
A Swiss multinational founded in 1910 with a presence in over 70 countries and around 12,000 employees, Sika has global sales of 4.2 billion Swiss Francs (CHF). It commenced operations in India in 1987; today, it has multiple manufacturing, sales and service facilities and a network of distributors and applicators across the country. Sika offers solutions that ensure high quality and durability of complex infrastructure projects and buildings as well as answers for advanced manufacturing industries such as automotive, surface and marine transportation and wind energy. “In short, we are present in all the mentioned organised sectors through our four business units,” says Subu Venkataraman, Managing Director, Sika India Pvt Ltd. “However, looking at the huge unorganised sector of domestic customers who have no access to quality advice or solutions, we are striving hard to reach out to the common man through our distribution and retail division for enhanced durability of domestic construction.”
Sika’s range of products includes concrete admixtures, specialty mortars and grouts, sealants and adhesives, damping used in acoustic applications, and industrial flooring mainly for automotives, food and pharmaceuticals. Its innovative product line include Viscocrete technology, the Carbodur range of structural strengthening systems, the Sikaplan range of membranes for advance watertight structures, Epocem and a range of antistatic, self-levelling, antiskid flooring and topping systems. According to Venkataraman, Sika will continue to strive to increase awareness and market penetration and bring world-class technologies to India. Three recent noteworthy projects are the Bandra - Worli Sea Link (a range of admixtures for higher strength, durability and prevention of marine corrosion); Mahindra & Mahindra at Nasik (epoxy flooring for over 1.5 lakh sq m of space); and the Indian Space Research Organisation in Bengaluru (antistatic flooring).
BASF Construction Chemicals (India) Pvt Ltd.
BASF Construction Chemicals India Pvt Ltd, wholly owned by the BASF Group, is a pioneer in energy-efficient building concepts and has met architectural design requirements in various climatic environments. Internationally, BASF also specialises in façade replacement and renovation using cement-free restoration mortars and stuccos compatible with lime-based original mortar, and has a total system for restoring damaged monuments and statues.
“Understanding the customer’s requirement, offering an appropriate solution from a wide product range and following a consultative process by front-end engineers make us unique,” asserts Himanshu Kapadia, Chief Executive, BASF Construction Chemicals (India) Pvt Ltd. Some latest innovative products include lightweight thermal and water insulation systems for concrete roof; Coniroof spray-applied polyurethane waterproofing system that can be applied on almost any kind of surface; exterior insulation finish systems (EIFS) like BASF Finestone and Neopor, and flat roof systems like BASF’s Peripor Board - an innovative, expandable, water-resistant insulating solution for protection against ingression of external heat.
BASF is now planning to introduce in India globally well-accepted technologies relating to green building concepts and sustainable construction solutions. “EIFS is one such green and economical solution to cope with energy conservation challenges in building operations,” reveals Kapadia. “In the concrete admixture front, we are locally evaluating the smart dynamic concrete (SDC) concept, a low-fine self-compacting concrete for lower to medium grade of concrete. SDC can revolutionise the way concrete is produced and placed. We are also working on the introduction of the Speed DAM and Vis-RCC concepts that would enable faster construction of dams and overall savings of up to 20 per cent.”
CICO Technologies Ltd.
A leading chemicals and protective coatings manufacturer, CICO Technologies Ltd (CTL) specialises in solutions to problems related to concrete and steel through its wide range of products. With over 200 products, CTL is now focusing on going green with its range. On the technology front, it has introduced several new protective coatings and hybrid systems with polyurethane technology. Polyurea and hybrid derivatives are next in line for launch.
“India loses over Rs 25,000 crore worth of steel and much more of concrete every year owing to corrosion,” reveals Sanjoy Dasgupta, Vice-President - Marketing, CICO Technologies Ltd. “CTL caters to the requirements of concrete/steel structures prone to weathering and corrosion. Introduction of certain new products like migratory corrosion inhibitors have created a revolution in the protection of rebars and reduced the costs of projects and man-hours for installation.” CTL’s focus has been on infrastructure and it also has a special team to lead its ‘Restoring India’s Pride’ campaign that provides consultancy and end-to-end solutions for heritage structures.
“One of the most important factors behind CTL’s wonderful growth rate is its unique ability to combine and customise products and ensure correct application for products and systems in all instances,” adds Dasgupta. “Our biggest strength is our distribution network designed so that the major intermediaries for CTL can become a solution provider and not just a product seller.” Future plans include enhancing its network, introducing newer and greener products, focusing on newer international markets and becoming India’s flag-bearer as a construction chemical multinational.
Case Study 1
Products and technical guidance: CICO Technologies Ltd (CTL)
Project: Simhadri Thermal Power Project, Andhra Pradesh
Scope: Total protection to concrete and steel sections against corrosion
Client: National Thermal Power Corporation (NTPC)
Contractor: National Buildings Construction Corporation Ltd (NBCC)
Period: 2002
Background: Owing to water scarcity, NTPC decided to use seawater to operate the project’s two concrete cooling towers with the water gushing through steel ducts. As a result, all the concrete and steel sections of the entire system will constantly be in contact with seawater and its contaminants. So CTL had to provide complete protection against corrosion to all steel and concrete sections. The towers were 110-m diameter at the bottom, 72-m diameter at the top and 165-m high with a capacity of 60,000 cu m per hour with a cooling range of 11°C. NTPC’s specifications stipulated the use of admix organic corrosion inhibitor (MCI type) in the concrete above the water zone and apply a 2-mm-thick 100 per cent solid polyurethane (PU) coating on all concrete and steel members in the water zone (up to 18 m) and hot water basin (1.8 m) to protect from the effect of seawater. The total area for the PU coating (2 mm) was measured as 57,500 sq m involving 88 racker columns supporting shell structure and 1,220 columns, 3,375 beams, 268 baffles and 260 bracing, etc, internal support of structure for distribution basin.
Solution: CTL supplied the total quantity of Corchem 60 (organic corrosion inhibitor) meeting NTPC’s specification and executed the application of 2- mm-thick 100 per cent solid PU coating with NTPC-approved material Corchem 210 (I) on Cooling Tower 2. The entire job was completed meeting the tight commissioning schedule. The PU coating job was started just after the completion of the shell structure. The precast concrete members were erected and screed concrete on floor was also done while the PU coating was in progress.
Challenge: The job required very close coordination with various agencies working simultaneously and the need for strict compliance to safety norms. It became very difficult to comply with environmental requirements such as temperature, humidity, dew point and moisture content of concrete, and the planned working schedule of the very sensitive PU coating was also disrupted. The CTL team in close consultation with Indian Institute of Chemical Technology, Hyderabad, rescheduled various application activities to reasonably suit environmental conditions and specified conditions to achieve the required progress of coating. CTL also deployed man and machines round the clock with an additional maintenance gang ensuring availability of all spare parts at site. The change in environmental conditions was managed with the extensive use of a hot air blower before application of primer and PU coating. Single-component, moisture-cured PU primer was also used where moisture content in concrete was anticipated to be lower than permissible owing to various construction activities around the coating area. This enabled NBCC to simultaneously carry out the overhead erection of the AC pipe, stainless steel channels and fills and plan the parallel activities of testing and commissioning of the CWC pump, hot water header and connected pipe line, ensuring the commissioning of the second unit as per schedule.
Case Study 2
Products and technical guidance: BASF Construction Chemicals (India) Pvt Ltd
Project: Rail over-bridge at Chalthan, Surat
Scope: Strengthening of bridge girders
Client: National Highways Authority of India (NHAI)
Designer and architect: Epicons Consultants, Mumbai
Contractor: Rebuild Strut Associates, Mumbai
Period: 2006
Background: The 25-year-old rail over-bridge near Chalthan, Surat, on NH 8 connecting Mumbai to Delhi needed structural strengthening. The 42-m-long, four-lane bridge is divided into three spans, end spans being 12 m each. It has eight main girders in the longitudinal direction about 0.5 m width ×1.2 m depth. NHAI decided to adopt fibre-reinforced polymer (FRP) system to strengthen the bridge. FRP composites have been used for nearly 30 years in aerospace and manufacturing applications where low weight, high-tensile strength and non-corrosive structural properties are required. FRP has proven itself in fabric roof structures, internal concrete reinforcement, deck gratings and most impressively as externally bonded reinforcement as it exhibits low creep, and compared to steel is thinner and lighter with 10 times the tensile strength.
Solution: Structural retrofitting involving shear and flexural capacity increase in the main girder beams in the end spans was undertaken to withstand the current and future loading conditions. As stipulated in the contract, designs and detailing were based on the international design guidelines of FIP and ACI.
Systems used: MBrace Primer, MBrace Saturant, MBraceGSheet EU 900. The MBrace Composite Strengthening System, an externally bonded FRP reinforcement system for concrete and masonry structures, is field-proven. Some advantages offered by MBrace FRP are high strength, high stiffness, light weight, high durability, non-corrosiveness and low installation time. It can be installed in areas with limited access, is easy to conceal and forms around complex surface shapes. MBrace G Sheet EU900, unidirectional E-Glass fibre sheets with 900 gsm weight were used for flexural and sheer capacity increase. Depending on the capacity increase required, single and multiple layers of the sheets were used. Substrate was primed using MBrace Primer while MBrace Saturant was used to install G Sheets in position and for the required impregnation. Final finish was provided with cement: sand plaster for facilitating an even look with the surrounding structure.
- Construction
- Update
- Portal
- World
- April
- Magazine
- 2010
- India
- Chemicals
- Mumbai
- Himanshu Kapadia
- CCMA
- CCI
- CAGR
- Sanjoy Dasgupta
- 2013
- BASF
- buildings
- infrastructure
- roads
- bridges
- dams
- ports
- renovation
- technology
- Subu Venkataraman
- Sika India Pvt Ltd
- railway tunnels
- metro
- RMC
- resistance
- durability
- strength
- Water-proofing
- Sika India Pvt Ltd.
- automotive
- marine transportation
- concrete admixtures
- Subu Venkataraman
- lightweight thermal
- water insulation
- EIFS
- Peripor Board
- SDC
- coatings
- polyurethane
- corrosion inhibitors
- NTPC
- NBCC
- PU primer
- NHAI
- Chalthan
- Surat
- MBrace Primer
- G Sheets
Buoyed by the prospect of tremendous growth, the construction chemicals industry in India is gearing up to meet the challenges ahead, writes Janaki Krishnamoorthi. Here’s a prediction that is cause for cheer for the construction chemicals industry. Speaking at an international conference on construction chemicals held in February in Mumbai, Himanshu Kapadia, President, Construction Chemicals Manufacturers Association (CCMA), a recently formed body, pronounced: “The construction chemicals industry (CCI) in India, which stands today at Rs 1,700 crore, has the potential to reach Rs 5,000 crore in the next five years.” If his predictions come true, it will be a big leap for the industry that has been moving forward at a snail’s pace. At present, the industry has several players in the organised sector and a substantially large unorganised sector offering a wide range of products. Yet a large bulk of the users in the construction industry are reportedly unaware of the utility and benefits of construction chemicals. Little wonder then, that the industry has been growing at a rate of only about 15 per cent in the past five years, though some maintain the pace has been higher. The pace of growth “Market research reports by leading firms suggest that the construction chemicals sector has grown at a CAGR (compound annual growth rate) of over 19 per cent from 2003 to 2009,” avers Sanjoy Dasgupta, Vice-President - Marketing, CICO Technologies Ltd. “The projected growth rate for the sector would be a CAGR of 22 per cent from 2010 to 2013. The recent recessionary slump could see the growth rate getting affected, but indications are strong that it would not go below 20 per cent.” Kapadia, who is also Chief Executive, BASF Construction Chemicals (India) Pvt Ltd, however subscribes to a higher growth level: “The industry has been growing at 25 to 30 per cent in the past five years,” he says. “This is my personal assessment based on the pace with which some chemical manufacturing companies like us have grown in the same period.” Either way, it is clear that there is a large dormant market yet to be tapped. The market for construction chemicals largely encompasses construction of buildings and infrastructure projects like roads, bridges, dams and ports. In both segments, there is new construction as well as repair and renovation. Construction technology in all these areas has undergone a sea change in the past decade and one cannot deny the significant role construction chemicals have played as evinced by Subu Venkataraman, Managing Director, Sika India Pvt Ltd. “Construction chemicals have brought about drastic changes in the Indian construction industry in the past decade,” he affirms. “Speedy, durable construction owing to advanced admixtures, curing compounds and mould release agents, manufacturing of higher grades of concrete resulting in structures once considered impossible, high quality repair and retrofitting, advanced watertight structures like metro railway tunnels and hydel project tunnels, and advanced range of industrial flooring have all been made possible today.” Venkataraman was recently elected Vice-President of CCMA. Growth drivers Rising awareness has been one of the factors that have made it possible. “Awareness has been one of the key growth drivers for construction chemicals,” reiterates Dasgupta. “Besides awareness, technological innovativeness, mechanisation of facilities, ability to provide detailed solutions, upgrades in the SCM processes, establishment of secondary blending units, training imparted to influencers and intermediaries by manufacturers and the government’s initiative to boost infrastructure, realty and construction activities have enhanced the growth of the sector.” Trends over the past few years indicate that growth areas are admixtures and repair system products. The increased acceptance of ready-mix concrete (RMC) in metros has definitely spurred the growth in admixture usage as has the government’s large-scale housing development and infrastructure projects. An increase in manufacturing activities and industrial growth is expected to trigger higher usage of floor treatment compounds too. Renovation and repair make up a substantial volume of construction chemical sales in India as the country has a large number of buildings and infrastructure projects that are over 50 years old. This is another factor likely to fuel growth of construction chemicals. Evidently, there are exciting prospects ahead. The challenges Much of this, though, will hinge on how manufacturers address stumbling blocks like low awareness and resistance to change among the older generation and government bodies. “The subject of construction chemicals is not taught at many engineering courses resulting in few practising engineers and architects passing out with knowledge of them,” elaborates Venkataraman. “There is resistance from sections of the older generation of practising architects and engineers not exposed to advanced construction techniques, especially in smaller towns. There is hardly any representation of people from the construction chemical field in professional private and government bodies related to construction.” Lack of trained personnel at various levels - from technical marketing professionals to skilled labour - is yet another major dampener. Application of construction chemicals requires technical expertise and special skills. However, a large chunk of construction industry labourers and end-users are unskilled, leading to fears of work being executed in a sloppy manner. There are also substandard substitutes floating around, which are likely to create unfavourable perceptions in the mind of consumers. “Entry barriers to the construction chemicals sector in India are practically non-existent,” states Dasgupta. “As a result, a large number of fly-by-night operators start manufacturing and selling construction chemicals with highly inadequate or no technical and technological base. After a while, unable to meet the requirements, they quit the sector. But by then they have created a big dent and a bad name for the sector.” It’s apparent that there are several challenges ahead but manufacturers in the organised sector are geared up to counter them under the umbrella of the CCMA. “As the industry was small and not consolidated, there was not enough force to tackle the various problems plaguing us,” says Kapadia. “We will now pool our resources and tackle every issue, including creating awareness, training artisans, and liaising with government, industrial and public bodies.” We like it! The Gamut of Construction Chemicals Construction chemicals are niche products used to impart the desired characteristics to structures like durability, strength, additional protection from environmental hazards, faster completion of work and minimising quantities of cement and water. They can be broadly classified as follows: Admixtures: Added to concrete or mortar to impart desired properties, water reduction for better quality, acceleration of strength development, etc. Water-proofing compounds: Prevent leakages.Grouts: A two-part grout system consisting of epoxy resin and epoxy hardener, especially formulated to have impervious qualities, stain and chemical resistance; used to fill joints between tile units.Repair and protection: Includes bonding agents, repair mortars and other special systems such as injection resins.Commercial and industrial flooring: Systems that exhibit exceptional resistance to chemicals, steam cleaning and mechanical loads.Floor hardeners: Harden and dust-proof concrete surfaces, reduce permeability of concrete to water and oils, improve floors in warehouses, factories and industrial locations, car parks, etc.Protective coating: Defined by protective rather than aesthetic properties though it can provide both. Commonly used for corrosion control of steel or concrete.Specialised FRP strengthening system: Epoxy resins (or simply resins) are a class of polymers used traditionally as a matrix material for fibre-reinforced composites (FRP/FDRP); strengthening existing and new structures. An appropriate combination of reinforcement and matrix material can produce properties that fit with requirements for a particular project.Source: Information sheet supplied at international conference on construction chemicals held in Mumbai on February 11 and 12, 2010. Sika India Pvt Ltd. A Swiss multinational founded in 1910 with a presence in over 70 countries and around 12,000 employees, Sika has global sales of 4.2 billion Swiss Francs (CHF). It commenced operations in India in 1987; today, it has multiple manufacturing, sales and service facilities and a network of distributors and applicators across the country. Sika offers solutions that ensure high quality and durability of complex infrastructure projects and buildings as well as answers for advanced manufacturing industries such as automotive, surface and marine transportation and wind energy. “In short, we are present in all the mentioned organised sectors through our four business units,” says Subu Venkataraman, Managing Director, Sika India Pvt Ltd. “However, looking at the huge unorganised sector of domestic customers who have no access to quality advice or solutions, we are striving hard to reach out to the common man through our distribution and retail division for enhanced durability of domestic construction.” Sika’s range of products includes concrete admixtures, specialty mortars and grouts, sealants and adhesives, damping used in acoustic applications, and industrial flooring mainly for automotives, food and pharmaceuticals. Its innovative product line include Viscocrete technology, the Carbodur range of structural strengthening systems, the Sikaplan range of membranes for advance watertight structures, Epocem and a range of antistatic, self-levelling, antiskid flooring and topping systems. According to Venkataraman, Sika will continue to strive to increase awareness and market penetration and bring world-class technologies to India. Three recent noteworthy projects are the Bandra - Worli Sea Link (a range of admixtures for higher strength, durability and prevention of marine corrosion); Mahindra & Mahindra at Nasik (epoxy flooring for over 1.5 lakh sq m of space); and the Indian Space Research Organisation in Bengaluru (antistatic flooring). BASF Construction Chemicals (India) Pvt Ltd. BASF Construction Chemicals India Pvt Ltd, wholly owned by the BASF Group, is a pioneer in energy-efficient building concepts and has met architectural design requirements in various climatic environments. Internationally, BASF also specialises in façade replacement and renovation using cement-free restoration mortars and stuccos compatible with lime-based original mortar, and has a total system for restoring damaged monuments and statues. “Understanding the customer’s requirement, offering an appropriate solution from a wide product range and following a consultative process by front-end engineers make us unique,” asserts Himanshu Kapadia, Chief Executive, BASF Construction Chemicals (India) Pvt Ltd. Some latest innovative products include lightweight thermal and water insulation systems for concrete roof; Coniroof spray-applied polyurethane waterproofing system that can be applied on almost any kind of surface; exterior insulation finish systems (EIFS) like BASF Finestone and Neopor, and flat roof systems like BASF’s Peripor Board - an innovative, expandable, water-resistant insulating solution for protection against ingression of external heat. BASF is now planning to introduce in India globally well-accepted technologies relating to green building concepts and sustainable construction solutions. “EIFS is one such green and economical solution to cope with energy conservation challenges in building operations,” reveals Kapadia. “In the concrete admixture front, we are locally evaluating the smart dynamic concrete (SDC) concept, a low-fine self-compacting concrete for lower to medium grade of concrete. SDC can revolutionise the way concrete is produced and placed. We are also working on the introduction of the Speed DAM and Vis-RCC concepts that would enable faster construction of dams and overall savings of up to 20 per cent.” CICO Technologies Ltd. A leading chemicals and protective coatings manufacturer, CICO Technologies Ltd (CTL) specialises in solutions to problems related to concrete and steel through its wide range of products. With over 200 products, CTL is now focusing on going green with its range. On the technology front, it has introduced several new protective coatings and hybrid systems with polyurethane technology. Polyurea and hybrid derivatives are next in line for launch. “India loses over Rs 25,000 crore worth of steel and much more of concrete every year owing to corrosion,” reveals Sanjoy Dasgupta, Vice-President - Marketing, CICO Technologies Ltd. “CTL caters to the requirements of concrete/steel structures prone to weathering and corrosion. Introduction of certain new products like migratory corrosion inhibitors have created a revolution in the protection of rebars and reduced the costs of projects and man-hours for installation.” CTL’s focus has been on infrastructure and it also has a special team to lead its ‘Restoring India’s Pride’ campaign that provides consultancy and end-to-end solutions for heritage structures. “One of the most important factors behind CTL’s wonderful growth rate is its unique ability to combine and customise products and ensure correct application for products and systems in all instances,” adds Dasgupta. “Our biggest strength is our distribution network designed so that the major intermediaries for CTL can become a solution provider and not just a product seller.” Future plans include enhancing its network, introducing newer and greener products, focusing on newer international markets and becoming India’s flag-bearer as a construction chemical multinational. Case Study 1 Products and technical guidance: CICO Technologies Ltd (CTL)Project: Simhadri Thermal Power Project, Andhra PradeshScope: Total protection to concrete and steel sections against corrosionClient: National Thermal Power Corporation (NTPC) Contractor: National Buildings Construction Corporation Ltd (NBCC)Period: 2002 Background: Owing to water scarcity, NTPC decided to use seawater to operate the project’s two concrete cooling towers with the water gushing through steel ducts. As a result, all the concrete and steel sections of the entire system will constantly be in contact with seawater and its contaminants. So CTL had to provide complete protection against corrosion to all steel and concrete sections. The towers were 110-m diameter at the bottom, 72-m diameter at the top and 165-m high with a capacity of 60,000 cu m per hour with a cooling range of 11°C. NTPC’s specifications stipulated the use of admix organic corrosion inhibitor (MCI type) in the concrete above the water zone and apply a 2-mm-thick 100 per cent solid polyurethane (PU) coating on all concrete and steel members in the water zone (up to 18 m) and hot water basin (1.8 m) to protect from the effect of seawater. The total area for the PU coating (2 mm) was measured as 57,500 sq m involving 88 racker columns supporting shell structure and 1,220 columns, 3,375 beams, 268 baffles and 260 bracing, etc, internal support of structure for distribution basin.Solution: CTL supplied the total quantity of Corchem 60 (organic corrosion inhibitor) meeting NTPC’s specification and executed the application of 2- mm-thick 100 per cent solid PU coating with NTPC-approved material Corchem 210 (I) on Cooling Tower 2. The entire job was completed meeting the tight commissioning schedule. The PU coating job was started just after the completion of the shell structure. The precast concrete members were erected and screed concrete on floor was also done while the PU coating was in progress. Challenge: The job required very close coordination with various agencies working simultaneously and the need for strict compliance to safety norms. It became very difficult to comply with environmental requirements such as temperature, humidity, dew point and moisture content of concrete, and the planned working schedule of the very sensitive PU coating was also disrupted. The CTL team in close consultation with Indian Institute of Chemical Technology, Hyderabad, rescheduled various application activities to reasonably suit environmental conditions and specified conditions to achieve the required progress of coating. CTL also deployed man and machines round the clock with an additional maintenance gang ensuring availability of all spare parts at site. The change in environmental conditions was managed with the extensive use of a hot air blower before application of primer and PU coating. Single-component, moisture-cured PU primer was also used where moisture content in concrete was anticipated to be lower than permissible owing to various construction activities around the coating area. This enabled NBCC to simultaneously carry out the overhead erection of the AC pipe, stainless steel channels and fills and plan the parallel activities of testing and commissioning of the CWC pump, hot water header and connected pipe line, ensuring the commissioning of the second unit as per schedule. Case Study 2 Products and technical guidance: BASF Construction Chemicals (India) Pvt LtdProject: Rail over-bridge at Chalthan, SuratScope: Strengthening of bridge girdersClient: National Highways Authority of India (NHAI)Designer and architect: Epicons Consultants, MumbaiContractor: Rebuild Strut Associates, MumbaiPeriod: 2006Background: The 25-year-old rail over-bridge near Chalthan, Surat, on NH 8 connecting Mumbai to Delhi needed structural strengthening. The 42-m-long, four-lane bridge is divided into three spans, end spans being 12 m each. It has eight main girders in the longitudinal direction about 0.5 m width ×1.2 m depth. NHAI decided to adopt fibre-reinforced polymer (FRP) system to strengthen the bridge. FRP composites have been used for nearly 30 years in aerospace and manufacturing applications where low weight, high-tensile strength and non-corrosive structural properties are required. FRP has proven itself in fabric roof structures, internal concrete reinforcement, deck gratings and most impressively as externally bonded reinforcement as it exhibits low creep, and compared to steel is thinner and lighter with 10 times the tensile strength.Solution: Structural retrofitting involving shear and flexural capacity increase in the main girder beams in the end spans was undertaken to withstand the current and future loading conditions. As stipulated in the contract, designs and detailing were based on the international design guidelines of FIP and ACI.Systems used: MBrace Primer, MBrace Saturant, MBraceGSheet EU 900. The MBrace Composite Strengthening System, an externally bonded FRP reinforcement system for concrete and masonry structures, is field-proven. Some advantages offered by MBrace FRP are high strength, high stiffness, light weight, high durability, non-corrosiveness and low installation time. It can be installed in areas with limited access, is easy to conceal and forms around complex surface shapes. MBrace G Sheet EU900, unidirectional E-Glass fibre sheets with 900 gsm weight were used for flexural and sheer capacity increase. Depending on the capacity increase required, single and multiple layers of the sheets were used. Substrate was primed using MBrace Primer while MBrace Saturant was used to install G Sheets in position and for the required impregnation. Final finish was provided with cement: sand plaster for facilitating an even look with the surrounding structure.
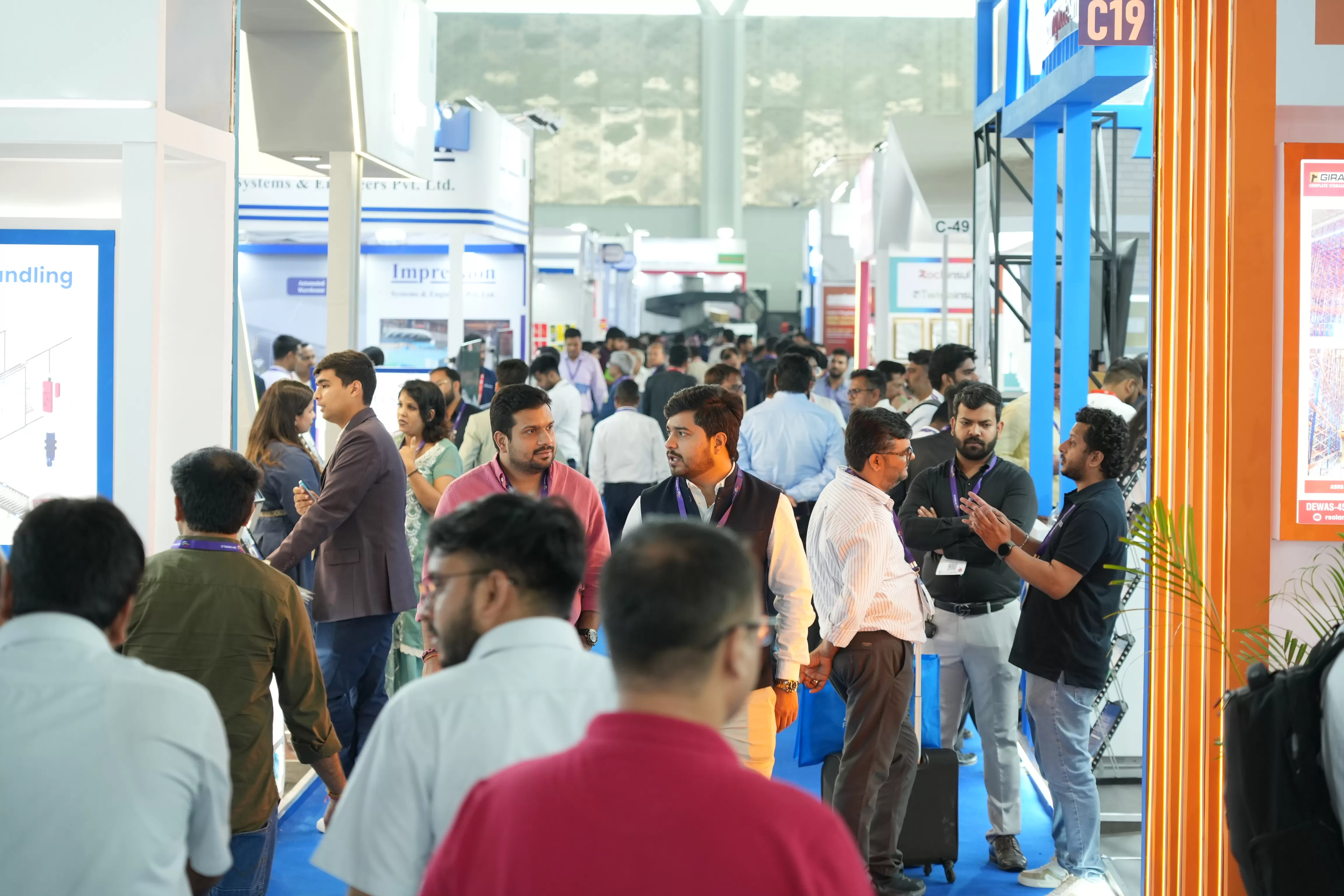
India Warehousing Show Concludes with Record Participation
The 14th edition of the India Warehousing Show (IWS) 2025 wrapped up successfully at Yashobhoomi (IICC), Dwarka, drawing over 300 exhibitors from 15 countries and welcoming more than 15,000 visitors from India and abroad. As the country’s leading platform for warehousing and supply-chain excellence, the event highlighted cutting-edge technologies, sustainable solutions, and new product innovations that are reshaping the logistics sector.The show was inaugurated by Shri Pankaj Kumar, Joint Secretary – Logistics, DPIIT, Ministry of Commerce and Industry, Government of India, who delivered a ..
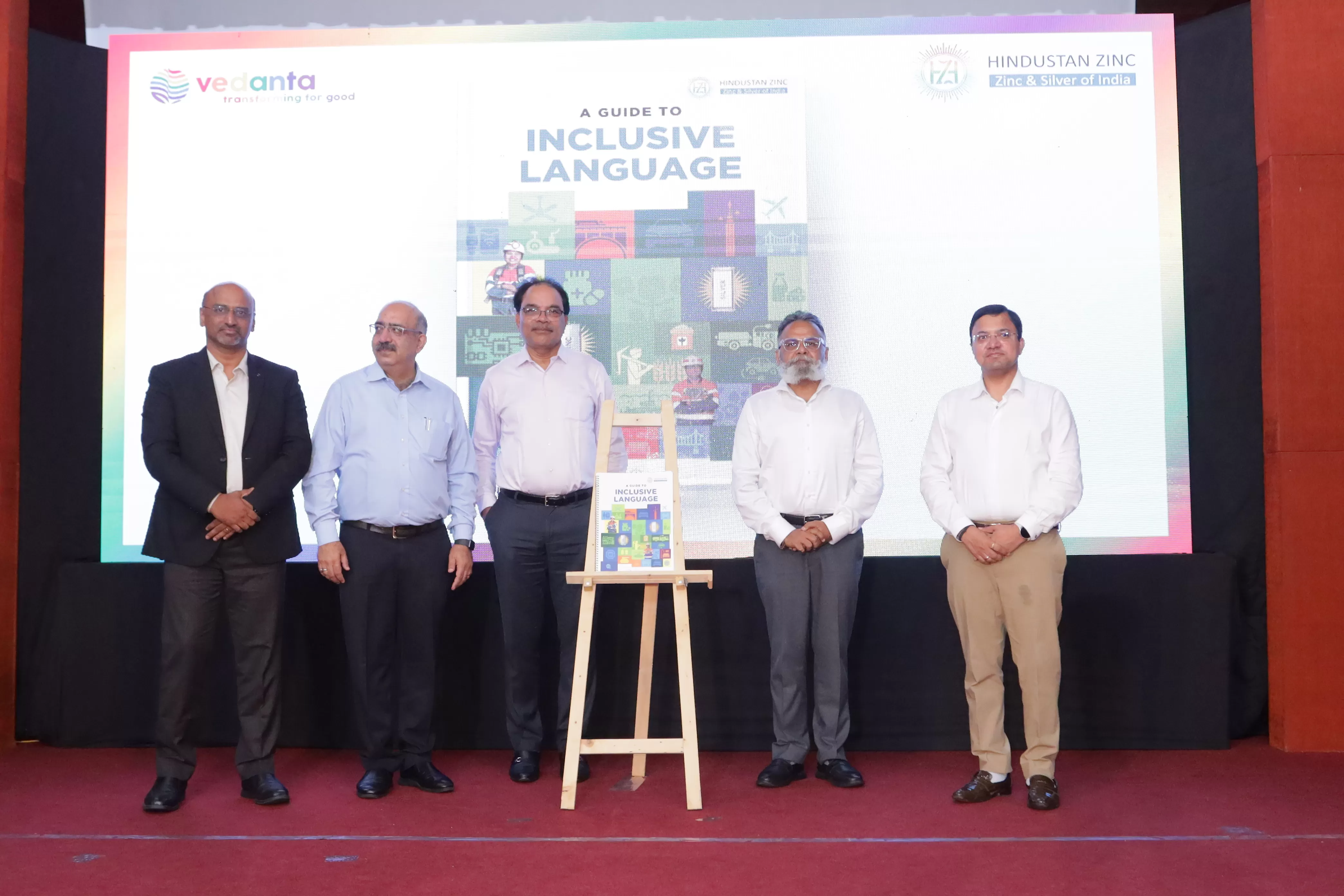
Hindustan Zinc Launches Inclusive Language Guide to Promote Workplace Diversity
Udaipur, 3rd July 2025: Hindustan Zinc Limited (NSE: HINDZINC), the world’s largest integrated zinc producer, has made a significant stride towards enhancing workplace equity with the launch of its Guidebook to Inclusive Language. This move underscores the company’s strong commitment to creating a respectful, diverse, and inclusive work environment. The guidebook serves as a framework to encourage inclusive communication, promote sensitivity towards various communities, and support equitable practices throughout the organization.The Guidebook was launched on Hindustan Zinc’s homegrown #Z..
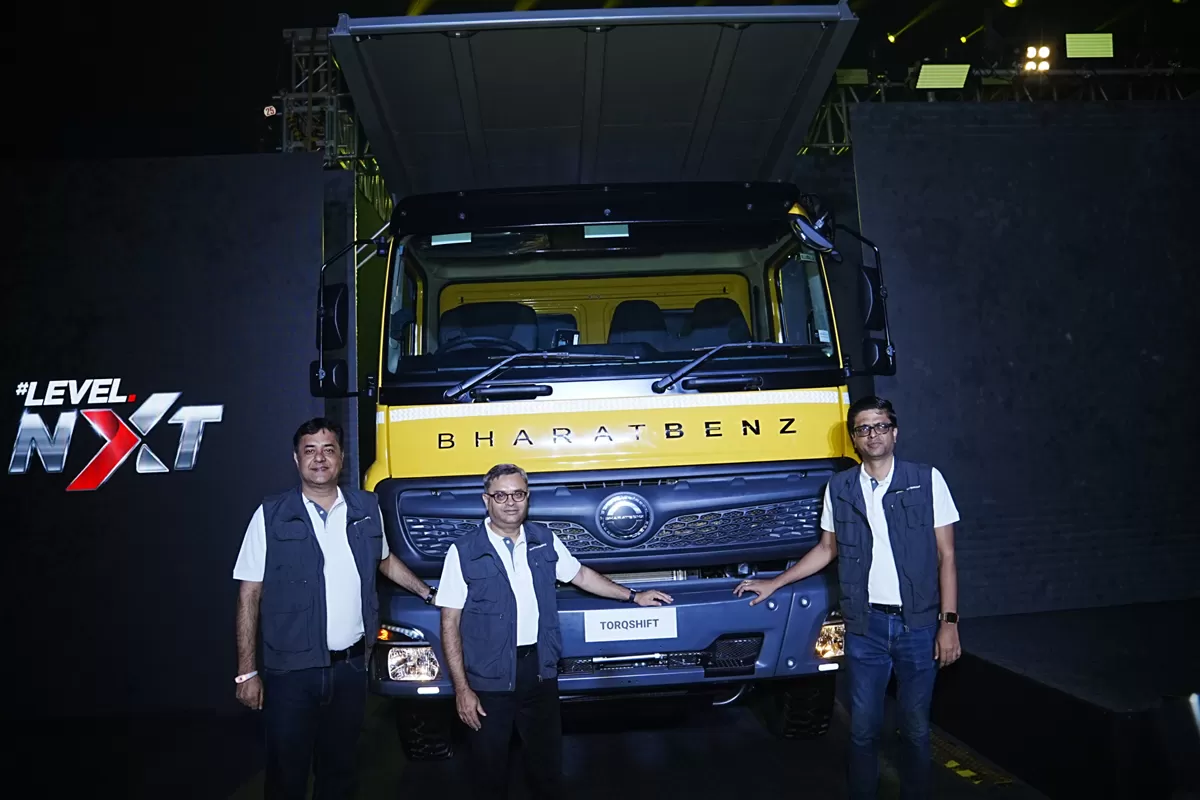
BharatBenz Launches New Mining Range to Support India’s Infra Growth
Chennai, India: The Indian construction and mining equipment sector is set to grow significantly, projected to increase from $16 billion to $45 billion by 2030. To support this expansion, Daimler India Commercial Vehicles (DICV), a wholly owned subsidiary of Daimler Truck AG, has launched its all-new BharatBenz Construction and Mining range. This range includes the HX and Torqshift series models, designed to meet the critical demand for reliable, high-performance vehicles as large contractors modernise their fleets and invest in owned assets.The HX and Torqshift series have undergone rigorous ..
Latest Updates
Advertisement
Recommended for you
Advertisement
Subscribe to Our Newsletter
Get daily newsletters around different themes from Construction world.
Advertisement
Advertisement
Advertisement
subscribe to the newsletter
Don't miss out on valuable insights and opportunities
to connect with like minded professionals