- Home
- Infrastructure Transport
- RAILWAYS & METRO RAIL
- Ticket to Ride!
Ticket to Ride!
Our capital city has proved to be a trendsetter. Major Indian cities are following the path shown by New Delhi, unrolling metro rail projects as a solution to the acute shortage of public transport systems in congested areas. For its part, the Government of India is actively encouraging all state capitals as well as other cities with a population of over 1 million to plan high-capacity public transport systems. It is offering equity participation and/or viability gap funding to the extent of 20 per cent of the capital cost of such projects to promote investments. Where projects are taken up as public-private partnerships (PPPs), it is providing up to 50 per cent of the project cost with the balance being met by the city development authority/state government and project developer.
Metro projects are appealing because of their large carrying capacity. A metro can carry more than 60,000 pphpd (people per hour per day) as against the 2,000 to 3,000 pphpd capacity of a regular bus or about 10,000 pphpd of a bus traversing a dedicated lane. But, as the outlay for metro projects is huge, the investment needs to be justified (see box). Questions are also being raised about whether PPPs - the preferred mode of developing metro rails - are really the best way forward while discussions abound about ways to make metro projects more financially viable.
Ownership models
What is the ideal ownership model for a metro rail? Should the infrastructure be owned by the government - the Centre or state, or both - in part or in whole? If so, should the operations and management of metros be outsourced to the private sector? Are there benefits associated with the private ownership of metros?
"The PPP concept, which is relatively new to India vis-à-vis overseas countries, best suits projects like a metro rail because the responsibility of the contractor who is executing the project is not limited to the construction period," says Bharat Modgil, Project Head, Mumbai Metro One Pvt Ltd. "Contractors become partners holding project equity and are focussed on minimising construction and lifecycle costs. In PPP projects, no compromises are made on the quality of construction to save on time and costs, thus resulting in world-class infrastructure benefiting the public and the country at large." In his view, PPP projects are preferable as they allow the government to channel limited resources for the betterment of the poor instead of investing in mega projects with long gestational periods.
While the PPP mode of development is being adopted for many infrastructure projects (not just metros) being rolled out in the Eleventh Plan, there has been mention of a blend between PPP and EPC contracts being adopted to significantly bring down the cost of development and operations and hence, benefit users and developers in turn. In India, the Delhi Metro Rail Corporation (DMRC) followed the PPP model only up to the award stage. After that, it adopted the EPC model. In contrast, the Metro-I and Metro-II in Mumbai and MRTS in Hyderabad are following the PPP model.
The benefits of the PPP model are believed to lie in enhanced quality and efficiency of infrastructure services. However, UW Hood, General Manager-Business Development-II, IRCON International Ltd, points out that the EPC mode has more inbuilt flexibility and can deliver high quality results, if the executing agency does not restrict itself to setting rules and takes bold decisions. For instance, some of the underground stations of DMRC were constructed using an innovative top-down method - the roof first and then the bottom - when hindrances were encountered during utility diversions and other problems. Besides, there is every possibility that the private player awarded the PPP contract underestimates project costs and overestimates revenues and resorts to cost-cutting on all possible fronts even at the cost of quality and safety.
Solving execution challenges
As the cost of funds raised by the private sector is higher than government borrowings, the PPP should deliver efficiency gains to offset the higher cost of finance. But, practical experience suggests otherwise; certain additions to the project cost offset the efficiency gains from the PPP. These include the additional cost of pre-tender feasibility studies and legal documentation, higher margins and contingencies to cover the risks associated with project completion, land acquisition delays, cost for international partners in JVs, higher training costs, and payments to international project management consultants.
Concerns arise from the significant difference in project cost under the two models. While PPP road contracts are said to be higher than EPC contracts by about one-fifth, in the case of railway projects, the price rise has been estimated to be as high as 75 to 100 per cent. Metro rail projects could therefore adopt the PPP model to cover the creation of fixed assets and maintenance and the EPC model for mobile assets and operations, which are complex, to deliver savings in O&M cost and thereby eliminate VGF (Viability Gap Funding) subsidies and reduce fares. According to Hood, "If the infrastructure is owned either by the Central or state governments or a separate government entity formed for the purpose, the construction of the infrastructure could be done by the owner under the EPC model, and the operation and maintenance could be outsourced to a private agency to allow the owner to cut down on overheads and liabilities. When the ownership lies with the government, delays and problems associated with land acquisition, utility diversion and permissions from various bodies can be solved in short order. In contrast, private players might be compelled to resort to inappropriate means to solve such issues. Alternatively, the job could be executed on a PPP basis by a private player with the responsibility of land acquisition and permission resting with the government body."
The fact remains that executing metros in large cities is no mean feat. According to Mohan Lal Gupta, Divisional Director, Metros & Railways, Mott MacDonald India, "Incomplete project data presents a huge challenge for both metro project designers and contractors. Receiving incorrect or incomplete geotechnical information and underground city utilities can cause significant delays in project execution as well as disrupt cost estimates - more so, when these challenges are seen in the light of the extremely unrealistic time schedules imposed for project completion. Delays also occur because the project's detailed designs tend to commence when the contractor is at site ready for construction."
To cite a practical example of how some of these delays practically affect the execution of metro projects, Mumbai Metro-I is facing significant challenges in implementing the project on account of existing utility infrastructure and city congestion. Some of the problems include delays in receiving Right of Way (RoW), working in narrow and highly congested areas and corridors with traffic diversions and barricading, restricted working hours on account of traffic clearances, and circumnavigating a complex network of underground utilities and planning around over-ground structures and encroachments.
Construction-related challenges include the acute shortage of adequately skilled manpower and quality construction materials like river sand and steel, and obtaining numerous approvals from agencies such as the traffic, BMC, Railways, etc. Challenges testing the core competency of the construction team include construction at a height of 21 m, by way of a large cable-stayed bridge over the Western Express Highway. Similarly, the corridor has been forced to traverse an extremely high section of the busy Western Railways tracks by way of a major steel bridge. At this section, the frequency of trains is about 90 seconds. What's more, the availability of a block on the power lines is limited to two to three hours at night when
the company faces noise level restrictions as well.
Towards greater financial viability
The four critical elements determining the financial viability of a metro rail project are the concession period, passenger volumes, user fees, and revenue from real-estate and capital cost. The first three of these four parameters are virtually predetermined but may be managed somewhat to improve project viability. VB Gadgil, Chief Executive and Managing Director, L&T Metro Rail (Hyderabad) Ltd, shares some methods that may be adopted to ensure that a metro project stays cost-effective. The concession period for such capital-intensive projects usually varies between 50 and 60 years, which helps immensely. Passenger volumes are seen to rise gradually over time and, therefore, considered beyond the control of the concessionaire. But, Gadgil believes that the initial gestimate time not only decides the volume but also the pattern of ridership critical to the success of the project.
Further, although user fees must be competitive to maximise usage, Gadgil suggests fixing these with an escalation formula connected with price indices. Revenue from commercial real-estate developments above metro facilities such as depots, parking and circulation areas at select stations is allied income for the concessionaire and, hence, such development rights are much sought after as capital subsidies alone may not suffice in meeting the gap in operational expenses. While agreeing that real-estate rentals are extremely critical for the viability of a project, Gadgil avers that these are extremely difficult to manage. "Rentals depend on the external environment that will boost city development," he says. "They should be futuristic and well maintainable to get the upside of rentals even when the upside of land price is not available. Developers must also consider that large real-estate volumes cannot be dumped in a city that has its own appetite for consumption of commercial space."
"Properties around a metro station should not be randomly allowed to be developed to augment the operational income of metro project concessionaires," agrees Gupta. "Developing commercial shopping complexes or hotels on the upper levels of city stations situated in congested areas would be extremely detrimental to the city fabric. Such rights must take into account the social fabric, available approaches and culture."
Consequently, capital cost becomes the variable that can significantly determine the financial viability of a metro rail project. Adopting cost-effective specifications as well as phasing of project components helps reduce capital costs and improve viability.
Here too, Gadgil cautions against going overboard the containment and phasing out of capital cost structuring. "One aims at creating a metro system that is fit for purpose and at the same time benchmarked with the best global practices for safety and quality," he emphasises.
Lowering capital costs
For his part, Parvesh Minocha, Managing Director, Transportation Advisory & Engineering Division, Feedback Infrastructure Services Pvt Ltd, says, "Well-designed cost-reduction strategies can reduce project costs by 15 to 20 per cent over their lifecycle." Citing a few measures to reduce costs, he first suggests that contract management should shift from following a unilateral paradigm favouring the client in case of disputes to a more flexible and transparent paradigm. While the former method results in higher risk loading by contractors, the latter distributes risks and rewards more evenly. It also helps if concessionaires adopt a 'project management' driven approach, especially during the construction phase with execution responsibilities handed over to contractors.
The standardisation of designs across project components like viaducts, piers, foundations and stations is another way to reduce costs, as is keeping designs utilitarian and efficient with minimal 'grandiosity'. Over-design depending on the geography and location of the site can be avoided by studying design standards guiding structural safety. General consultancy charges can be brought down by hiring the bare minimum international expertise and adopting a 'fixed-price' rather than a 'time-spent' approach for fee payments. Efficient planning can minimise land acquisition requirements and, hence, associated costs. One should negotiate with state agencies to get state-owned land at subsidised rates. Rolling stock manufactured in the country is less expensive than imported components. Maintenance costs after the defect liability period have also reduced. Adopting advanced signalling and train operation systems is a worthy investment and improves efficiency and passenger moving capacities through lesser cars and other infrastructure. From the point of view of employers, Minocha proposes awarding 'design-build' contracts to a single entity instead of splitting contracts to two or even more agencies as the latter creates client-consultant-contractor coordination issues.
"Adopting these measures would help newer concessionaires avoid the pitfalls of cost underestimation - a global phenomenon rooted in political, social and financial causes with the underlying objective of 'kick-starting' the project initially," he adds. "While this cannot be overcome in totality, resulting in cost overruns at the audit and review stage, newer metros can learn significantly from Delhi Metro's experience to reduce the cost of metro implementation."
Ensuring better outcomes
Cost-effective specifications can help reduce metro project capital costs, but these should not be minimised beyond a point. Speaking about the recent trend to submit very low bids for metro projects, which creates the risk of reducing the quality of the created infrastructure, Gupta says, "There can be no doubt that cutthroat competition led to these submissions. The blind acceptance of the lowest bid, without establishing the reasons, could increase risks to qualitative output. It should be checked back knowing that it is impossible to execute a project to exacting standards without incurring a certain minimum cost."
When bid prices are too low, developers tend to miss out on the finer aspects of the metro services. "This is undesirable," he adds. "After all, people do not use the basic construction. They use the facilities and services added to the base. Whether it is railways, signage, evacuation, safety or services, they all have a high impact on the design of metros and eventual usability. Indian metro owners and developers are yet to show commitment in investing in world-class services."
According to Gupta, "The outcome of metro projects could also improve if the credentials of the people proposed to execute the project are reviewed more thoroughly. While the specifications of the organisations are studied in detail, the CVs of the people who will practically do the work should be given the same importance."
Bonanza for material vendors
Irrespective of the issues surrounding the design and construction of metros, projects unrolled in the past five years are widening the market for companies certified to supply metro rail components. Achal Puri, AGM - Marketing, JSL Architecture (formerly known as Jindal Architecture), estimates that the Delhi, Hyderabad, Mumbai and Chennai metro projects will generate demand for over 1,000 cars in the coming three to five years alone. This will open up new opportunities for established players.
"We are already supplying battery boxes, mounting and lifting beams and roofing and floor components to Bombardier and BEML," he says. "Recently, we have started supplying grab poles to Bombardier as well, which makes us the only source for grab poles supplies such that any pole used in any of the newer metro projects in India would be made in the JSL Architecture unit near Manesar-Gurgaon. This establishes our quality and delivery credentials for entering the European and other international markets. It also marks a major shift in the market as the component was previously being imported from China." JSL Architecture will also be supplying the 22-m-long cant rail components to Bombardier for which a new line is being set up at the company's Manesar plant.
"With the Government of India encouraging cities with a population above 3 million to develop mass transit systems, demand is set to expand," observes Harsh Mehta, Director, Communications, Bombardier Transportation India. "We foresee an available market volume of about 2,000 metro cars in the next five years in India to meet the expanding demand," he continues.
Starting with the order to equip the 23.5 km Line 3 of the Delhi Metro with an automatic train control signalling and communications system, Siemens has been making the most of the emerging opportunities to equip metro rails with energy-efficient signalling, communication, surveillance, supervision, monitoring and electrification systems. For the Rapid Metro Rail Gurgaon Ltd project, Siemens Mobility, for the first time in India, supplied not only the sub-systems but also assumed responsibility for the key components and their integration, including the interfaces, for the construction of a complete system as well as the supply of five three-car metro coaches with aluminium design.
According to Tilakraj Seth, Sector Cluster Lead, South Asia, Infrastructure & Cities, Siemens Ltd, "Increasing urbanisation and the resulting rise in traffic volumes in cities as well as the need to protect the environment and minimise climate change are fuelling the demand for more eco-friendly mobility solutions. National census figures indicate that India has 40 cities with a population of over 1 million, the threshold limit over which a metro project is viable. As metros are increasingly being seen as environment-friendly transport modes, town planners are turning to metro rails as solutions for the transport woes of city-dwellers."
Siemens Mobility has major metro projects in its kitty. The Mumbai Metro will feature the latest signalling technology from Siemens for the 12-km, east-west corridor constituting the first phase, including automatic train protection system (ATPS) and automated signalling to control the high volume of train movements. Siemens has also been awarded two more contracts by Chennai Metro Rail Ltd: one involves the supply of power to stations, air-conditioning, tunnel ventilation, lighting and other utilities at the stations and overhead equipment; the second is a design and build contract for signalling, platform screen doors and telecommunications. In Kolkata, Siemens Mobility has won an order to supply the complete railway electrification system for the new east-west metro line spanning 8.9 km and serving six stations. Part of the line will run in a tunnel below the Hooghly, making it the first underwater metro line in India.
With city congestion peaking in metros across the country, Sreedhara Narayanan, General Manager, Casagrande India, is of the opinion that construction for underground stations will become more popular, thus paving the way for higher sales of foundation equipment. Casagrande is already providing reliable and safe equipment for the execution of water-tight, strong diaphragm walls and special equipment for shafts where tunnel boring machines (TBMs) can be inserted. Several Casagrande KRC rigs are being used by Valecha Engineering, Afcons and IPEX at different construction sites of the Chennai Metro underground stations. Also, a number of the company's rigs are carrying out geotechnical works at construction sites of the Kolkata Metro for Afcons.
Product innovations
With energy accounting for the biggest chunk of the operational costs of metro rail operators around the world, the need for energy-saving rolling stock cannot be over-emphasised. In consideration of Bombardier's best-in-class, energy-saving technologies make sound economical sense. "The Bombardier ECO4 portfolio boasts of reliable energy, efficiency, economy and ecology-friendly technologies," says Mehta. "Our flexible, reliable and easy-to-maintain modular mass transit vehicles are also fully customisable (structure and body shell) to help meet the present and future needs of each rail system."
In India, Bombardier manufactures all the key electrical and mechanical components used in railway vehicles at its Savli site, making it the first wholly-owned plant of a foreign multinational company with the capacity to manufacture complete railway vehicles including bogies, car body production units, a final assembly area, most advanced rail equipment tog-ether with R&D and training centres. Bombardier's MITRAC propulsion system with regenerative braking can generate up to 30 per cent in energy savings. This system has enabled the DMRC (from whom Bombardier has an order of 614 MOVIA metro cars, of which it has already delivered over 500) to become the first railway project to be registered by the
UN Framework Convention on Climate Change. In May 2011, DMRC earned over Rs 20 million for selling carbon credits.
According to Puri, the stainless steel used by JSL Architecture as an input material to manufacture metro components is a preferred material because it is environment-friendly (100 per cent recyclable), economical (vis-à-vis its long life), requires minimal maintenance, and is non-polluting and hygienic. In comparison, high-strength aluminium used in coaches is not recyclable because of its iron content. A more aesthetic, ceramic, hard-coated stainless steel is also available for interior panelling, partitioning, flooring and other inner decorative applications. This has better resistance to temperature and corrosion and is easy to clean.
Besides green components, Seth points out that customers are also open to innovative new features, which is helping the market to grow the market some more. For instance, alongside the signalling and interlocking technology and electrification of the 23 km Airport Metro Express Line in New Delhi, Siemens Mobility has supplied the line the Sibag train baggage-handling system. "Passengers travelling to the airport now have the option to check in their baggage at the metro stations at New Delhi City Airport Terminal Station and Shivaji Stadium City Airport Terminal Station," he explains. "Passengers can pick up their boarding cards, ride the Airport Express to the international airport and proceed straight to the security check and departure gate. The automatic handling system located on the station platform uses a conveyor system to take the containerised baggage through the automatic security check and onto the connecting plane."
Beyond doubt, with the slew of equipment on offer, Indian metros are bound to reduce transit times in congested city corridors. Here's to happy riding!
Metro: Yes or No?
The choice of a transport mode depends on the length and number of corridors needing mass transit systems, their projected future demand and suitability for the possible modes, and the feasibility of introducing the desired mode based on a lifecycle cost analysis. Rail transit is beyond doubt more efficient than buses. The passenger capacity of a rail coach is thrice that of a bus. The life of the coach is also thrice that of a bus. So, although the initial cost of light rail transit is high, it is nine times more efficient than a bus. Still, city planning authorities should not jump to opt for metro rails as the backbone of the urban transport system.
Metros are associated with a very high-capacity mode that may only be required in high-density corridors in mega cities. If light rail transit (LRT) modes can adequately meet the demand in medium-size cities or in other corridors in mega cities, they should be preferred as they are less capital intensive than metros. LRT requires lighter structures and mandates less ongoing expenditure on traction energy. It also necessitates less acquisition of roadside property, which is of significant importance considering that the scarcity of land for metro rail-related activities, challenges involved in fixing the price of the land, the need for measures such as transferable development rights to motivate sellers to part with land, and the delays in handing over land to contractors are major hurdles in many infrastructure projects. The projected cost of Phase III of the Delhi Metro Rail is approximately Rs 300 crore per km, at the very least. As it is, even where the huge investment on a metro can be justified, authorities must take steps to link the metro line with other public transport systems to maximise the utilisation of the capital outlay.
Give us your comments on this article at feedback@ASAPPmedia.com
- New Delhi
- metro rail projects
- transport system
- Government of India
- PPPs
- investment
- infrastructure
- Bharat Modgil
- Mumbai Metro One Pvt Ltd
- EPC contracts
- DMRC
- VGF
- O&M cost
- Mohan Lal Gupta
- Mott MacDonald India
- VB Gadgil
- L&T Metro Rail Ltd
- real estate
- project management
- Delhi Metro
- BEML
- Bombardier
- Manesar
- ATPS
- Mumbai Metro
As metro projects get underway in leading Indian cities, the public looks forward to the new mode of transport. By adding to the experience of owners and developers, each project is also helping to shape the future of metro rail contracts, finds Charu Bahri.Our capital city has proved to be a trendsetter. Major Indian cities are following the path shown by New Delhi, unrolling metro rail projects as a solution to the acute shortage of public transport systems in congested areas. For its part, the Government of India is actively encouraging all state capitals as well as other cities with a population of over 1 million to plan high-capacity public transport systems. It is offering equity participation and/or viability gap funding to the extent of 20 per cent of the capital cost of such projects to promote investments. Where projects are taken up as public-private partnerships (PPPs), it is providing up to 50 per cent of the project cost with the balance being met by the city development authority/state government and project developer.Metro projects are appealing because of their large carrying capacity. A metro can carry more than 60,000 pphpd (people per hour per day) as against the 2,000 to 3,000 pphpd capacity of a regular bus or about 10,000 pphpd of a bus traversing a dedicated lane. But, as the outlay for metro projects is huge, the investment needs to be justified (see box). Questions are also being raised about whether PPPs - the preferred mode of developing metro rails - are really the best way forward while discussions abound about ways to make metro projects more financially viable.Ownership modelsWhat is the ideal ownership model for a metro rail? Should the infrastructure be owned by the government - the Centre or state, or both - in part or in whole? If so, should the operations and management of metros be outsourced to the private sector? Are there benefits associated with the private ownership of metros?The PPP concept, which is relatively new to India vis-à-vis overseas countries, best suits projects like a metro rail because the responsibility of the contractor who is executing the project is not limited to the construction period, says Bharat Modgil, Project Head, Mumbai Metro One Pvt Ltd. Contractors become partners holding project equity and are focussed on minimising construction and lifecycle costs. In PPP projects, no compromises are made on the quality of construction to save on time and costs, thus resulting in world-class infrastructure benefiting the public and the country at large. In his view, PPP projects are preferable as they allow the government to channel limited resources for the betterment of the poor instead of investing in mega projects with long gestational periods.While the PPP mode of development is being adopted for many infrastructure projects (not just metros) being rolled out in the Eleventh Plan, there has been mention of a blend between PPP and EPC contracts being adopted to significantly bring down the cost of development and operations and hence, benefit users and developers in turn. In India, the Delhi Metro Rail Corporation (DMRC) followed the PPP model only up to the award stage. After that, it adopted the EPC model. In contrast, the Metro-I and Metro-II in Mumbai and MRTS in Hyderabad are following the PPP model.The benefits of the PPP model are believed to lie in enhanced quality and efficiency of infrastructure services. However, UW Hood, General Manager-Business Development-II, IRCON International Ltd, points out that the EPC mode has more inbuilt flexibility and can deliver high quality results, if the executing agency does not restrict itself to setting rules and takes bold decisions. For instance, some of the underground stations of DMRC were constructed using an innovative top-down method - the roof first and then the bottom - when hindrances were encountered during utility diversions and other problems. Besides, there is every possibility that the private player awarded the PPP contract underestimates project costs and overestimates revenues and resorts to cost-cutting on all possible fronts even at the cost of quality and safety.Solving execution challengesAs the cost of funds raised by the private sector is higher than government borrowings, the PPP should deliver efficiency gains to offset the higher cost of finance. But, practical experience suggests otherwise; certain additions to the project cost offset the efficiency gains from the PPP. These include the additional cost of pre-tender feasibility studies and legal documentation, higher margins and contingencies to cover the risks associated with project completion, land acquisition delays, cost for international partners in JVs, higher training costs, and payments to international project management consultants.Concerns arise from the significant difference in project cost under the two models. While PPP road contracts are said to be higher than EPC contracts by about one-fifth, in the case of railway projects, the price rise has been estimated to be as high as 75 to 100 per cent. Metro rail projects could therefore adopt the PPP model to cover the creation of fixed assets and maintenance and the EPC model for mobile assets and operations, which are complex, to deliver savings in O&M cost and thereby eliminate VGF (Viability Gap Funding) subsidies and reduce fares. According to Hood, If the infrastructure is owned either by the Central or state governments or a separate government entity formed for the purpose, the construction of the infrastructure could be done by the owner under the EPC model, and the operation and maintenance could be outsourced to a private agency to allow the owner to cut down on overheads and liabilities. When the ownership lies with the government, delays and problems associated with land acquisition, utility diversion and permissions from various bodies can be solved in short order. In contrast, private players might be compelled to resort to inappropriate means to solve such issues. Alternatively, the job could be executed on a PPP basis by a private player with the responsibility of land acquisition and permission resting with the government body.The fact remains that executing metros in large cities is no mean feat. According to Mohan Lal Gupta, Divisional Director, Metros & Railways, Mott MacDonald India, Incomplete project data presents a huge challenge for both metro project designers and contractors. Receiving incorrect or incomplete geotechnical information and underground city utilities can cause significant delays in project execution as well as disrupt cost estimates - more so, when these challenges are seen in the light of the extremely unrealistic time schedules imposed for project completion. Delays also occur because the project's detailed designs tend to commence when the contractor is at site ready for construction.To cite a practical example of how some of these delays practically affect the execution of metro projects, Mumbai Metro-I is facing significant challenges in implementing the project on account of existing utility infrastructure and city congestion. Some of the problems include delays in receiving Right of Way (RoW), working in narrow and highly congested areas and corridors with traffic diversions and barricading, restricted working hours on account of traffic clearances, and circumnavigating a complex network of underground utilities and planning around over-ground structures and encroachments.Construction-related challenges include the acute shortage of adequately skilled manpower and quality construction materials like river sand and steel, and obtaining numerous approvals from agencies such as the traffic, BMC, Railways, etc. Challenges testing the core competency of the construction team include construction at a height of 21 m, by way of a large cable-stayed bridge over the Western Express Highway. Similarly, the corridor has been forced to traverse an extremely high section of the busy Western Railways tracks by way of a major steel bridge. At this section, the frequency of trains is about 90 seconds. What's more, the availability of a block on the power lines is limited to two to three hours at night when the company faces noise level restrictions as well.Towards greater financial viabilityThe four critical elements determining the financial viability of a metro rail project are the concession period, passenger volumes, user fees, and revenue from real-estate and capital cost. The first three of these four parameters are virtually predetermined but may be managed somewhat to improve project viability. VB Gadgil, Chief Executive and Managing Director, L&T Metro Rail (Hyderabad) Ltd, shares some methods that may be adopted to ensure that a metro project stays cost-effective. The concession period for such capital-intensive projects usually varies between 50 and 60 years, which helps immensely. Passenger volumes are seen to rise gradually over time and, therefore, considered beyond the control of the concessionaire. But, Gadgil believes that the initial gestimate time not only decides the volume but also the pattern of ridership critical to the success of the project.Further, although user fees must be competitive to maximise usage, Gadgil suggests fixing these with an escalation formula connected with price indices. Revenue from commercial real-estate developments above metro facilities such as depots, parking and circulation areas at select stations is allied income for the concessionaire and, hence, such development rights are much sought after as capital subsidies alone may not suffice in meeting the gap in operational expenses. While agreeing that real-estate rentals are extremely critical for the viability of a project, Gadgil avers that these are extremely difficult to manage. Rentals depend on the external environment that will boost city development, he says. They should be futuristic and well maintainable to get the upside of rentals even when the upside of land price is not available. Developers must also consider that large real-estate volumes cannot be dumped in a city that has its own appetite for consumption of commercial space.Properties around a metro station should not be randomly allowed to be developed to augment the operational income of metro project concessionaires, agrees Gupta. Developing commercial shopping complexes or hotels on the upper levels of city stations situated in congested areas would be extremely detrimental to the city fabric. Such rights must take into account the social fabric, available approaches and culture.Consequently, capital cost becomes the variable that can significantly determine the financial viability of a metro rail project. Adopting cost-effective specifications as well as phasing of project components helps reduce capital costs and improve viability.Here too, Gadgil cautions against going overboard the containment and phasing out of capital cost structuring. One aims at creating a metro system that is fit for purpose and at the same time benchmarked with the best global practices for safety and quality, he emphasises.Lowering capital costsFor his part, Parvesh Minocha, Managing Director, Transportation Advisory & Engineering Division, Feedback Infrastructure Services Pvt Ltd, says, Well-designed cost-reduction strategies can reduce project costs by 15 to 20 per cent over their lifecycle. Citing a few measures to reduce costs, he first suggests that contract management should shift from following a unilateral paradigm favouring the client in case of disputes to a more flexible and transparent paradigm. While the former method results in higher risk loading by contractors, the latter distributes risks and rewards more evenly. It also helps if concessionaires adopt a 'project management' driven approach, especially during the construction phase with execution responsibilities handed over to contractors.The standardisation of designs across project components like viaducts, piers, foundations and stations is another way to reduce costs, as is keeping designs utilitarian and efficient with minimal 'grandiosity'. Over-design depending on the geography and location of the site can be avoided by studying design standards guiding structural safety. General consultancy charges can be brought down by hiring the bare minimum international expertise and adopting a 'fixed-price' rather than a 'time-spent' approach for fee payments. Efficient planning can minimise land acquisition requirements and, hence, associated costs. One should negotiate with state agencies to get state-owned land at subsidised rates. Rolling stock manufactured in the country is less expensive than imported components. Maintenance costs after the defect liability period have also reduced. Adopting advanced signalling and train operation systems is a worthy investment and improves efficiency and passenger moving capacities through lesser cars and other infrastructure. From the point of view of employers, Minocha proposes awarding 'design-build' contracts to a single entity instead of splitting contracts to two or even more agencies as the latter creates client-consultant-contractor coordination issues.Adopting these measures would help newer concessionaires avoid the pitfalls of cost underestimation - a global phenomenon rooted in political, social and financial causes with the underlying objective of 'kick-starting' the project initially, he adds. While this cannot be overcome in totality, resulting in cost overruns at the audit and review stage, newer metros can learn significantly from Delhi Metro's experience to reduce the cost of metro implementation.Ensuring better outcomesCost-effective specifications can help reduce metro project capital costs, but these should not be minimised beyond a point. Speaking about the recent trend to submit very low bids for metro projects, which creates the risk of reducing the quality of the created infrastructure, Gupta says, There can be no doubt that cutthroat competition led to these submissions. The blind acceptance of the lowest bid, without establishing the reasons, could increase risks to qualitative output. It should be checked back knowing that it is impossible to execute a project to exacting standards without incurring a certain minimum cost.When bid prices are too low, developers tend to miss out on the finer aspects of the metro services. This is undesirable, he adds. After all, people do not use the basic construction. They use the facilities and services added to the base. Whether it is railways, signage, evacuation, safety or services, they all have a high impact on the design of metros and eventual usability. Indian metro owners and developers are yet to show commitment in investing in world-class services.According to Gupta, The outcome of metro projects could also improve if the credentials of the people proposed to execute the project are reviewed more thoroughly. While the specifications of the organisations are studied in detail, the CVs of the people who will practically do the work should be given the same importance.Bonanza for material vendorsIrrespective of the issues surrounding the design and construction of metros, projects unrolled in the past five years are widening the market for companies certified to supply metro rail components. Achal Puri, AGM - Marketing, JSL Architecture (formerly known as Jindal Architecture), estimates that the Delhi, Hyderabad, Mumbai and Chennai metro projects will generate demand for over 1,000 cars in the coming three to five years alone. This will open up new opportunities for established players.We are already supplying battery boxes, mounting and lifting beams and roofing and floor components to Bombardier and BEML, he says. Recently, we have started supplying grab poles to Bombardier as well, which makes us the only source for grab poles supplies such that any pole used in any of the newer metro projects in India would be made in the JSL Architecture unit near Manesar-Gurgaon. This establishes our quality and delivery credentials for entering the European and other international markets. It also marks a major shift in the market as the component was previously being imported from China. JSL Architecture will also be supplying the 22-m-long cant rail components to Bombardier for which a new line is being set up at the company's Manesar plant.With the Government of India encouraging cities with a population above 3 million to develop mass transit systems, demand is set to expand, observes Harsh Mehta, Director, Communications, Bombardier Transportation India. We foresee an available market volume of about 2,000 metro cars in the next five years in India to meet the expanding demand, he continues.Starting with the order to equip the 23.5 km Line 3 of the Delhi Metro with an automatic train control signalling and communications system, Siemens has been making the most of the emerging opportunities to equip metro rails with energy-efficient signalling, communication, surveillance, supervision, monitoring and electrification systems. For the Rapid Metro Rail Gurgaon Ltd project, Siemens Mobility, for the first time in India, supplied not only the sub-systems but also assumed responsibility for the key components and their integration, including the interfaces, for the construction of a complete system as well as the supply of five three-car metro coaches with aluminium design.According to Tilakraj Seth, Sector Cluster Lead, South Asia, Infrastructure & Cities, Siemens Ltd, Increasing urbanisation and the resulting rise in traffic volumes in cities as well as the need to protect the environment and minimise climate change are fuelling the demand for more eco-friendly mobility solutions. National census figures indicate that India has 40 cities with a population of over 1 million, the threshold limit over which a metro project is viable. As metros are increasingly being seen as environment-friendly transport modes, town planners are turning to metro rails as solutions for the transport woes of city-dwellers.Siemens Mobility has major metro projects in its kitty. The Mumbai Metro will feature the latest signalling technology from Siemens for the 12-km, east-west corridor constituting the first phase, including automatic train protection system (ATPS) and automated signalling to control the high volume of train movements. Siemens has also been awarded two more contracts by Chennai Metro Rail Ltd: one involves the supply of power to stations, air-conditioning, tunnel ventilation, lighting and other utilities at the stations and overhead equipment; the second is a design and build contract for signalling, platform screen doors and telecommunications. In Kolkata, Siemens Mobility has won an order to supply the complete railway electrification system for the new east-west metro line spanning 8.9 km and serving six stations. Part of the line will run in a tunnel below the Hooghly, making it the first underwater metro line in India.With city congestion peaking in metros across the country, Sreedhara Narayanan, General Manager, Casagrande India, is of the opinion that construction for underground stations will become more popular, thus paving the way for higher sales of foundation equipment. Casagrande is already providing reliable and safe equipment for the execution of water-tight, strong diaphragm walls and special equipment for shafts where tunnel boring machines (TBMs) can be inserted. Several Casagrande KRC rigs are being used by Valecha Engineering, Afcons and IPEX at different construction sites of the Chennai Metro underground stations. Also, a number of the company's rigs are carrying out geotechnical works at construction sites of the Kolkata Metro for Afcons.Product innovationsWith energy accounting for the biggest chunk of the operational costs of metro rail operators around the world, the need for energy-saving rolling stock cannot be over-emphasised. In consideration of Bombardier's best-in-class, energy-saving technologies make sound economical sense. The Bombardier ECO4 portfolio boasts of reliable energy, efficiency, economy and ecology-friendly technologies, says Mehta. Our flexible, reliable and easy-to-maintain modular mass transit vehicles are also fully customisable (structure and body shell) to help meet the present and future needs of each rail system.In India, Bombardier manufactures all the key electrical and mechanical components used in railway vehicles at its Savli site, making it the first wholly-owned plant of a foreign multinational company with the capacity to manufacture complete railway vehicles including bogies, car body production units, a final assembly area, most advanced rail equipment tog-ether with R&D and training centres. Bombardier's MITRAC propulsion system with regenerative braking can generate up to 30 per cent in energy savings. This system has enabled the DMRC (from whom Bombardier has an order of 614 MOVIA metro cars, of which it has already delivered over 500) to become the first railway project to be registered by the UN Framework Convention on Climate Change. In May 2011, DMRC earned over Rs 20 million for selling carbon credits.According to Puri, the stainless steel used by JSL Architecture as an input material to manufacture metro components is a preferred material because it is environment-friendly (100 per cent recyclable), economical (vis-à-vis its long life), requires minimal maintenance, and is non-polluting and hygienic. In comparison, high-strength aluminium used in coaches is not recyclable because of its iron content. A more aesthetic, ceramic, hard-coated stainless steel is also available for interior panelling, partitioning, flooring and other inner decorative applications. This has better resistance to temperature and corrosion and is easy to clean.Besides green components, Seth points out that customers are also open to innovative new features, which is helping the market to grow the market some more. For instance, alongside the signalling and interlocking technology and electrification of the 23 km Airport Metro Express Line in New Delhi, Siemens Mobility has supplied the line the Sibag train baggage-handling system. Passengers travelling to the airport now have the option to check in their baggage at the metro stations at New Delhi City Airport Terminal Station and Shivaji Stadium City Airport Terminal Station, he explains. Passengers can pick up their boarding cards, ride the Airport Express to the international airport and proceed straight to the security check and departure gate. The automatic handling system located on the station platform uses a conveyor system to take the containerised baggage through the automatic security check and onto the connecting plane.Beyond doubt, with the slew of equipment on offer, Indian metros are bound to reduce transit times in congested city corridors. Here's to happy riding!Metro: Yes or No?The choice of a transport mode depends on the length and number of corridors needing mass transit systems, their projected future demand and suitability for the possible modes, and the feasibility of introducing the desired mode based on a lifecycle cost analysis. Rail transit is beyond doubt more efficient than buses. The passenger capacity of a rail coach is thrice that of a bus. The life of the coach is also thrice that of a bus. So, although the initial cost of light rail transit is high, it is nine times more efficient than a bus. Still, city planning authorities should not jump to opt for metro rails as the backbone of the urban transport system. Metros are associated with a very high-capacity mode that may only be required in high-density corridors in mega cities. If light rail transit (LRT) modes can adequately meet the demand in medium-size cities or in other corridors in mega cities, they should be preferred as they are less capital intensive than metros. LRT requires lighter structures and mandates less ongoing expenditure on traction energy. It also necessitates less acquisition of roadside property, which is of significant importance considering that the scarcity of land for metro rail-related activities, challenges involved in fixing the price of the land, the need for measures such as transferable development rights to motivate sellers to part with land, and the delays in handing over land to contractors are major hurdles in many infrastructure projects. The projected cost of Phase III of the Delhi Metro Rail is approximately Rs 300 crore per km, at the very least. As it is, even where the huge investment on a metro can be justified, authorities must take steps to link the metro line with other public transport systems to maximise the utilisation of the capital outlay.Give us your comments on this article at feedback@ASAPPmedia.com
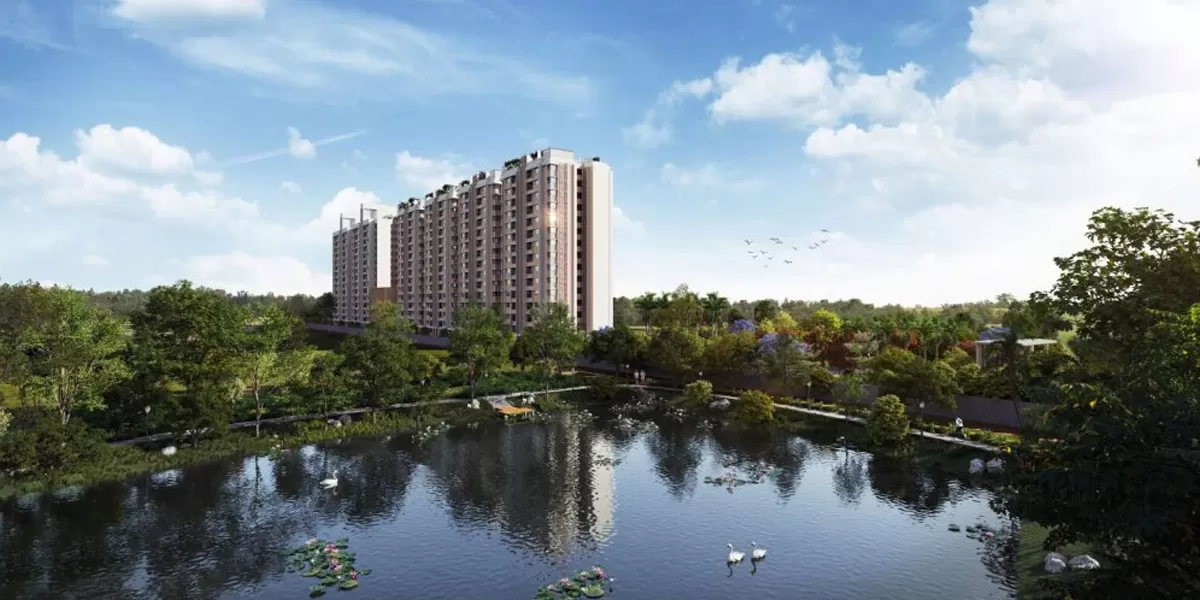
Shriram Properties Launches ‘Codename: The One’ in Bengaluru
Shriram Properties (SPL), a leading real estate developer focused on the mid-market and mid-premium segments, has announced the launch of its latest residential project under the banner “Codename: The One” in Bengaluru’s Electronic City corridor. This feature-rich gated community will offer 340 spacious 2- and 3-BHK residences, with a total saleable area of approximately 5 lakh square feet and an estimated revenue potential of over Rs 3.5 billion. The project is expected to be developed over a span of more than three years. Strategically located near the Bommasandra Metro stat..
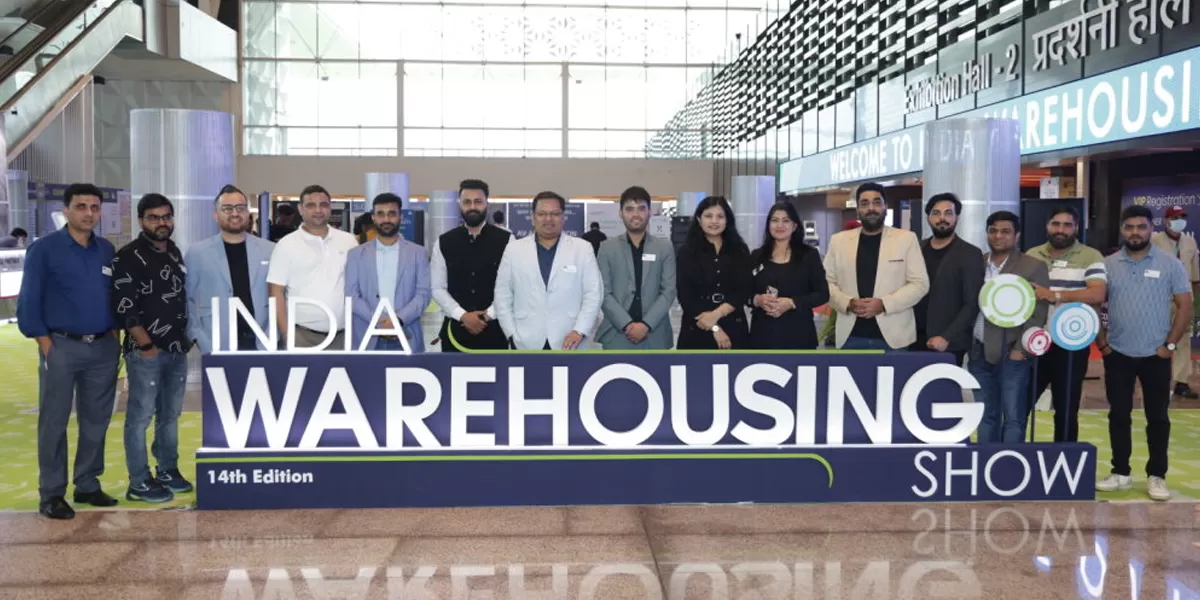
India Warehousing Show 2025 Closes with Strong Global Presence
The 14th edition of the India Warehousing Show (IWS) 2025 concluded successfully at Yashobhoomi (IICC), Dwarka, drawing participation from over 300 exhibitors across 15 countries and welcoming 15,000+ visitors. Recognised as India’s leading platform for warehousing and logistics excellence, IWS 2025 offered a comprehensive display of cutting-edge automation, sustainable warehousing solutions, and next-gen supply chain technologies. The show was inaugurated by Shri Pankaj Kumar, Joint Secretary – Logistics, DPIIT, Ministry of Commerce and Industry, Government of India. In his opening a..
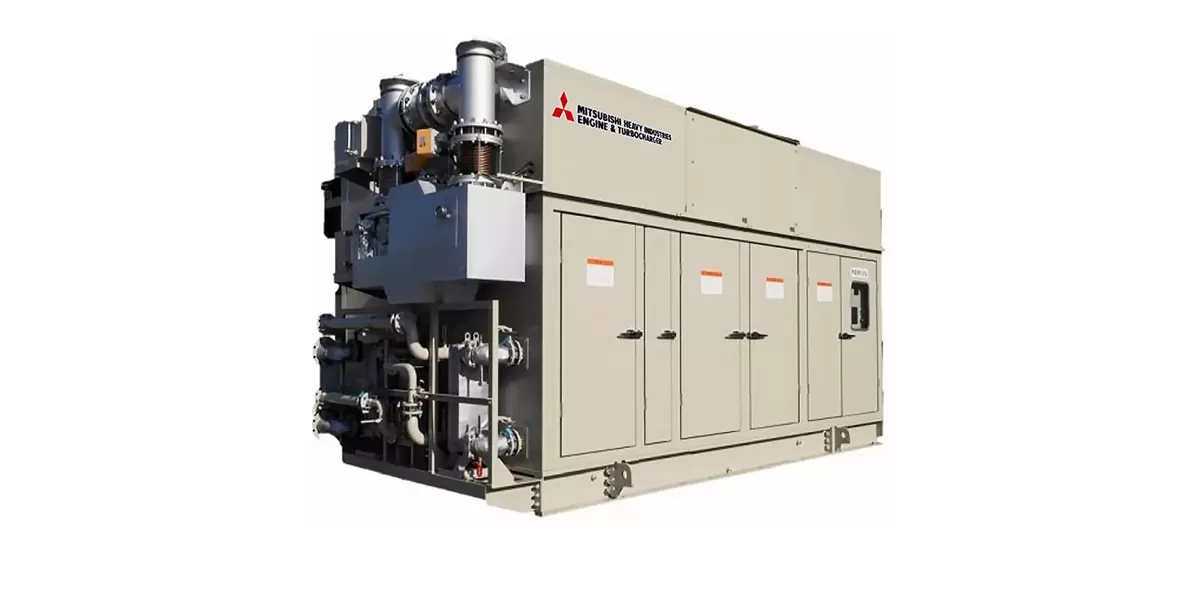
MHIET Launches 450kW Gas Cogeneration System with H₂ Co-Firing
Mitsubishi Heavy Industries Engine & Turbocharger (MHIET), part of the Mitsubishi Heavy Industries Group, has launched a new 450kW gas cogeneration system, the SGP M450, jointly developed with Toho Gas Co.,. The system supports hydrogen co-firing at up to 15 vol per cent, with no loss in performance or reliability. The system is currently available in the Japanese market, and has been developed from the existing GS6R2 city gas engine platform. Key modifications were made to the fuel gas and engine control systems to enable hydrogen co-firing. Verified through de..
Latest Updates
Advertisement
Recommended for you
Advertisement
Subscribe to Our Newsletter
Get daily newsletters around different themes from Construction world.
Advertisement
Advertisement
Advertisement
subscribe to the newsletter
Don't miss out on valuable insights and opportunities
to connect with like minded professionals