MOBISCREEN EVO Screens in Action
Read full article
CW Gold Benefits
- Weekly Industry Updates
- Industry Feature Stories
- Premium Newsletter Access
- Building Material Prices (weekly) + trends/analysis
- Best Stories from our sister publications - Indian Cement Review, Equipment India, Infrastructure Today
- Sector focused Research Reports
- Sector Wise Updates (infrastructure, cement, equipment & construction) + trend analysis
- Exclusive text & video interviews
- Digital Delivery
- Financial Data for publically listed companies + Analysis
- Preconceptual Projects in the pipeline PAN India
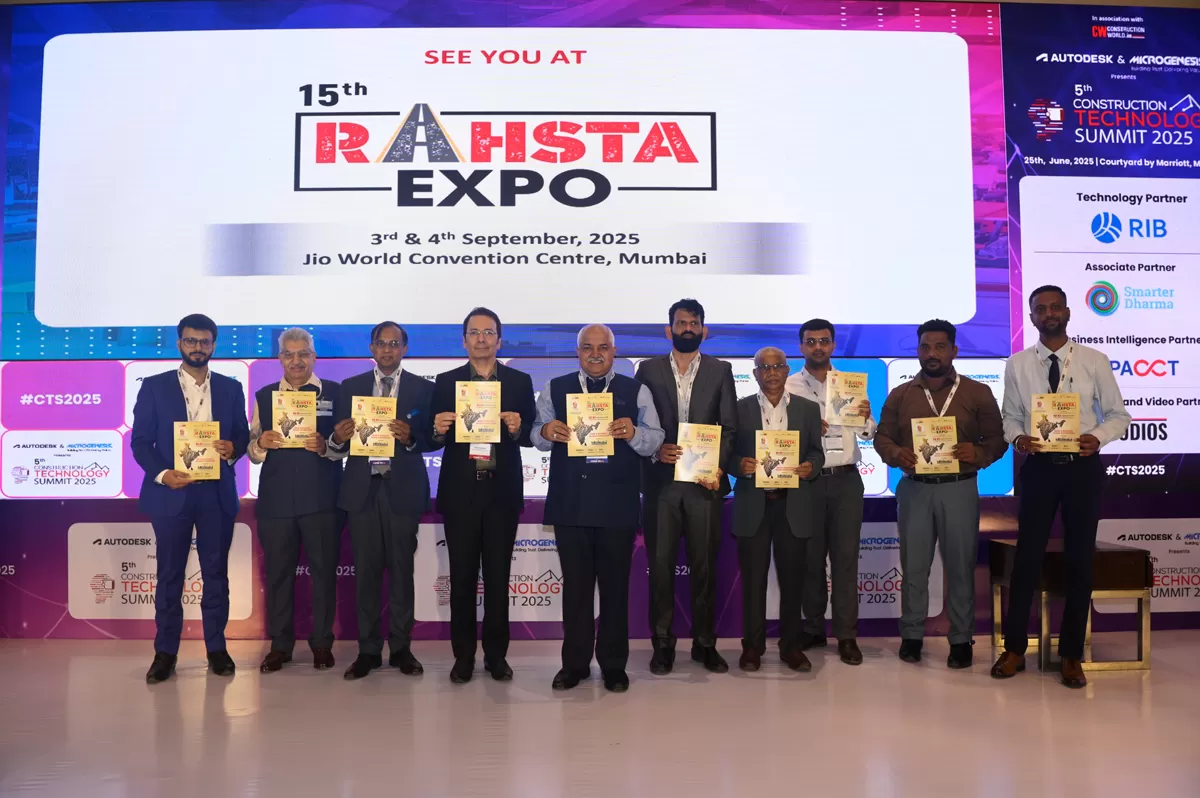
India’s Maha Kumbh of Road Construction
The RAHSTA Forum 2025, held on June 25 at Courtyard by Marriott, Mumbai, delivered powerful insights and dialogue on the future of India’s roads and highways sector. Organised by the FIRST Construction Council, the Forum served as the curtain-raiser to the much-anticipated RAHSTA Expo 2025, set to take place on 3rd and 4th September at the Jio Convention Centre, Mumbai.Union Minister of Roads Transport & Highways Shri Nitin Gadkari, while appreciating the efforts of FIRST Construction Council and ASAPP Info Global Group, commended the awards which recognise excellence across various..
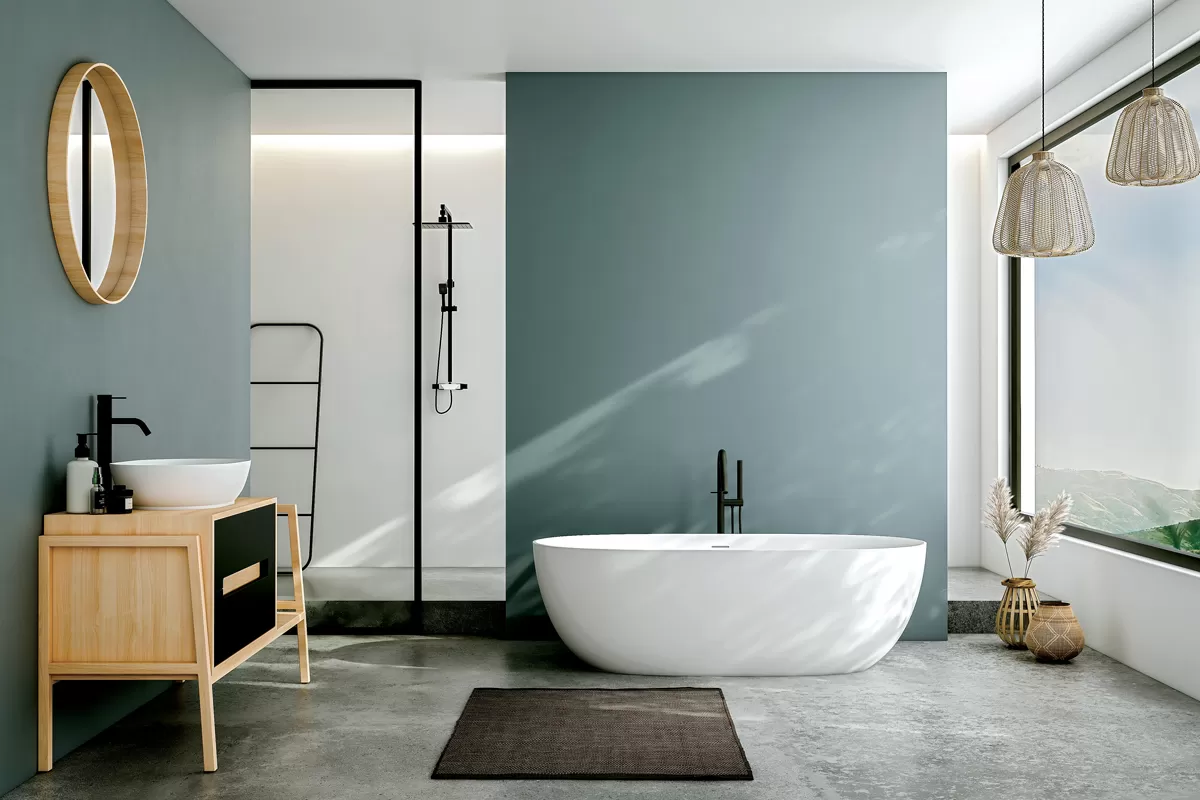
Built to Last, Designed to Impress
The construction and interior design industries stand at the confluence of functionality and aesthetics, where innovation powers the creation of enduring structures and inspiring spaces. At the heart of this process are materials and solutions that enable architects, designers, and builders to realise their visions with precision and reliability.Featuring iconic brands such as Fevicol—synonymous with adhesive solutions—Dr. Fixit, a complete waterproofing system renowned for addressing every critical area of construction, and Roff, a specialist in tile-fixing solutions, Pidilite has earned ..
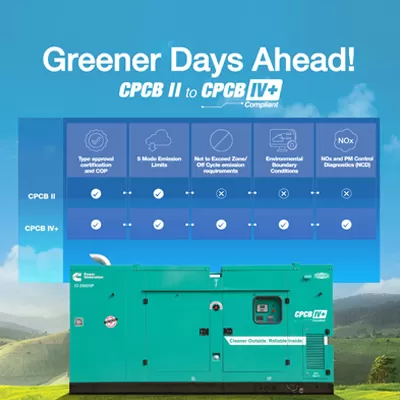
New Push to Cut India’s Air Pollution through Power Sector Reforms
In a significant stride toward environmental sustainability, Cummins India introduced CPCB IV+ compliant gensets to India on July 5, 2023, marking a paradigm shift in the power generation industry. These generators are engineered to adhere to the progressive emission norms set by the Ministry of Environment, Forest, and Climate Change. Being the first sets in the field, they have garnered praise for their remarkable achievements in emissions reduction and cutting-edge technology. Powerica, with its four-decade-long partnership with Cummins India Limited, is dedicated to consistently deliver th..