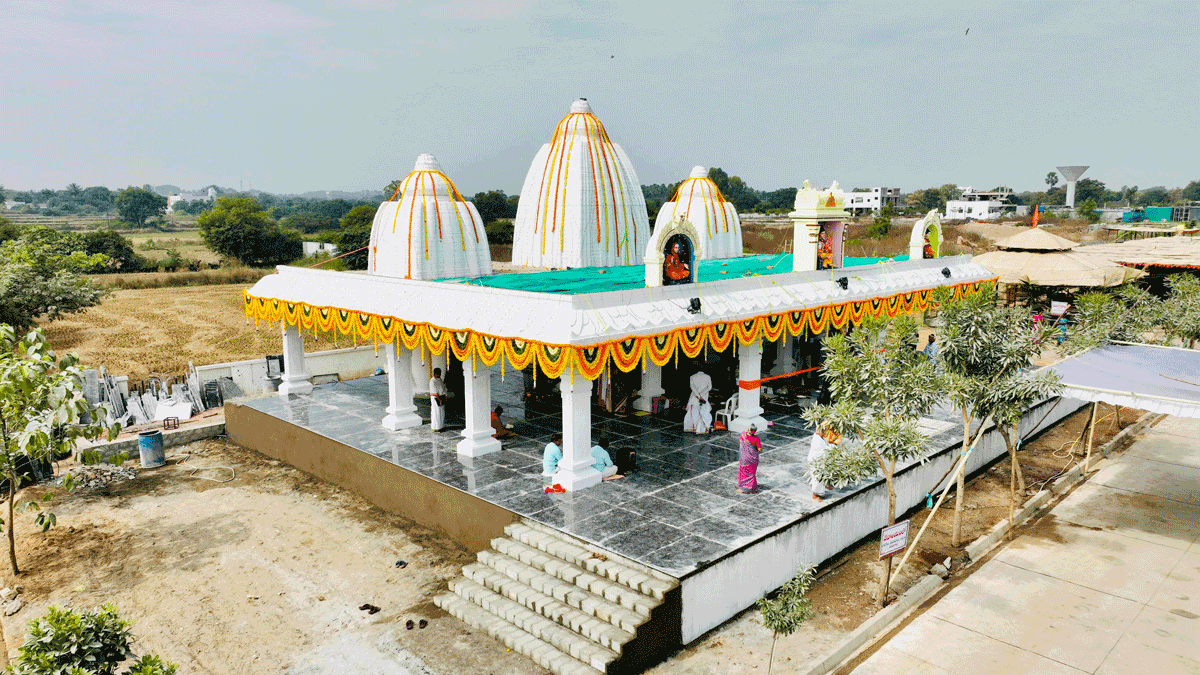
"Perfecting Your Public Speaking: Mastering the Art of Effective Communication"
Read full article
CW Gold Benefits
- Weekly Industry Updates
- Industry Feature Stories
- Premium Newsletter Access
- Building Material Prices (weekly) + trends/analysis
- Best Stories from our sister publications - Indian Cement Review, Equipment India, Infrastructure Today
- Sector focused Research Reports
- Sector Wise Updates (infrastructure, cement, equipment & construction) + trend analysis
- Exclusive text & video interviews
- Digital Delivery
- Financial Data for publically listed companies + Analysis
- Preconceptual Projects in the pipeline PAN India
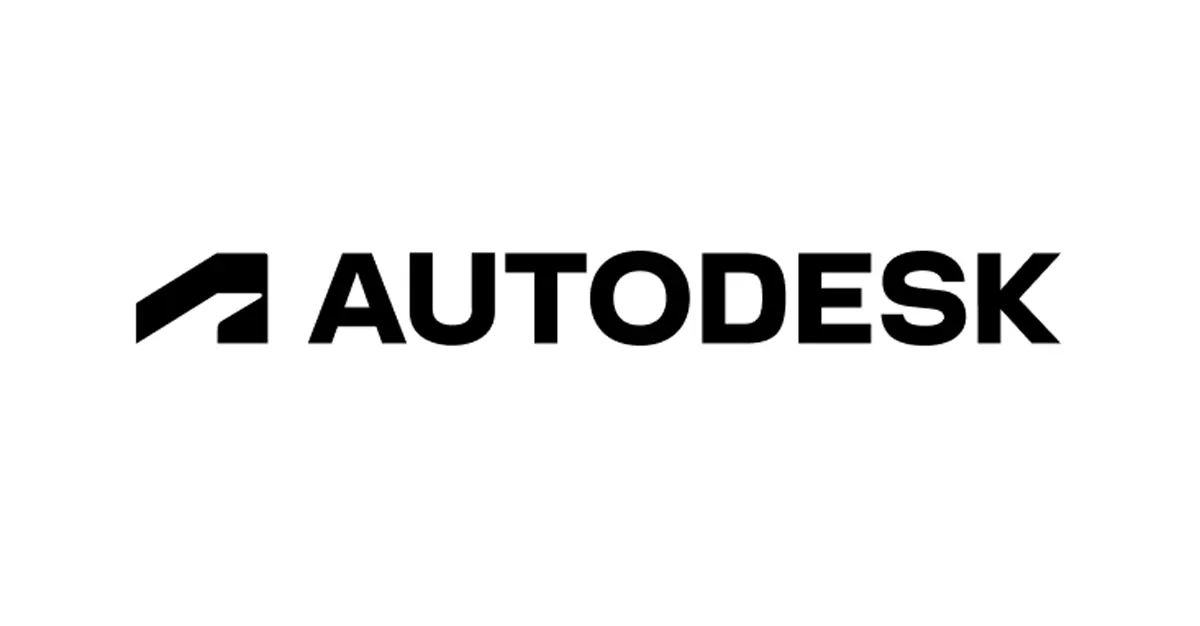
Rosatom Opens Pilot Uranium Facility at Tanzania’s Mkuju River Project
Mantra Tanzania, a subsidiary of Uranium One Group (part of Rosatom), has commissioned a pilot uranium processing facility at the Mkuju River project in southern Tanzania. The inauguration, attended by Her Excellency Samia Suluhu Hassan, President of the United Republic of Tanzania, alongside senior government officials, community leaders, and Rosatom representatives, marks a major step forward in Russia–Tanzania nuclear energy cooperation.Alexey Likhachev, Director General of Rosatom, said: “Rosatom offers its cutting-edge uranium processing technologies to unlock Tanzania’s geological ..
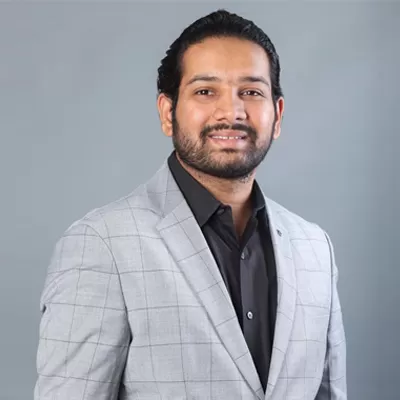
Enlight Metals Forays into Cable Tray Aggregation
Pune-based Enlight Metals, a leading metal aggregator, has entered the cable tray aggregation business, marking a strategic step in its evolution from raw material supplier to a comprehensive steel solutions provider. The move strengthens the company’s capability to deliver project-ready components for industries and infrastructure projects across India.Leveraging its strong sourcing network, OEM relationships, and deep industry knowledge, Enlight Metals will streamline procurement for electrical EPCs, renewable energy developers, industrial automation firms, and infrastructure contractors. ..
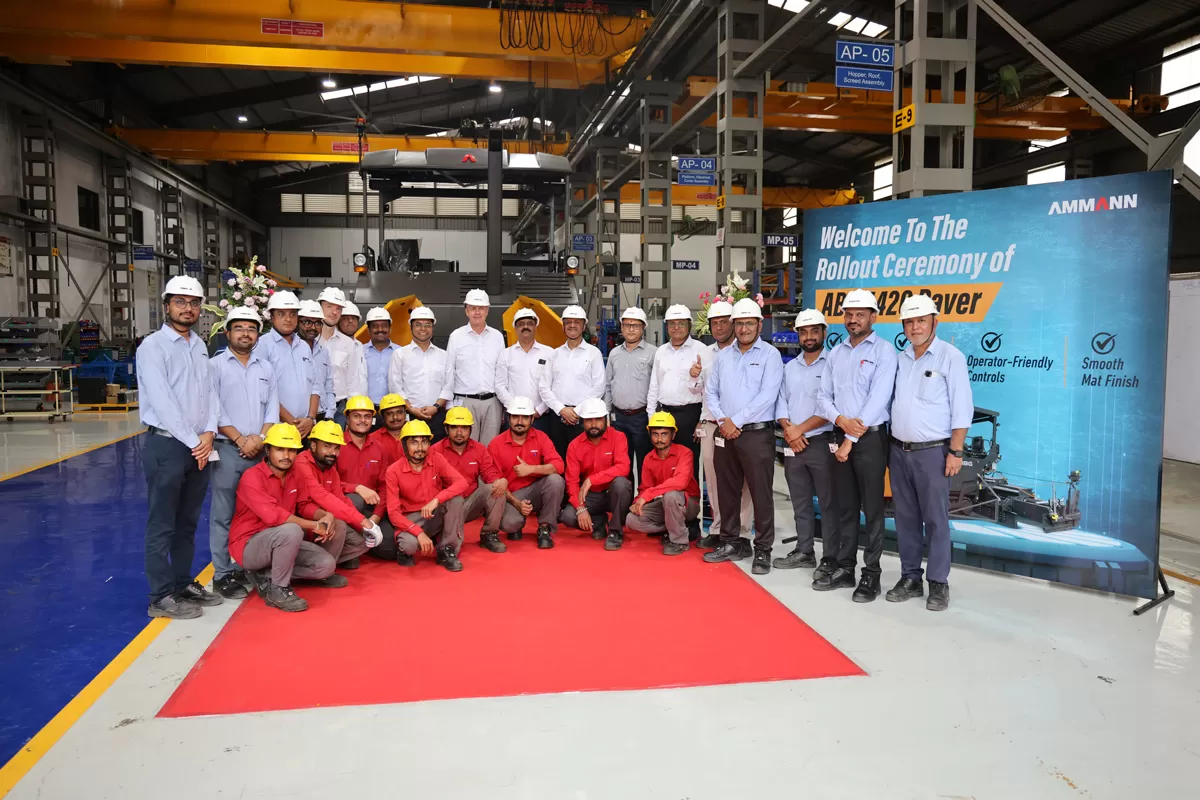
Ammann India Unveils First ABG Paver & New Parts Warehouse in Gujarat
Ammann India has marked a major milestone with the launch of its first locally assembled ABG 5420 Tracked Paver (Tier 3) from its new assembly line at the Ditasan manufacturing facility in Gujarat, alongside the inauguration of a high-tech ABG parts warehouse. These developments solidify Ammann India’s role in delivering advanced, localized road construction solutions for both domestic and export markets, aligned with the Government of India’s ‘Make in India for the World’ vision.The ceremonial roll-out was led by Bernd Holz, Executive Vice President, ABG General Management, and Dheera..