Construction activities face hurdles as cement prices shoot up exorbitantly
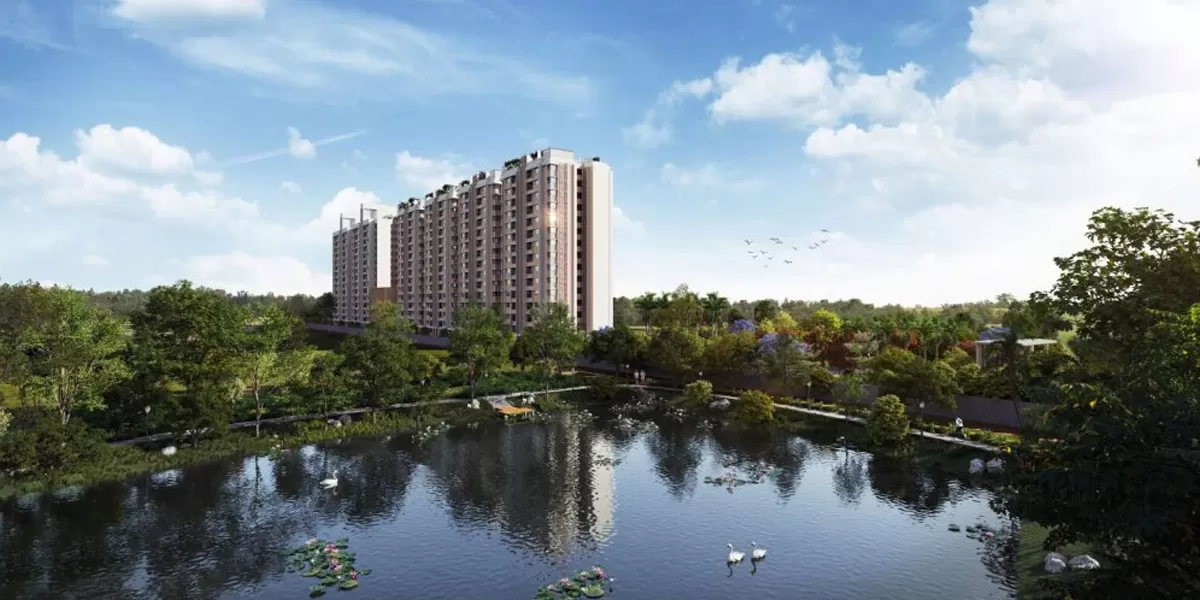
Shriram Properties Launches ‘Codename: The One’ in Bengaluru
Shriram Properties (SPL), a leading real estate developer focused on the mid-market and mid-premium segments, has announced the launch of its latest residential project under the banner “Codename: The One” in Bengaluru’s Electronic City corridor. This feature-rich gated community will offer 340 spacious 2- and 3-BHK residences, with a total saleable area of approximately 5 lakh square feet and an estimated revenue potential of over Rs 3.5 billion. The project is expected to be developed over a span of more than three years. Strategically located near the Bommasandra Metro stat..
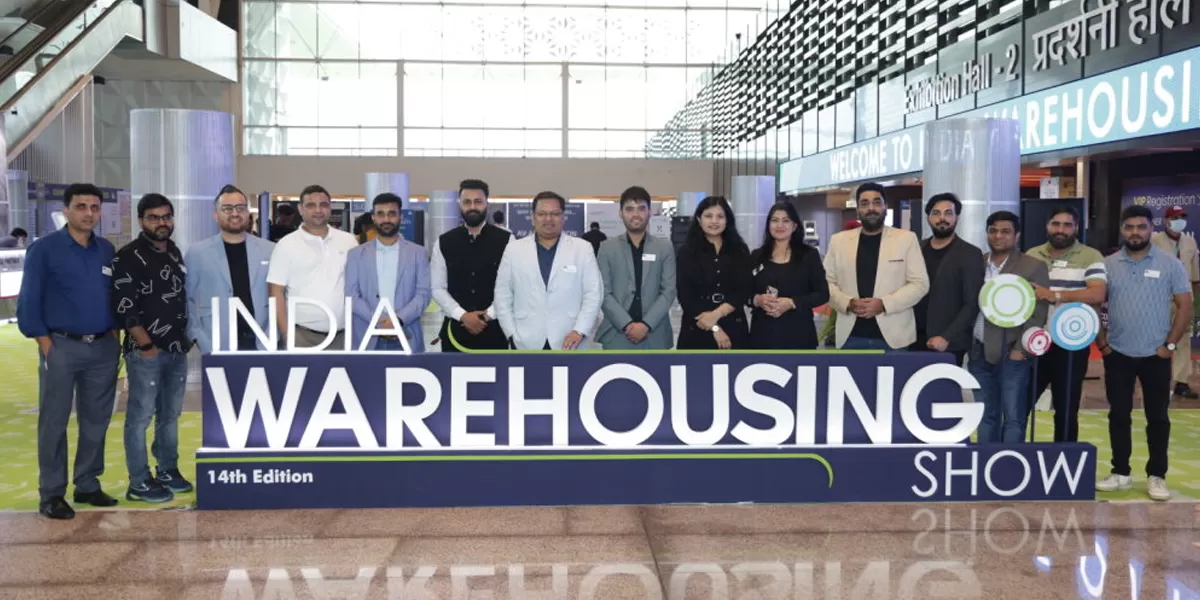
India Warehousing Show 2025 Closes with Strong Global Presence
The 14th edition of the India Warehousing Show (IWS) 2025 concluded successfully at Yashobhoomi (IICC), Dwarka, drawing participation from over 300 exhibitors across 15 countries and welcoming 15,000+ visitors. Recognised as India’s leading platform for warehousing and logistics excellence, IWS 2025 offered a comprehensive display of cutting-edge automation, sustainable warehousing solutions, and next-gen supply chain technologies. The show was inaugurated by Shri Pankaj Kumar, Joint Secretary – Logistics, DPIIT, Ministry of Commerce and Industry, Government of India. In his opening a..
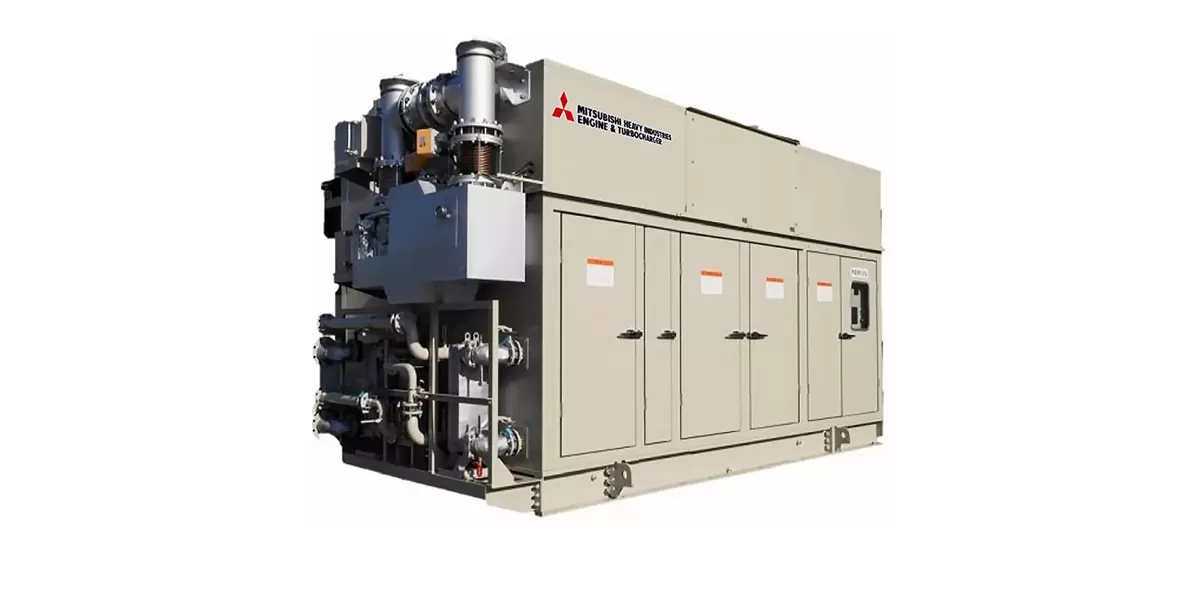
MHIET Launches 450kW Gas Cogeneration System with H₂ Co-Firing
Mitsubishi Heavy Industries Engine & Turbocharger (MHIET), part of the Mitsubishi Heavy Industries Group, has launched a new 450kW gas cogeneration system, the SGP M450, jointly developed with Toho Gas Co.,. The system supports hydrogen co-firing at up to 15 vol per cent, with no loss in performance or reliability. The system is currently available in the Japanese market, and has been developed from the existing GS6R2 city gas engine platform. Key modifications were made to the fuel gas and engine control systems to enable hydrogen co-firing. Verified through de..