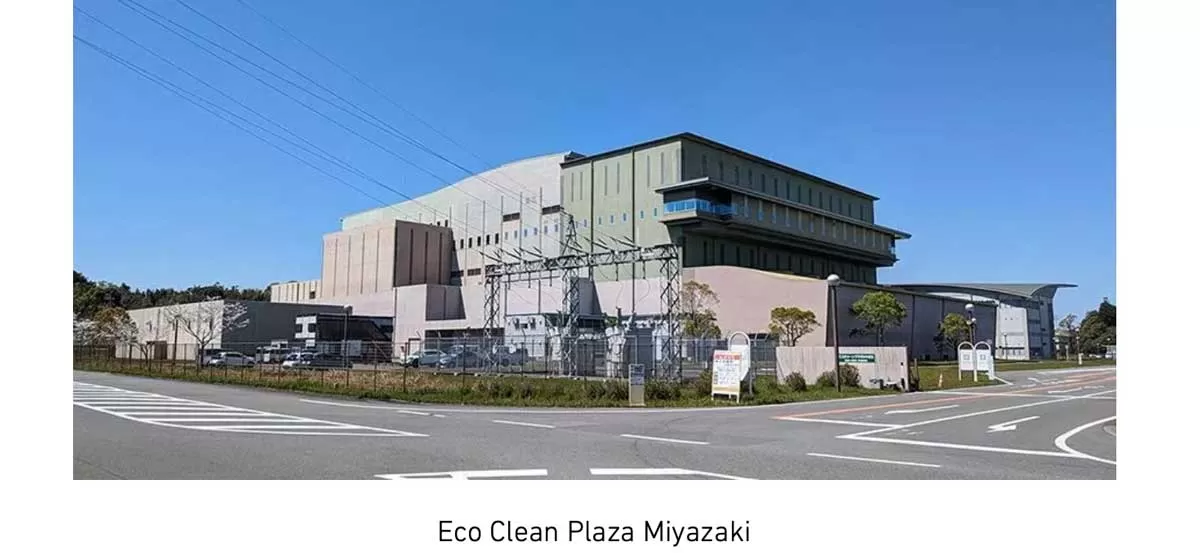
MHIEC Upgrades Core Facilities at Miyazaki Waste-to-Energy Plant
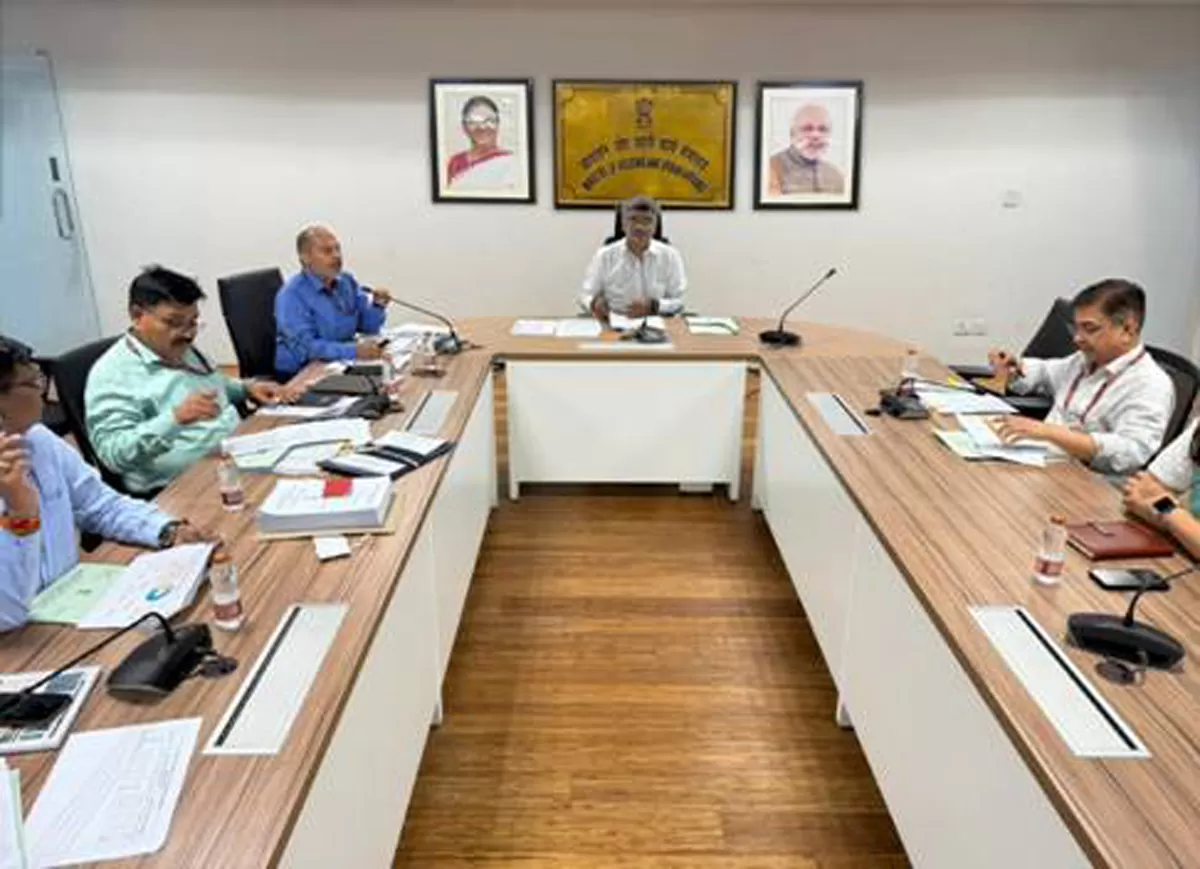
MoHUA Sanctions 1.47 Lakh Additional Houses Under PMAY-U 2.0
In a major push towards the Government’s Housing for All mission, the Ministry of Housing and Urban Affairs (MoHUA) has approved 1,46,582 additional pucca houses under Pradhan Mantri Awas Yojana – Urban 2.0 (PMAY-U 2.0) for 14 States/UTs, bringing total sanctions under the revamped scheme to 8.56 lakh.The decision came during the fourth meeting of the Central Sanctioning and Monitoring Committee (CSMC), chaired by Srinivas Katikithala, Secretary, MoHUA, at the Ministry’s Kasturba Gandhi Marg office. Senior officials, State Principal Secretaries, and PMAY-U Mission Directors participated ..
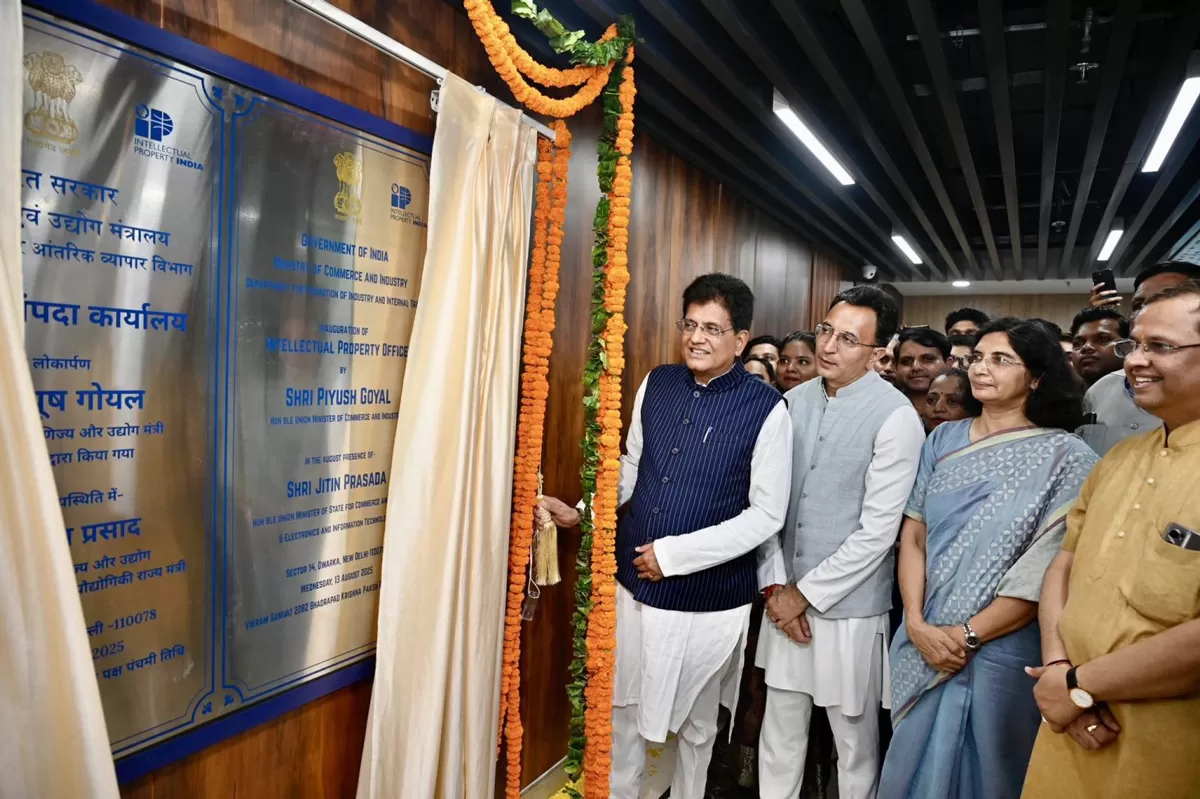
Piyush Goyal Inaugurates Expanded ISA Building at Intellectual Property Office
Union Minister of Commerce and Industry, Piyush Goyal, today inaugurated the newly expanded International Searching Authority (ISA) building at the Intellectual Property Office (IPO) in Dwarka, New Delhi, marking a major step forward in India’s intellectual property ecosystem.Addressing the gathering, Goyal highlighted that innovation has been central to India’s heritage for centuries, citing the engineering brilliance of the Konark Temple as a historic example. He emphasised that innovation is not just intellectual property but a symbol of sovereignty, and a key driver in India’s journe..
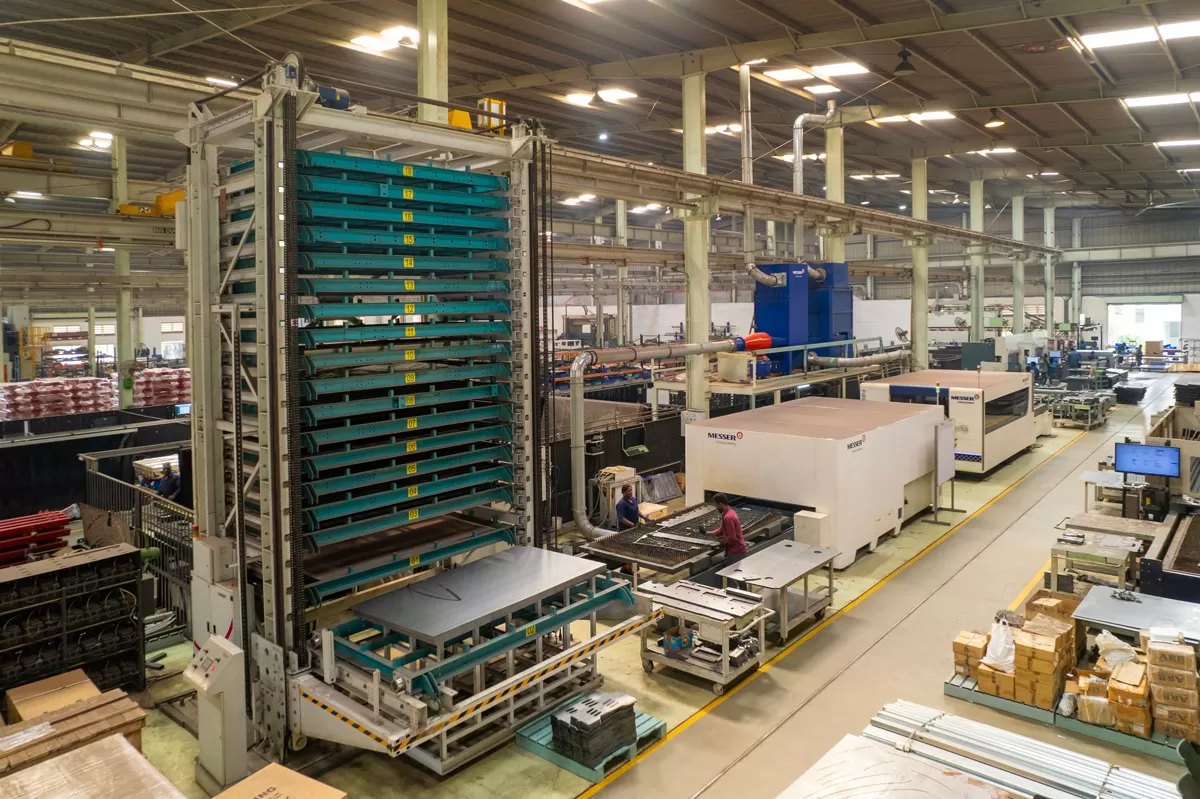
SIEGER Boosts Automation in Mumbai Realty
SIEGER, a leading automation solutions provider, is expanding its advanced manufacturing capabilities to meet the surging demand for precision, high-speed automation in Mumbai’s rapidly growing real estate sector.Operating from a 21,000 m² advanced production hub in Coimbatore—part of a 40,000 m² integrated campus—SIEGER offers complete solutions from design and prototyping to manufacturing and deployment. The fully digitalised facility features CNC machining, QR-coded component tracking, conveyorized powder coating, and a Government of India–certified R&D centre, ensuring unmatc..